- お役立ち記事
- The difference between 3S and 5S
The difference between 3S and 5S
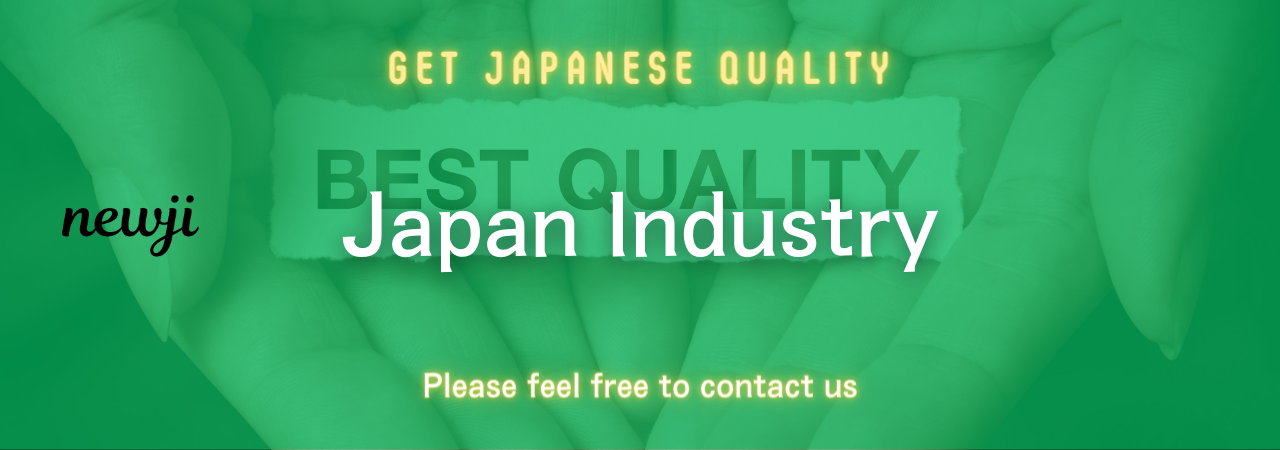
When it comes to improving workplace efficiency and organization, the concepts of 3S and 5S are often discussed.
These methodologies originated in Japan and have become popular worldwide due to their effectiveness.
But what exactly are 3S and 5S, and how do they differ from one another?
Let’s take a closer look at these systems, their definitions, and their benefits.
目次
Understanding 3S
What is 3S?
The 3S methodology focuses on three key practices: Seiri (Sort), Seiton (Set in Order), and Seiso (Shine).
These practices are designed to create a clean, organized, and efficient work environment.
Details of Each S in 3S
– **Seiri (Sort):**
The first step involves sorting through all items in the workplace and removing unnecessary ones.
This helps eliminate clutter and make the workspace more efficient.
– **Seiton (Set in Order):**
In this step, the remaining items are organized logically and systematically.
Tools and materials are arranged in a way that maximizes efficiency and minimizes wasted time searching for items.
– **Seiso (Shine):**
The final step of 3S is to clean the workplace and keep it neat and tidy.
Regular cleaning routines are established to maintain an orderly environment.
Benefits of 3S
Implementing the 3S methodology can lead to numerous benefits, such as:
– Improved efficiency: A clutter-free and organized workspace can significantly boost productivity.
– Enhanced safety: Removing unnecessary items and keeping the area clean can reduce the risk of accidents.
– Better morale: A tidy workplace can improve employee satisfaction and morale.
Understanding 5S
What is 5S?
The 5S methodology expands upon the principles of 3S by adding two additional practices: Seiketsu (Standardize) and Shitsuke (Sustain).
These additional steps help further improve and maintain workplace organization and efficiency.
Details of Each S in 5S
– **Seiri (Sort):**
Just like in 3S, the first step in 5S involves sorting and removing unnecessary items from the workplace.
– **Seiton (Set in Order):**
The second step is to arrange the remaining items in an orderly manner to maximize efficiency.
– **Seiso (Shine):**
The third step focuses on cleaning the workspace and keeping it tidy.
– **Seiketsu (Standardize):**
This step involves creating standards and protocols to maintain the organization and cleanliness achieved through the first three steps.
