- お役立ち記事
- Harnessing Visual Sensors: The Future of Innovation in Japanese Manufacturing
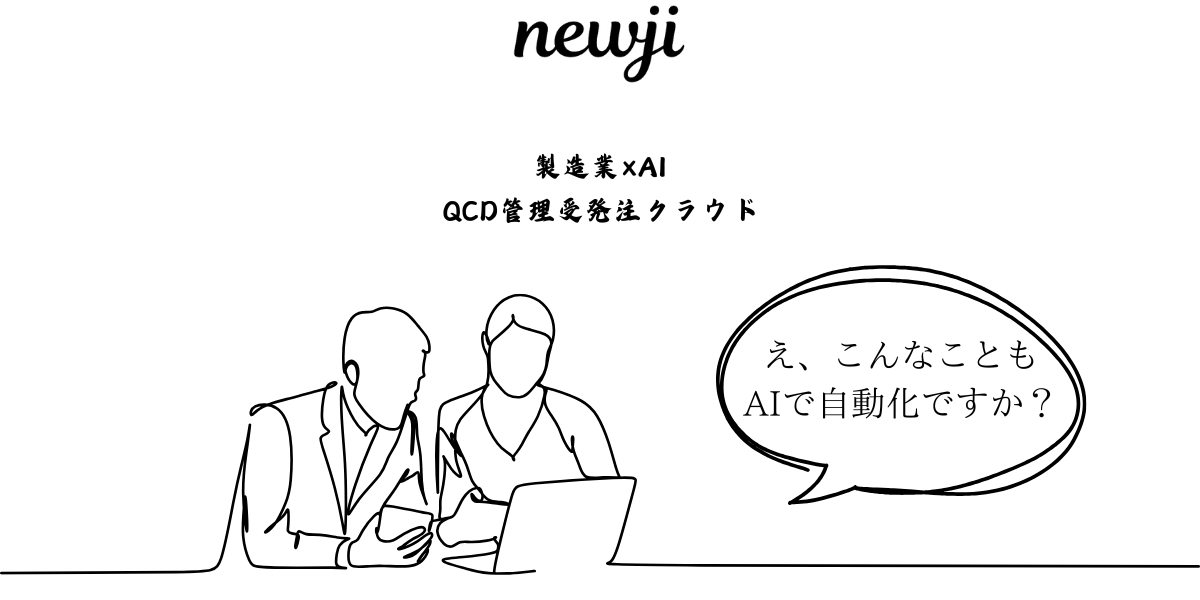
Harnessing Visual Sensors: The Future of Innovation in Japanese Manufacturing
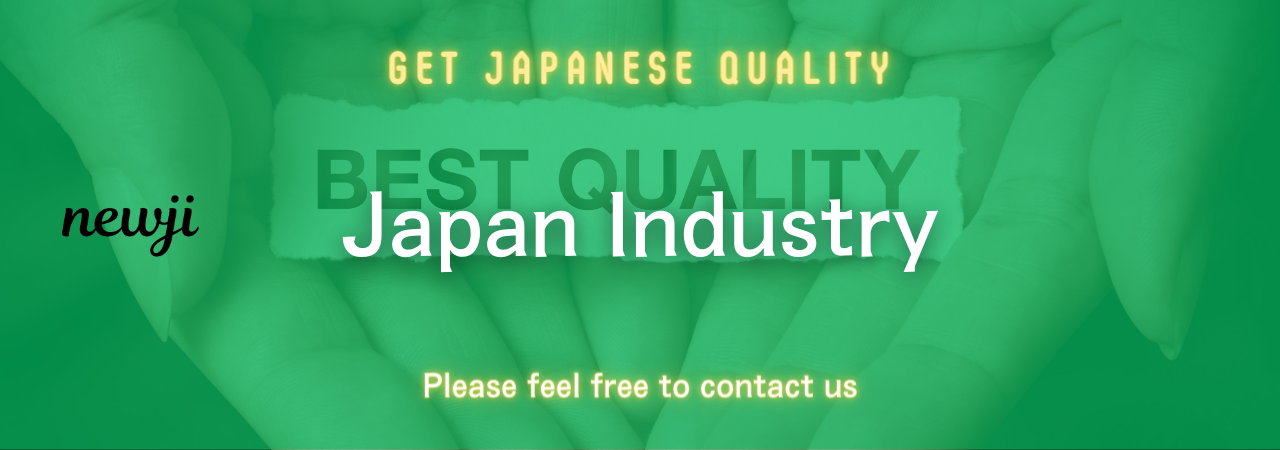
目次
Introduction
Over the last few decades, Japan’s manufacturing sector has earned a reputation for its innovative approach and high-quality production.
