- お役立ち記事
- Smart Sensors and IoT Spinning the Future of Manufacturing
Smart Sensors and IoT Spinning the Future of Manufacturing
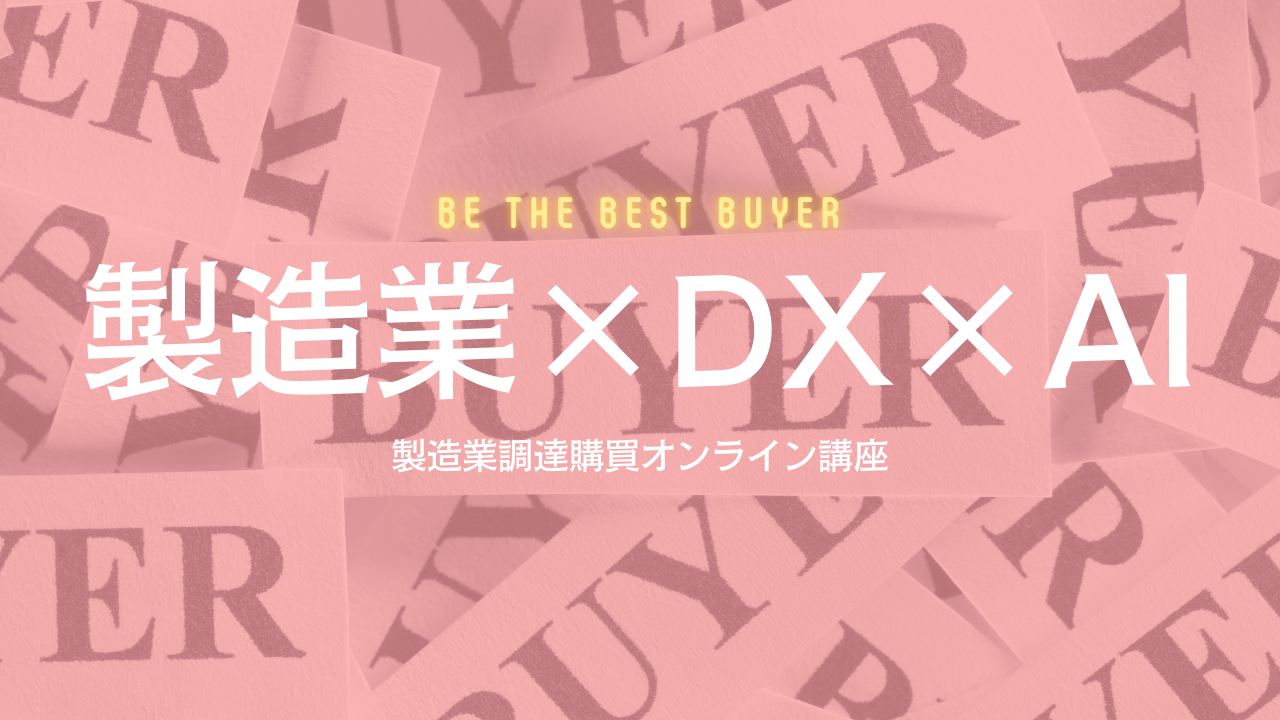
The manufacturing industry has always been at the forefront of innovation and technological advancement. From the Industrial Revolution automating repetitive processes to the computer age streamlining operations with software, manufacturing has continuously taken advantage of new technologies to strengthen productivity and quality. Now, a new paradigm is poised to transform manufacturing yet again – the Industrial Internet of Things (IIoT) powered by smart sensors.
Smart sensors allow machines, products and components to communicate digitally, enabling a much more connected and data-driven approach to manufacturing. Sensor technology has advanced rapidly in recent years, becoming smaller, cheaper and more reliable. When networked through an IIoT platform, smart sensors generate vast amounts of real-time operational data that provides unprecedented visibility into industrial processes. Manufacturers can now monitor production lines, assets and product performance like never before.
