- お役立ち記事
- Manufacturing Process of Lighting Fixtures and Electrical Wiring Assembly
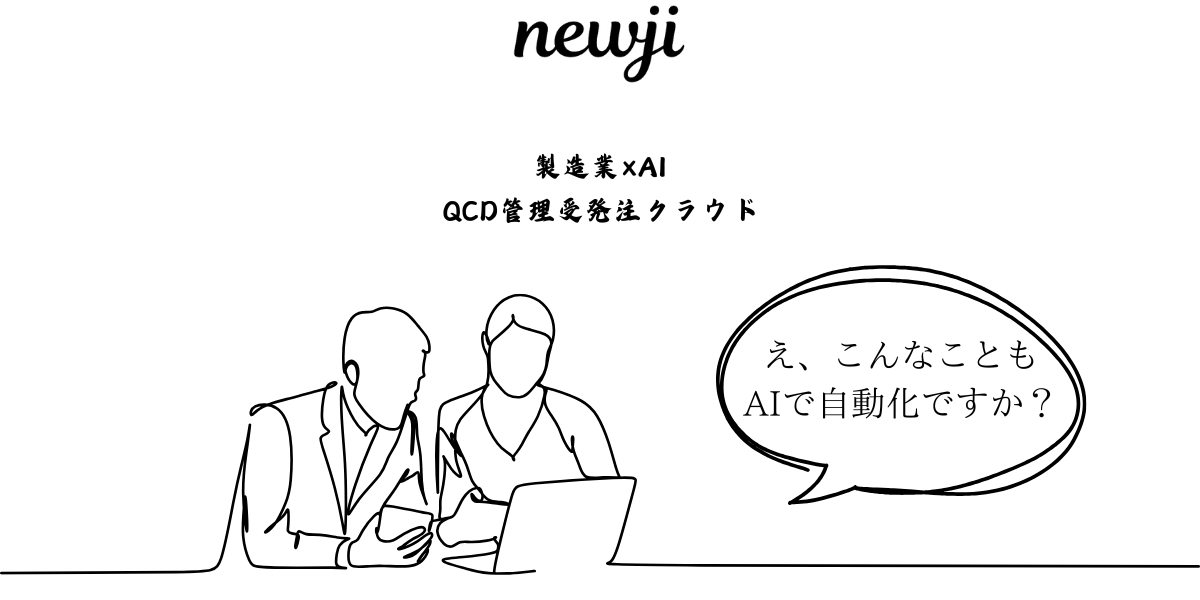
Manufacturing Process of Lighting Fixtures and Electrical Wiring Assembly
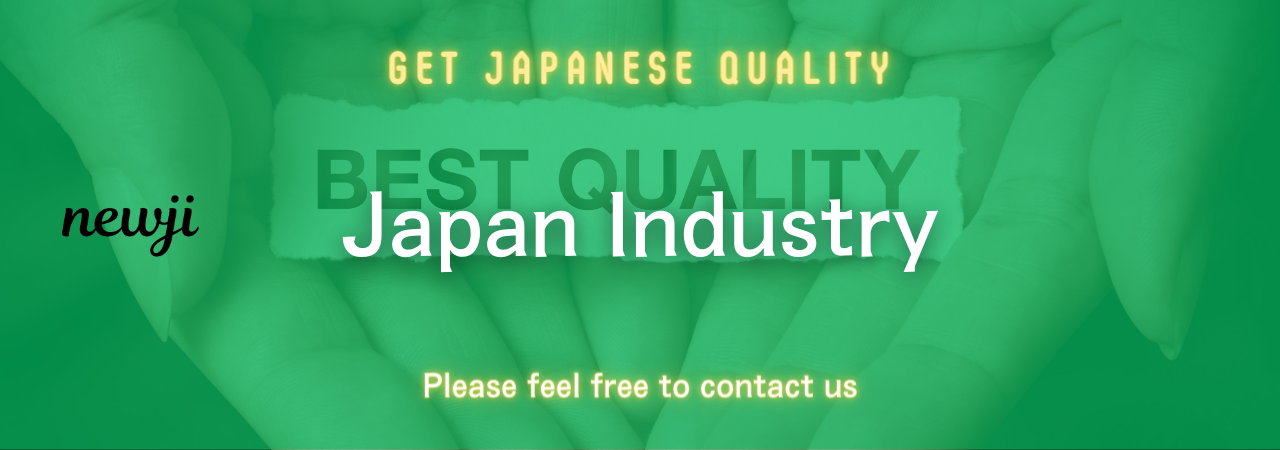
Lighting fixtures and electrical wiring are essential components of our daily lives.
We use them in our homes, workplaces, and public spaces to illuminate our surroundings and ensure safety.
This article will take you through the manufacturing process of lighting fixtures and the assembly of electrical wiring.
Understanding these processes not only gives you insight into what goes into the products you use daily but also enhances your appreciation for the engineering involved.
目次
The Manufacturing Process of Lighting Fixtures
Design and Planning
The first step in manufacturing lighting fixtures is the design phase.
Engineers and designers collaborate to create functional, stylish, and energy-efficient products.
They use specialized software to draft 3D models and blueprints of the fixtures.
