- お役立ち記事
- FMEAとFTAの違い
FMEAとFTAの違い
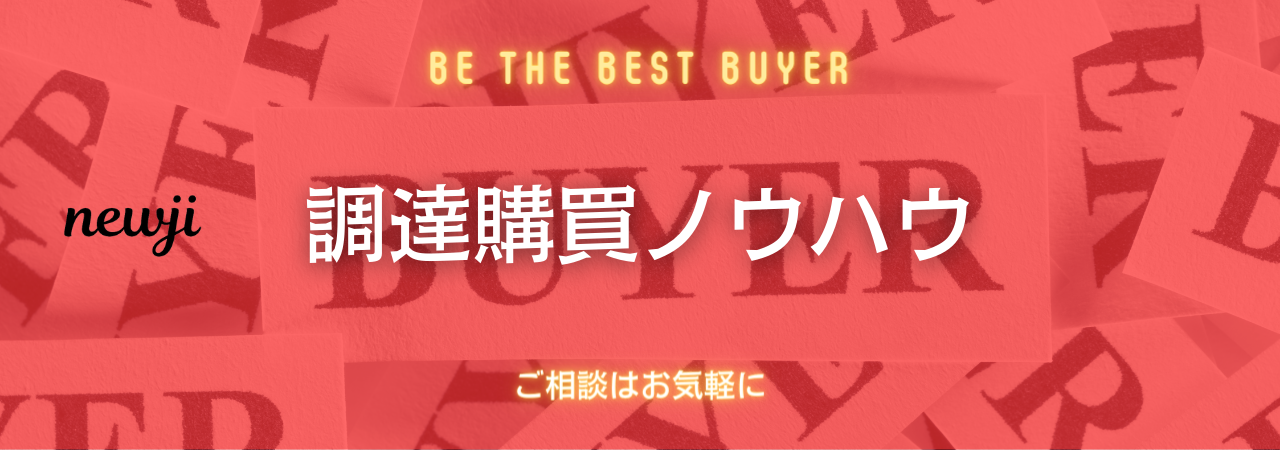
目次
FMEAとFTAの違いとは?
製造業の現場では、品質管理やリスク評価の手法が非常に重要です。
その中でも特に注目されているのがFMEA(Failure Mode and Effects Analysis)とFTA(Fault Tree Analysis)です。
この二つの手法は、いずれもリスクの特定と管理に役立ちますが、そのアプローチや目的には違いがあります。
本記事では、FMEAとFTAの違いについて具体的な事例や最新の技術動向を交えながら詳しく解説していきます。
FMEAとは?
FMEAの基本概念
FMEAは、日本語で「故障モード影響解析」と呼ばれる手法です。
主に設計や製造プロセスにおける潜在的な故障モードを洗い出し、それが製品やプロセスに与える影響を評価します。
これにより、発生する可能性の高い問題を事前に特定し、対策を講じることが可能です。
FMEAの実施方法
FMEAの実施は、以下のステップに分けて行われます。
まず、対象となる製品やシステムを詳細に理解し、それを構成する各コンポーネントやプロセスをリストアップします。
次に、それぞれのコンポーネントに関して起こり得る故障モードを特定します。
その後、それぞれの故障モードがシステム全体に与える影響を評価し、リスクの大きさを数値として算出します。
最後に、高リスクの項目に対して具体的な対策を検討します。
FMEAの利点と課題
FMEAの最大の利点は、故障の原因や影響を事前に把握し、適切な対策を講じることで品質向上を図れる点にあります。
また、リスクが高い箇所を数値化して明確にすることで、エンジニアやマネジメント層の間で共有しやすくなります。
一方で、FMEAの課題としては、詳細な解析を行うためには多くのリソースと時間が必要である点が挙げられます。
FTAとは?
