- お役立ち記事
- Defect Prevention Strategies for Insert Molding
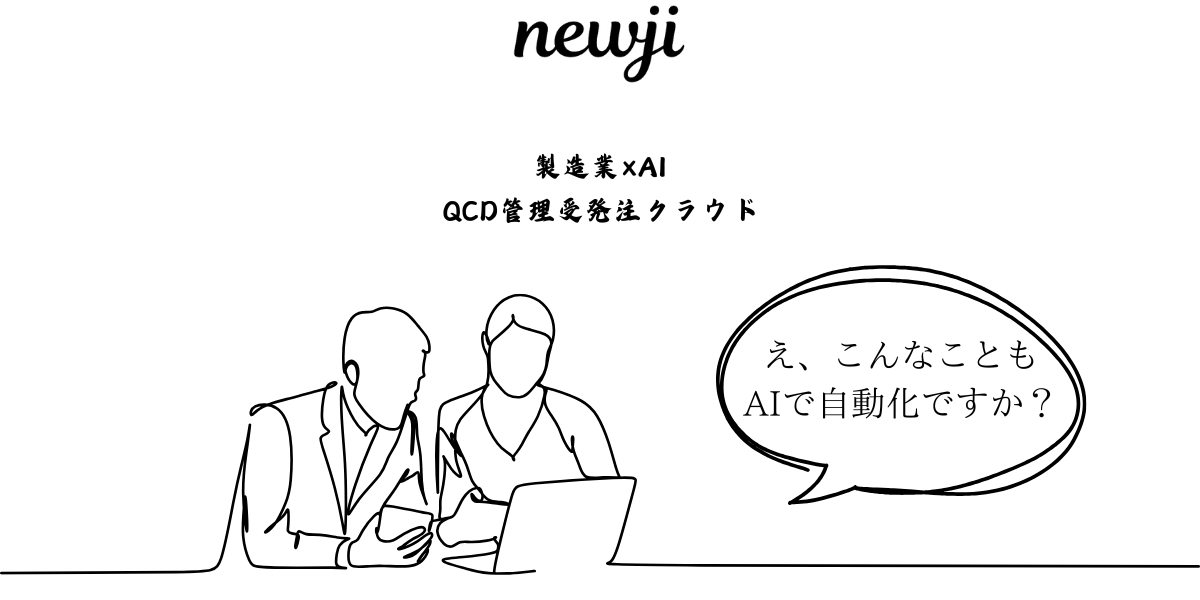
Defect Prevention Strategies for Insert Molding
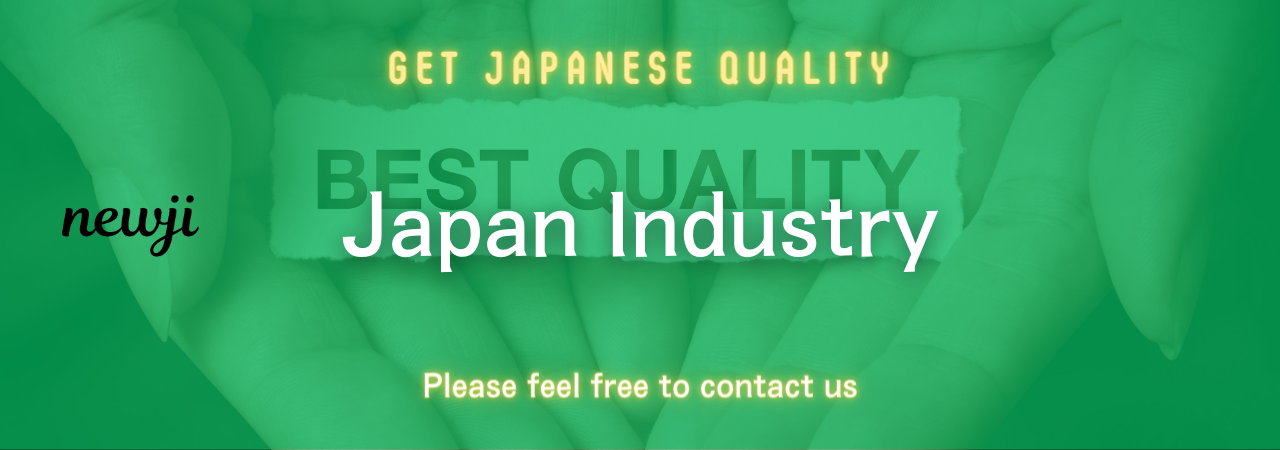
目次
Understanding Insert Molding
Insert molding is a specialized process in the manufacturing industry where a pre-formed component, often metal, is placed into a mold and then encapsulated with plastic or another material.
This process is widely used to combine multiple materials into a single finished product, enhancing the part’s strength and function.
The success of insert molding hinges on precise alignment and compatibility between the insert and the molding material.
