- お役立ち記事
- Digital Solutions for Sustainable Manufacturing
Digital Solutions for Sustainable Manufacturing
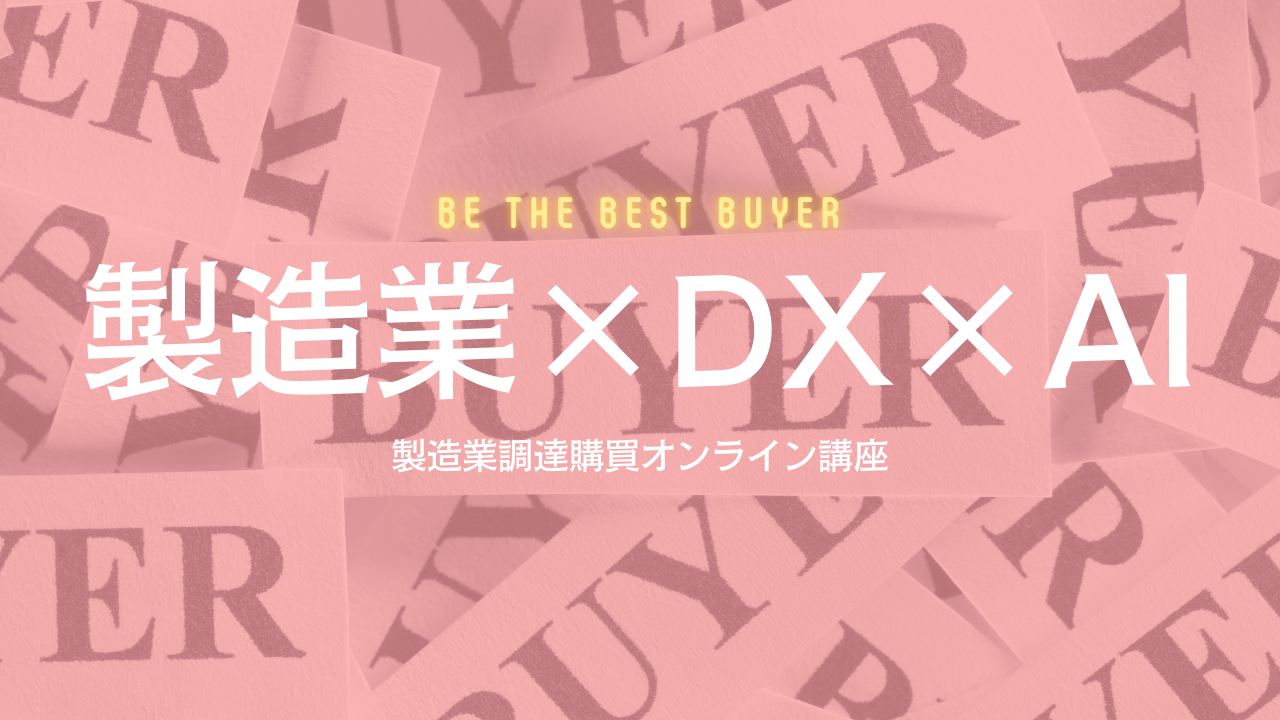
Many companies that make products are trying to be more environmentally friendly. They want to use less energy and materials to help the planet. But how can factories make products without harming the earth? Good thing scientists and engineers have come up with digital technology solutions that can help!
Digital technology refers to computers, software programs, robots, sensors and more that use electronics and code instead of physical things.
Some common digital solutions that can help factories be more sustainable, or eco-friendly, include:
Automated Processes and Robotics
Robots and computer-controlled machines can now do many of the tasks in a factory that used to be done by people. This means factories don’t need as many human workers to run. It also means the processes can be more precise and wasteful steps can be eliminated. Robots and machines don’t get tired or make as many mistakes as people, so less materials have to be used to make products. Sensors on robots can also track exactly how much of each material is needed at each step to cut down on waste.
