- お役立ち記事
- Calibration Methods for Automated Inspection Systems in Production Lines
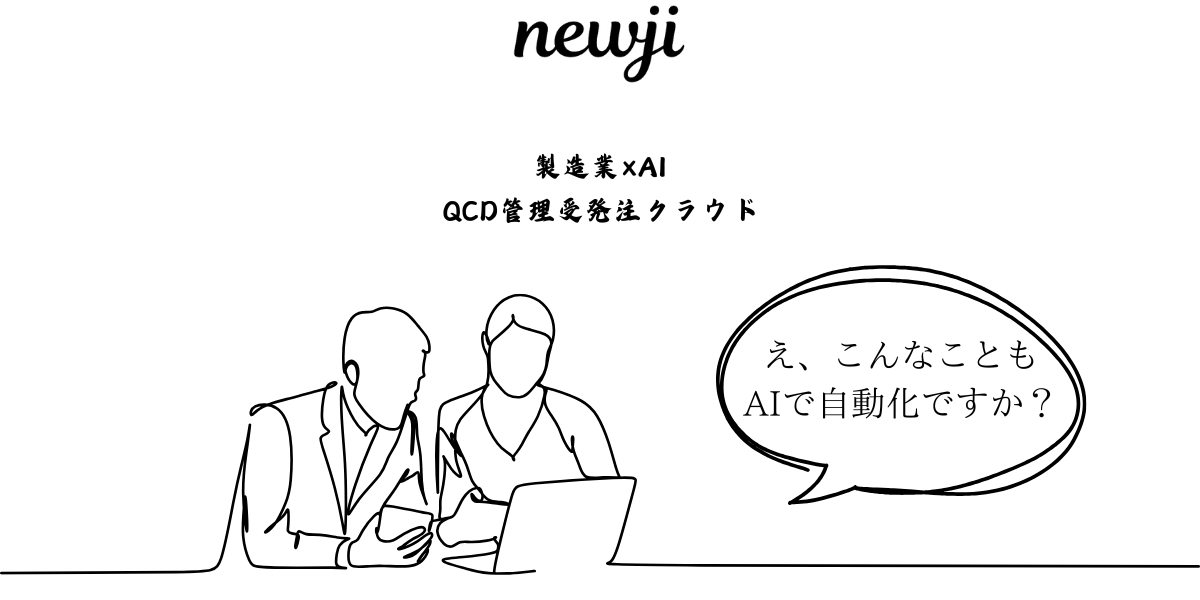
Calibration Methods for Automated Inspection Systems in Production Lines
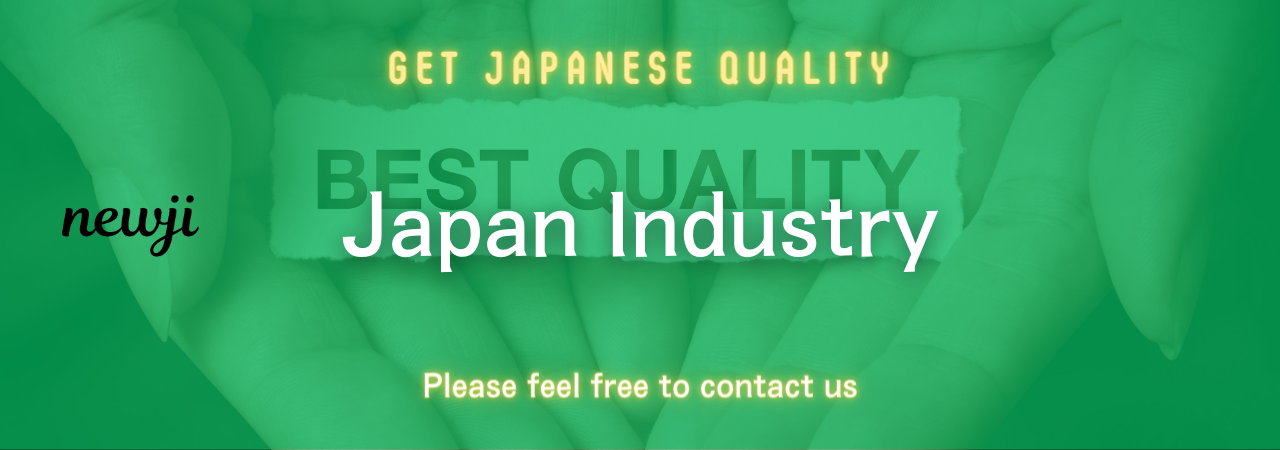
目次
Introduction to Calibration in Automated Inspection Systems
Automated inspection systems have become an integral part of modern production lines, ensuring high-quality standards and reducing human error.
These systems rely heavily on accurate calibration to function correctly.
But what exactly does calibration mean in this context?
Calibration refers to the process of configuring an automated system to perform its tasks with precision.
Without proper calibration, these systems might produce inaccurate results, potentially leading to costly errors in production.
Why Calibration is Crucial
The importance of calibration cannot be overstated.
In automated inspection systems, even minor deviations can result in significant production issues.
If a system is not properly calibrated, it may fail to detect defects, which leads to the delivery of faulty products to customers.
