- お役立ち記事
- For SMEs: Quality Control and Improvement Methods in Injection Molding
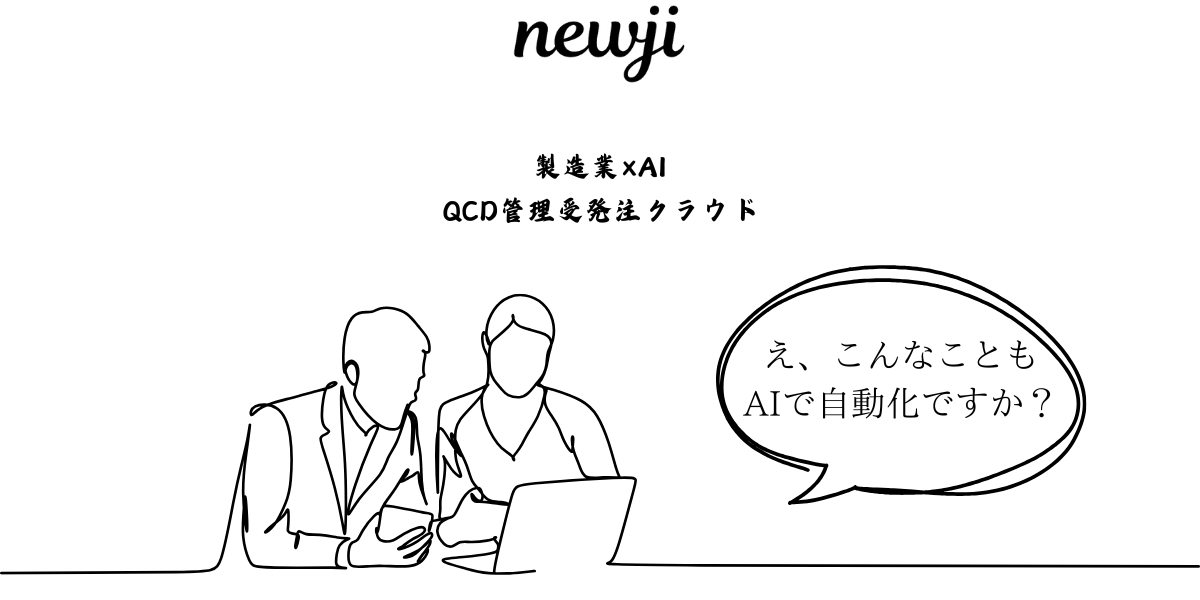
For SMEs: Quality Control and Improvement Methods in Injection Molding
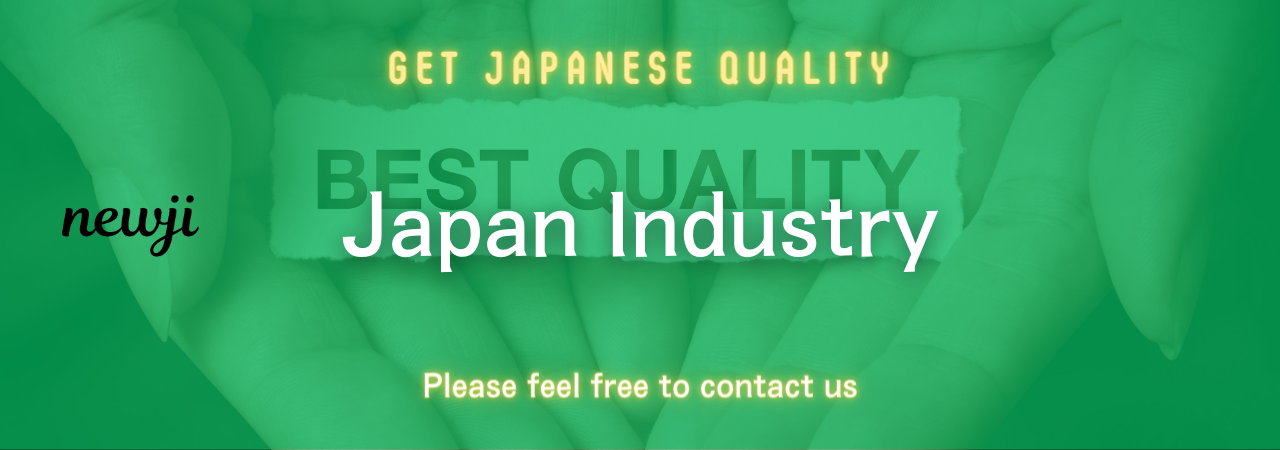
目次
Understanding Injection Molding
Injection molding is a widely used manufacturing process that produces various parts by injecting molten material into a mold.
It is particularly popular for creating plastic components due to its efficiency and versatility.
This method is widely adopted in industries ranging from automotive to consumer goods, thanks to its ability to produce high volumes of products with consistent quality.
For small and medium-sized enterprises (SMEs), mastering injection molding starts with understanding its basics.
The process involves using a molding machine, where raw material (usually thermoplastic) is heated until it becomes pliable and then injected into a precision-engineered mold.
Once cooled, the mold is opened, and the solidified part is ejected.
The Importance of Quality Control
Quality control is essential in injection molding for ensuring that the finished products meet the required specifications and standards.