FTAの基本概念
FTAは「フォールトツリー解析」とも呼ばれ、故障や不具合の原因をツリー形式で視覚化する手法です。
この解析方法は、特に複雑なシステムやプロセスでの使用に適しています。
主に故障や事故が発生した場合に、その原因を特定し、再発防止策を検討するために用いられます。
FTAの実施方法
FTAの実施は、大きく以下のステップに分けられます。
最初に、解析の対象となるトップレベルのイベントを定義します。
次に、そのイベントを引き起こす可能性のある全ての原因を分解し、ツリー状に組織化します。
最後に、各原因の発生確率を評価し、全体のリスクを算出します。
FTAの利点と課題
FTAの最大の利点は、原因と結果の関係を明確に視覚化できる点にあります。
これにより、複雑なシステムでも効率的に問題解決が可能です。
また、原因を詳細に分解することで、再発防止策の検討が容易になります。
しかし、FTAの課題としては、解析の精度がデータの質に強く依存する点や、ツリーが複雑になりすぎる場合は管理が難しくなる点が挙げられます。
FMEAとFTAの主な違い
では、FMEAとFTAの主な違いをいくつかの観点から比較してみましょう。
アプローチの違い
まず、アプローチの違いです。
FMEAは「ボトムアップ」アプローチを採用しており、各コンポーネントやプロセスの詳細を分析し、全体に及ぼす影響を評価します。
一方、FTAは「トップダウン」アプローチを採用し、故障や事故のトップレベルのイベントから始めてその原因を分解していきます。
目的の違い
FMEAの目的は、設計や製造プロセスにおける潜在的な問題を事前に特定し、未然に防ぐことです。
それに対して、FTAの目的は、発生した故障や事故の原因を特定し、再発防止策を講じることです。
適用範囲の違い
FMEAは、主に製品設計や製造プロセスに適用され、問題が発生する前にリスクを特定するために使用されます。
FTAは、主にシステム全体や大規模なプロジェクトに適用され、発生した故障や事故の原因を分析するために使用されます。
結果の視覚化の違い
FMEAは、各コンポーネントやプロセスの故障モードとその影響をリスト形式で整理します。
FTAは、故障や事故の原因をツリー形式で視覚化するため、視覚的なインパクトが大きいと言えます。
最新の技術動向
AIとデータ解析の活用
最近では、AIとデータ解析を活用したFMEAやFTAの手法が注目されています。
具体的には、ビッグデータを解析して潜在的なリスクを自動で検出する技術や、AIを活用して故障モードの影響を予測する技術が開発されています。
これにより、解析の精度や効率が大幅に向上しています。
クラウドベースのツールの普及
クラウドベースのFMEAやFTAツールも増えてきています。
これらのツールは、複数のエンジニアやマネジメント層がリアルタイムで情報を共有できるため、効率的なリスク管理が可能です。
また、クラウド環境でのデータ保存や自動バックアップも行えるため、データの管理も容易になります。
まとめ
FMEAとFTAは、いずれも製造業におけるリスク管理や品質向上に欠かせない手法ですが、そのアプローチや目的には明確な違いがあります。
FMEAはボトムアップアプローチで問題の未然防止を目指し、FTAはトップダウンアプローチで発生した問題の原因を特定します。
最新の技術動向を取り入れることで、これらの手法の精度や効率はさらに向上しています。
製造現場でのリスク管理には、状況に応じて最適な手法を選び、効果的に活用することが重要です。
資料ダウンロード
QCD調達購買管理クラウド「newji」は、調達購買部門で必要なQCD管理全てを備えた、現場特化型兼クラウド型の今世紀最高の購買管理システムとなります。
ユーザー登録
調達購買業務の効率化だけでなく、システムを導入することで、コスト削減や製品・資材のステータス可視化のほか、属人化していた購買情報の共有化による内部不正防止や統制にも役立ちます。
NEWJI DX
製造業に特化したデジタルトランスフォーメーション(DX)の実現を目指す請負開発型のコンサルティングサービスです。AI、iPaaS、および先端の技術を駆使して、製造プロセスの効率化、業務効率化、チームワーク強化、コスト削減、品質向上を実現します。このサービスは、製造業の課題を深く理解し、それに対する最適なデジタルソリューションを提供することで、企業が持続的な成長とイノベーションを達成できるようサポートします。
オンライン講座
製造業、主に購買・調達部門にお勤めの方々に向けた情報を配信しております。
新任の方やベテランの方、管理職を対象とした幅広いコンテンツをご用意しております。
お問い合わせ
コストダウンが利益に直結する術だと理解していても、なかなか前に進めることができない状況。そんな時は、newjiのコストダウン自動化機能で大きく利益貢献しよう!
(Β版非公開)