On the other hand, over-sensitivity might cause the rejection of perfectly acceptable items, increasing waste and loss.
Calibration ensures that the system is perfectly tuned to identify defects while maintaining efficiency.
Quality Assurance
The primary goal of automated inspection is to maintain high-quality standards.
Calibration helps set the benchmark that the system should follow.
A well-calibrated system enhances quality assurance processes by accurately identifying products that do not meet predefined standards.
Cost-Effectiveness
Incorrect calibration can lead to significant financial losses.
Reworking or scrapping defective products after they reach the end of the line is far more costly than catching them during production.
Accurate calibration minimizes these costs by ensuring defects are spotted early.
Production Efficiency
When an inspection system is not correctly calibrated, it may slow down the production line.
Frequent false alarms or failures in detection can lead to unnecessary halts.
With precise calibration, the production process becomes smoother and more efficient, maximizing output.
Methods of Calibration
There are several methods used to calibrate automated inspection systems.
Each method has its own advantages and is chosen based on the specific requirements of the production line.
Manual Calibration
Manual calibration involves human intervention, where technicians adjust the system’s parameters to optimal settings.
This method requires skilled personnel who can interpret data and make adjustments accordingly.
While it might seem outdated, manual calibration is still used in situations where high customization is required.
Automatic Calibration
In automatic calibration, the system is programmed to adjust itself without human intervention.
Certain algorithms are applied to fine-tune the system according to the data it receives.
This method is less prone to human error and can handle large volumes, making it ideal for complex production lines.
Adaptive Calibration
Adaptive calibration is a dynamic method where the system continuously calibrates itself based on the production environment.
Using real-time data, it adjusts to varying conditions such as temperature, humidity, and material changes.
This method is highly effective in environments where conditions are constantly changing.
Hybrid Calibration
A combination of manual and automatic methods, hybrid calibration brings the best of both worlds.
It allows for human intervention where required, yet automates routine adjustments.
This method is often preferred in modern production environments where flexibility and precision are needed.
Steps in the Calibration Process
Regardless of the method used, the calibration process typically follows a structured approach.
Initial Assessment
The first step involves assessing the current performance of the inspection system.
This includes identifying any discrepancies and determining the calibration requirements.
Setting Benchmarks
Benchmarking is crucial in this step.
Specifications are established for acceptable quality levels.
These benchmarks will guide the calibration and ensure the system is tuned accordingly.
Implementation
Once benchmarks are set, calibration is undertaken using the chosen method.
Any changes made are documented, and the system is adjusted to meet the standards.
Verification
After calibration, the system’s performance is verified.
This ensures that all adjustments have been effective and the system is operating within the desired parameters.
Ongoing Monitoring
Calibration is not a one-time task.
Continuous monitoring is essential to maintain system accuracy.
Regular checks help detect any deviations and prompt recalibration if necessary.
Challenges in Calibration
Although calibration is essential, it is not without its challenges.
Understanding these challenges helps in optimizing the calibration process.
Complexity of Systems
Modern automated systems are highly complex, with multiple variables affecting their performance.
Calibrating such systems requires a deep understanding of both the technology and the production environment.
Resource Intensity
Calibration can be resource-intensive, requiring time, skilled personnel, and sometimes a halt in production.
Balancing these resources while maintaining production schedules is a common challenge.
Data Management
With numerous data points involved, managing and analyzing calibration data can be overwhelming.
Efficient data management systems must be in place to facilitate the process.
Conclusion
Calibration is a critical component in the operation of automated inspection systems in production lines.
It ensures quality, efficiency, and cost-effectiveness.
By employing various calibration methods and overcoming associated challenges, production lines can maintain high standards and minimize errors.
Continual advancements in technology promise further enhancements in calibration techniques, paving the way for even more sophisticated and efficient inspection systems.
資料ダウンロード
QCD調達購買管理クラウド「newji」は、調達購買部門で必要なQCD管理全てを備えた、現場特化型兼クラウド型の今世紀最高の購買管理システムとなります。
ユーザー登録
調達購買業務の効率化だけでなく、システムを導入することで、コスト削減や製品・資材のステータス可視化のほか、属人化していた購買情報の共有化による内部不正防止や統制にも役立ちます。
NEWJI DX
製造業に特化したデジタルトランスフォーメーション(DX)の実現を目指す請負開発型のコンサルティングサービスです。AI、iPaaS、および先端の技術を駆使して、製造プロセスの効率化、業務効率化、チームワーク強化、コスト削減、品質向上を実現します。このサービスは、製造業の課題を深く理解し、それに対する最適なデジタルソリューションを提供することで、企業が持続的な成長とイノベーションを達成できるようサポートします。
オンライン講座
製造業、主に購買・調達部門にお勤めの方々に向けた情報を配信しております。
新任の方やベテランの方、管理職を対象とした幅広いコンテンツをご用意しております。
お問い合わせ
コストダウンが利益に直結する術だと理解していても、なかなか前に進めることができない状況。そんな時は、newjiのコストダウン自動化機能で大きく利益貢献しよう!
(Β版非公開)