- お役立ち記事
- “Revolutionizing Japanese Manufacturing: How Odor Sensors are Transforming Quality Control”
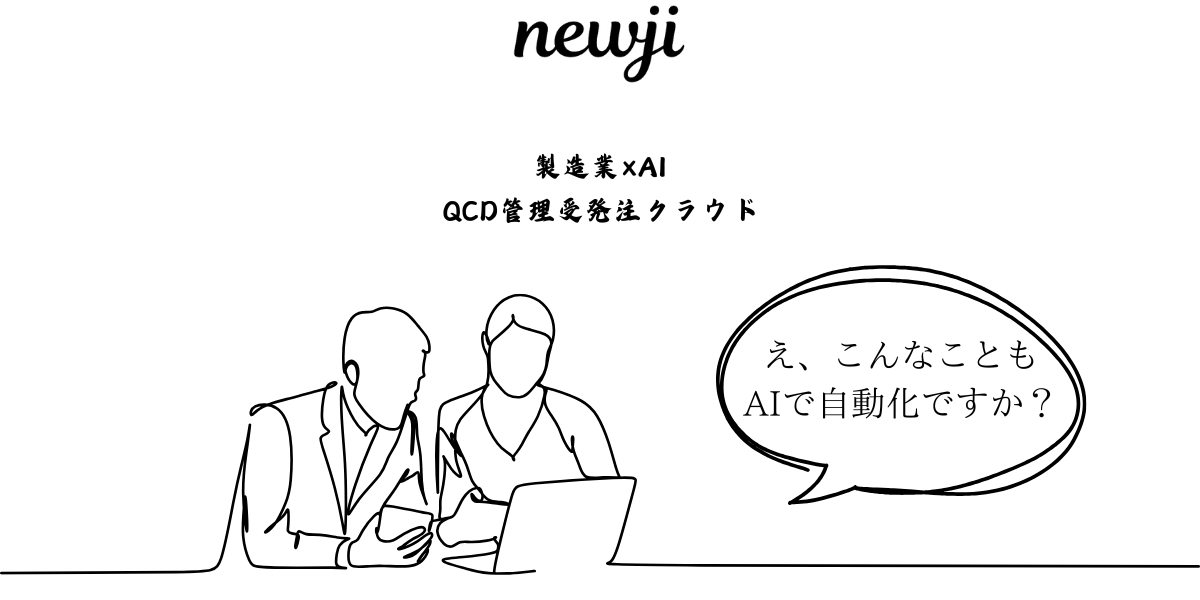
“Revolutionizing Japanese Manufacturing: How Odor Sensors are Transforming Quality Control”
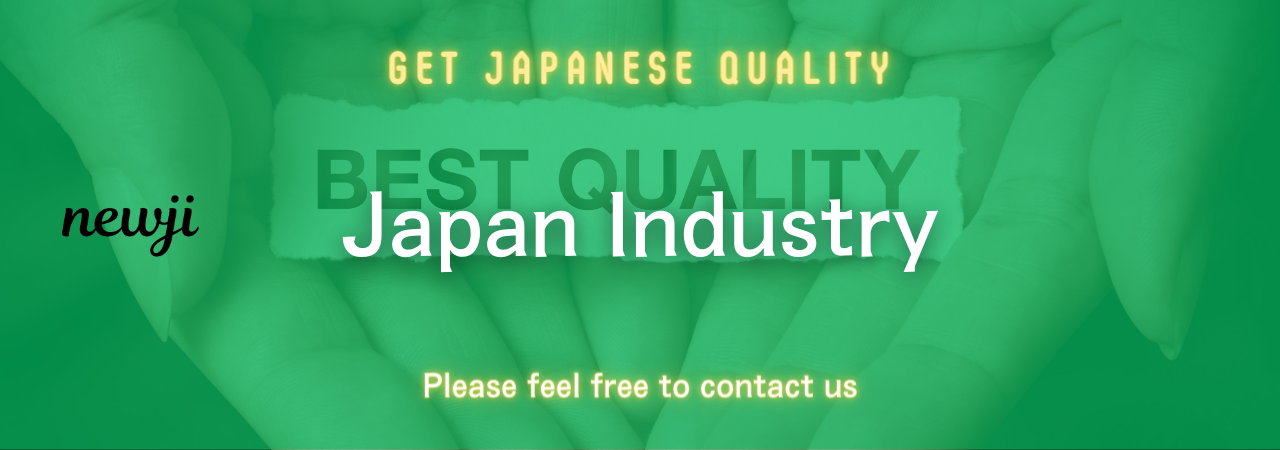
目次
Introduction to Odor Sensors in Japanese Manufacturing
Japanese manufacturing has long been synonymous with precision, quality, and innovation. In recent years, the integration of advanced technologies has further elevated these standards. One such innovation is the use of odor sensors in quality control processes. These sensors are revolutionizing the way manufacturers ensure product excellence, offering new dimensions of inspection and analysis that were previously unattainable. This article delves into how odor sensors are transforming quality control in Japanese manufacturing, exploring their benefits, challenges, and the strategic approaches required for successful implementation.
