- お役立ち記事
- Innovative Manufacturing Techniques in Japan: Understanding the “Rock Line” Transition
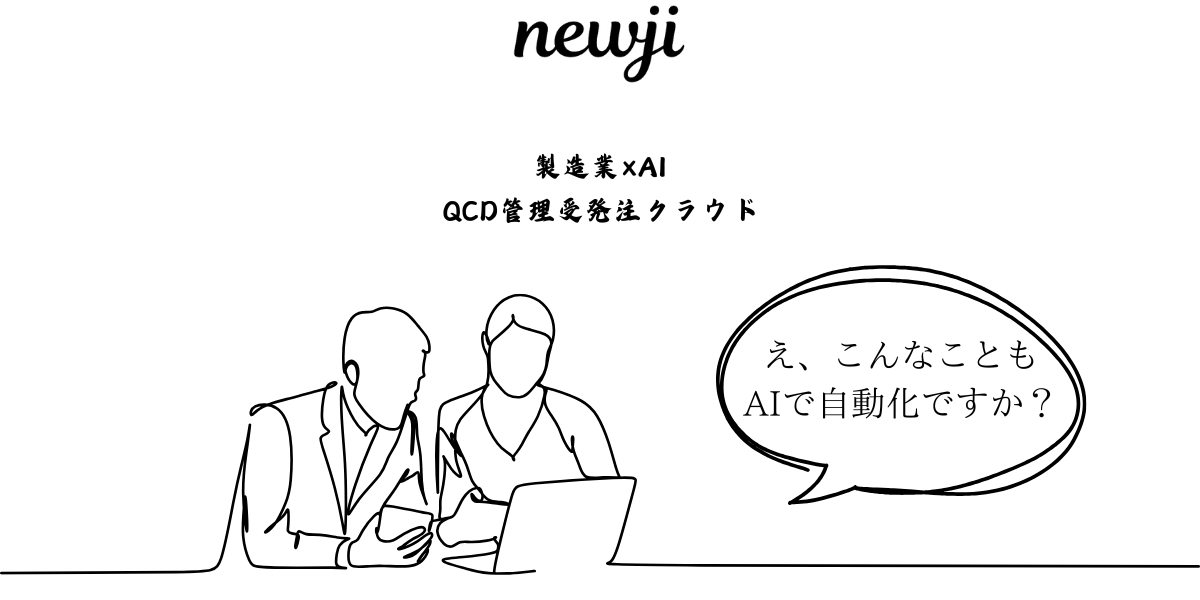
Innovative Manufacturing Techniques in Japan: Understanding the “Rock Line” Transition
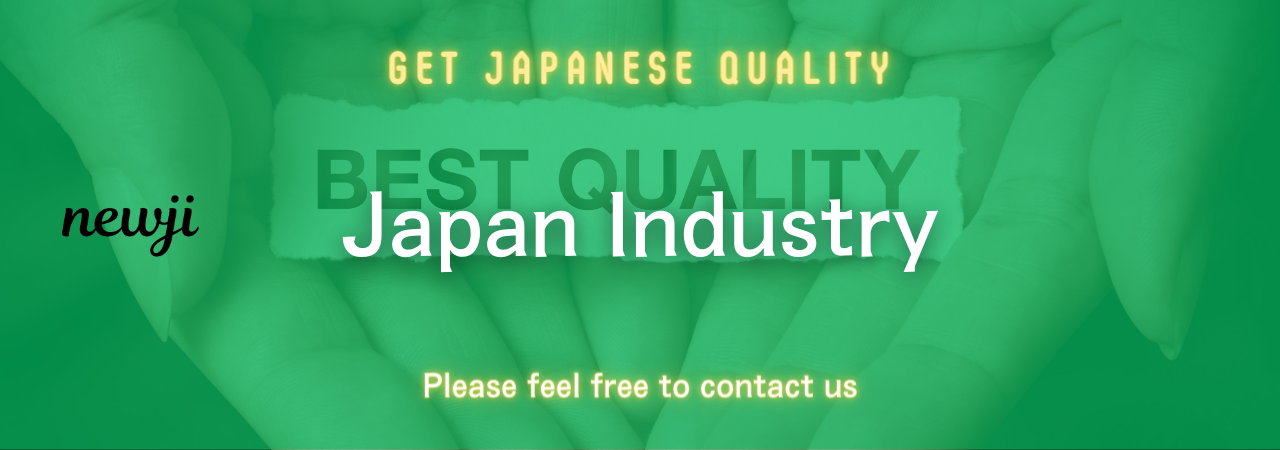
目次
Innovative Manufacturing Techniques in Japan: Understanding the “Rock Line” Transition
When it comes to manufacturing, few countries boast the level of efficiency, precision, and quality that Japan consistently achieves. A significant factor in this excellence lies in Japan’s innovative manufacturing techniques, one of which is the “Rock Line” transition. This article aims to provide an extensive overview of the Rock Line concept, its benefits and drawbacks, real-world applications, strategies for successful implementation, and its impact on global procurement.
