- お役立ち記事
- How to Properly Manage Shot Size to Achieve Cost Reduction
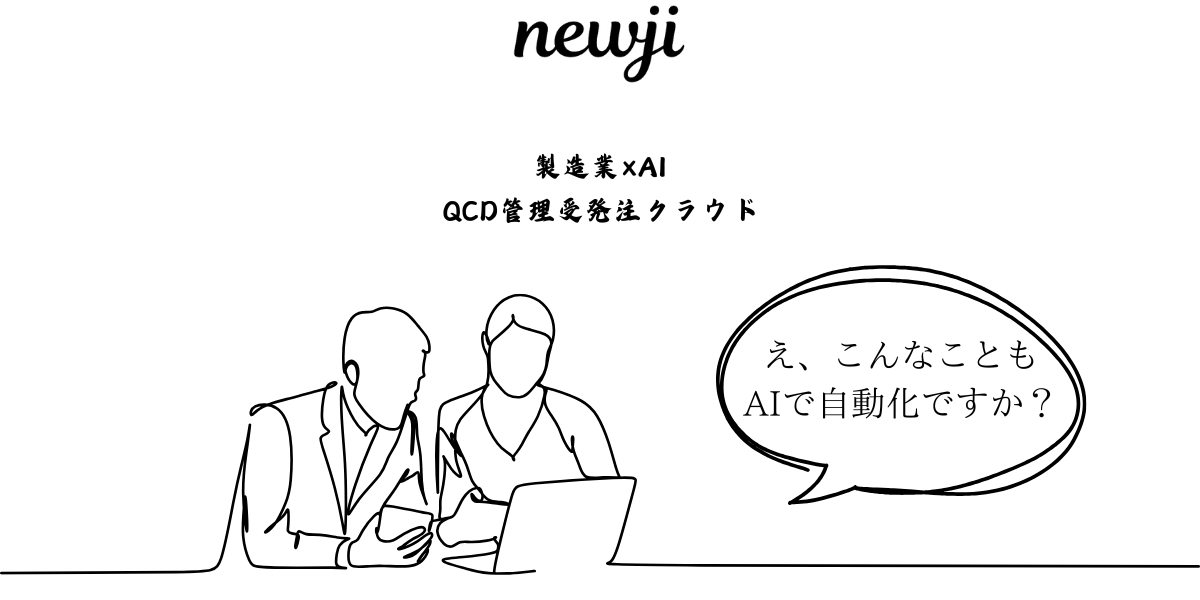
How to Properly Manage Shot Size to Achieve Cost Reduction
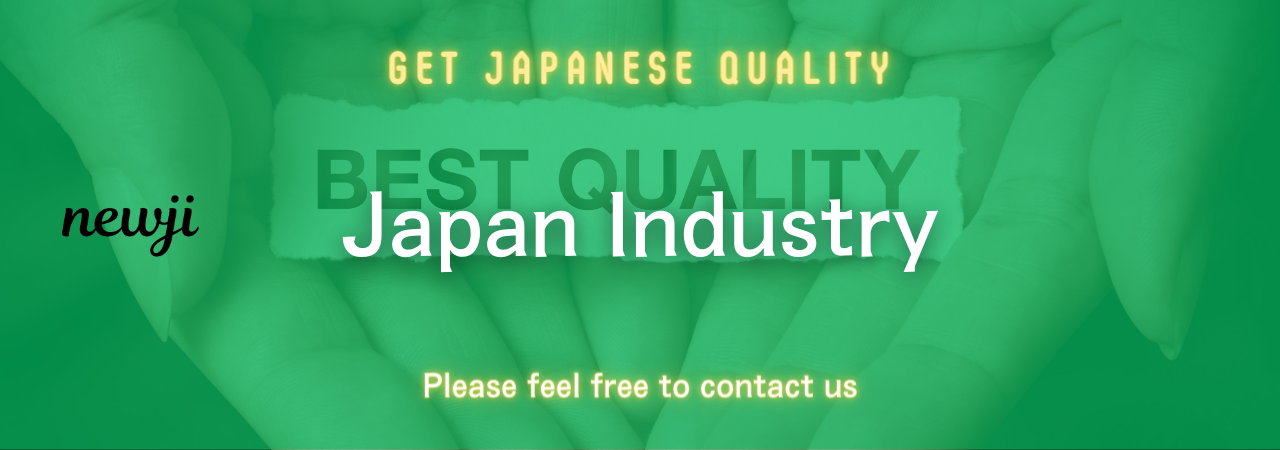
目次
Understanding Shot Size in Manufacturing
In the world of manufacturing, shot size refers to the amount of material injected into a mold during the production of a part or product.
This is a crucial factor that manufacturers must manage effectively to achieve cost reduction.
By optimizing shot size, businesses can minimize waste, reduce cycle times, and improve the quality of their products.
A deep understanding of how shot size impacts the manufacturing process can drive significant improvements in efficiency and profitability.
The Importance of Shot Size Management
Proper management of shot size is essential for several reasons.
Firstly, it directly affects the amount of raw material used in the production process.
An oversized shot can lead to material waste, which increases production costs and reduces overall efficiency.