The Role of Odor Sensors in Quality Control
Quality control is a critical aspect of manufacturing, ensuring that products meet the desired standards and specifications. Traditional quality control methods have relied heavily on visual inspections, manual testing, and basic instrumentation. However, as products and processes become more complex, these methods alone are no longer sufficient. Odor sensors, also known as electronic noses, provide an additional layer of quality assurance by detecting and analyzing volatile compounds that may indicate defects or inconsistencies in products.
How Odor Sensors Work
Odor sensors mimic the human sense of smell by detecting volatile organic compounds (VOCs) emitted by products during manufacturing. These sensors consist of an array of chemical sensors that respond to different VOCs, creating a unique fingerprint for each product. Advanced algorithms then analyze these fingerprints to identify patterns and anomalies that may signify quality issues. This technology allows for real-time monitoring and early detection of defects, enabling manufacturers to address issues promptly and maintain high-quality standards.
Applications in Various Industries
Odor sensors are versatile tools used across various industries beyond traditional manufacturing. In the food and beverage sector, they ensure freshness and detect spoilage. In the pharmaceutical industry, they monitor the integrity of products and packaging. Automotive manufacturers use odor sensors to assess material quality and detect off-gassing from components. This wide range of applications highlights the adaptability of odor sensors in enhancing quality control processes across different manufacturing sectors.
Advantages of Using Odor Sensors
Integrating odor sensors into quality control systems offers numerous benefits that contribute to overall manufacturing excellence.
Enhanced Detection Capabilities
Odor sensors are capable of detecting subtle changes in VOCs that may be imperceptible to human senses or traditional instruments. This heightened sensitivity allows for the identification of minor defects early in the production process, reducing the likelihood of faulty products reaching the market.
Real-Time Monitoring
One of the significant advantages of odor sensors is their ability to provide real-time data. Continuous monitoring enables manufacturers to track quality throughout the production cycle, facilitating immediate corrective actions when anomalies are detected. This proactive approach minimizes waste and downtime, enhancing overall efficiency.
Consistency and Reliability
Human sensory assessment can be subjective and vary between operators. Odor sensors offer consistent and objective measurements, ensuring uniformity in quality assessments. This reliability is crucial for maintaining high standards, especially in large-scale manufacturing operations where consistency is paramount.
Cost Efficiency
While the initial investment in odor sensor technology may be significant, the long-term cost savings are substantial. By reducing the rate of defective products, minimizing waste, and preventing costly recalls, manufacturers can realize a strong return on investment. Additionally, the automation of quality control processes decreases labor costs associated with manual inspections.
Challenges and Considerations
Despite their numerous advantages, the implementation of odor sensors in quality control presents several challenges that manufacturers must address to ensure successful integration.
Initial Investment and Maintenance
The purchase and installation of odor sensor systems require a considerable upfront investment. Furthermore, maintaining and calibrating these sensors to ensure accurate readings incur ongoing costs. Manufacturers must carefully evaluate the cost-benefit ratio and plan for these expenses in their budgeting process.
Technical Expertise
Operating and interpreting data from odor sensors necessitates specialized knowledge. Manufacturers may need to invest in training for their staff or hire technical experts to manage these systems effectively. The complexity of the technology can be a barrier for organizations lacking the necessary expertise.
Integration with Existing Systems
Integrating odor sensors with existing quality control and manufacturing systems can be challenging. Compatibility issues, data synchronization, and workflow adjustments must be addressed to ensure seamless operation. A thorough assessment of current systems and strategic planning are essential for successful integration.
Environmental Factors
Odor sensors can be sensitive to environmental variables such as temperature, humidity, and background VOC levels. Variations in these factors can affect sensor performance and data accuracy. Manufacturers must implement measures to control environmental conditions or calibrate sensors to account for these influences.
Supplier Negotiation Techniques for Odor Sensors
When procuring odor sensor technology, effective negotiation with suppliers is crucial to secure favorable terms and ensure the acquisition of high-quality equipment. The following strategies can aid in successful supplier negotiations.
