- お役立ち記事
- For SMEs: How to Improve Product Quality with Hold Pressure Processes
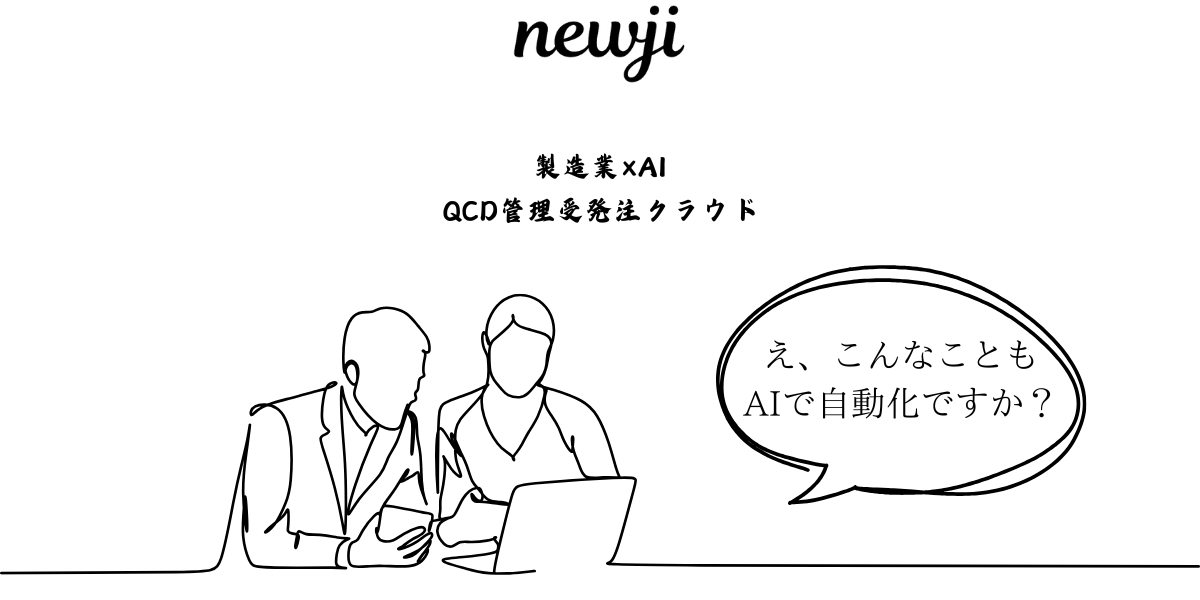
For SMEs: How to Improve Product Quality with Hold Pressure Processes
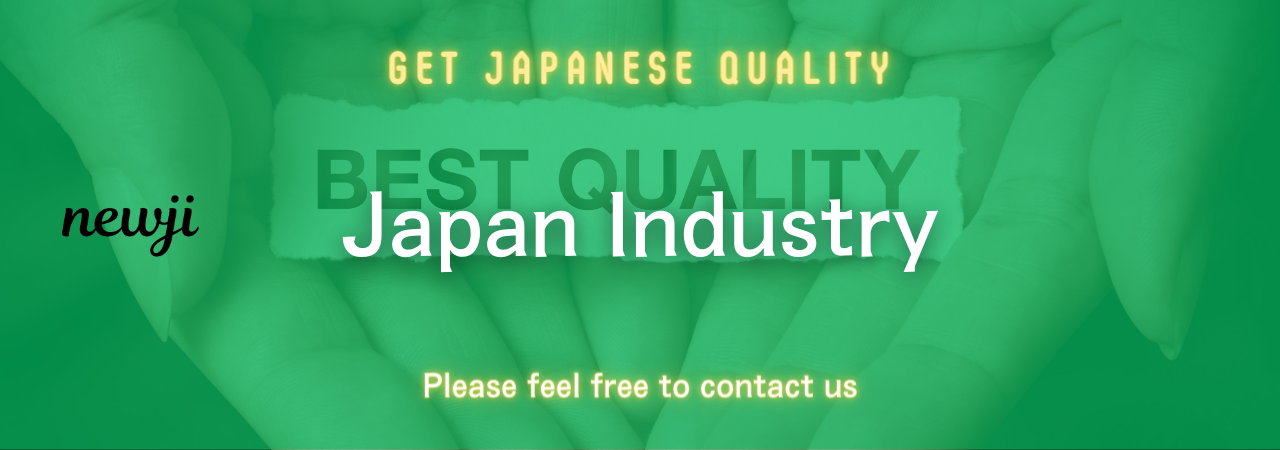
目次
Understanding the Basics of Hold Pressure Processes
Hold pressure is an essential step in the injection molding process.
It involves applying a specific amount of pressure to the molten plastic in a mold after the initial injection.
This step ensures that the molten plastic fills out all the cavities of the mold, correcting any shrinkage and improving the product’s overall integrity.
For small to medium-sized enterprises (SMEs), gaining an understanding of the hold pressure process can greatly enhance product quality.
By optimizing this phase, businesses can reduce defects and ensure that their products meet the desired specifications consistently.
Why Hold Pressure Matters
Without adequate hold pressure, product quality can suffer significantly.
