- お役立ち記事
- How to Avoid Troubles in Nylon Molding
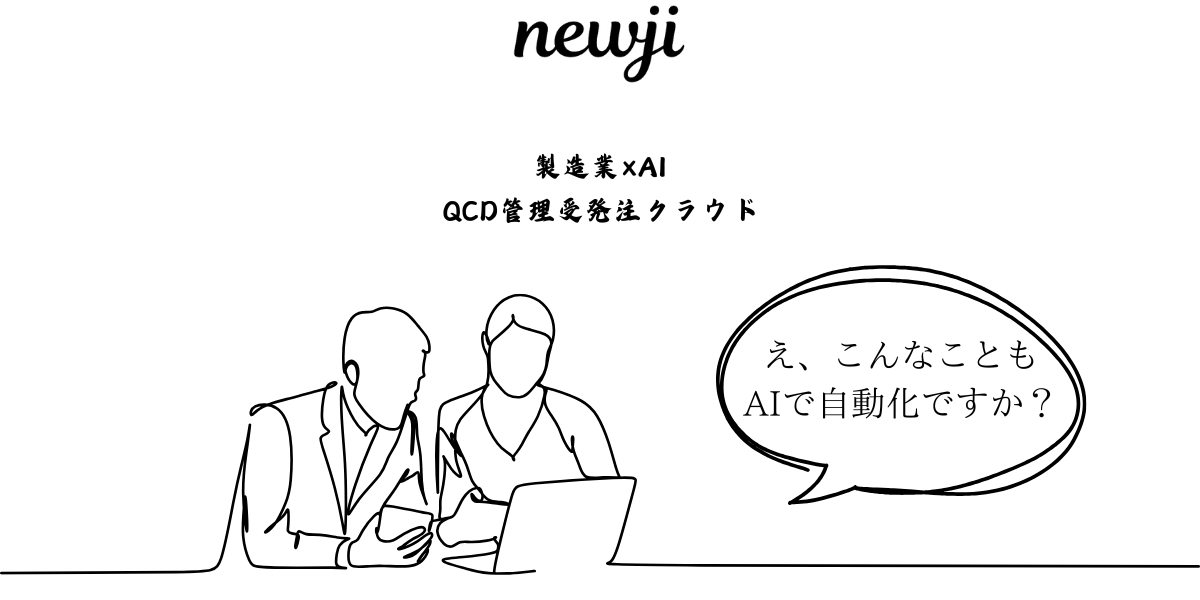
How to Avoid Troubles in Nylon Molding
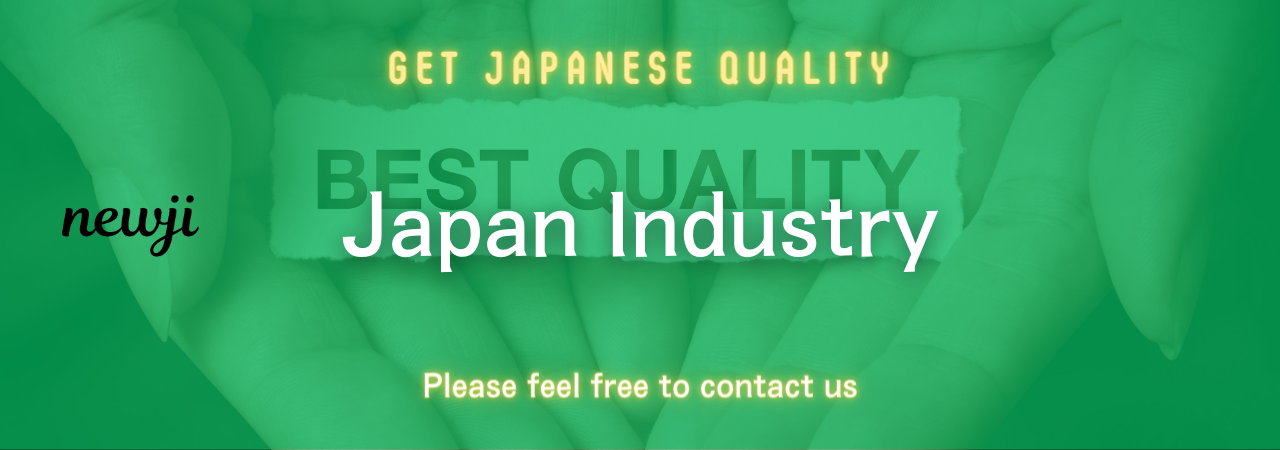
目次
Understanding Nylon Molding
Nylon molding is a widespread method used in manufacturing to create durable and lightweight plastic parts.
Commonly employed in automotive, industrial, and consumer products, nylon components require precision and expertise in the molding process.
Despite its prevalence, manufacturers often encounter various challenges that can affect the quality and efficiency of nylon molding.
Let’s dive into some strategies to avoid troubles in nylon molding and achieve optimal results.
Choose the Right Type of Nylon
Nylon comes in different grades and formulations, each designed for specific applications.
Understanding these variations is the first step in successful nylon molding.
Nylon 6 and Nylon 66 are the most common types, each offering unique properties.