Understanding Market Conditions
Before entering negotiations, it is vital to comprehend the current market landscape for odor sensors. Knowledge of supply and demand dynamics, pricing trends, and the availability of advanced features allows manufacturers to make informed decisions and identify opportunities for favorable agreements.
Evaluating Supplier Capabilities
Assessing the capabilities and credibility of potential suppliers is essential. Manufacturers should consider the supplier’s track record, technological expertise, after-sales support, and ability to customize solutions to meet specific quality control needs. Engaging with reputable suppliers ensures access to reliable and cutting-edge technology.
Leveraging Bulk Purchasing
For large-scale manufacturing operations, procuring odor sensors in bulk can lead to significant cost savings. Negotiating volume discounts or long-term contracts with suppliers can reduce per-unit costs and secure a steady supply of sensors, contributing to overall cost efficiency.
Emphasizing Total Cost of Ownership
When negotiating, it is important to consider the total cost of ownership, which includes not only the initial purchase price but also installation, maintenance, calibration, and operational costs. Focusing on overall value rather than just upfront costs can lead to more sustainable and cost-effective procurement decisions.
Building Strong Supplier Relationships
Establishing and maintaining strong relationships with suppliers fosters trust and collaboration. Open communication, mutual respect, and fair dealings can lead to better terms, priority support, and opportunities for joint innovation. Long-term partnerships are beneficial for both manufacturers and suppliers in achieving shared goals.
Best Practices for Implementing Odor Sensors in Quality Control
To maximize the benefits of odor sensors in quality control, manufacturers should adhere to best practices throughout the implementation process.
Comprehensive Needs Assessment
Begin by conducting a thorough assessment of quality control requirements and identifying specific areas where odor sensors can add value. Understanding the types of VOCs relevant to the products and processes helps in selecting appropriate sensor technology and configuring systems effectively.
Selecting the Right Technology
Choose odor sensor technology that aligns with the specific needs of the manufacturing process. Factors to consider include sensitivity, selectivity, response time, durability, and ease of integration with existing systems. Collaborate with suppliers to customize sensors that meet these requirements.
Training and Skill Development
Invest in training programs to equip staff with the necessary skills to operate, maintain, and interpret data from odor sensors. Comprehensive training ensures that the technology is utilized effectively and that personnel can respond appropriately to quality control insights.
Data Management and Analysis
Implement robust data management systems to handle the large volumes of data generated by odor sensors. Utilize advanced analytics and machine learning algorithms to extract meaningful insights, identify trends, and predict potential quality issues. Effective data management enhances decision-making and process optimization.
Continuous Improvement and Feedback Loops
Establish continuous improvement processes that incorporate feedback from odor sensor data. Regularly review and refine quality control strategies based on sensor insights to enhance product quality and operational efficiency. Foster a culture of proactive quality management and responsiveness to emerging challenges.
Market Conditions and Trends
The market for odor sensors is evolving rapidly, driven by advancements in technology and increasing demand for higher quality standards.
Technological Advancements
Recent developments in sensor technology, including improved sensitivity, miniaturization, and integration with Internet of Things (IoT) platforms, are expanding the capabilities of odor sensors. These advancements enable more precise detection, remote monitoring, and seamless data integration, enhancing their applicability in diverse manufacturing environments.
Increased Demand for Quality Assurance
As global competition intensifies, manufacturers are prioritizing quality assurance to differentiate their products in the market. Odor sensors offer a competitive edge by providing robust quality control measures that ensure product excellence and customer satisfaction.
Regulatory Compliance
Stringent regulatory standards in various industries mandate rigorous quality control measures. Odor sensors help manufacturers comply with these regulations by offering reliable and traceable quality assessments, reducing the risk of non-compliance and associated penalties.
Sustainability and Environmental Considerations
There is a growing emphasis on sustainability and reducing environmental impact in manufacturing. Odor sensors contribute to these goals by enabling the detection of VOCs and hazardous emissions, facilitating more environmentally friendly production processes and compliance with environmental regulations.
Advantages and Disadvantages of Odor Sensors
While odor sensors provide significant benefits, it is important to consider both their advantages and potential drawbacks to make informed decisions.
Advantages
- High Sensitivity: Capable of detecting low concentrations of VOCs, ensuring early identification of quality issues.
- Real-Time Monitoring: Provides immediate feedback, allowing for prompt corrective actions.
- Consistency: Delivers objective and repeatable measurements, reducing variability in quality assessments.
- Cost Savings: Minimizes waste and reduces costs associated with defective products and recalls.
- Versatility: Applicable across various industries and adaptable to different manufacturing processes.
Disadvantages
- Initial Costs: High upfront investment for purchasing and installing sensor systems.
