- お役立ち記事
- Workstyle Reforms in Textile Factories and Their Impact
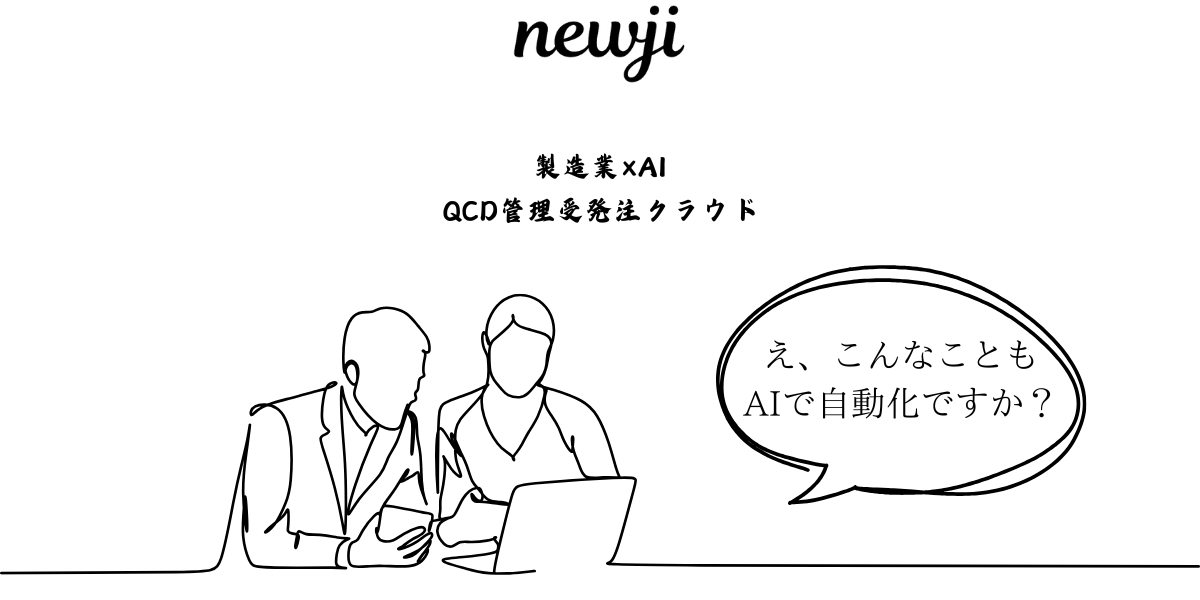
Workstyle Reforms in Textile Factories and Their Impact
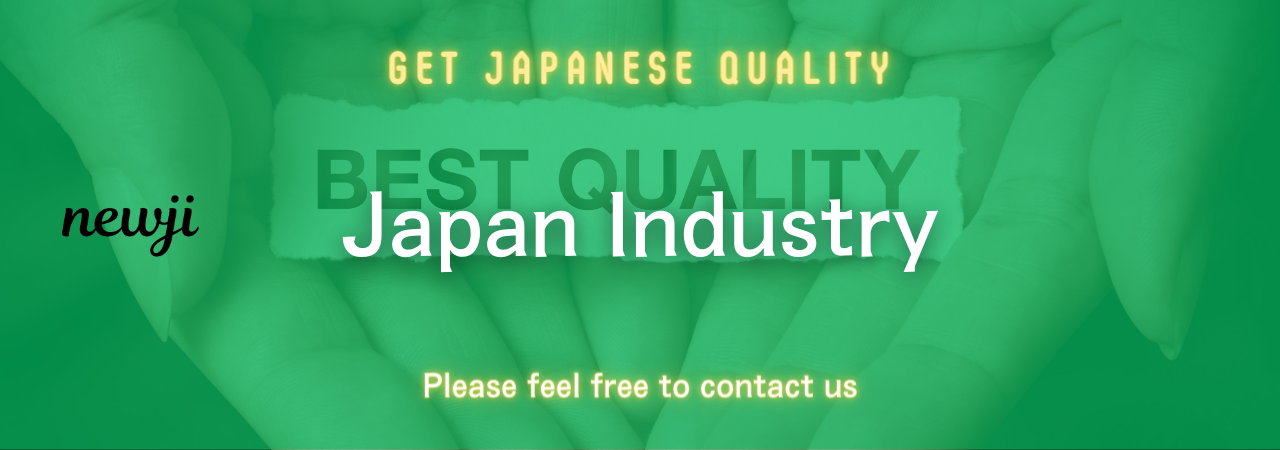
Understanding Workstyle Reforms in Textile Factories
In recent years, changes in workstyle have become a hot topic across various industries, including the textile sector.
Textile factories, traditionally known for their labor-intensive environments, are now experiencing a significant shift in how they operate.
Workstyle reforms aim to improve working conditions, enhance productivity, and promote employee well-being.
What Are Workstyle Reforms?