For SMEs, maintaining high-quality outputs is crucial not only for customer satisfaction but also for cost efficiency.
Producing defective pieces can lead to waste, rework, and ultimately, increased production costs.
Effective quality control involves monitoring the entire production process, from the raw material selection to the final product inspection.
By doing so, issues can be identified early, preventing defects and reducing material wastage.
Common Quality Issues in Injection Molding
When diving into quality control, it’s essential to understand the common issues that can arise in injection molding.
Some of the most frequently encountered issues include:
– **Warping:** Caused by uneven cooling, which leads to parts becoming distorted.
– **Short Shots:** Occur when the mold cavity is not completely filled with material.
– **Burn Marks:** Result from excessive heat or trapped air within the mold.
– **Flash:** Happens when material leaks out of the mold cavity, creating excess material along the edges.
Recognizing these problems is a crucial first step for SMEs to develop effective strategies to minimize or eliminate them.
Methods for Quality Improvement
Optimizing the Molding Parameters
One way to improve quality is by optimizing molding parameters such as temperature, pressure, and injection speed.
Finding the ideal settings for these variables ensures that the material flows properly into the mold and cools evenly, minimizing defects like warping or short shots.
Conducting regular tests and recording the results helps in identifying the optimal parameters, which can vary between different materials or part designs.
Using High-Quality Molds
The mold itself plays a critical role in the final product’s quality.
Investing in high-quality, precisely engineered molds is essential for minimizing defects.
Regular maintenance and cleaning of molds also prevent potential issues such as flash or burn marks.
For SMEs, it might be tempting to cut costs by using cheaper molds, but this can lead to increased defects and higher long-term expenses.
Implementing Automation
Automation can significantly enhance the injection molding process by reducing human error and ensuring consistency.
Using automated systems for material feeding, mold monitoring, and part ejection improves accuracy and repeatability.
Advanced technologies like robotic arms can also handle parts with precision, reducing the risk of damage or defects.
Regular Quality Inspections
Scheduled quality checks during and after the production process can catch defects early.
Using techniques like statistical process control (SPC), SMEs can monitor production in real-time and make adjustments as necessary.
Visual inspections, as well as more advanced methods like coordinate measuring machines (CMM), help ensure that each part meets the desired specifications.
Training and Skilled Workforce
To ensure consistently high-quality products, it’s essential for SMEs to have a well-trained workforce.
Employees involved in the injection molding process should be knowledgeable about the equipment, materials, and quality control techniques.
Providing continuous training and development programs helps staff stay updated on the latest practices and technologies, ultimately leading to better product quality.
Adopting Continuous Improvement
Continuous improvement is a strategy that can significantly benefit SMEs in injection molding.
By adopting methodologies like Kaizen or Six Sigma, businesses can regularly evaluate and enhance their processes.
Continuous improvement involves analyzing production data, identifying inefficiencies, and implementing changes that lead to better quality and lower costs.
Utilizing Simulation Software
Simulation software is an invaluable tool for predicting and preventing quality issues in the injection molding process.
By using this software, SMEs can simulate the molding process and identify potential issues like flow imbalances or air entrapment before actual production begins.
This proactive approach helps in designing better molds and optimizing the process, saving both time and resources.
Supplier Management
The quality of raw materials used in injection molding significantly impacts the final product.
Building strong relationships with reliable suppliers helps ensure that SMEs receive consistent, high-quality materials.
Regular audits and communication with suppliers improve the supply chain and contribute to maintaining the desired quality standards.
Conclusion
For SMEs engaged in injection molding, focusing on quality control and continuous improvement is crucial for long-term success.
By understanding the common issues, optimizing processes, and investing in technology and training, businesses can enhance their product quality and reduce costs.
Implementing these quality improvement methods not only satisfies customer expectations but also positions SMEs competitively in the marketplace.
As the industry evolves, staying committed to innovative practices and quality assurance will be key for enduring success in the injection molding sector.
資料ダウンロード
QCD調達購買管理クラウド「newji」は、調達購買部門で必要なQCD管理全てを備えた、現場特化型兼クラウド型の今世紀最高の購買管理システムとなります。
ユーザー登録
調達購買業務の効率化だけでなく、システムを導入することで、コスト削減や製品・資材のステータス可視化のほか、属人化していた購買情報の共有化による内部不正防止や統制にも役立ちます。
NEWJI DX
製造業に特化したデジタルトランスフォーメーション(DX)の実現を目指す請負開発型のコンサルティングサービスです。AI、iPaaS、および先端の技術を駆使して、製造プロセスの効率化、業務効率化、チームワーク強化、コスト削減、品質向上を実現します。このサービスは、製造業の課題を深く理解し、それに対する最適なデジタルソリューションを提供することで、企業が持続的な成長とイノベーションを達成できるようサポートします。
オンライン講座
製造業、主に購買・調達部門にお勤めの方々に向けた情報を配信しております。
新任の方やベテランの方、管理職を対象とした幅広いコンテンツをご用意しております。
お問い合わせ
コストダウンが利益に直結する術だと理解していても、なかなか前に進めることができない状況。そんな時は、newjiのコストダウン自動化機能で大きく利益貢献しよう!
(Β版非公開)