- お役立ち記事
- Case Studies of Quality Assurance Departments’ Efforts to Reduce Quality Costs in the Manufacturing Industry
Case Studies of Quality Assurance Departments’ Efforts to Reduce Quality Costs in the Manufacturing Industry
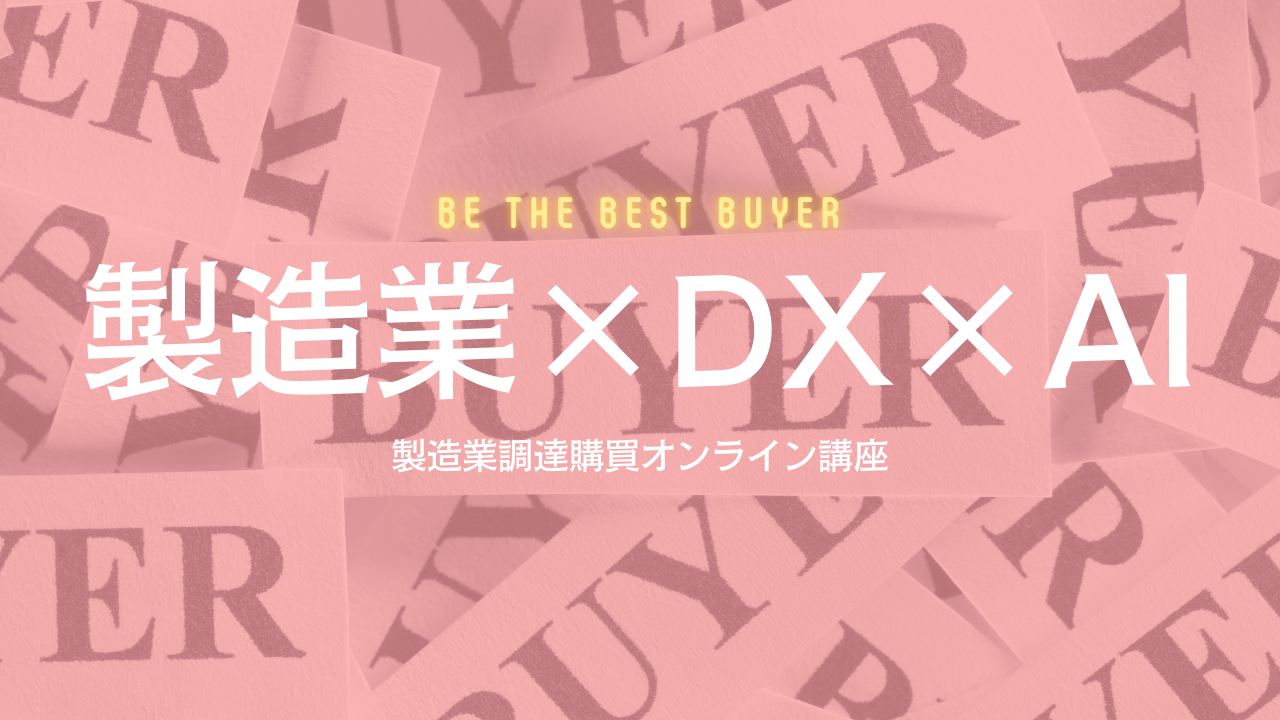
Quality costs can eat into a manufacturing company’s profits if not properly managed. This is why quality assurance departments work hard to reduce costs associated with quality issues. Here are a few case studies of real efforts manufacturing QA teams have undertaken to drive down expenses from quality problems.
ACME Manufacturing is a toy company that was spending over $200,000 per year fixing and replacing defective products. Their QA lead, Maria, decided it was time for a change. First, she had inspectors take a closer look at their assembly lines to pinpoint where issues were originating. They found a few machines were not properly calibrated, leading to tolerance problems. Getting those machines serviced cut reject rates by 15% immediately.
