- お役立ち記事
- Smart Maintenance Solutions Reducing Downtime in Manufacturing
Smart Maintenance Solutions Reducing Downtime in Manufacturing
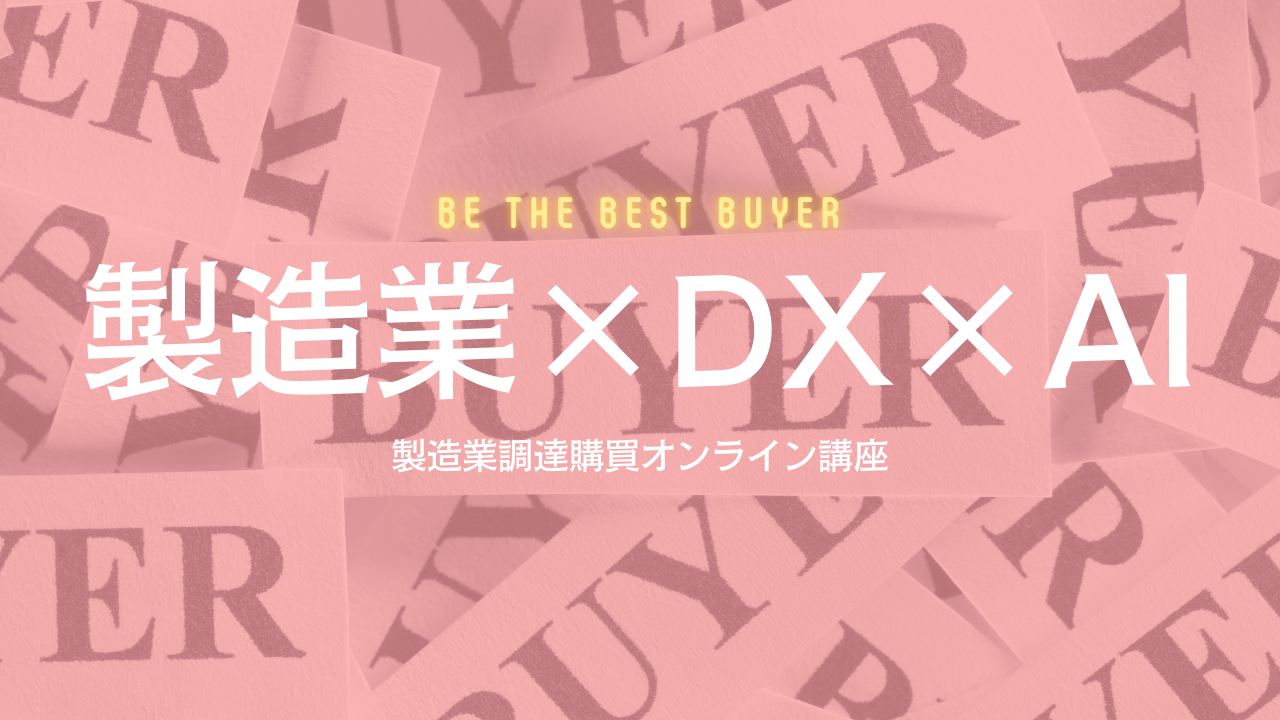
Manufacturing businesses operate around the clock to fulfill production goals and meet customer demand. However, unexpected equipment failures or unplanned downtime can cost a manufacturer thousands – even millions – of dollars per hour in lost production. Smart maintenance plays a vital role in minimizing unplanned outages and reducing costly downtime in manufacturing facilities.
Condition-based maintenance uses sensors and data analytics to actively monitor equipment performance and detect early signs of deterioration or anomalies. This predictive approach allows maintenance crews to address issues before a breakdown occurs, eliminating unexpected downtime. Systems from companies like Emerson, Siemens, Schneider Electric, and GE Digital provide remote condition monitoring of critical assets using vibration analysis, thermography, lubricant analysis, and other non-invasive techniques. Wireless sensors installed on machines transmit operational data to the cloud for analysis, flagging any deviations from normal baseline performance.
