- お役立ち記事
- シックスシグマとリーン生産方式の違い
シックスシグマとリーン生産方式の違い
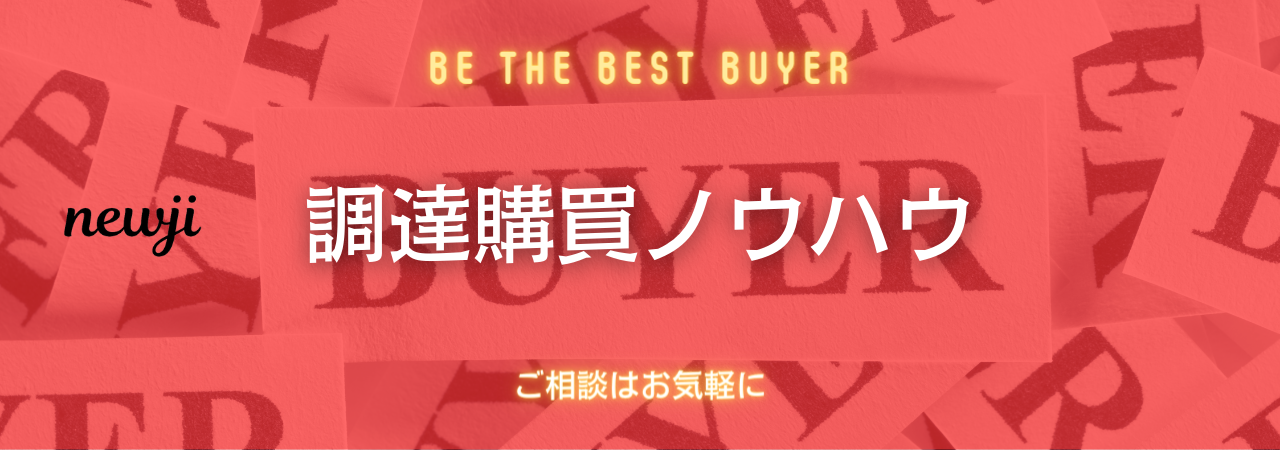
目次
シックスシグマとリーン生産方式の基本概念
シックスシグマとリーン生産方式は、どちらも製造業におけるプロセス改善のための手法として広く認識されています。
しかし、この二つにはそれぞれ異なるアプローチや目的があります。
シックスシグマの基本概念
シックスシグマは、1980年代にモトローラによって開発された品質管理の手法です。
主な目的は、プロセスのばらつきを減らし、欠陥を極力排除することです。
シックスシグマは、統計学的手法を用いてデータを分析し、問題点を特定し、持続可能な解決方法を提供します。
この手法はDMAIC(定義、計測、分析、改善、制御)というフレームワークに基づいて進められます。
リーン生産方式の基本概念
一方、リーン生産方式は、1940年代後半にトヨタによって開発された生産管理の手法です。
主な目的は、無駄を排除し、効率を最大化することです。
この手法は、プロセスの中で「価値を生み出さない行動」(ムダ)を取り除くことに焦点を当てています。
価値の流れを改善し、顧客に価値を提供するスピードを上げることで、全体の生産性を向上させます。
目的とアプローチの違い
シックスシグマとリーン生産方式は、それぞれ異なる目的とアプローチを持っています。
シックスシグマの目的とアプローチ
シックスシグマの主な目的は、プロセスのばらつきを減らし、高品質の製品を提供することです。
このため、データ駆動のアプローチを取ります。
統計的な分析手法を用い、プロセスの中で発生するばらつきや欠陥の根本原因を特定し、それに対して効果的な改善策を講じます。
リーン生産方式の目的とアプローチ
一方、リーン生産方式の主な目的は、価値を生まない活動を排除し、プロセス全体のフローを改善することです。
このため、「ムダ」を識別し、排除することに焦点を当てます。
リーンでは、PDSA(計画、実行、評価、改善)サイクルを用いて継続的にプロセスを改善します。
手法の違い
シックスシグマとリーン生産方式では、使用するツールや手法にも違いがあります。
シックスシグマのツールと手法
シックスシグマでは、主に以下のようなツールや手法が使用されます:
– **DMAICフレームワーク**:プロジェクトの進行を体系的にステップバイステップで進めるフレームワークです。
– **統計的プロセス制御(SPC)**:プロセスのばらつきをリアルタイムで監視し、異常を早期に検出します。
– **FMEA(Failure Modes and Effects Analysis)**:潜在的な故障モードとその影響を評価し、リスクを低減します。
– **回帰分析**:複数の変数間の関係を解析し、プロセスの予測を行います。
リーン生産方式のツールと手法
リーン生産方式では、主に以下のようなツールや手法が使用されます:
– **5S活動**:整理、整頓、清掃、清潔、しつけの5つの要素から成り立ち、職場環境の整備を行います。
– **カイゼン**:継続的な改善を意味し、現場での小さな改善を積み重ねていきます。
– **バリューストリームマッピング(VSM)**:プロセス全体の流れを視覚的に表現し、ムダを識別します。
– **ジャストインタイム(JIT)**:必要なものを必要な時に、必要な量だけ生産し、在庫を最小限に抑えます。
組織への影響と導入の違い
シックスシグマとリーン生産方式は、組織に与える影響や導入のしやすさにおいても違いがあります。