- Maintenance Requirements: Requires regular calibration and maintenance to ensure accuracy.
- Technical Complexity: Necessitates specialized knowledge for operation and data interpretation.
- Environmental Sensitivity: Performance can be affected by changes in temperature, humidity, and background VOC levels.
- Integration Challenges: May require significant adjustments to existing systems and workflows.
Strategic Implementation in Japanese Manufacturing
Japanese manufacturers are renowned for their commitment to quality and continuous improvement. Integrating odor sensors into their quality control processes aligns with these values and supports the pursuit of manufacturing excellence.
Aligning with Lean Manufacturing Principles
Japanese manufacturing often employs lean principles aimed at eliminating waste and optimizing processes. Odor sensors contribute to these objectives by enabling precise quality control, reducing defects, and minimizing resource wastage. This alignment enhances overall efficiency and competitiveness.
Emphasizing Kaizen and Continuous Improvement
The Kaizen philosophy of continuous improvement is central to Japanese manufacturing. Odor sensors provide valuable data that feeds into Kaizen initiatives, allowing for ongoing refinements in production processes and quality standards. This fosters a culture of excellence and adaptability.
Collaborative Supplier Relationships
Japanese manufacturers typically maintain close collaborative relationships with suppliers, fostering mutual trust and innovation. When implementing odor sensors, working closely with suppliers ensures that the technology is tailored to specific needs and that there is ongoing support for optimization and troubleshooting.
Focus on Training and Development
Investing in employee training is crucial for the effective use of odor sensors. Japanese manufacturers prioritize skill development, ensuring that their workforce is proficient in operating advanced technologies and interpreting quality control data. This focus on training enhances the overall effectiveness of odor sensor integration.
Future Outlook and Trends
The integration of odor sensors in quality control is set to expand further, driven by technological advancements and evolving manufacturing needs.
Integration with Artificial Intelligence
The convergence of odor sensors with artificial intelligence (AI) and machine learning is enhancing their capabilities. AI algorithms can analyze complex data patterns from odor sensors, enabling predictive maintenance, anomaly detection, and more sophisticated quality control measures.
Expansion into New Industries
While already prevalent in certain sectors, the application of odor sensors is expected to grow in industries such as electronics, textiles, and aerospace. These industries can benefit from the precise quality control and defect detection capabilities offered by odor sensors.
Enhanced Connectivity and IoT Integration
The rise of the Internet of Things (IoT) is facilitating greater connectivity between odor sensors and other manufacturing systems. This integration enables more comprehensive monitoring, data sharing, and real-time decision-making, further enhancing quality control processes.
Miniaturization and Portability
Advancements in sensor technology are leading to smaller, more portable odor sensors. This trend allows for more flexible deployment across various points in the manufacturing process, enhancing the versatility and reach of quality control measures.
Conclusion
Odor sensors are playing a pivotal role in transforming quality control within Japanese manufacturing. Their ability to detect subtle VOCs, provide real-time monitoring, and ensure consistent measurements aligns with the high standards of Japanese manufacturing excellence. Despite challenges such as initial costs and technical complexity, the advantages of odor sensors in enhancing product quality, reducing waste, and supporting continuous improvement make them a valuable investment for manufacturers. By adopting strategic implementation practices and staying abreast of technological advancements, Japanese manufacturers can continue to lead in quality and innovation, ensuring their products meet the evolving demands of the global market.
資料ダウンロード
QCD調達購買管理クラウド「newji」は、調達購買部門で必要なQCD管理全てを備えた、現場特化型兼クラウド型の今世紀最高の購買管理システムとなります。
ユーザー登録
調達購買業務の効率化だけでなく、システムを導入することで、コスト削減や製品・資材のステータス可視化のほか、属人化していた購買情報の共有化による内部不正防止や統制にも役立ちます。
NEWJI DX
製造業に特化したデジタルトランスフォーメーション(DX)の実現を目指す請負開発型のコンサルティングサービスです。AI、iPaaS、および先端の技術を駆使して、製造プロセスの効率化、業務効率化、チームワーク強化、コスト削減、品質向上を実現します。このサービスは、製造業の課題を深く理解し、それに対する最適なデジタルソリューションを提供することで、企業が持続的な成長とイノベーションを達成できるようサポートします。
オンライン講座
製造業、主に購買・調達部門にお勤めの方々に向けた情報を配信しております。
新任の方やベテランの方、管理職を対象とした幅広いコンテンツをご用意しております。
お問い合わせ
コストダウンが利益に直結する術だと理解していても、なかなか前に進めることができない状況。そんな時は、newjiのコストダウン自動化機能で大きく利益貢献しよう!
(Β版非公開)