- お役立ち記事
- Technical Points for Manufacturing High-Quality Products with Precision Injection Molding
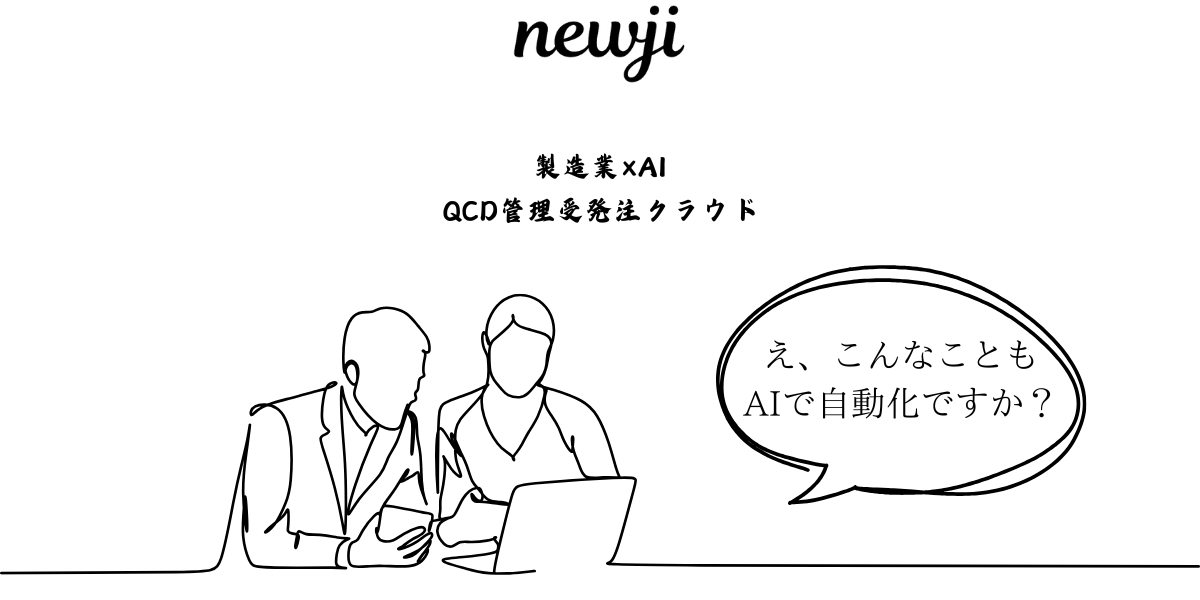
Technical Points for Manufacturing High-Quality Products with Precision Injection Molding
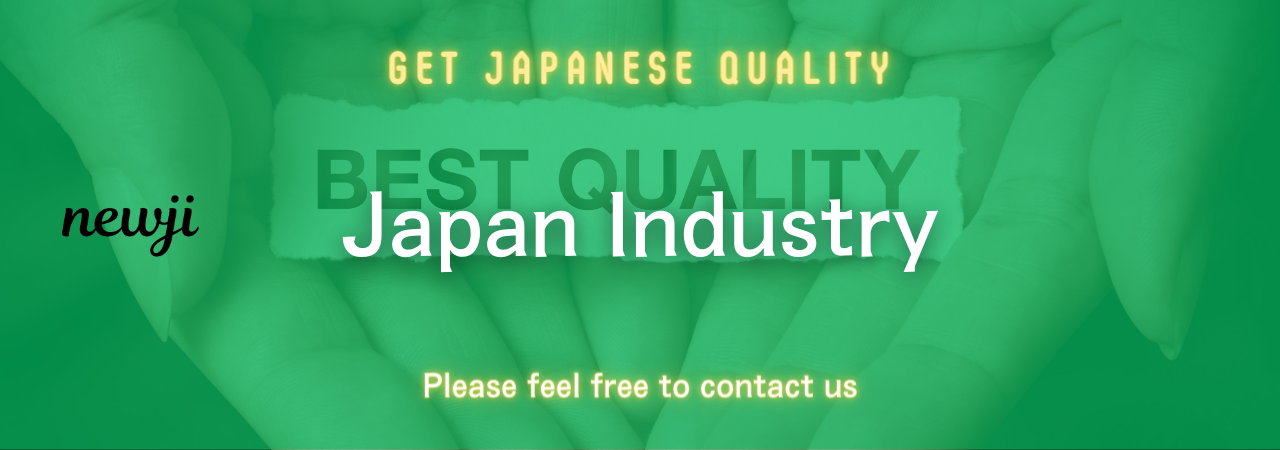
目次
Understanding Precision Injection Molding
Precision injection molding is a sophisticated manufacturing process primarily used for producing high-quality, complex plastic parts with tight tolerances and intricate designs.
This process involves injecting molten plastic into a precisely fabricated mold, where it cools and solidifies into the desired shape.
