- お役立ち記事
- The Impact of Workstyle Reforms in the Textile Industry
The Impact of Workstyle Reforms in the Textile Industry
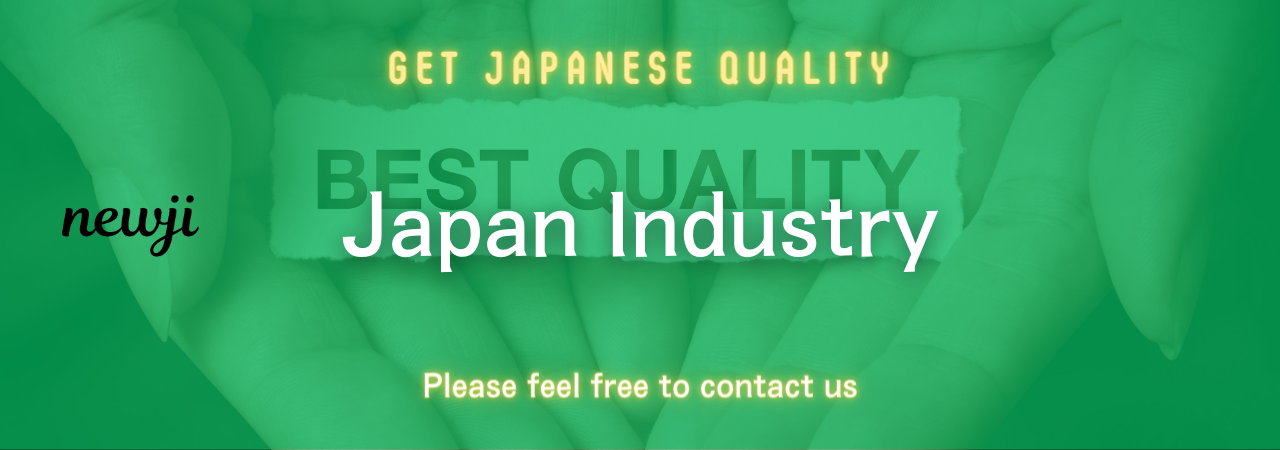
目次
Introduction
The textile industry, a crucial sector in global trade and production, has been undergoing significant transformations.
With the advent of workstyle reforms, companies in this industry are reevaluating their operations and management practices.
These changes aim to improve worker satisfaction, increase productivity, and adapt to modern technological advancements.
Understanding Workstyle Reforms
Workstyle reforms refer to modifications in the traditional way work is structured and executed.
These changes could include flexible working hours, remote work opportunities, and a greater emphasis on work-life balance.
In the textile industry, where labor-intensive operations are common, such reforms are becoming increasingly necessary to attract and retain skilled workers.
Flexibility in Working Hours
One of the key components of workstyle reforms is the introduction of flexible working hours.
Textile companies are now more open to allowing their employees to choose when they start and end their workdays.
This flexibility helps workers manage their personal commitments while ensuring that production targets are still met.
Remote Work Opportunities
Though traditionally not suited for remote work, the textile industry is finding creative ways to enable it.
With advancements in technology, many roles, especially those related to design, management, and sales, can now be done from afar.
This shift not only broadens the talent pool available to companies but also helps reduce costs associated with maintaining large physical workspaces.
Emphasis on Work-Life Balance
Companies in the textile sector are increasingly focusing on the well-being of their employees.
By offering initiatives such as mental health days, fitness programs, and better leave policies, these organizations aim to ensure a healthier and more motivated workforce.
Such measures lead to decreased turnover rates and enhance the overall work environment.
Impact on Production and Efficiency
The introduction of workstyle reforms in the textile industry has had notable effects on production efficiency and operational dynamics.
Boosted Productivity
When employees find balance and satisfaction in their work environments, their productivity tends to increase.
Flexible working conditions lead to improved morale, which in turn reduces absenteeism and increases worker focus.
This heightened efficiency helps textile companies meet their production deadlines more consistently.
Enhanced Technological Adoption
To facilitate remote work and flexible schedules, textile companies are investing more in technology.
This increased focus on technology adoption streamlines processes, reduces inefficiencies, and leads to higher quality outputs.
Employing digital tools also helps these companies remain competitive in an ever-evolving market.
Cost Efficiency
Workstyle reforms can lead to considerable cost savings for textile companies.
By reducing the need for large office spaces and minimizing turnover rates, organizations can allocate resources more effectively.
These changes contribute to the bottom line, allowing companies to reinvest in growth and innovation.
Challenges and Considerations
While workstyle reforms offer numerous benefits, they also present several challenges that textile companies need to consider.
Adapting to Change
Not all employees or management teams may be immediately receptive to workstyle reforms.
Adapting to new systems and processes requires time, training, and patience.
Textile companies need to conduct thorough assessments to understand how best to implement these changes in a way that benefits everyone involved.
Infrastructure and Technology Investment
Implementing remote work capabilities and flexible schedules often requires significant investment in technology and infrastructure.
For smaller companies, especially those operating on tighter budgets, these investments can be daunting.
However, viewing them as long-term investments in efficiency and employee satisfaction can justify the initial costs.
Maintaining Quality Control
In an industry known for its emphasis on quality, textile companies must ensure that workstyle reforms do not compromise standards.
Clear guidelines and regular check-ins become crucial in maintaining high quality while embracing these new work styles.
Companies may need to develop comprehensive training programs to align the work output with set standards.
Conclusion
The impact of workstyle reforms in the textile industry is profound, and while it presents its own set of challenges, the benefits typically outweigh the obstacles.
As textile companies continue to evolve, adopting such reforms becomes not only a necessity but a strategic advantage in a competitive market.
With careful planning and execution, the industry can improve worker satisfaction, boost productivity, and ensure long-term success.
資料ダウンロード
QCD調達購買管理クラウド「newji」は、調達購買部門で必要なQCD管理全てを備えた、現場特化型兼クラウド型の今世紀最高の購買管理システムとなります。
ユーザー登録
調達購買業務の効率化だけでなく、システムを導入することで、コスト削減や製品・資材のステータス可視化のほか、属人化していた購買情報の共有化による内部不正防止や統制にも役立ちます。
NEWJI DX
製造業に特化したデジタルトランスフォーメーション(DX)の実現を目指す請負開発型のコンサルティングサービスです。AI、iPaaS、および先端の技術を駆使して、製造プロセスの効率化、業務効率化、チームワーク強化、コスト削減、品質向上を実現します。このサービスは、製造業の課題を深く理解し、それに対する最適なデジタルソリューションを提供することで、企業が持続的な成長とイノベーションを達成できるようサポートします。
オンライン講座
製造業、主に購買・調達部門にお勤めの方々に向けた情報を配信しております。
新任の方やベテランの方、管理職を対象とした幅広いコンテンツをご用意しております。
お問い合わせ
コストダウンが利益に直結する術だと理解していても、なかなか前に進めることができない状況。そんな時は、newjiのコストダウン自動化機能で大きく利益貢献しよう!
(Β版非公開)