This continuous digital feedback loop unlocks many opportunities to optimize operations. Production managers have actionable insights to spot inefficiencies, prevent maintenance issues and detect quality problems earlier. Data analytics tools scour sensor readings for patterns, predicting outcomes and helping manufacturers be more proactive. Remote monitoring also reduces downtime by enabling remote troubleshooting and condition-based maintenance. With the right IIoT solutions, manufacturers gain a virtual “x-ray vision” into their own operations.
Perhaps the biggest game changer is how smart sensors enable flexible, on-demand manufacturing. Traditionally, factories were designed based on forecasts of product demand that were often inaccurate. This resulted in excess inventory or shortage situations that hurt profitability. Now manufacturers can integrate production planning directly with real-time demand signals. As orders come in, smart sensors and IIoT platforms help dynamically reallocate manufacturing resources and adjust workflows to minimize lead times. This just-in-time flexibility was not previously possible at scale.
Another new frontier is personalized manufacturing using 3D printing and smart sensors. Consumers increasingly demand customized products tailored to unique specifications. Rather than mass producing one-size-fits-all items, businesses can digitally simulate designs, program 3D printers using sensor data on materials and settings. Fluid robots work in tandem with sensors to autonomously fabricate optimized parts on demand. Production runs shrink to singles, allowing unlimited personalization options. Manufacturers effectively move from factories to micro-factories embedded throughout supply chains.
Smart sensors are also enabling predictive quality control during manufacturing. By embedding sensor technology directly into components like pumps, sensors monitor variables like pressure, vibration and temperature during operation. Data streams into IIoT platforms for real-time quality monitoring. Algorithms analyze sensor readings against design benchmarks to spot anomalies indicating potential defects. Issues can be addressed immediately before larger problems emerge. Over time, sensor data builds predictive models to flag at-risk parts and proactively prevent quality escapes. Smart products even self-diagnose during use and autonomously schedule maintenance.
Smart sensors combined with IIoT are bringing unprecedented connectivity to manufacturing plants, supply chains and finished products. This digital transformation is already bearing fruit for early adopters. A leading engine manufacturer deployed wireless sensors throughout its factories, connecting 40,000 machines to an IIoT platform. This improved overall equipment effectiveness by 20% and reduced downtime by 30%. A medical device maker uses real-time sensor data from its assembly lines for predictive quality monitoring. They’ve decreased defect rates by 70% and sped new product introductions. As technology costs fall and use cases multiply, the full potential of smart sensor and IIoT networks is just starting to be tapped. Over the next decade, they will fundamentally change the face of manufacturing.
資料ダウンロード
QCD調達購買管理クラウド「newji」は、調達購買部門で必要なQCD管理全てを備えた、現場特化型兼クラウド型の今世紀最高の購買管理システムとなります。
ユーザー登録
調達購買業務の効率化だけでなく、システムを導入することで、コスト削減や製品・資材のステータス可視化のほか、属人化していた購買情報の共有化による内部不正防止や統制にも役立ちます。
NEWJI DX
製造業に特化したデジタルトランスフォーメーション(DX)の実現を目指す請負開発型のコンサルティングサービスです。AI、iPaaS、および先端の技術を駆使して、製造プロセスの効率化、業務効率化、チームワーク強化、コスト削減、品質向上を実現します。このサービスは、製造業の課題を深く理解し、それに対する最適なデジタルソリューションを提供することで、企業が持続的な成長とイノベーションを達成できるようサポートします。
オンライン講座
製造業、主に購買・調達部門にお勤めの方々に向けた情報を配信しております。
新任の方やベテランの方、管理職を対象とした幅広いコンテンツをご用意しております。
お問い合わせ
コストダウンが利益に直結する術だと理解していても、なかなか前に進めることができない状況。そんな時は、newjiのコストダウン自動化機能で大きく利益貢献しよう!
(Β版非公開)