This planning stage also involves selecting the right materials, such as metals, plastics, and glass, based on the desired properties and aesthetics of the final product.
Material Selection and Procurement
Once the design is finalized, the next step is material procurement.
Manufacturers source high-quality materials to ensure the durability and performance of the lighting fixtures.
This may involve working with various suppliers to obtain metals like aluminum or steel, glass for lampshades, and electrical components.
Quality control is crucial at this stage to ensure that all materials meet the specified standards.
Cutting and Shaping
With materials on hand, the next phase involves cutting and shaping them into the required components.
This can be achieved using various techniques such as laser cutting, CNC machining, and stamping.
These methods allow for precise shaping and high-quality finishes.
For example, metal components might be cut into intricate shapes, while plastic parts may be molded to adhere to the design specs.
Assembly
After cutting and shaping the components, the next step is the assembly process.
Skilled workers or automated machines put together all parts to form the complete fixture.
This process may involve welding, bolting, or screwing parts together.
In some cases, assembly lines are used to ensure efficiency and consistency across large production runs.
The fixtures are then tested to ensure they meet the required illumination levels and safety standards.
Finishing
The next step is finishing, which adds aesthetic touches and protective coatings to the fixtures.
Finishing techniques include painting, powder coating, and anodizing.
These processes not only enhance the appearance but also protect against corrosion and wear.
For instance, powder coating provides a durable and colorful finish, while anodizing adds a protective layer to metal surfaces.
Quality Control and Testing
Quality control is an integral part of the manufacturing process.
Each fixture undergoes rigorous testing to ensure it meets safety and performance standards.
This includes electrical testing, stress testing, and environmental testing.
Manufacturers conduct various inspections to identify and rectify any defects.
Only when a fixture passes all tests is it cleared for packaging and distribution.
Electrical Wiring Assembly
Design and Planning
Similar to lighting fixtures, electrical wiring assembly begins with a design phase.
Engineers draft detailed schematics and layouts to map out the wiring configuration.
Considerations include the type of wiring, insulation requirements, and safety standards.
This planning phase also involves selecting appropriate materials like copper wires, insulators, and connectors.
Material Selection and Procurement
Once the design is set, the next step is procuring the necessary materials.
High-quality copper wires are often chosen for their excellent conductivity.
Insulation materials like PVC or rubber are selected to protect against electrical hazards.
Connectors, switches, and other components are also sourced during this stage.
Cutting and Stripping Wires
The next phase involves cutting the wires to the required lengths and stripping their ends.
Specialized machinery is used for precise cutting and stripping.
This ensures that each wire meets the exact specifications outlined in the design.
Proper handling at this stage is crucial to avoid damaging the wires.
Crimping and Soldering
After cutting and stripping, the next steps are crimping and soldering.
Crimping involves attaching connectors to the wire ends using a crimping tool.
This ensures a secure connection that can handle electrical loads.
Soldering involves using a soldering iron to fuse wires and connectors.
This step ensures robust electrical connections that are less prone to failure.
Harness Assembly
In many applications, individual wires are bundled together to form wire harnesses.
This makes installation easier and more efficient.
Harness assembly involves organizing wires according to the design layout and binding them with ties, clamps, or sleeves.
This step reduces clutter and enhances the overall appearance and safety of the electrical system.
Testing and Quality Control
Quality control is vital in electrical wiring assembly.
Each wire, connector, and harness undergoes rigorous testing to ensure it meets safety and performance standards.
Tests include continuity testing, insulation resistance testing, and high-voltage testing.
Any defects are identified and corrected before the wiring assembly is approved for use.
Conclusion
The manufacturing process of lighting fixtures and the assembly of electrical wiring are intricate and precise.
Each step, from design to quality control, ensures that the final products are safe, efficient, and reliable.
Understanding these processes deepens our appreciation for the everyday tools that illuminate our lives and power our devices.
By prioritizing quality and precision, manufacturers ensure that their products meet the highest standards of safety and performance.
資料ダウンロード
QCD調達購買管理クラウド「newji」は、調達購買部門で必要なQCD管理全てを備えた、現場特化型兼クラウド型の今世紀最高の購買管理システムとなります。
ユーザー登録
調達購買業務の効率化だけでなく、システムを導入することで、コスト削減や製品・資材のステータス可視化のほか、属人化していた購買情報の共有化による内部不正防止や統制にも役立ちます。
NEWJI DX
製造業に特化したデジタルトランスフォーメーション(DX)の実現を目指す請負開発型のコンサルティングサービスです。AI、iPaaS、および先端の技術を駆使して、製造プロセスの効率化、業務効率化、チームワーク強化、コスト削減、品質向上を実現します。このサービスは、製造業の課題を深く理解し、それに対する最適なデジタルソリューションを提供することで、企業が持続的な成長とイノベーションを達成できるようサポートします。
オンライン講座
製造業、主に購買・調達部門にお勤めの方々に向けた情報を配信しております。
新任の方やベテランの方、管理職を対象とした幅広いコンテンツをご用意しております。
お問い合わせ
コストダウンが利益に直結する術だと理解していても、なかなか前に進めることができない状況。そんな時は、newjiのコストダウン自動化機能で大きく利益貢献しよう!
(Β版非公開)