What is the “Rock Line” Technique?
The term “Rock Line” may be unfamiliar to some, but within the realms of Japanese manufacturing, it holds significant importance. The Rock Line approach focuses on creating a highly efficient and flexible production line that can adapt to varying demand levels without compromising on quality or speed.
The Rock Line methodology is centered around the concept of “stop-and-go” production. Unlike traditional production lines where items move seamlessly from one stage to another, Rock Line introduces deliberate pauses. These pauses serve two main purposes: allowing for quality checks and enabling quick adjustments in response to demand changes.
Core Principles of the Rock Line Technique
To fully understand this system’s advantages, it is essential to delve into its core principles:
– **Stop-and-go production:** The production line is designed to stop at crucial points for quality checks or adjustments.
– **Flexibility:** The design accommodates variations in demand and production volume.
– **Efficiency:** Minimizes waste and optimizes resource utilization through careful planning and execution.
– **Continuous improvement:** Emphasizes ongoing refinement based on feedback and performance metrics.
Advantages of the Rock Line Method
The Rock Line method offers several advantages that make it highly appealing to manufacturers globally.
Enhanced Quality Control
By incorporating deliberate pauses in the production line, the Rock Line technique enables thorough quality inspections at crucial stages. This reduces the likelihood of defects and ensures that any issues are addressed promptly, maintaining high-quality standards.
Improved Flexibility
The ability to pause and adjust the production process makes the Rock Line method highly adaptable to changing market demands. Manufacturers can quickly shift production volumes or change product specifications without significant downtime.
Efficiency and Waste Reduction
The Rock Line approach emphasizes the efficient use of resources and minimization of waste. By carefully planning production stages and incorporating regular inspections, manufacturers can optimize resource utilization and reduce material waste, thus lowering overall costs.
Continuous Improvement
The Rock Line method fosters a culture of continuous improvement. By regularly analyzing performance metrics and incorporating feedback, manufacturers can refine their processes and achieve higher levels of efficiency and quality over time.
Disadvantages of the Rock Line Method
While the Rock Line method offers numerous benefits, it also has certain drawbacks that manufacturers should consider.
Initial Implementation Costs
Implementing the Rock Line technique can require significant upfront investments in terms of equipment, training, and process redesign. Small and medium-sized enterprises (SMEs) may find these initial costs burdensome.
Complexity in Management
Managing a Rock Line production system can be more complex than traditional linear production lines. It requires meticulous planning, coordination, and monitoring to ensure that production pauses and adjustments are effectively executed.
Potential for Downtime
While the Rock Line method’s pauses are designed to enhance quality control and flexibility, they can also result in production downtime. If not managed properly, these pauses can lead to delays and affect overall production efficiency.
Real-World Applications of the Rock Line Method
The Rock Line method has found applications in various industries, demonstrating its versatility and effectiveness in different manufacturing contexts.
Automotive Industry
In the automotive industry, where precision and quality are paramount, the Rock Line technique is used to ensure that every vehicle meets stringent quality standards. By incorporating pauses for rigorous inspections and adjustments, automotive manufacturers can maintain high levels of quality while adapting to varying production demands.
Electronics Manufacturing
Electronics manufacturers often face fluctuating demand and rapid technological advancements. The Rock Line method allows them to quickly adjust production volumes and incorporate new technologies without compromising on quality or efficiency. This flexibility is crucial in an industry characterized by fast-paced innovation.
Consumer Goods Production
The consumer goods industry benefits from the Rock Line technique’s ability to adapt to changing consumer preferences and market trends. Manufacturers can quickly introduce new products or adjust existing ones, ensuring that they remain competitive in a dynamic market.
Pharmaceutical Manufacturing
In the pharmaceutical industry, quality control is critical to ensuring the safety and efficacy of products. The Rock Line method’s emphasis on thorough inspections and adjustments makes it an ideal choice for pharmaceutical manufacturers seeking to maintain high-quality standards while meeting regulatory requirements.
Strategies for Successful Implementation of the Rock Line Method
Implementing the Rock Line technique requires careful planning and execution. Here are some strategies that can help manufacturers successfully adopt this innovative manufacturing approach.
Invest in Training and Skill Development
To effectively implement the Rock Line method, manufacturers need a workforce that is skilled in the necessary processes and techniques. Investing in training and skill development is crucial to ensure that employees are well-equipped to manage the complexities of the Rock Line system.
Implement Robust Quality Control Systems
Quality control is a central aspect of the Rock Line technique. Manufacturers should implement robust quality control systems that allow for thorough inspections and prompt identification of issues. This includes investing in advanced inspection technologies and establishing clear quality standards.
Leverage Technology and Automation
Technology and automation play a key role in the success of the Rock Line method. By leveraging advanced manufacturing technologies and automation systems, manufacturers can enhance the efficiency and accuracy of production processes. This includes using sensors, data analytics, and machine learning to optimize production stages and make informed adjustments.