Workstyle reforms involve modifying the way work is structured within organizations.
These reforms can include flexible working hours, remote work options, enhanced safety measures, and better working conditions.
In the context of textile factories, it means integrating technological advancements to optimize production processes and improve job satisfaction among workers.
The Need for Change in Textile Factories
Textile factories have long faced challenges such as long working hours, inadequate safety measures, and limited employee benefits.
These issues often result in high employee turnover rates and lower productivity.
Furthermore, the global demand for sustainable and ethically produced textiles has increased pressure on factories to adopt more responsible practices.
Workstyle reforms address these challenges by focusing on employee-centric policies and efficiency-boosting technologies.
Impact of Technological Innovations
One of the key elements of workstyle reforms in textile factories is the introduction of new technologies.
Automation and advanced machinery have transformed the way textiles are manufactured.
Robotics and AI-driven systems are now handling complex tasks, leading to faster production times and reduced error rates.
This shift not only boosts productivity but also reduces the physical burden on workers, allowing them to transition to roles that require human creativity and problem-solving skills.
Flexible Work Arrangements
Incorporating flexible work arrangements is another significant aspect of workstyle reforms.
Factories are increasingly offering flexible shift schedules and remote work options for non-production roles.
Such flexibility helps employees achieve a better work-life balance, reducing burnout and improving overall job satisfaction.
For example, scheduling systems can allow workers to select shifts that suit their personal needs, leading to a more engaged and motivated workforce.
Enhancing Safety and Health Standards
Improved health and safety standards are integral to the workstyle reforms in textile factories.
By implementing stricter regulations and regular safety audits, factories can provide a safer working environment for their employees.
This includes better ventilation systems, ergonomic workstations, and access to on-site medical facilities.
These measures not only protect workers from occupational hazards but also boost their morale, fostering a culture of safety and trust.
Education and Skill Development
Workstyle reforms are also emphasizing the importance of education and skill development.
Many textile factories are investing in training programs to upskill their workforce.
Employees are being trained to handle new technologies, improve their technical skills, and develop leadership abilities.
This focus on continuous learning ensures that workers remain competitive and adaptable in an ever-evolving industry.
Environmental and Ethical Considerations
The textile industry is under immense pressure to adopt sustainable practices due to environmental concerns.
Workstyle reforms encourage factories to minimize waste, reduce water usage, and shift to eco-friendly materials.
Moreover, ethical considerations like fair wages and working conditions are being prioritized.
These changes help factories meet international compliance standards and cater to the growing consumer demand for ethical products.
Challenges in Implementing Reforms
While the benefits of workstyle reforms are evident, implementing these changes is not without challenges.
There can be resistance from both management and workers who are accustomed to traditional ways of operation.
Additionally, the cost of upgrading technology and training staff can be significant.
To overcome these hurdles, clear communication and collaboration among stakeholders are essential.
Engaging workers in the reform process, understanding their concerns, and demonstrating the long-term benefits can facilitate smoother transitions.
The Future of Textile Workplaces
As workstyle reforms continue to gain momentum, the future of textile factories looks promising.
Factories that embrace these changes are likely to see increased productivity, higher-quality products, and more satisfied employees.
Moreover, they will be better positioned to compete in the global market by aligning with sustainable practices and ethical standards.
Ultimately, these reforms pave the way for a more modern, efficient, and responsible textile industry.
In conclusion, workstyle reforms are reshaping the landscape of textile factories, offering a path forward to more sustainable and humane working environments.
By addressing the needs of workers and the challenges of modern production, these reforms not only benefit the textile industry but also contribute positively to society at large.
資料ダウンロード
QCD調達購買管理クラウド「newji」は、調達購買部門で必要なQCD管理全てを備えた、現場特化型兼クラウド型の今世紀最高の購買管理システムとなります。
ユーザー登録
調達購買業務の効率化だけでなく、システムを導入することで、コスト削減や製品・資材のステータス可視化のほか、属人化していた購買情報の共有化による内部不正防止や統制にも役立ちます。
NEWJI DX
製造業に特化したデジタルトランスフォーメーション(DX)の実現を目指す請負開発型のコンサルティングサービスです。AI、iPaaS、および先端の技術を駆使して、製造プロセスの効率化、業務効率化、チームワーク強化、コスト削減、品質向上を実現します。このサービスは、製造業の課題を深く理解し、それに対する最適なデジタルソリューションを提供することで、企業が持続的な成長とイノベーションを達成できるようサポートします。
オンライン講座
製造業、主に購買・調達部門にお勤めの方々に向けた情報を配信しております。
新任の方やベテランの方、管理職を対象とした幅広いコンテンツをご用意しております。
お問い合わせ
コストダウンが利益に直結する術だと理解していても、なかなか前に進めることができない状況。そんな時は、newjiのコストダウン自動化機能で大きく利益貢献しよう!
(Β版非公開)