- お役立ち記事
- The difference between Target Costing and Cost Reduction
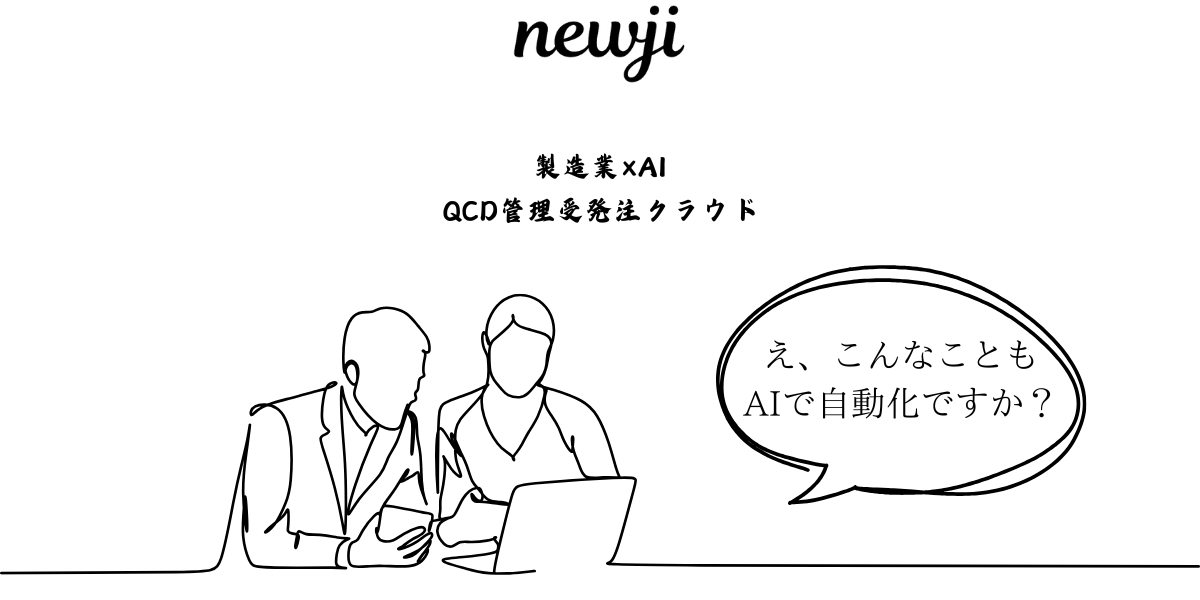
The difference between Target Costing and Cost Reduction
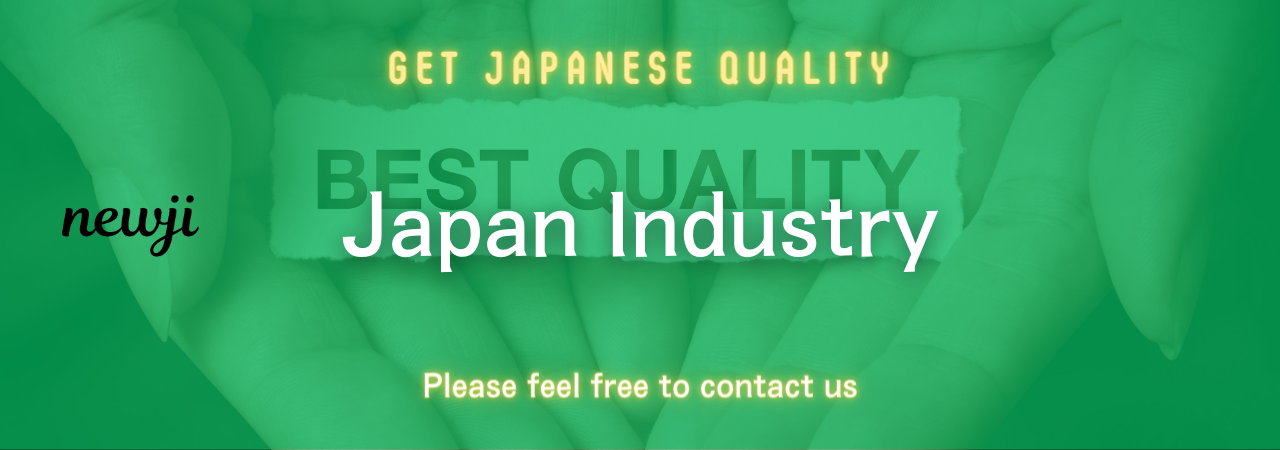
In the world of business and finance, understanding the nuances of various cost management strategies holds paramount importance. Two of the most often discussed and frequently confounded cost management terms are target costing and cost reduction.
Misunderstanding these concepts can lead to suboptimal business decisions.
So, let’s dive deep and explore the difference between target costing and cost reduction.
目次
Understanding Target Costing
Target costing is a proactive cost management technique primarily used during the product design and development phase.
Definition of Target Costing
Target costing sets a planned selling price for a product.
Subtracting the desired profit margin from this planned selling price gives the target cost.
The main idea is to ensure that the final product can be produced and sold at the target cost while earning the expected profit margin.
How Target Costing Works
The process of target costing involves several key steps:
1. **Market Research**: Conduct thorough market research to know the acceptable price point for the product.
2. **Set the Target Price**: Determine the selling price based on market competition and consumer demand.
3. **Establish the Desired Profit Margin**: Define the profit margin that the company aims to achieve.
