- お役立ち記事
- The difference between Electroplating and Chemical Plating
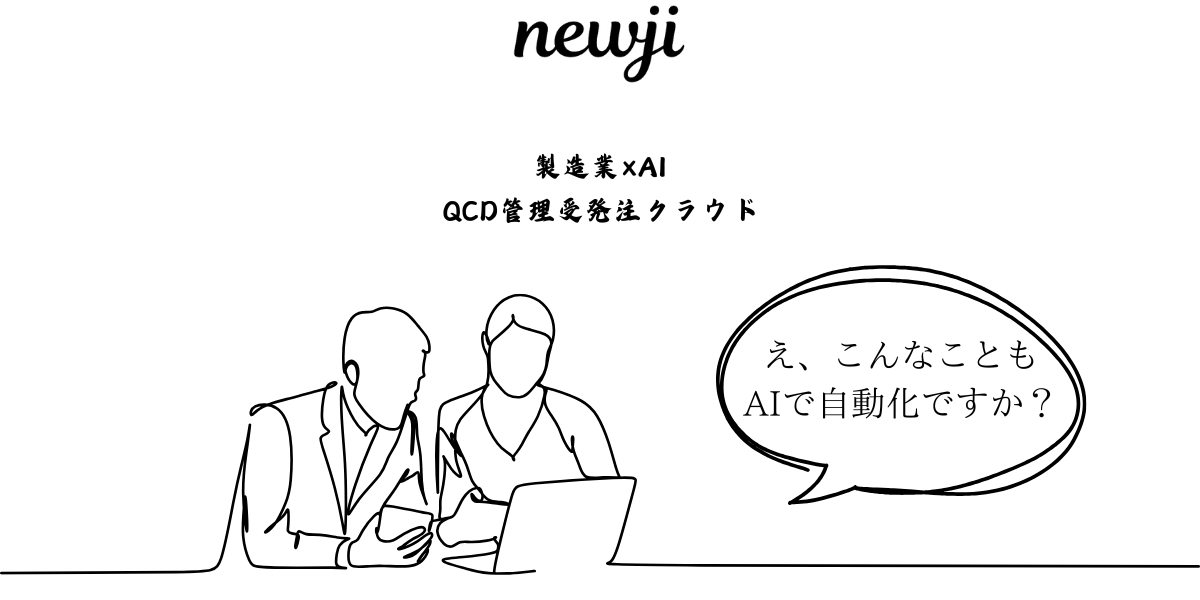
The difference between Electroplating and Chemical Plating
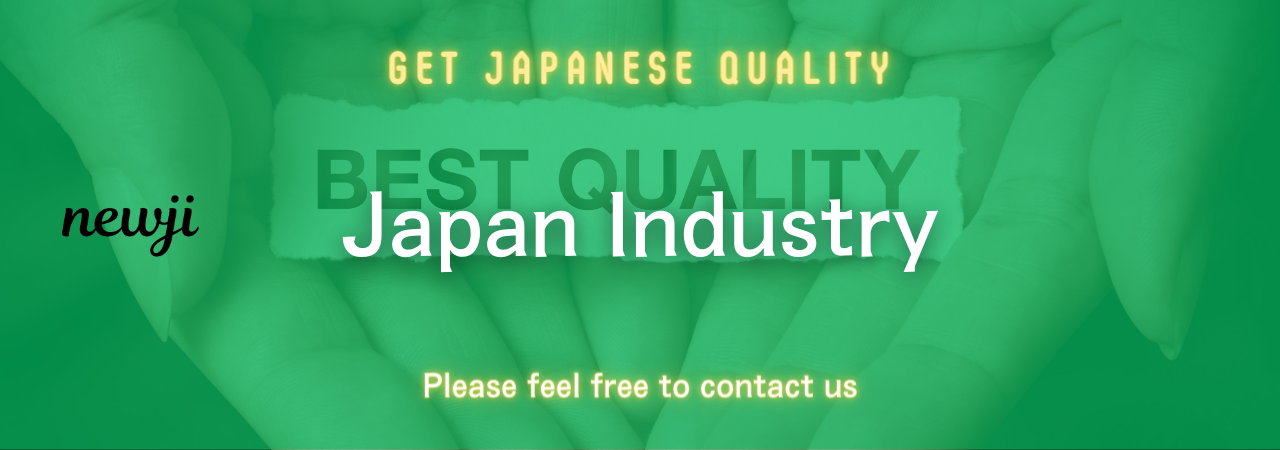
Electroplating and chemical plating are two popular methods used to coat surfaces with a thin layer of metal.
Although they may sound quite similar, they have distinct differences in their processes, applications, and benefits.
In this article, we will delve into the details of each method, explain their advantages, and help you understand which one might be the best fit for a particular application.
目次
What is Electroplating?
Electroplating is a process in which a thin layer of metal is deposited onto the surface of an object using an electric current.
This method involves immersing the object to be plated in an electrolyte solution containing metal ions.
The Electroplating Process
The process starts with cleaning the object to ensure that it is free from any dirt, oil, or oxidation.
Once cleaned, the object, also known as the cathode, is placed into the electrolyte solution.