Computer Monitoring and Control Systems
Factories now have computer systems that remotely monitor and control the whole manufacturing process. High-tech sensors are installed throughout the factory to track things like temperature, pressure, material levels and more. If any readings go outside the normal range, the computer can automatically adjust equipment settings to fix the problem and prevent wasted batches of products or materials. Control systems also optimize energy use by powering down unused machinery.
Additive Manufacturing
New 3D printing and additive manufacturing technologies allow products to be “grown” one super thin layer at a time from digital design files. This replaces manufacturing methods that cut away or form materials into shapes. 3D printing uses much less material waste compared to traditional methods. It also gives designers more flexibility to create complex shapes and parts that can combine multiple functions into a single component, further cutting down on materials and assembly steps needed.
Big Data Analytics and Artificial Intelligence
Factories collect huge amounts of data from sensors, machines and production records. Specialized software uses techniques like machine learning, predictive analysis and pattern recognition on all this “big data”. The analytics can find hidden connections and insights to continuously improve processes. AI and big data help optimize material usage, energy consumption, machine maintenance schedules and more to eliminate inefficiencies. They predict problems before they happen too so factories can be more proactive instead of reactive.
Virtual Prototyping and Simulation
Computer-aided design (CAD) and virtual reality (VR) simulations let factory engineers test and refine product designs and manufacturing workflows completely digitally before building expensive physical prototypes or retooling assembly lines. Any design flaws or inefficient processes can be detected and fixed in the virtual world to minimize costly real-world mistakes. Simulations also help train workers on new equipment without risk of accidents. Digital prototyping saves tons of material that would have been wasted on physical design iterations.
Cloud Computing Infrastructure
Storing factory data and running software programs in remote data centers through high-speed internet connections, known as cloud computing, drastically cuts a plant’s energy needs compared to running applications locally on high-power on-site servers and storage devices. Cloud infrastructure is also more affordable and flexible than owning physical IT equipment. Manufacturers only “rent” the exact computing power they need through simple online software-as-a-service subscriptions. This optimizes costs. The cloud also allows seamless collaboration and data-sharing between different teams and global factories.
As you can see, digital innovations are enabling greener, more intelligent manufacturing solutions. Factories of the future will rely heavily on technologies like robotics, AI systems, 3D printing, VR simulations and cloud computing to produce goods with maximum resource efficiency and minimal waste. With digital help, sustainable manufacturing practices can become widespread, benefitting both businesses and the environment for generations to come. These advanced technologies may seem like science fiction, but they are already hard at work behind the scenes of many products we see and use every day!
資料ダウンロード
QCD調達購買管理クラウド「newji」は、調達購買部門で必要なQCD管理全てを備えた、現場特化型兼クラウド型の今世紀最高の購買管理システムとなります。
ユーザー登録
調達購買業務の効率化だけでなく、システムを導入することで、コスト削減や製品・資材のステータス可視化のほか、属人化していた購買情報の共有化による内部不正防止や統制にも役立ちます。
NEWJI DX
製造業に特化したデジタルトランスフォーメーション(DX)の実現を目指す請負開発型のコンサルティングサービスです。AI、iPaaS、および先端の技術を駆使して、製造プロセスの効率化、業務効率化、チームワーク強化、コスト削減、品質向上を実現します。このサービスは、製造業の課題を深く理解し、それに対する最適なデジタルソリューションを提供することで、企業が持続的な成長とイノベーションを達成できるようサポートします。
オンライン講座
製造業、主に購買・調達部門にお勤めの方々に向けた情報を配信しております。
新任の方やベテランの方、管理職を対象とした幅広いコンテンツをご用意しております。
お問い合わせ
コストダウンが利益に直結する術だと理解していても、なかなか前に進めることができない状況。そんな時は、newjiのコストダウン自動化機能で大きく利益貢献しよう!
(Β版非公開)