Maria then had workers time study each assembly step to see if processes could be streamlined. They found employees were over-torquing some screws out of habit, cracking plastic parts. Re-training to use just the right amount of force saved $35,000 annually in replacement parts. Batch testing finished products caught another recurring flaw. Some toys were not fully cured under the painting robots due to a clogged spray nozzle. A repair saved $50,000 per year by eliminating those failures.
Through small process improvements, ACME saw quality costs reduced by over 30% compared to the previous year. Management was so pleased that Maria was given a budget to automate more inspection steps. New vision systems now scan toys for any assembly or finish defects, further cutting down on human errors.
Reliable Parts is an automotive supplier known for precision components. But the company noticed failure rates creeping up on a critical transmission gear product line. Jun, the plant manager, tasked his QA team with determining the root causes. After mapping out the manufacturing flow, a troubled washing station was pinpointed. Old bearings within were causing gears to become water damaged before heat treatment.
Replacing those bearings reduced failures by 20% on the spot. But more issues kept occurring down the line. Ultrasound testing found small cracks forming during hardening. The heat treat ovens were out of calibration. New controls resolved that problem. Finally, micro-fractures in the finishing area were traced to improperly adjusted honing machines. Correcting those alignments slashed failures by another 35%.
Within 6 months, Reliable Parts had quality costs down 55% on that transmission gear line thanks to Jun’s comprehensive investigation and fixes. The effort more than paid for itself in reduced rework, returns, and new business gained from perfect quality.
Fabrikool Tools is a manufacturer known worldwide for its high-end wrenches, sockets, and pliers. However, customers began complaining of stripped or broken fasteners when using certain product lines. Annette, VP of operations, knew this had to be addressed quickly to protect Fabrikool’s sterling reputation.
Her team started by surveying customers on the problematic tools. They learned one type of extra-long ratchet had been bending during tough jobs, ruining bolt heads. Metallurgical testing found the raw material had inconsistent strength levels. Switching to a more rugged supplier immediately ended those calls.
Meanwhile, Fabrikool’s pride and joy, a line of ultra-lightweight wrenches, was identified as too flimsy. Users reported stripped bolt heads even in moderate applications. Redesigning the wrench heads with beefier walls and a precision surface treatment solved the problem.
Annette was pleased to report zero client complaints within 3 months of the materiel and design changes. Fabrikool’s quality image remained untarnished thanks to swift problem solving guided by direct customer input. The company avoided a PR disaster and has seen growing sales as a result.
As these case studies show, proactive and data-driven quality assurance work is key to reducing manufacturing costs from quality issues. Taking the time to thoroughly examine production and get customer feedback on product weaknesses pays off. It leads to more efficient processes, longer lasting products, and ultimately greater profits and customer satisfaction for manufacturing companies. With attention to continuous improvement, QA departments can really help boost the bottom line.
資料ダウンロード
QCD調達購買管理クラウド「newji」は、調達購買部門で必要なQCD管理全てを備えた、現場特化型兼クラウド型の今世紀最高の購買管理システムとなります。
ユーザー登録
調達購買業務の効率化だけでなく、システムを導入することで、コスト削減や製品・資材のステータス可視化のほか、属人化していた購買情報の共有化による内部不正防止や統制にも役立ちます。
NEWJI DX
製造業に特化したデジタルトランスフォーメーション(DX)の実現を目指す請負開発型のコンサルティングサービスです。AI、iPaaS、および先端の技術を駆使して、製造プロセスの効率化、業務効率化、チームワーク強化、コスト削減、品質向上を実現します。このサービスは、製造業の課題を深く理解し、それに対する最適なデジタルソリューションを提供することで、企業が持続的な成長とイノベーションを達成できるようサポートします。
オンライン講座
製造業、主に購買・調達部門にお勤めの方々に向けた情報を配信しております。
新任の方やベテランの方、管理職を対象とした幅広いコンテンツをご用意しております。
お問い合わせ
コストダウンが利益に直結する術だと理解していても、なかなか前に進めることができない状況。そんな時は、newjiのコストダウン自動化機能で大きく利益貢献しよう!
(Β版非公開)