An anode made of the metal to be deposited is also immersed in the solution.
When an electric current is applied, metal ions from the anode dissolve in the solution and are attracted to the cathode.
These ions then adhere to the surface of the object, forming a thin and even layer of metal.
Advantages of Electroplating
Electroplating offers several benefits that make it a popular choice in various industries.
One of the main advantages is enhanced corrosion resistance.
Coating a metal object with another type of metal can protect it from rust and other forms of corrosion.
Additionally, electroplating can improve the appearance of an object by making it shinier and more aesthetically pleasing.
It also enhances the electrical conductivity of the object, which is beneficial in electronic applications.
Lastly, electroplating can increase the hardness and durability of the surface, extending the lifespan of the object.
What is Chemical Plating?
Chemical plating, also known as electroless plating, is a method where a metal coating is deposited onto a surface through a chemical reaction.
Unlike electroplating, this process does not require an electric current.
The Chemical Plating Process
The chemical plating process also starts with thoroughly cleaning the object.
The clean object is then placed into a solution containing metal ions and a reducing agent.
The reducing agent causes the metal ions to be deposited onto the surface of the object through a chemical reaction.
This results in a uniform and even layer of metal coating the object.
Advantages of Chemical Plating
Chemical plating has its own unique set of benefits.
One of the primary advantages is that it provides an even coating, even on complex shapes and hard-to-reach areas.
This is because the process relies on chemical reactions rather than electrical current.
This method is also advantageous for coating non-conductive materials such as plastics.
Since it does not require an electric current, chemical plating can coat objects that would otherwise be challenging to plate using electroplating.
Furthermore, chemical plating offers excellent wear resistance and adhesion properties.
This makes it suitable for high-wear applications where durability is critical.
Comparing Electroplating and Chemical Plating
Now that we have a basic understanding of electroplating and chemical plating, let’s compare the two methods in more detail.
Complexity and Equipment
Electroplating requires a power source to generate the electric current, as well as specific anodes depending on the metal being used for plating.
This adds a level of complexity to the setup and maintenance of electroplating equipment.
Chemical plating, on the other hand, relies solely on chemical reactions and does not need a power source.
This can simplify the equipment and setup required, making it easier for smaller operations or hobbyists to get started.
Surface Compatibility
Electroplating primarily works with conductive materials such as metals.
It is challenging to use electroplating on non-conductive surfaces.
In contrast, chemical plating can be used on a variety of materials, including non-conductive surfaces like plastics.
This makes chemical plating more versatile in terms of the types of materials that can be coated.
Coating Uniformity
While electroplating can provide a good finish, it may struggle with achieving uniformity on complex shapes.
High current density areas may receive thicker deposits, while recessed areas may end up with thinner coatings.
Chemical plating excels in providing a uniform coating, even on intricate and complex surfaces.
Since the coating is deposited through a chemical reaction rather than electrical means, it results in a more consistent layer.
Cost Considerations
The cost factors for these two methods can also vary.
Electroplating may be more costly due to the need for electrical equipment and the consumption of electrical energy.
Chemical plating may lower costs by eliminating the need for a power source, but it may require more careful handling of chemicals.
Both methods have their own specific material and labor costs to consider based on the complexity and scale of the application.
Choosing the Right Method
Deciding between electroplating and chemical plating depends on the specific requirements of the task at hand.
If the objective is to coat conductive materials, improve appearance, or enhance electrical conductivity, electroplating may be the better option.
It is widely used in industries such as electronics, automotive, and jewelry.
However, if uniform coating on complex shapes or non-conductive materials is required, chemical plating may be the more suitable choice.
Industries such as aerospace, medical devices, and plastic manufacturing often rely on chemical plating for its reliability and versatility.
In conclusion, both electroplating and chemical plating have their unique strengths and applications.
Understanding the differences between these two methods can help you select the appropriate plating technique for your specific needs.
資料ダウンロード
QCD調達購買管理クラウド「newji」は、調達購買部門で必要なQCD管理全てを備えた、現場特化型兼クラウド型の今世紀最高の購買管理システムとなります。
ユーザー登録
調達購買業務の効率化だけでなく、システムを導入することで、コスト削減や製品・資材のステータス可視化のほか、属人化していた購買情報の共有化による内部不正防止や統制にも役立ちます。
NEWJI DX
製造業に特化したデジタルトランスフォーメーション(DX)の実現を目指す請負開発型のコンサルティングサービスです。AI、iPaaS、および先端の技術を駆使して、製造プロセスの効率化、業務効率化、チームワーク強化、コスト削減、品質向上を実現します。このサービスは、製造業の課題を深く理解し、それに対する最適なデジタルソリューションを提供することで、企業が持続的な成長とイノベーションを達成できるようサポートします。
オンライン講座
製造業、主に購買・調達部門にお勤めの方々に向けた情報を配信しております。
新任の方やベテランの方、管理職を対象とした幅広いコンテンツをご用意しております。
お問い合わせ
コストダウンが利益に直結する術だと理解していても、なかなか前に進めることができない状況。そんな時は、newjiのコストダウン自動化機能で大きく利益貢献しよう!
(Β版非公開)