- お役立ち記事
- The difference between Turning and Milling
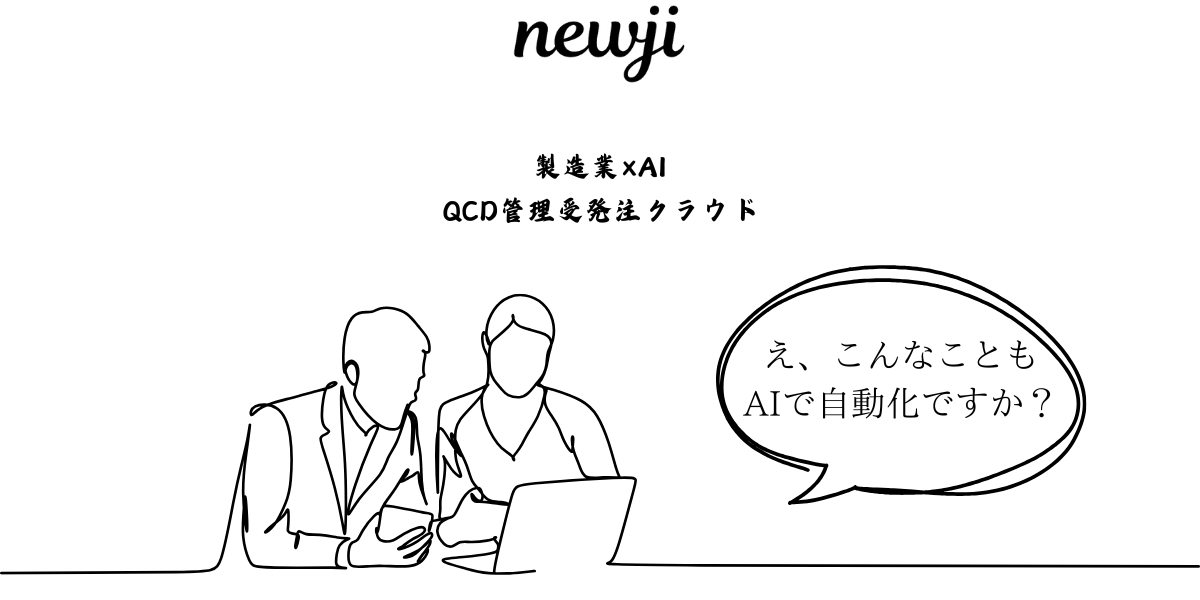
The difference between Turning and Milling
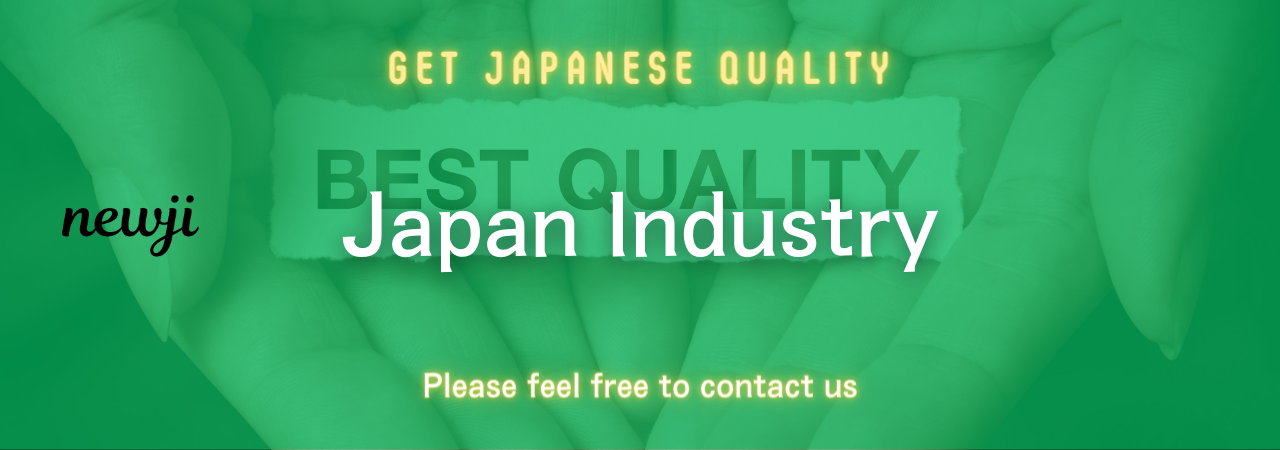
When it comes to manufacturing and creating parts from materials like metal, wood, or plastic, two fundamental machining processes often come into play: turning and milling.
Both are essential in the world of machining, yet they serve different purposes and use distinct methods.
Understanding their differences can help you choose the right process for your specific needs.
So, let’s explore the differences between turning and milling.
目次
What is Turning?
Turning is a machining process where the workpiece is rotated while a single-point cutting tool moves parallel to the axis of rotation.
This method primarily produces cylindrical shapes.
The cutting tool removes material from the workpiece to achieve the desired shape and size.
