- お役立ち記事
- 品質検証と品質確認の違い
品質検証と品質確認の違い
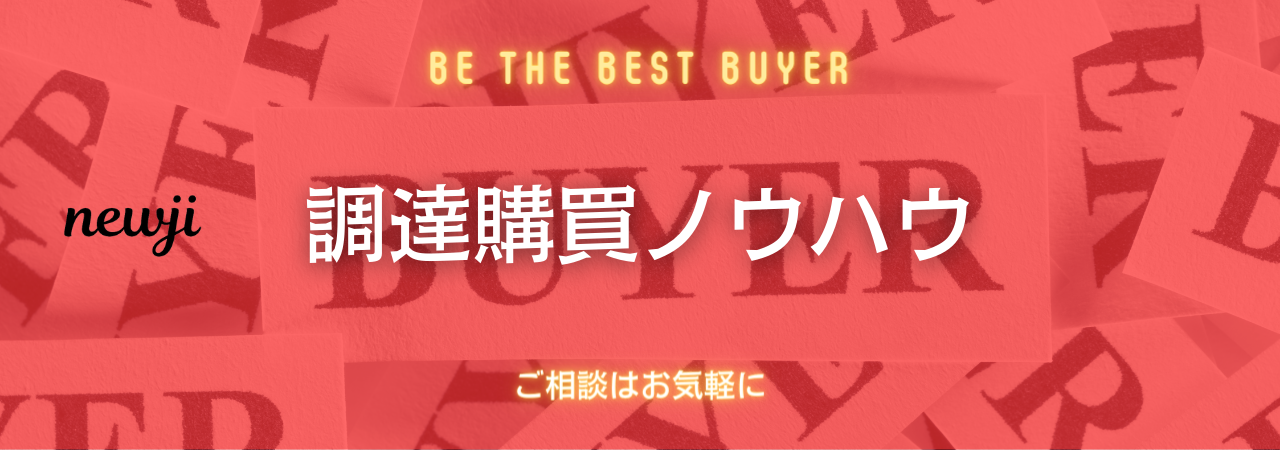
目次
品質検証と品質確認の概要
製造業における品質管理は、製品の性能や信頼性を確保するための重要なプロセスです。
この品質管理の中でも、「品質検証」と「品質確認」という二つの概念が頻繁に登場します。
これらは似て非なるものであり、役割や目的が異なります。
本記事では、その違いについて詳しく説明し、それぞれのプロセスがどのように製造業の現場で活用されているかを見ていきます。
品質検証とは
品質検証の定義
品質検証(Verification)は、設計や仕様に基づき、製品やシステムが正しく作られているかを確認するプロセスです。
具体的には、製造過程や工程において、設計図や作業指示書、規格などの基準に従っているかを検査します。
品質検証は、品質保証の一環として実施され、内部的なチェックが主となります。
品質検証の目的
品質検証の主な目的は、製品が設計通りに製造されているかを確認することです。
製造過程での不具合や手順の逸脱を防ぐため、工程ごとに詳細なチェックを行います。
これにより、最終製品の品質が保持されるだけでなく、不良品が市場に出回るリスクを低減できます。
具体例と実践方法
具体的な品質検証の方法としては、以下のようなものがあります:
1. **設計資料のレビュー**:
設計図や仕様書などのドキュメントを詳しくチェックし、記載内容が明確で正確かを確認します。
2. **工程監査**:
製造ラインや作業場を訪問し、実際の作業が指示書通りに行われているかを目視や計測器を使って確認します。
3. **テストとシミュレーション**:
小規模の試作やシミュレーションテストを行い、パフォーマンスや安全性を確認します。
これらの検証活動を通じて、事前に問題を発見し、必要な修正を行うことで、高品質な製品を継続的に供給することが可能になります。
品質確認とは
品質確認の定義
品質確認(Validation)は、最終製品が実際の使用条件下で必要な機能を果たすかを検証するプロセスです。
これは、エンドユーザーが製品を使用する際に求められる性能や品質が達成されているかを確認するものです。
品質検証が「設計通りに作られているか」をチェックするのに対し、品質確認は「期待通りに機能するか」を確認します。
品質確認の目的
品質確認の主な目的は、製品が意図された用途や環境で適切に動作するかを確認することです。
これにより、最終ユーザーに確実に満足を提供し、ブランドの信頼性を維持・向上させることができます。
具体例と実践方法
具体的な品質確認の方法としては、以下のようなものがあります:
1. **実環境テスト**:
実際の使用環境を模擬して、製品が想定通りに機能するかをテストします。
2. **フィールドテスト**:
実際のユーザーが製品を使用する状況でテストを行い、フィードバックを収集します。
3. **信頼性試験**:
長期間にわたる使用を想定し、製品の耐久性や信頼性を確認するための試験を行います。
これにより、製品が市場に出る前に問題点を洗い出し、必要な改善を行うことで、高い顧客満足度を実現します。
品質検証と品質確認の違い
品質検証と品質確認には明確な違いがあります。
双方とも品質保証の一環ではありますが、その目的と対象となる検査範囲が異なります。
目的の違い