Foster a Culture of Continuous Improvement
The Rock Line method thrives on continuous improvement. Manufacturers should foster a culture that encourages ongoing refinement of processes based on feedback and performance metrics. This includes regular performance reviews, employee involvement in process improvements, and establishing mechanisms for capturing and analyzing data.
Impact on Global Procurement
The Rock Line method’s advantages extend beyond the manufacturing floor, influencing global procurement practices in significant ways.
Enhanced Supplier Relationships
The emphasis on quality control and continuous improvement in the Rock Line technique fosters stronger relationships with suppliers. By collaborating with suppliers to ensure consistent quality and incorporating feedback, manufacturers can build long-term partnerships that enhance overall procurement effectiveness.
Increased Flexibility in Supply Chains
The flexibility of the Rock Line method translates to increased agility in supply chains. Manufacturers can quickly adjust production volumes and respond to changes in demand, reducing lead times and enhancing the responsiveness of the supply chain.
Cost Savings through Waste Reduction
The efficient use of resources and minimization of waste in the Rock Line method contribute to cost savings in procurement. By optimizing material usage and reducing waste, manufacturers can lower procurement costs and improve the overall cost-effectiveness of their supply chains.
Improved Risk Management
The Rock Line technique’s focus on quality control and continuous improvement enhances risk management in procurement. By identifying and addressing quality issues early in the production process, manufacturers can mitigate risks associated with defective products and ensure compliance with regulatory requirements.
Market Conditions and Best Practices
The successful implementation of the Rock Line method is influenced by market conditions and best practices. Understanding these factors can help manufacturers maximize the benefits of this innovative manufacturing approach.
Stay Informed about Market Trends
Staying informed about market trends and developments is crucial for manufacturers adopting the Rock Line technique. By monitoring changes in consumer preferences, technological advancements, and industry regulations, manufacturers can make informed decisions and adapt their Rock Line processes accordingly.
Collaborate with Industry Experts
Collaborating with industry experts and consultants can provide valuable insights and guidance for implementing the Rock Line method. These experts can offer recommendations based on their experience and knowledge of best practices, helping manufacturers navigate the complexities of the Rock Line technique.
Benchmark against Competitors
Benchmarking against competitors can provide manufacturers with a reference point for evaluating the effectiveness of their Rock Line processes. By comparing performance metrics and best practices, manufacturers can identify areas for improvement and make adjustments to enhance their Rock Line systems.
Invest in Research and Development
Investing in research and development (R&D) is essential for manufacturers seeking to stay ahead of the curve in Rock Line implementation. By continuously exploring new technologies, materials, and processes, manufacturers can refine their Rock Line systems and achieve higher levels of efficiency and quality.
Conclusion
The Rock Line method represents a significant innovation in Japanese manufacturing, offering numerous advantages in terms of quality control, flexibility, and efficiency. While it presents certain challenges, careful planning, investment in training and technology, and a commitment to continuous improvement can help manufacturers successfully implement this technique.
As global procurement practices continue to evolve, the Rock Line method’s impact on supplier relationships, supply chain agility, cost savings, and risk management cannot be overlooked. By understanding market conditions, collaborating with industry experts, benchmarking against competitors, and investing in R&D, manufacturers can maximize the benefits of the Rock Line technique and stay competitive in an ever-changing market.
In conclusion, the Rock Line method is a testament to Japan’s commitment to innovation and excellence in manufacturing. By embracing this technique, manufacturers can elevate their production processes, enhance quality control, and achieve new levels of efficiency and flexibility. As the global manufacturing landscape continues to evolve, the Rock Line method stands as a beacon of innovation, guiding manufacturers towards a future of greater efficiency and success.
資料ダウンロード
QCD調達購買管理クラウド「newji」は、調達購買部門で必要なQCD管理全てを備えた、現場特化型兼クラウド型の今世紀最高の購買管理システムとなります。
ユーザー登録
調達購買業務の効率化だけでなく、システムを導入することで、コスト削減や製品・資材のステータス可視化のほか、属人化していた購買情報の共有化による内部不正防止や統制にも役立ちます。
NEWJI DX
製造業に特化したデジタルトランスフォーメーション(DX)の実現を目指す請負開発型のコンサルティングサービスです。AI、iPaaS、および先端の技術を駆使して、製造プロセスの効率化、業務効率化、チームワーク強化、コスト削減、品質向上を実現します。このサービスは、製造業の課題を深く理解し、それに対する最適なデジタルソリューションを提供することで、企業が持続的な成長とイノベーションを達成できるようサポートします。
オンライン講座
製造業、主に購買・調達部門にお勤めの方々に向けた情報を配信しております。
新任の方やベテランの方、管理職を対象とした幅広いコンテンツをご用意しております。
お問い合わせ
コストダウンが利益に直結する術だと理解していても、なかなか前に進めることができない状況。そんな時は、newjiのコストダウン自動化機能で大きく利益貢献しよう!
(Β版非公開)