- お役立ち記事
- Latest Technologies for Shortening Filling Time and Case Studies
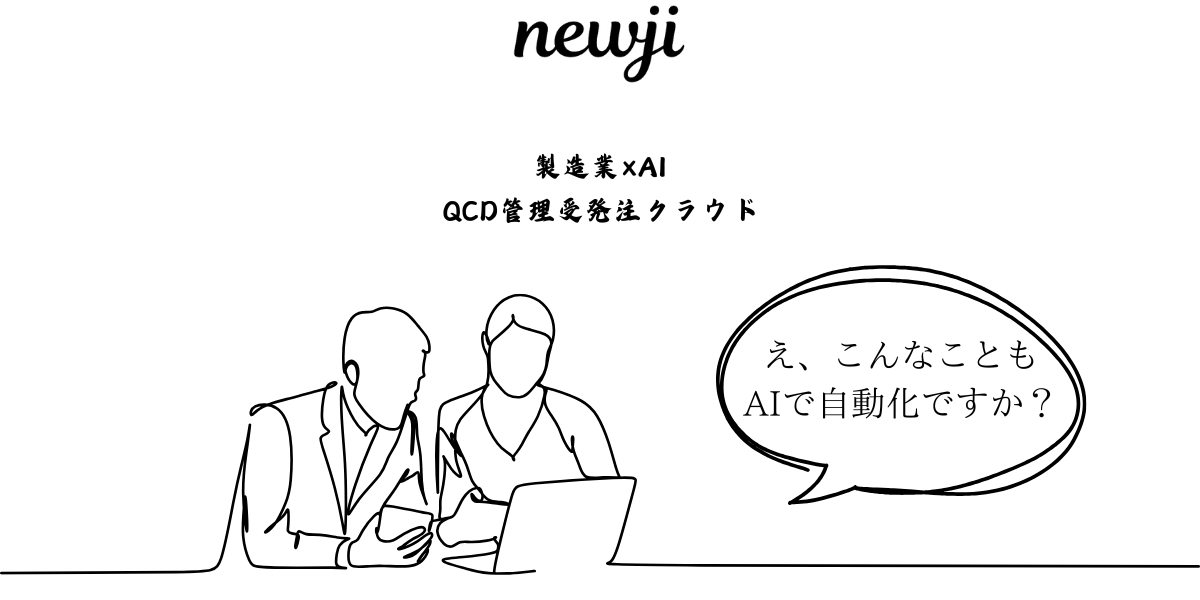
Latest Technologies for Shortening Filling Time and Case Studies
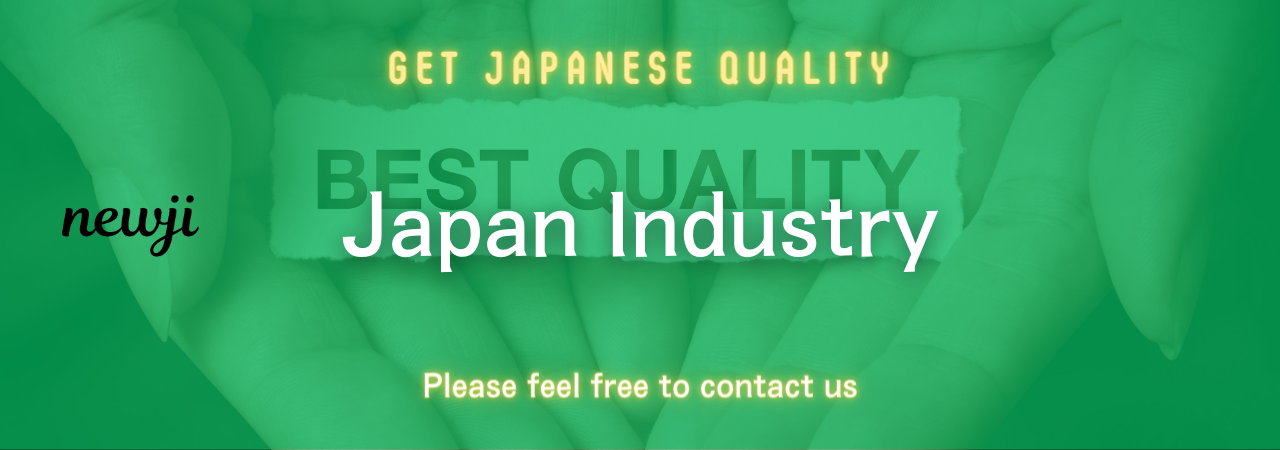
目次
Introduction to Filling Time Reduction
The efficiency of manufacturing processes is crucial for the success and competitiveness of any industry.
One key aspect where manufacturers strive to improve is the filling time of products.
Reducing filling time can lead to increased production rates, lower operational costs, and enhanced product quality.
In this article, we will explore the latest technologies designed to shorten filling time and examine case studies that highlight their effectiveness.
Understanding the Importance of Filling Time
Filling time refers to the duration it takes to fill a container with a specified product, whether it’s a liquid, powder, or granular material.
In industries such as food and beverage, pharmaceuticals, and chemicals, reducing this time is essential to meet demand and maintain quality.