品質検証は、「製品が設計通りに作られているか」を確認することが主な目的です。
一方、品質確認は、「製品が実際の使用条件下で期待通りに機能するか」を確認します。
検査のタイミング
品質検証は製造過程や工程の初期段階で行われることが多いです。
例えば、設計段階や製造ラインの途中でのチェックが該当します。
これに対し、品質確認は製品の完成後、出荷前や市場投入前に行われます。
検査対象と方法
品質検証では設計図や作業手順書、規格に基づく内部的なチェックが行われます。
一方、品質確認では実際のユーザー環境や使用条件を想定した外部的なテストが行われます。
業界動向と現場での活用
最新の品質管理技術
近年では、IoT(Internet of Things)やAI(Artificial Intelligence)技術の進化により、より高度な品質検証と品質確認が可能になっています。
例えば、IoTセンサーを用いることで、リアルタイムで製造過程のデータを収集し、AIを使って異常検知や予測分析を行うことができます。
これにより、問題の早期発見と対策が可能となり、製品の品質向上に寄与します。
現場での実践例
例えば、自動車産業では、製造ラインにIoTセンサーを取り付け、各工程のデータをリアルタイムで監視しています。
異常が検出されると、即座にアラートが発信され、担当者が迅速に対応することができます。
また、AIを用いて過去のデータから異常発生のパターンを学習し、未然に問題を防ぐこともできるようになっています。
結論
品質検証と品質確認は、製造業における品質保証の二大柱です。
それぞれの役割と目的を理解し、適切に活用することで、製品の品質を高めるだけでなく、顧客満足を向上させることができます。
最新技術の導入や現場での実践例を参考に、自社の品質管理プロセスを見直し、さらに改善していくことが重要です。
製品の品質を確保するためには、品質検証と品質確認の両方が欠かせません。
適切なタイミングでの実施と最新技術の活用により、高品質な製品を市場に提供し続けることが、長期的な企業の成功につながります。
資料ダウンロード
QCD調達購買管理クラウド「newji」は、調達購買部門で必要なQCD管理全てを備えた、現場特化型兼クラウド型の今世紀最高の購買管理システムとなります。
ユーザー登録
調達購買業務の効率化だけでなく、システムを導入することで、コスト削減や製品・資材のステータス可視化のほか、属人化していた購買情報の共有化による内部不正防止や統制にも役立ちます。
NEWJI DX
製造業に特化したデジタルトランスフォーメーション(DX)の実現を目指す請負開発型のコンサルティングサービスです。AI、iPaaS、および先端の技術を駆使して、製造プロセスの効率化、業務効率化、チームワーク強化、コスト削減、品質向上を実現します。このサービスは、製造業の課題を深く理解し、それに対する最適なデジタルソリューションを提供することで、企業が持続的な成長とイノベーションを達成できるようサポートします。
オンライン講座
製造業、主に購買・調達部門にお勤めの方々に向けた情報を配信しております。
新任の方やベテランの方、管理職を対象とした幅広いコンテンツをご用意しております。
お問い合わせ
コストダウンが利益に直結する術だと理解していても、なかなか前に進めることができない状況。そんな時は、newjiのコストダウン自動化機能で大きく利益貢献しよう!
(Β版非公開)