Conversely, an undersized shot may result in incomplete products, leading to rework or scrap, both of which also drive up costs.
Additionally, the shot size can influence the cycle time—the duration required to produce each part.
An optimized shot size ensures that the cycle time is minimized, allowing manufacturers to produce more parts in less time.
This efficiency translates into higher throughput, enabling businesses to meet demand more effectively.
Lastly, shot size plays a critical role in determining the quality of the final product.
A well-calibrated shot size can prevent common defects, such as warping or sink marks, ensuring that the products meet quality standards.
High-quality products reduce the likelihood of returns or dissatisfaction, preserving the manufacturer’s reputation and customer trust.
Strategies for Optimizing Shot Size
To manage shot size effectively, manufacturers can adopt several strategies that help refine the injection molding process and reduce costs.
Conducting a Shot Size Analysis
A shot size analysis involves closely examining the current manufacturing process to identify the optimal shot size for each product.
This may involve experimenting with different shot sizes to determine which produces the best results with the least waste.
Using simulation software can help manufacturers predict the outcome of different shot sizes, reducing the need for physical trials.
Implementing Advanced Technology
Leveraging advanced technologies, such as computer-aided design (CAD) and process simulation tools, enables precise control over the shot size.
These tools can help manufacturers model the injection molding process and predict the effects of different shot sizes.
Automated systems may also adjust the shot size during production, responding to real-time data to maintain optimal performance.
Training and Educating Personnel
Ensuring that the personnel involved in the production process are well-trained is key to effective shot size management.
Operators need to understand the impact of shot size on material usage, cycle time, and product quality to make informed decisions.
Continuous education and training programs can keep staff updated on the latest technologies and best practices in shot size management.
Benefits of Proper Shot Size Management
The advantages of effectively managing shot size extend beyond mere cost reduction and positively impact several areas of manufacturing operations.
Material Savings
When shot sizes are optimized, manufacturers use the exact amount of material necessary for each part.
This precision reduces waste, resulting in substantial savings on material costs.
In industries where raw materials represent a significant portion of production expenses, these savings can be particularly impactful.
Improved Production Efficiency
By reducing cycle times with optimized shot sizes, production processes become more efficient.
This increased efficiency can lead to higher output, enabling manufacturers to fulfill large orders more quickly and with fewer resources.
Businesses can thus enjoy increased competitiveness and the ability to meet market demands without overburdening their production facilities.
Enhanced Product Quality
Well-managed shot size contributes to higher-quality products by minimizing defects.
Products with fewer defects require less rework and meet customer specifications more consistently.
This focus on quality helps manufacturers build and maintain strong relationships with their customers, as well as reduce the costs associated with returns or warranties.
Challenges in Managing Shot Size
While optimizing shot size offers numerous benefits, it can also present certain challenges that manufacturers need to navigate effectively.
Complexity of Injection Molding
Injection molding is a complex process that involves numerous variables, such as temperature, pressure, and mold design, which can affect shot size.
Successfully managing these variables requires in-depth knowledge and experience, as well as sophisticated technology to monitor and control the process.
Balancing Cost and Quality
Optimizing shot size to achieve cost reduction must not compromise product quality.
Manufacturers need to find the right balance between using the minimum amount of material and maintaining the structural integrity of the final product.
This balance requires careful analysis and may involve trade-offs that need to be carefully considered.
Equipment Limitations
Some older manufacturing equipment may not have the capability to adjust shot size with the precision required for maximum efficiency.
Upgrading equipment or investing in newer technologies can represent a significant upfront cost, but it may be necessary for businesses looking to reduce costs through better shot size management.
Conclusion
Effective shot size management is a vital component of cost reduction strategies in the manufacturing industry.
By understanding the importance of shot size, implementing strategies to optimize it, and recognizing the associated challenges, manufacturers can significantly enhance their operations.
The result is a more efficient production process, lower material costs, and higher-quality products—all of which contribute to the overall success and sustainability of the business.
資料ダウンロード
QCD調達購買管理クラウド「newji」は、調達購買部門で必要なQCD管理全てを備えた、現場特化型兼クラウド型の今世紀最高の購買管理システムとなります。
ユーザー登録
調達購買業務の効率化だけでなく、システムを導入することで、コスト削減や製品・資材のステータス可視化のほか、属人化していた購買情報の共有化による内部不正防止や統制にも役立ちます。
NEWJI DX
製造業に特化したデジタルトランスフォーメーション(DX)の実現を目指す請負開発型のコンサルティングサービスです。AI、iPaaS、および先端の技術を駆使して、製造プロセスの効率化、業務効率化、チームワーク強化、コスト削減、品質向上を実現します。このサービスは、製造業の課題を深く理解し、それに対する最適なデジタルソリューションを提供することで、企業が持続的な成長とイノベーションを達成できるようサポートします。
オンライン講座
製造業、主に購買・調達部門にお勤めの方々に向けた情報を配信しております。
新任の方やベテランの方、管理職を対象とした幅広いコンテンツをご用意しております。
お問い合わせ
コストダウンが利益に直結する術だと理解していても、なかなか前に進めることができない状況。そんな時は、newjiのコストダウン自動化機能で大きく利益貢献しよう!
(Β版非公開)