When the molten plastic cools down rapidly without enough pressure, it can cause voids, sink marks, and dimensional inaccuracies.
This negatively affects the aesthetics and functionality of the final product.
Moreover, hold pressure helps in maintaining a uniform distribution of material throughout the mold.
This uniformity is vital for the structural strength and durability of the product.
For SMEs, especially those working with tight budgets, reducing material wastage and improving product consistency can directly impact the bottom line positively.
Steps to Optimize Hold Pressure for SMEs
1. Analyze Your Current Process
The first step in optimizing hold pressure is to understand your existing injection molding process.
Evaluate cycle times, pressures used, and any common defects in your products.
Analyzing the current process with performance metrics will give you invaluable insights into where improvements are needed.
Consulting with engineers or leveraging technical resources could also uncover hidden inefficiencies.
2. Test Different Pressure Levels
Once you’ve analyzed the current process, it’s time to experiment.
Varying the hold pressure levels can show you what works best for your specific products.
It’s critical to document each test meticulously, comparing outcomes and looking for trends that signify optimal pressure levels.
With each iteration, you can refine and identify the best parameters for minimizing defects and material usage.
3. Train Your Team
A well-trained team is crucial for any process improvement.
Ensure that your production staff understands the significance of hold pressure and how to implement any new procedures effectively.
Training sessions, instructional materials, and hands-on workshops can facilitate knowledge transfer and empower your team to contribute to quality improvements.
With everyone on the same page, your SME will be adept at making swift adjustments, addressing challenges proactively, and keeping the process optimized.
Invest in Technology to Enhance Control
Upgrade Machinery
Modern injection molding machines offer greater precision and control over the hold pressure process.
While upgrading machinery represents a significant investment, it often pays off in terms of improved product quality and reduced operational costs.
Advanced controls allow for fine-tuning and maintaining consistent hold pressure that manual settings simply can’t replicate.
When considering an upgrade, prioritize machines offering features like automated pressure adjustments and closed-loop control systems.
Utilize Sensors and Data Analytics
Integrating sensors into your molding machinery can provide real-time data on pressure, temperature, and other critical parameters.
This information is valuable for identifying any deviations from optimal pressure levels swiftly.
Coupled with data analytics tools, sensors can also highlight long-term patterns, helping you make informed decisions about process improvements.
SMEs should consider harnessing the power of big data to ensure consistency and quality across production batches.
Rethink Material Usage
Select the Right Materials
Not all materials respond the same way to pressure.
It’s important to choose the right raw materials that fit well with your hold pressure capabilities.
Collaborate with materials specialists to select resins or polymers that provide the best flow characteristics, thermal stability, and resistance to defects under the pressures you apply.
Sometimes, slight changes to the material or resin can lead to significant improvements in product quality while still running within budget constraints.
Experiment with Additives
Additives can enhance the properties of your plastic materials, affecting everything from melt flow to shrinkage behavior.
Conduct controlled experiments to determine which additives work best in concert with your selected hold pressure levels.
Be sure that any additive used does not compromise the structural integrity or safety of the final product.
Working with your material suppliers can also yield recommendations for additives that maximize performance within specific pressure ranges.
Benefits of Optimized Hold Pressure
Optimizing hold pressure goes beyond enhancing product finish or reducing defects.
Improved processes lead to a better reputation as a reliable manufacturer, opening more business opportunities.
Cost savings are realized through reduced material wastage, fewer rejected products, and less rework.
SMEs gain competitive advantage by offering consistent quality, which is increasingly vital in today’s precise, demand-driven market.
Optimized processes also ensure sustainable practices as material efficiency is improved and energy usage is potentially curtailed.
A focus on high-quality outputs aligned with reduced environmental impact is advantageous both economically and socially.
Remember, the journey to optimizing hold pressure is iterative.
Consistent analysis, testing, and adaptation in response to changing demands ensure that SMEs can continue to thrive by producing superior quality products.
資料ダウンロード
QCD調達購買管理クラウド「newji」は、調達購買部門で必要なQCD管理全てを備えた、現場特化型兼クラウド型の今世紀最高の購買管理システムとなります。
ユーザー登録
調達購買業務の効率化だけでなく、システムを導入することで、コスト削減や製品・資材のステータス可視化のほか、属人化していた購買情報の共有化による内部不正防止や統制にも役立ちます。
NEWJI DX
製造業に特化したデジタルトランスフォーメーション(DX)の実現を目指す請負開発型のコンサルティングサービスです。AI、iPaaS、および先端の技術を駆使して、製造プロセスの効率化、業務効率化、チームワーク強化、コスト削減、品質向上を実現します。このサービスは、製造業の課題を深く理解し、それに対する最適なデジタルソリューションを提供することで、企業が持続的な成長とイノベーションを達成できるようサポートします。
オンライン講座
製造業、主に購買・調達部門にお勤めの方々に向けた情報を配信しております。
新任の方やベテランの方、管理職を対象とした幅広いコンテンツをご用意しております。
お問い合わせ
コストダウンが利益に直結する術だと理解していても、なかなか前に進めることができない状況。そんな時は、newjiのコストダウン自動化機能で大きく利益貢献しよう!
(Β版非公開)