At the heart of this success lies a commitment to adopting cutting-edge technology and fine-tuning operational efficiency. One of the most transformative technologies in recent times is the integration of visual sensors.
Visual sensors represent the future of innovation in manufacturing. These devices capture and interpret visual information, enabling machines to perform complex tasks with precision and efficiency.
Japan has been at the forefront of this technology, utilizing visual sensors to enhance various aspects of manufacturing including quality control, automation, and operational efficiency.
This article delves into the role of visual sensors in Japanese manufacturing, highlighting their benefits, supplier dynamics, and best practices for leveraging this technology effectively.
The Role of Visual Sensors in Enhancing Manufacturing
Improving Quality Control
Quality control is paramount in manufacturing.
Visual sensors play a crucial role by providing real-time inspection capabilities that human eyes simply cannot match. These sensors can identify minute defects, ensuring each product meets stringent quality standards.
For example, in the automotive industry, visual sensors can analyze car parts for imperfections that could lead to significant issues down the line. As a result, manufacturers can prevent defective products from reaching the market, enhancing brand reliability.
Boosting Automation
Visual sensors are vital for advancing automation in manufacturing.
They enable machines to ‘see’ their environment and make autonomous decisions, significantly improving operational efficiency.
For instance, in assembly lines, visual sensors can guide robotic arms to align components with pinpoint accuracy, drastically reducing the margin of error and increasing production speed.
Japanese factories have widely adopted this technology, setting a benchmark in smart manufacturing practices.
Enhancing Operational Efficiency
By integrating visual sensors, manufacturers can streamline their processes.
These sensors provide valuable data that can be analyzed to optimize workflows, reduce downtime, and save costs. For example, sensors can monitor machinery wear and tear in real-time, predicting maintenance needs before a breakdown occurs.
This predictive maintenance approach minimizes unplanned downtime, ensuring continuous production and maximizing equipment lifespan.
Advantages of Leveraging Visual Sensors
Precision and Accuracy
One of the standout advantages of visual sensors is their ability to provide precise and accurate measurements.
This capability translates into consistent product quality and reduced waste. Manufacturing processes become more reliable, producing items that align with design specifications without the need for extensive human oversight.
Cost-Effectiveness
While the initial investment in visual sensors might be substantial, the long-term gains are considerable.
The reduction in defective products, minimized downtime, and increased production efficiency contribute to significant cost savings. Additionally, the lifespan of machinery is extended due to predictive maintenance, lowering replacement costs.
Data-Driven Insights
Visual sensors are pivotal in generating a wealth of data that can be used for continuous improvement.
By analyzing this data, manufacturers can gain insights into their operations, identifying areas for improvement and making informed decisions. This data-driven approach leads to more efficient and adaptable manufacturing processes.
Challenges and Considerations
Initial Investment and Implementation
Despite their advantages, visual sensors come with a high upfront cost.
Implementing these systems also requires significant time and expertise to integrate them seamlessly into existing processes. Manufacturers need to be prepared for potential disruptions during the transitional phase.
Need for Technical Expertise
Operating and maintaining visual sensor systems require specialized knowledge.
Manufacturers must either train their existing workforce or hire experts to manage these systems. This could be a formidable challenge, especially for companies without prior experience with advanced technologies.
Data Security
With the increase in data collection comes the responsibility of ensuring its security.
Manufacturers must invest in robust cybersecurity measures to protect sensitive information from potential breaches. This adds another layer of complexity and cost to the implementation of visual sensors.
Supplier Negotiation Techniques
Understanding Supplier Capabilities
When sourcing visual sensors, it’s crucial to evaluate the supplier’s capabilities thoroughly.
