- お役立ち記事
- FMEAとFMECAの違い
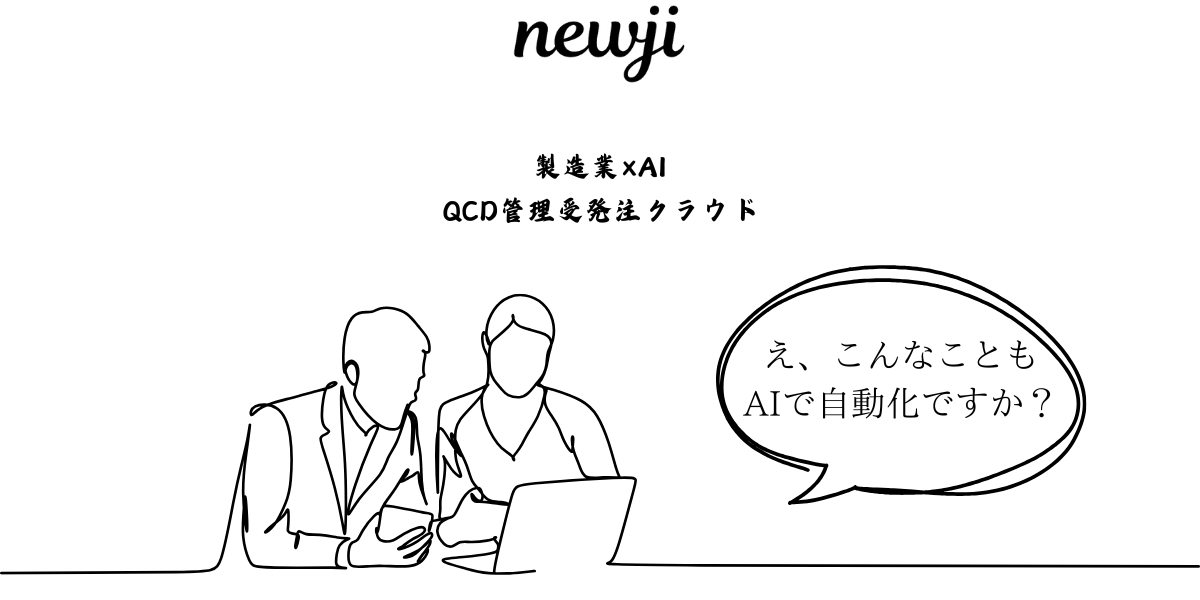
FMEAとFMECAの違い
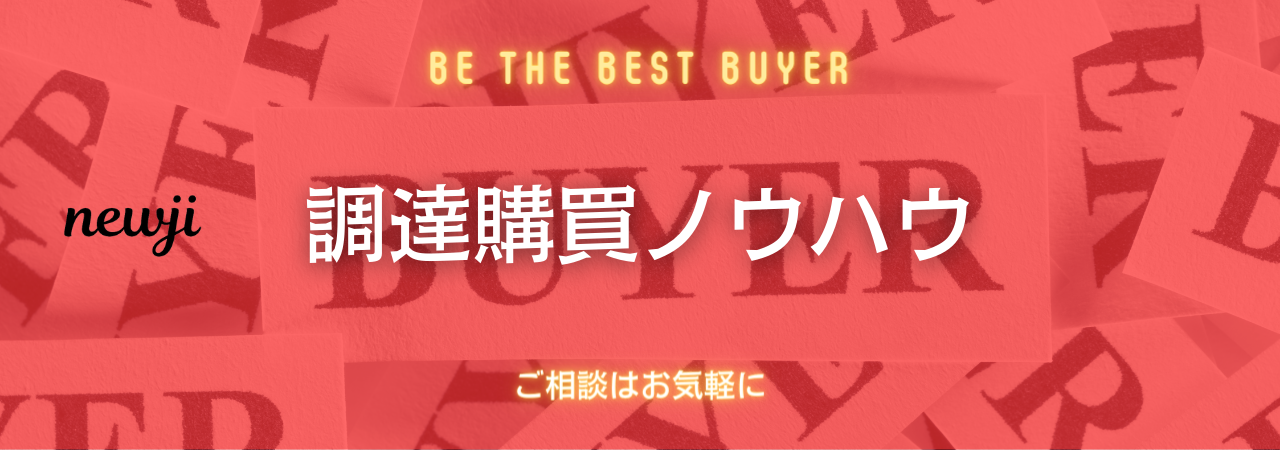
目次
はじめに
製造業の現場では、品質管理や信頼性の向上が不可欠です。
この目標を達成するための有効な手法として、FMEA(Failure Mode and Effects Analysis、故障モード影響解析)とFMECA(Failure Mode, Effects, and Criticality Analysis、故障モード影響および致命度解析)が広く利用されています。
この記事では、FMEAとFMECAの違いについて詳しく解説し、それぞれの手法がどのように使われるのかを説明します。
FMEAとは
基本概念
FMEAは、製品やプロセスがどのように故障する可能性があるか(故障モード)を分析し、その故障がどのような影響を及ぼすか(影響)を評価する手法です。
具体的には、個々の要素(部品、工程など)が故障した場合に、それがシステム全体にどのような影響を与えるかを予測します。
ステップバイステップ解析
FMEAの実施手順は以下の通りです。
1. **システムの特定**: 分析対象とするシステムや工程を明確にします。
2. **故障モードの識別**: そのシステムがどのように故障する可能性があるかをリストアップします。
3. **故障の影響評価**: 各故障モードがシステム全体に及ぼす影響を評価します。
4. **原因の特定**: 故障の原因を分析し、特定します。
5. **リスクの評価**: 故障の発生頻度や影響度を評価し、リスクの優先順位を設定します。
6. **対策の策定**: リスクを最小化するための対策を検討し、実行します。
FMECAとは
基本概念
FMECAは、FMEAに致命度の評価を加えた手法です。
致命度とは、故障が発生した際のシステム全体への影響の重大度を意味します。
この評価を加えることで、単なる故障の影響だけでなく、その影響の重大性も考慮することができます。
ステップバイステップ解析
FMECAの実施手順は以下の通りです。
1. **故障モードの特定**: FMEAと同様に、故障モードを識別します。
2. **影響の評価**: 同様に故障の影響を評価します。
3. **致命度の評価**: 各故障モードの致命度を評価し、クリティカル度(重要度)をつけます。
4. **リスクの優先順位設定**: 致命度を考慮してリスクの優先順位を設定します。
5. **対策の策定**: リスクを最小化するための効果的な対策を実行します。
FMEAとFMECAの違い
致命度評価の有無
最も大きな違いは、致命度の評価があるかないかです。
FMEAは故障モードとその影響を評価しますが、致命度については考慮しません。
一方、FMECAでは、致命度を評価し、それに基づいてリスクの優先順位を設定します。
適用範囲
FMEAは、製品設計や製造プロセスにおける一般的なリスクアセスメント手法として広く用いられます。
一方、FMECAは航空宇宙、医療機器などの高信頼性が求められる分野でよく利用されています。
これにより、クリティカルな故障モードを特定し、重点的に対策を講じることができるからです。
コストと時間