The faster and more accurately a product can be filled, the more efficient the production process becomes.
Impact on Production Efficiency
Reducing filling time impacts several facets of production efficiency.
First, it allows companies to produce more units in a shorter period, catering to higher demand or freeing up time for other critical operations.
Second, it helps minimize energy consumption and labor costs, leading to a more sustainable business model.
Enhancement of Product Quality
Proper filling processes also ensure consistent product quality.
Variations in filling time can lead to inconsistent filling volumes, affecting the final product’s quality.
By adopting technologies that reduce and standardize filling times, companies can enhance product reliability, ensuring that each unit meets quality standards.
Latest Technologies for Reducing Filling Time
The advancement of technology has ushered in innovative solutions aimed at minimizing filling time.
The following are some of the cutting-edge technologies that are making significant strides in this area.
Automated Filling Systems
Automation has revolutionized many manufacturing processes, and filling is no exception.
Modern automated filling systems use advanced robotics and sensors to detect the precise amount of product required and fill containers quickly and efficiently.
These systems are capable of handling a wide variety of product types and container sizes, making them versatile options for manufacturers.
Advanced Sensor Technology
The integration of advanced sensor technology in filling machines allows for real-time monitoring and adjustments.
Sensors can detect discrepancies in filling levels or flow rates, automatically adjusting the process to maintain optimal filling times.
This not only reduces waste but also ensures each container is filled accurately and uniformly.
High-Performance Nozzles
Innovations in nozzle design and materials have significantly enhanced filling speed and accuracy.
High-performance nozzles are engineered to reduce splash and turbulence, facilitating a smoother, faster flow of the product into the container.
This minimizes the risk of spills and ensures efficient use of materials, which is particularly beneficial in industries handling expensive or sensitive products.
Intelligent Software Systems
Intelligent software systems are increasingly being utilized to monitor and control filling operations.
These systems can analyze large sets of data to predict and resolve potential bottlenecks, ensuring continuous and optimized filling processes.
By using machine learning algorithms, they can adapt to new products or changes in production schedules without the need for extensive manual input.
Case Studies Demonstrating Effectiveness
Several companies have successfully implemented the aforementioned technologies, realizing tangible benefits in their manufacturing processes.
Below are a few case studies that highlight the effectiveness of these techniques.
Case Study 1: Beverage Company
A leading beverage company integrated automated filling systems across its production lines, reducing the average filling time by 30%.
By leveraging robotics and smart sensors, the company experienced a 40% increase in production capacity, enabling it to meet growing consumer demand without compromising quality.
The automation also led to a significant decline in labor costs, freeing up resources for other areas of operation.
Case Study 2: Pharmaceutical Manufacturer
In the pharmaceutical industry, precision is crucial.
A pharmaceutical manufacturer implemented high-performance nozzles and intelligent software systems to address filling inconsistencies.
This not only decreased filling time by 25% but also ensured that each medicinal product adhered to stringent quality standards.
The software’s predictive analytics also helped in preemptively identifying and addressing equipment failures, minimizing downtime.
Case Study 3: Chemical Processing Plant
A chemical processing plant adopted advanced sensor technology to enhance real-time monitoring of its filling processes.
This technology allowed for immediate corrections during filling, leading to a 20% reduction in waste and a 15% decrease in filling time.
As a result, the plant not only increased its operational efficiency but also reduced its environmental impact.
Conclusion
As the demand for faster and more efficient production processes grows, companies must continually explore and implement technologies that reduce filling times.
The latest advancements in automated systems, sensor technology, nozzle design, and intelligent software have proven to be effective in achieving these goals.
Case studies from various industries illustrate the tangible benefits of these innovations, showcasing increased efficiency, reduced costs, and improved product quality.
Embracing these technologies will be key for manufacturers aiming to remain competitive in an ever-evolving marketplace.
資料ダウンロード
QCD調達購買管理クラウド「newji」は、調達購買部門で必要なQCD管理全てを備えた、現場特化型兼クラウド型の今世紀最高の購買管理システムとなります。
ユーザー登録
調達購買業務の効率化だけでなく、システムを導入することで、コスト削減や製品・資材のステータス可視化のほか、属人化していた購買情報の共有化による内部不正防止や統制にも役立ちます。
NEWJI DX
製造業に特化したデジタルトランスフォーメーション(DX)の実現を目指す請負開発型のコンサルティングサービスです。AI、iPaaS、および先端の技術を駆使して、製造プロセスの効率化、業務効率化、チームワーク強化、コスト削減、品質向上を実現します。このサービスは、製造業の課題を深く理解し、それに対する最適なデジタルソリューションを提供することで、企業が持続的な成長とイノベーションを達成できるようサポートします。
オンライン講座
製造業、主に購買・調達部門にお勤めの方々に向けた情報を配信しております。
新任の方やベテランの方、管理職を対象とした幅広いコンテンツをご用意しております。
お問い合わせ
コストダウンが利益に直結する術だと理解していても、なかなか前に進めることができない状況。そんな時は、newjiのコストダウン自動化機能で大きく利益貢献しよう!
(Β版非公開)