Predictive maintenance using vibration analysis is particularly effective for rotating equipment like motors, pumps, fans and compressors. Vibration levels increase as components wear and internal clearances grow larger. Monitoring vibration signatures can pinpoint the source of a developing issue, whether it’s unbalanced rotors, misaligned shafts, worn bearings, or loose components. Taking proactive action avoids a sudden catastrophic failure that stops production. Thermography cameras also detect temperature irregularities indicating electrical or mechanical faults developing within electrical panels or machine components.
Rather than fixing equipment only after it breaks down, condition monitoring enables maintenance work to be scheduled during planned downtime when spare parts are on hand. This avoids risky, unplanned repairs that extend downtime. Planned repairs are much less disruptive when factored into regular maintenance windows. Leveraging real-time usage and operational data, maintenance teams know exactly which machines need attention and when.
The move to smart, digital maintenance solutions also improves spare parts management. Tools like IBM Maximo use predictive failure dates to optimize the spare parts inventory. Only essential components likely to fail within the next maintenance cycle are stocked, avoiding wasted capital tied up in unused parts. An optimized stock eliminates delays waiting for replacements to arrive when needed most urgently. Digital twin simulations additionally help qualify new parts and avoid re-ordering the same components that continually fail prematurely.
Advanced maintenance techniques like remote diagnostics using augmented reality (AR) are gaining popularity, too. AR apps allow off-site experts to see what on-site technicians see, even diagnosing and guiding repairs in real-time. Using AR smart glasses equipped with cameras, remote assistance can visually triangulate issues and walk technicians through every step of the fix. Connection to OEM databases ensures the right repair methods are used. AR eliminates time-consuming trips by experts and speeds every maintenance process.
Big data analytics and artificial intelligence (AI) take predictive maintenance to the next level. Pattern recognition software factors in historical repair records, operational parameters, ambient conditions, and more to forecast machine reliabilities with a high degree of accuracy. Any unplanned breakdown becomes almost impossible thanks to early warnings from AI models. Self-learning algorithms also continuously refine failure predictions as more operational data becomes available over time. By autonomously monitoring fleets of equipment across multiple plant locations, AI empowers manufacturers to eliminate downtime proactively wherever issues surface.
Smart maintenance powered by IoT, big data, and AI delivers significant benefits to manufacturing organizations. Early issue detection means fewer breakdowns and less unplanned downtime for higher equipment availability and utilization. Optimized maintenance schedules increase planning certainty while targeted parts stocking minimizes capital costs. Remote monitoring and assistance technologies connect expertise more efficiently across sites. Overall, advanced digital solutions help manufacturers reliably and productively deliver quality goods on-time to customers through reduced production disruptions. When uptime becomes the top priority, smart maintenance plays a defining role in success.
資料ダウンロード
QCD調達購買管理クラウド「newji」は、調達購買部門で必要なQCD管理全てを備えた、現場特化型兼クラウド型の今世紀最高の購買管理システムとなります。
ユーザー登録
調達購買業務の効率化だけでなく、システムを導入することで、コスト削減や製品・資材のステータス可視化のほか、属人化していた購買情報の共有化による内部不正防止や統制にも役立ちます。
NEWJI DX
製造業に特化したデジタルトランスフォーメーション(DX)の実現を目指す請負開発型のコンサルティングサービスです。AI、iPaaS、および先端の技術を駆使して、製造プロセスの効率化、業務効率化、チームワーク強化、コスト削減、品質向上を実現します。このサービスは、製造業の課題を深く理解し、それに対する最適なデジタルソリューションを提供することで、企業が持続的な成長とイノベーションを達成できるようサポートします。
オンライン講座
製造業、主に購買・調達部門にお勤めの方々に向けた情報を配信しております。
新任の方やベテランの方、管理職を対象とした幅広いコンテンツをご用意しております。
お問い合わせ
コストダウンが利益に直結する術だと理解していても、なかなか前に進めることができない状況。そんな時は、newjiのコストダウン自動化機能で大きく利益貢献しよう!
(Β版非公開)