FMECAは致命度の評価を行うため、FMEAに比べてコストと時間がかかります。
しかし、致命度の高い故障を特定し、それに対応することが求められる場合、この追加の投入は価値があります。
FMEAとFMECAの実践例
FMEAの実践例
例えば、自動車のエンジン設計を考えます。
エンジンの故障モードには「ピストンの摩耗」「燃料ポンプの故障」などが考えられます。
これらの故障モードがエンジン全体に与える影響(エンジン停止、性能低下など)を評価し、故障の原因(材料の不具合、設計ミスなど)を特定します。
その後、リスクを評価し、対策を講じます(素材の見直し、設計変更など)。
FMECAの実践例
航空機エンジンの場合、致命度の評価が特に重要です。
例えば、エンジン燃料供給システムの故障モードを考えます。
燃料ポンプの故障が致命的な影響(飛行中のエンジン停止)をもたらす可能性があるため、この故障モードはFMECAで高い致命度が付けられます。
その結果、燃料ポンプの冗長化や定期点検の強化などの対策が求められます。
最新技術動向
デジタルFMEAとFMECA
現在、デジタルツールやソフトウェアを活用したFMEAとFMECAが注目されています。
これにより、故障モードの特定や影響分析が効率的に行えるだけでなく、大量のデータを迅速かつ正確に処理することが可能です。
AIと機械学習の活用
AIや機械学習を利用することで、過去のデータや現場のセンサー情報を基に、故障モードやその影響の予測精度を向上させる研究が進んでいます。
これにより、より精度の高いFMEAおよびFMECAが可能となります。
まとめ
FMEAとFMECAは、いずれも製造業におけるリスク評価と品質管理の重要な手法です。
FMEAは一般的なリスクアセスメントを行うのに適しており、FMECAは致命度の評価により高信頼性が求められる分野での活用が効果的です。
最新の技術を利用することで、これらの手法はより精度と効率が高まり、現場でのリスク管理に大いに役立つでしょう。
資料ダウンロード
QCD調達購買管理クラウド「newji」は、調達購買部門で必要なQCD管理全てを備えた、現場特化型兼クラウド型の今世紀最高の購買管理システムとなります。
ユーザー登録
調達購買業務の効率化だけでなく、システムを導入することで、コスト削減や製品・資材のステータス可視化のほか、属人化していた購買情報の共有化による内部不正防止や統制にも役立ちます。
NEWJI DX
製造業に特化したデジタルトランスフォーメーション(DX)の実現を目指す請負開発型のコンサルティングサービスです。AI、iPaaS、および先端の技術を駆使して、製造プロセスの効率化、業務効率化、チームワーク強化、コスト削減、品質向上を実現します。このサービスは、製造業の課題を深く理解し、それに対する最適なデジタルソリューションを提供することで、企業が持続的な成長とイノベーションを達成できるようサポートします。
オンライン講座
製造業、主に購買・調達部門にお勤めの方々に向けた情報を配信しております。
新任の方やベテランの方、管理職を対象とした幅広いコンテンツをご用意しております。
お問い合わせ
コストダウンが利益に直結する術だと理解していても、なかなか前に進めることができない状況。そんな時は、newjiのコストダウン自動化機能で大きく利益貢献しよう!
(Β版非公開)