4. **Calculate the Target Cost**: Subtract the desired profit margin from the target price to get the target cost.
5. **Product Design and Process Engineering**: Design the product and refine the production process to meet the target cost.
Benefits of Target Costing
Target costing offers various advantages to businesses:
**Market Orientation**: Helps in making the product price competitive.
**Cost Control**: Encourages cost-efficiency from the initial stages, allowing the company to avoid excessive costs.
**Customer Focus**: Ensures that the product meets market demand both in terms of features and pricing.
Understanding Cost Reduction
Unlike target costing, cost reduction is commonly an ongoing process aimed at cutting down existing expenses.
Definition of Cost Reduction
Cost reduction is the process of actively finding and implementing ways to lower the current cost levels without compromising the quality and functionality of the product or service.
How Cost Reduction Works
Cost reduction can be achieved through various approaches such as:
**Process Improvement**: Streamline existing workflows and operational processes to eliminate inefficiencies.
**Material Substitution**: Replace expensive materials with cost-effective alternatives without affecting product quality.
**Outsourcing**: Contract out certain business operations to specialized service providers who can perform these activities more cost-effectively.
**Economies of Scale**: Increase production to lower the per-unit cost through economies of scale.
Benefits of Cost Reduction
Cost reduction brings multiple benefits to businesses:
**Profit Maximization**: Directly contributes to higher profit margins.
**Competitiveness**: Offers the ability to compete more effectively by lowering prices or increasing marketing efforts.
**Resource Optimization**: Ensures that existing resources are used more efficiently.
Key Differences Between Target Costing and Cost Reduction
While both target costing and cost reduction aim to manage and reduce costs, they differ significantly in their application and scope.
Focus and Timing
Target costing is primarily a proactive measure undertaken during product development.
In contrast, cost reduction is generally a reactive strategy applied at any stage of a product’s lifecycle.
Objective
The primary objective of target costing is to meet the market-driven price point while ensuring profitability.
On the other hand, the main aim of cost reduction is to lower existing cost levels to improve profit margins.
Approach
Target costing involves designing and engineering the product from the ground up to achieve the desired cost.
Cost reduction usually focuses on fine-tuning existing processes and finding cost-effective alternatives.
Real-World Examples
To better understand the practical applications of these concepts, let’s look at real-world examples.
Example of Target Costing
Consider a consumer electronics company planning to launch a new smartphone.
They conduct market research to determine that an optimal selling price is $500.
If the company wishes to achieve a profit margin of $100 per unit, the target cost for manufacturing the smartphone would be $400.
The design and production teams work collaboratively to ensure that the total manufacturing cost of the smartphone does not exceed this target cost.
Example of Cost Reduction
On the other hand, consider a manufacturing firm that produces kitchen appliances.
Their current production cost per unit is $250.
Through process improvement initiatives, such as automating certain manual tasks and negotiating better rates for raw materials, they manage to reduce the production cost to $200.
This brings higher profitability while maintaining the quality of the kitchen appliances.
Challenges and Considerations
Both target costing and cost reduction come with their own set of challenges.
Challenges in Target Costing
**Rigorous Market Research**: Requires accurate market data and consumer insights, which can be time-consuming and expensive.
**Cross-Functional Collaboration**: Needs coordinated efforts across multiple departments, including marketing, design, and production.
**Risk of Compromising Quality**: Focusing too much on cost control can sometimes lead to substandard products.
Challenges in Cost Reduction
**Initial Investment**: Implementing cost reduction techniques may require an initial investment in new technologies or processes.
**Employee Resistance**: Employees may resist changes, especially if it involves learning new skills or altering established practices.
**Quality Assurance**: Constant vigilance is needed to ensure that cost-cutting measures do not compromise product quality.
Conclusion
Understanding the difference between target costing and cost reduction is crucial for effective cost management.
Target costing is a forward-looking approach focused on market-driven price points and profitability goals during the design and development stages.
Meanwhile, cost reduction is an ongoing effort to optimize existing costs and improve profit margins.
Both strategies have their unique advantages and challenges, and the successful application of either depends on the business context and objectives.
Armed with this knowledge, companies can better navigate the complexities of cost management to achieve sustainable growth and profitability.
資料ダウンロード
QCD調達購買管理クラウド「newji」は、調達購買部門で必要なQCD管理全てを備えた、現場特化型兼クラウド型の今世紀最高の購買管理システムとなります。
ユーザー登録
調達購買業務の効率化だけでなく、システムを導入することで、コスト削減や製品・資材のステータス可視化のほか、属人化していた購買情報の共有化による内部不正防止や統制にも役立ちます。
NEWJI DX
製造業に特化したデジタルトランスフォーメーション(DX)の実現を目指す請負開発型のコンサルティングサービスです。AI、iPaaS、および先端の技術を駆使して、製造プロセスの効率化、業務効率化、チームワーク強化、コスト削減、品質向上を実現します。このサービスは、製造業の課題を深く理解し、それに対する最適なデジタルソリューションを提供することで、企業が持続的な成長とイノベーションを達成できるようサポートします。
オンライン講座
製造業、主に購買・調達部門にお勤めの方々に向けた情報を配信しております。
新任の方やベテランの方、管理職を対象とした幅広いコンテンツをご用意しております。
お問い合わせ
コストダウンが利益に直結する術だと理解していても、なかなか前に進めることができない状況。そんな時は、newjiのコストダウン自動化機能で大きく利益貢献しよう!
(Β版非公開)