This ensures consistency and helps prevent backsliding into disorder.
– **Shitsuke (Sustain):**
The final step is about creating a culture of discipline and continuous improvement.
Employees are encouraged to adhere to the established standards and take ownership of maintaining the organized workspace.
Benefits of 5S
The additional steps in the 5S methodology offer even greater benefits, including:
– Long-term sustainability: Standardizing processes and encouraging continuous improvement helps maintain the benefits of 3S over the long term.
– Greater consistency: With established protocols, all employees follow the same procedures, leading to more consistent results.
– Enhanced employee involvement: The 5S methodology promotes a culture of ownership and responsibility among employees, leading to higher engagement.
Comparing 3S and 5S
While both 3S and 5S aim to create a more organized and efficient workplace, the key difference lies in the additional steps of Seiketsu (Standardize) and Shitsuke (Sustain) in the 5S methodology.
These extra steps bring several advantages that help ensure the long-term success of the organizational efforts.
Implementation
Implementing 3S can be a great starting point for organizations looking to improve their workplace environment.
It lays the foundation for a clutter-free, efficient, and safe workspace.
However, without the additional steps of 5S, it may be challenging to maintain these improvements over time.
On the other hand, implementing 5S requires a more comprehensive approach, but it offers a more sustainable solution.
By establishing standards and promoting a culture of continuous improvement, organizations can ensure that the benefits of their efforts are maintained over the long term.
Adaptability
3S can be easier to implement initially, especially for smaller organizations with limited resources.
It provides immediate benefits and helps create a more efficient work environment quickly.
5S, while more demanding in terms of resources and commitment, is more adaptable in the long run.
It can be scaled and modified to fit the specific needs of different organizations, industries, and workplace environments.
Cultural Impact
Both 3S and 5S methodologies promote a culture of organization, cleanliness, and efficiency.
However, 5S goes a step further by encouraging standardization and continuous improvement, leading to a more ingrained and long-lasting cultural impact.
Choosing the Right Methodology
Deciding between 3S and 5S depends on the organization’s goals, resources, and commitment level.
For organizations looking for a quick, straightforward way to improve workplace efficiency and organization, 3S may be the ideal choice.
It provides immediate benefits and establishes a foundation for a more organized work environment.
For organizations seeking a more comprehensive and sustainable solution, 5S is the way to go.
Its additional steps ensure that the improvements are maintained over time, and it promotes a culture of continuous improvement.
Conclusion
In summary, both 3S and 5S are effective methodologies for improving workplace efficiency and organization.
3S focuses on sorting, setting in order, and shining, while 5S builds upon these principles by adding standardization and sustainability.
Implementing either methodology can lead to numerous benefits, including increased productivity, enhanced safety, and improved employee morale.
Ultimately, the choice between 3S and 5S depends on the organization’s specific needs and goals.
資料ダウンロード
QCD調達購買管理クラウド「newji」は、調達購買部門で必要なQCD管理全てを備えた、現場特化型兼クラウド型の今世紀最高の購買管理システムとなります。
ユーザー登録
調達購買業務の効率化だけでなく、システムを導入することで、コスト削減や製品・資材のステータス可視化のほか、属人化していた購買情報の共有化による内部不正防止や統制にも役立ちます。
NEWJI DX
製造業に特化したデジタルトランスフォーメーション(DX)の実現を目指す請負開発型のコンサルティングサービスです。AI、iPaaS、および先端の技術を駆使して、製造プロセスの効率化、業務効率化、チームワーク強化、コスト削減、品質向上を実現します。このサービスは、製造業の課題を深く理解し、それに対する最適なデジタルソリューションを提供することで、企業が持続的な成長とイノベーションを達成できるようサポートします。
オンライン講座
製造業、主に購買・調達部門にお勤めの方々に向けた情報を配信しております。
新任の方やベテランの方、管理職を対象とした幅広いコンテンツをご用意しております。
お問い合わせ
コストダウンが利益に直結する術だと理解していても、なかなか前に進めることができない状況。そんな時は、newjiのコストダウン自動化機能で大きく利益貢献しよう!
(Β版非公開)