Nylon 6, for instance, has higher impact resistance and is often used in products that require flexibility.
On the other hand, Nylon 66 offers greater thermal stability and is used in high-temperature environments.
Selecting the appropriate type based on your application needs is critical to mitigating troubles related to product performance and longevity.
Maintain Proper Moisture Levels
Nylon is hygroscopic, meaning it absorbs moisture from the air.
Excessive moisture can lead to defects such as bubbles, splay, and dimensional inaccuracies.
To avoid these issues, it’s crucial to dry nylon resins adequately before molding.
Invest in a reliable drying system with accurate temperature controls.
Typically, drying nylon for a minimum of 4-6 hours at 80-100°C should suffice.
Make sure to check the manufacturer’s guidelines for specific drying conditions, as these can vary between nylon grades.
Optimize Molding Parameters
Setting the right processing parameters is essential to overcoming challenges in nylon molding.
This includes adjusting the injection temperature, pressure, speed, and cooling time.
Here’s how each parameter can impact the molding process:
Injection Temperature
Ensure that the barrel temperature is adequately set to melt the nylon without degradation.
Too low a temperature can result in incomplete filling, while too high a temperature may cause thermal degradation.
A typical processing temperature for nylon ranges from 230°C to 300°C.
Injection Pressure and Speed
Find the optimal balance that ensures complete cavity filling and avoids excessive shear stress.
High pressure and speed can cause inconsistency and flash.
It’s important to perform trial runs to fine-tune these parameters.
Cooling Time
Efficient cooling is necessary to maintain part dimensions and surface finish.
Nylon has a high crystallization rate, so it’s crucial to control the mold temperature.
Maintain uniform cooling to prevent warping and residual stress, and consult with your mold manufacturer on recommended practices.
Design Considerations for Nylon Parts
The design of the molded part plays a significant role in minimizing issues.
Here are some key considerations when designing nylon parts:
Wall Thickness
Aim for uniform wall thickness throughout the part to prevent warping and sink marks.
If varying thickness is unavoidable, transition gradually to minimize stress concentrations.
Draft Angles
Incorporate an adequate draft angle, typically between 1° to 2°, to facilitate easy ejection of the part from the mold.
This reduces the chances of sticking and damage during removal.
Flow Path
Optimize the flow path by minimizing bends and abrupt changes.
A smooth flow path ensures even filling and reduces the risk of defects such as short shots or incomplete filling.
Select Proper Equipment and Maintenance
Using high-quality and well-maintained equipment is equally important in preventing issues.
Ensure that molds and machines are cleaned and serviced regularly.
This reduces downtime and minimizes the risk of contamination.
Invest in mold sensors and process monitoring tools to detect any irregularities during production.
This helps in making real-time adjustments to the molding parameters.
Train and Educate the Workforce
An experienced and knowledgeable workforce is invaluable in avoiding problems in nylon molding.
Provide regular training and workshops on the latest industry practices and technologies.
Encourage a culture of continuous improvement and problem-solving.
Skilled operators can quickly identify and address potential issues, ensuring consistent quality and efficiency in the production line.
Conduct Quality Control and Testing
Implement stringent quality control measures throughout the manufacturing process.
Conduct regular inspections and testing to identify defects early.
Use tools like X-ray inspection or ultrasonic testing to detect internal flaws that may not be visible to the naked eye.
Quality control efforts ensure that only parts meeting the required standards are dispatched to customers.
In conclusion, understanding the complexities of nylon molding and implementing the right strategies can prevent common problems.
By choosing the right materials, maintaining proper conditions, and optimizing design and process parameters, you can enhance the quality and reliability of nylon molded parts.
Regular maintenance, workforce training, and quality control further contribute to achieving seamless production.
Heeding these guidelines will steer you towards successful nylon molding with minimal disruptions.
資料ダウンロード
QCD調達購買管理クラウド「newji」は、調達購買部門で必要なQCD管理全てを備えた、現場特化型兼クラウド型の今世紀最高の購買管理システムとなります。
ユーザー登録
調達購買業務の効率化だけでなく、システムを導入することで、コスト削減や製品・資材のステータス可視化のほか、属人化していた購買情報の共有化による内部不正防止や統制にも役立ちます。
NEWJI DX
製造業に特化したデジタルトランスフォーメーション(DX)の実現を目指す請負開発型のコンサルティングサービスです。AI、iPaaS、および先端の技術を駆使して、製造プロセスの効率化、業務効率化、チームワーク強化、コスト削減、品質向上を実現します。このサービスは、製造業の課題を深く理解し、それに対する最適なデジタルソリューションを提供することで、企業が持続的な成長とイノベーションを達成できるようサポートします。
オンライン講座
製造業、主に購買・調達部門にお勤めの方々に向けた情報を配信しております。
新任の方やベテランの方、管理職を対象とした幅広いコンテンツをご用意しております。
お問い合わせ
コストダウンが利益に直結する術だと理解していても、なかなか前に進めることができない状況。そんな時は、newjiのコストダウン自動化機能で大きく利益貢献しよう!
(Β版非公開)