How Turning Works
In a turning operation, the workpiece is secured in a chuck and rotated at varying speeds.
The cutting tool, typically a carbide insert, is then fed into the rotating workpiece to remove material in a controlled manner.
The process can be used for both external and internal cutting, making it versatile for creating shafts, cylindrical parts, and even threaded components.
Applications of Turning
Turning is widely used in several industries for various applications:
– Creating precise cylindrical components like shafts, pins, and bushings.
– Manufacturing threaded parts, such as screws and bolts.
– Producing parts with complex profiles that require multiple machining steps.
Advantages of Turning
Turning offers several benefits:
– High accuracy and consistent results.
– Opportunity to achieve smooth finishes.
– Capability to machine both ferrous and non-ferrous materials.
What is Milling?
Milling, on the other hand, is a machining process that involves the use of rotary cutters to remove material from a workpiece.
Unlike turning, where the workpiece rotates, in milling, the cutting tool rotates while the workpiece remains stationary or moves along different axes.
How Milling Works
In a milling operation, the workpiece is clamped onto a table or fixture.
The milling cutter, which has multiple cutting edges, is rotated at high speeds.
The table moves the workpiece toward the rotating cutter, removing material to achieve the desired shape.
Milling machines can be vertical or horizontal, and they use a variety of tools like end mills, face mills, and ball nose cutters.
Applications of Milling
Milling is extremely versatile and is used for numerous applications, including:
– Creating flat or contoured surfaces.
– Machining complex shapes and features, such as slots, pockets, and holes.
– Producing parts with intricate surface finishes.
Advantages of Milling
Milling has several distinct advantages:
– Capability to machine a wide range of shapes and complex geometries.
– Flexibility to use various cutting tools for different tasks.
– Suitable for both short and long production runs.
Key Differences Between Turning and Milling
Now that we have a basic understanding of both processes, let’s compare the key differences between turning and milling.
The Role of Workpiece and Cutting Tool
In turning, the workpiece rotates while the cutting tool remains stationary.
In milling, the cutting tool rotates, and the workpiece either remains stationary or moves along various axes.
Shape and Type of Cuts
Turning primarily creates cylindrical shapes and uses single-point cutting tools.
Milling is versatile, capable of creating flat surfaces, complex shapes, and intricate features using multi-point rotating cutters.
Material Removal
Turning generally involves removing material from the external surface of the workpiece.
Milling allows for material removal from both external and internal surfaces, giving it an edge when producing complex parts.
Machines Used
Turning operations are performed on lathes, which have a straightforward setup focused on rotating the workpiece.
Milling operations are conducted on milling machines, which can be more complex and involve multiple axes for moving both the workpiece and the cutting tool.
Production Rates
Turning tends to be faster for producing cylindrical parts, as the setup and machining processes are relatively straightforward.
Milling, with its versatility, can handle more complex geometries but may require more time and setup for intricate designs.
When to Use Turning and Milling
Understanding when to use turning or milling can help optimize your manufacturing process.
Here’s a quick guide:
Use Turning When:
– You need to produce cylindrical or conical shapes.
– You require high precision for components like shafts and threaded parts.
– The project involves simple geometric shapes that can be easily addressed by rotating the workpiece.
Use Milling When:
– The part requires complex geometries, intricate details, or multiple features.
– You need to machine flat or contoured surfaces.
– The design includes slots, holes, or pockets that need precise machining.
Conclusion
Both turning and milling are crucial machining processes, each with its specific advantages and applications.
By understanding their differences, you can make informed decisions about which method to use for your manufacturing needs.
Remember, the key to successful machining lies in choosing the right process tailored to the shape, complexity, and requirements of the part you are producing.
Whether it’s the high precision of turning or the versatile complexity of milling, each method brings unique strengths to the table.
資料ダウンロード
QCD調達購買管理クラウド「newji」は、調達購買部門で必要なQCD管理全てを備えた、現場特化型兼クラウド型の今世紀最高の購買管理システムとなります。
ユーザー登録
調達購買業務の効率化だけでなく、システムを導入することで、コスト削減や製品・資材のステータス可視化のほか、属人化していた購買情報の共有化による内部不正防止や統制にも役立ちます。
NEWJI DX
製造業に特化したデジタルトランスフォーメーション(DX)の実現を目指す請負開発型のコンサルティングサービスです。AI、iPaaS、および先端の技術を駆使して、製造プロセスの効率化、業務効率化、チームワーク強化、コスト削減、品質向上を実現します。このサービスは、製造業の課題を深く理解し、それに対する最適なデジタルソリューションを提供することで、企業が持続的な成長とイノベーションを達成できるようサポートします。
オンライン講座
製造業、主に購買・調達部門にお勤めの方々に向けた情報を配信しております。
新任の方やベテランの方、管理職を対象とした幅広いコンテンツをご用意しております。
お問い合わせ
コストダウンが利益に直結する術だと理解していても、なかなか前に進めることができない状況。そんな時は、newjiのコストダウン自動化機能で大きく利益貢献しよう!
(Β版非公開)