シックスシグマの組織への影響と導入
シックスシグマは、データ駆動のアプローチであり、専門知識が求められます。
そのため、シックスシグマのマスター・ブラックベルトやブラックベルトなどの専門家が必要です。
この手法は、比較的大規模な組織での導入に向いており、初期投資やトレーニングコストがかかります。
しかし、一度導入されれば、プロセスのばらつきを減少させ、品質を大幅に向上させることが可能です。
リーン生産方式の組織への影響と導入
一方、リーン生産方式は、全社員が参加できる比較的簡便な手法です。
全員がムダを識別し、それを排除するための改善活動に参加することが求められます。
導入コストが低く、特に小規模な組織でも手軽に導入できるのが特徴です。
また、リーンは即効性が高く、短期間で生産性を向上させることが可能です。
実際の現場での適用事例
最後に、シックスシグマとリーン生産方式の実際の現場での適用事例を紹介します。
シックスシグマの適用事例
ある大手電子部品メーカーでは、シックスシグマを導入して不良品率の大幅な削減に成功しました。
DMAICフレームワークを使用し、欠陥の根本原因を特定し、統計的手法を用いてプロセス改善を行いました。
その結果、不良品率が6%から0.5%に減少し、年間数億円のコスト削減を実現しました。
リーン生産方式の適用事例
一方、ある自動車部品メーカーでは、リーン生産方式を導入して生産ラインの効率を向上させました。
5S活動を通じて職場環境を整備し、バリューストリームマッピングを用いてムダを識別しました。
その結果、リードタイムが50%短縮され、在庫コストが大幅に削減されました。
まとめ
シックスシグマとリーン生産方式は、それぞれ異なるアプローチと目的を持ち、製造業におけるプロセス改善に寄与しています。
シックスシグマは品質の向上に焦点を当て、データ駆動のアプローチを取ります。
一方、リーン生産方式は効率の向上に焦点を当て、ムダの排除を目指します。
どちらの手法も、それぞれの組織やプロジェクトの特性に応じて選択し、適用することが重要です。
両手法の特徴と適用方法を理解することで、製造業の現場での効果的なプロセス改善が可能となり、競争力の向上につながります。
資料ダウンロード
QCD調達購買管理クラウド「newji」は、調達購買部門で必要なQCD管理全てを備えた、現場特化型兼クラウド型の今世紀最高の購買管理システムとなります。
ユーザー登録
調達購買業務の効率化だけでなく、システムを導入することで、コスト削減や製品・資材のステータス可視化のほか、属人化していた購買情報の共有化による内部不正防止や統制にも役立ちます。
NEWJI DX
製造業に特化したデジタルトランスフォーメーション(DX)の実現を目指す請負開発型のコンサルティングサービスです。AI、iPaaS、および先端の技術を駆使して、製造プロセスの効率化、業務効率化、チームワーク強化、コスト削減、品質向上を実現します。このサービスは、製造業の課題を深く理解し、それに対する最適なデジタルソリューションを提供することで、企業が持続的な成長とイノベーションを達成できるようサポートします。
オンライン講座
製造業、主に購買・調達部門にお勤めの方々に向けた情報を配信しております。
新任の方やベテランの方、管理職を対象とした幅広いコンテンツをご用意しております。
お問い合わせ
コストダウンが利益に直結する術だと理解していても、なかなか前に進めることができない状況。そんな時は、newjiのコストダウン自動化機能で大きく利益貢献しよう!
(Β版非公開)