Consider factors such as the supplier’s experience, product quality, and after-sales support. A reputable supplier will have a proven track record of serving established companies and providing reliable products and services.
Building Long-Term Relationships
Developing long-term relationships with suppliers can lead to better terms and mutual trust.
Engage in transparent communications and regularly review performance metrics. By fostering a collaborative relationship, both parties can work towards continuous improvements and innovation.
Leverage Bulk Purchasing
Buying visual sensors in bulk can often result in favorable pricing and terms.
Larger orders are attractive to suppliers, giving manufacturers leverage in negotiations for discounts or additional services. However, it’s essential to balance bulk purchasing with the flexibility to adjust orders based on evolving needs.
Current Market Conditions
Technological Advancements
The market for visual sensors is continually evolving, with rapid advancements in technology.
Manufacturers should stay abreast of the latest developments to ensure they are investing in cutting-edge solutions. Newer models often offer enhanced capabilities at reduced costs, providing better ROI.
Competitive Landscape
The competitive landscape for visual sensors includes a mix of established players and emerging startups.
While established companies offer reliability and extensive support, startups often bring innovative approaches and competitive pricing. Evaluating both types of suppliers can provide a broader perspective on available options.
Regulatory Standards
Manufacturers must be aware of regulatory standards governing the use of visual sensors.
Compliance with these standards is essential to avoid legal complications and to ensure the safety and efficiency of operations. Regular updates to these regulations require manufacturers to stay informed and adapt accordingly.
Best Practices for Visual Sensor Integration
Comprehensive Training Programs
Investing in comprehensive training programs for staff is crucial for the successful integration of visual sensors.
Employees must understand how to operate and maintain these systems effectively. Continuous education ensures that the workforce remains adept at handling new advancements in sensor technology.
Regular Maintenance and Upgrades
Regular maintenance of visual sensors is essential to ensure their optimal performance.
Manufacturers should establish routine inspection schedules and upgrade systems as needed. Keeping the technology updated guarantees that it continues to meet production demands and technological advancements.
Data Analytics Integration
Integrating visual sensors with data analytics platforms can provide deeper insights into manufacturing processes.
By analyzing the data collected, manufacturers can identify trends, anticipate issues, and implement corrective measures swiftly. This integration fosters a proactive approach to production management.
Conclusion
Visual sensors are revolutionizing the manufacturing landscape by enhancing quality control, boosting automation, and improving operational efficiency.
Japanese manufacturers, with their emphasis on precision and innovation, are leading the way in leveraging this technology.
While the journey to integrating visual sensors comes with its challenges, the long-term benefits far outweigh the initial hurdles. By adopting best practices, fostering strong supplier relationships, and staying informed about market trends, manufacturers can fully harness the potential of visual sensors.
In doing so, they pave the way for a future characterized by superior product quality, cost-efficient operations, and groundbreaking innovations in manufacturing.
資料ダウンロード
QCD調達購買管理クラウド「newji」は、調達購買部門で必要なQCD管理全てを備えた、現場特化型兼クラウド型の今世紀最高の購買管理システムとなります。
ユーザー登録
調達購買業務の効率化だけでなく、システムを導入することで、コスト削減や製品・資材のステータス可視化のほか、属人化していた購買情報の共有化による内部不正防止や統制にも役立ちます。
NEWJI DX
製造業に特化したデジタルトランスフォーメーション(DX)の実現を目指す請負開発型のコンサルティングサービスです。AI、iPaaS、および先端の技術を駆使して、製造プロセスの効率化、業務効率化、チームワーク強化、コスト削減、品質向上を実現します。このサービスは、製造業の課題を深く理解し、それに対する最適なデジタルソリューションを提供することで、企業が持続的な成長とイノベーションを達成できるようサポートします。
オンライン講座
製造業、主に購買・調達部門にお勤めの方々に向けた情報を配信しております。
新任の方やベテランの方、管理職を対象とした幅広いコンテンツをご用意しております。
お問い合わせ
コストダウンが利益に直結する術だと理解していても、なかなか前に進めることができない状況。そんな時は、newjiのコストダウン自動化機能で大きく利益貢献しよう!
(Β版非公開)