This can lead to improved quality and performance of the final product but also presents unique challenges.
Defects in insert molding can arise due to a variety of factors, including material incompatibility, improper mold design, and process inconsistencies.
The Importance of Defect Prevention
Preventing defects in insert molding is crucial for ensuring product durability and functionality.
Defective parts can cause significant issues, not only increasing waste and costs but also damaging the manufacturer’s reputation.
The key to effective defect prevention lies in comprehensive understanding and control of the manufacturing process.
This includes careful selection of materials, precise mold design, and rigorous process control.
By implementing preventive strategies, manufacturers can reduce defects, improve product quality, and maintain customer satisfaction.
Key Strategies for Defect Prevention
There are several strategies manufacturers can employ to prevent defects in insert molding.
These strategies focus on optimizing materials, processes, and machinery to ensure quality and efficiency.
Material Selection and Compatibility
One of the primary considerations in insert molding is the compatibility between the insert and the molding material.
Incompatible materials can lead to poor adhesion, warping, or surface defects.
Therefore, it is essential to select materials that not only meet the functional requirements of the finished product but also work well together.
Testing and analysis can help ensure that the selected materials will perform as expected under the given conditions.
Optimized Mold Design
A well-designed mold is critical for preventing defects in insert molding.
The mold must accommodate the insert precisely, allowing for consistent alignment and stability during the molding process.
Attention to detail in mold design can prevent common issues such as misalignment, air gaps, or material leakage.
Using simulation software, manufacturers can test and refine mold designs before production, reducing the risk of defects.
Process Control and Consistency
Maintaining control over the insert molding process is crucial for minimizing defects.
This involves monitoring and adjusting variables like temperature, pressure, and cycle time to ensure they remain within optimal ranges.
Consistent processes lead to consistent products, reducing variability and the likelihood of defects.
Implementing statistical process control (SPC) can help manufacturers track process consistency and identify potential issues before they escalate.
Quality Inspections and Testing
Regular quality inspections and testing are vital components of a defect prevention strategy.
These measures help identify defects early, enabling corrective action before full-scale production.
Both visual inspections and more advanced testing techniques, like ultrasonic or X-ray testing, can be used depending on the complexity of the part and the materials involved.
Ongoing testing and feedback loops help in refining processes and improving overall product quality.
Additional Tips for Enhanced Control
Beyond the foundational strategies, there are additional practices manufacturers can adopt to further reduce the risk of defects in insert molding.
Employee Training and Expertise
Well-trained employees are better equipped to recognize and respond to potential issues in the insert molding process.
Regular training programs ensure that staff are up-to-date with the latest technologies, techniques, and quality standards.
Experienced employees can also contribute valuable insights into process improvements, drawing from their hands-on experience to enhance overall operation efficiency.
Use of Advanced Technology
Embracing advanced technology can significantly improve defect prevention efforts.
Automation and robotics can enhance precision and repeatability, while smart sensors and IoT devices offer real-time monitoring and analytics.
These technologies can provide insights into the manufacturing process, helping identify areas for improvement and aiding in quick resolution of issues when they arise.
Conclusion
Defect prevention in insert molding requires a comprehensive approach that encompasses material selection, mold design, process control, and quality assurance.
By implementing these strategies, manufacturers can significantly reduce defects, leading to higher-quality products and greater customer satisfaction.
Investing in training and technology further supports defect prevention efforts, ensuring that manufacturers remain competitive in a demanding industry.
Adopting a proactive mindset toward defect prevention not only improves product outcomes but also contributes to operational efficiency and cost savings in the long term.
資料ダウンロード
QCD調達購買管理クラウド「newji」は、調達購買部門で必要なQCD管理全てを備えた、現場特化型兼クラウド型の今世紀最高の購買管理システムとなります。
ユーザー登録
調達購買業務の効率化だけでなく、システムを導入することで、コスト削減や製品・資材のステータス可視化のほか、属人化していた購買情報の共有化による内部不正防止や統制にも役立ちます。
NEWJI DX
製造業に特化したデジタルトランスフォーメーション(DX)の実現を目指す請負開発型のコンサルティングサービスです。AI、iPaaS、および先端の技術を駆使して、製造プロセスの効率化、業務効率化、チームワーク強化、コスト削減、品質向上を実現します。このサービスは、製造業の課題を深く理解し、それに対する最適なデジタルソリューションを提供することで、企業が持続的な成長とイノベーションを達成できるようサポートします。
オンライン講座
製造業、主に購買・調達部門にお勤めの方々に向けた情報を配信しております。
新任の方やベテランの方、管理職を対象とした幅広いコンテンツをご用意しております。
お問い合わせ
コストダウンが利益に直結する術だと理解していても、なかなか前に進めることができない状況。そんな時は、newjiのコストダウン自動化機能で大きく利益貢献しよう!
(Β版非公開)