The technique is widely used in various industries, including automotive, medical, and electronics, due to its ability to produce components with exceptional accuracy and consistency.
The Importance of Precision in Injection Molding
Precision is critical in injection molding because even the smallest deviations can significantly affect the final product’s functionality and appearance.
Ensuring high precision involves controlling several factors throughout the process, from the design of the mold to the selection of materials and the settings of the molding machine itself.
Achieving high precision is essential for meeting stringent industry standards and delivering products that meet customer expectations.
Key Factors in Precision Injection Molding
Mold Design
The design of the mold is fundamental to achieving high-quality precision injection molding.
A well-designed mold must account for factors such as part geometry, material flow, and cooling efficiency.
Computer-aided design (CAD) software is often used to create detailed and accurate mold designs, allowing manufacturers to visualize the mold and make necessary adjustments before production begins.
Proper mold design ensures even filling of the mold cavity, minimizes defects, and reduces the need for post-processing work.
Material Selection
Choosing the right material is also crucial in precision injection molding.
The material must have the appropriate characteristics, such as flowability, shrinkage rate, and thermal stability, to ensure it behaves predictably during the molding process.
Commonly used materials include thermoplastics like ABS, polycarbonate, and nylon, each offering different properties suitable for various applications.
Manufacturers must consider the end-use of the product and environmental factors to select the most suitable material for their specific needs.
Machine Parameters
The parameters of the injection molding machine play a vital role in precision molding.
These include temperature settings, injection speed, and pressure.
Each of these parameters must be finely tuned to maintain consistent quality across runs.
For example, the injection speed affects how quickly the mold is filled and can influence the occurrence of defects such as warping or incomplete filling.
The precise control of these parameters ensures that each part is produced to the required specifications and reduces waste.
Challenges and Solutions in Precision Injection Molding
Addressing Common Defects
Despite the advanced nature of precision injection molding, there are several common defects that manufacturers may encounter, such as warping, sink marks, and short shots.
Warping occurs when there are uneven stresses in the part as it cools, leading to a distorted shape.
This can be minimized by adjusting the cooling time and ensuring uniform wall thickness in the mold design.
Sink marks are depressions on the surface of the molded part caused by material shrinkage.
Proper material selection and adjusting the holding pressure of the machine can help reduce this defect.
Short shots occur when the mold cavity is not completely filled, which can be resolved by increasing the injection pressure or speed.
Ensuring Consistency
Consistency is key in precision injection molding, especially when producing high volumes of parts.
To ensure consistent quality, manufacturers must implement stringent quality control measures, including regular machine maintenance and real-time monitoring of production parameters.
Statistical process control (SPC) techniques are often used to monitor and control the process, allowing for early detection and correction of potential issues.
Additionally, investing in skilled operators and ongoing training can greatly enhance the consistency and efficiency of the production process.
Advancements in Precision Injection Molding
Automation and AI Integration
Advancements in technology have significantly impacted precision injection molding, with automation and AI playing increasingly important roles.
Automated systems can control the entire molding process, from material handling to quality inspection, reducing the likelihood of human error and improving efficiency.
Artificial intelligence can analyze large data sets to identify patterns and optimize process parameters, leading to higher precision and reduced cycle times.
These innovations enable manufacturers to produce high-quality parts faster and at lower costs, making them more competitive in the global market.
Sustainable Practices
Sustainability is becoming a growing concern in manufacturing, and precision injection molding is no exception.
Manufacturers are exploring ways to minimize waste and reduce energy consumption without compromising quality.
Recyclable materials and bio-based polymers are being increasingly used to lower environmental impact.
Moreover, energy-efficient machinery and processes, such as heat recovery systems and advanced cooling techniques, are being implemented to enhance sustainability.
These practices not only benefit the environment but can also lead to cost savings in the long run.
Conclusion
Precision injection molding is a complex yet remarkably effective manufacturing process critical to producing high-quality plastic parts.
By focusing on key factors such as mold design, material selection, and machine parameters, manufacturers can achieve the precision necessary to meet stringent industry standards.
Addressing common challenges with innovative solutions and embracing technological advancements can further enhance the process’s efficiency and sustainability.
As the industry continues to evolve, precision injection molding will undoubtedly remain a cornerstone of modern manufacturing, delivering products that consistently meet the highest quality expectations.
資料ダウンロード
QCD調達購買管理クラウド「newji」は、調達購買部門で必要なQCD管理全てを備えた、現場特化型兼クラウド型の今世紀最高の購買管理システムとなります。
ユーザー登録
調達購買業務の効率化だけでなく、システムを導入することで、コスト削減や製品・資材のステータス可視化のほか、属人化していた購買情報の共有化による内部不正防止や統制にも役立ちます。
NEWJI DX
製造業に特化したデジタルトランスフォーメーション(DX)の実現を目指す請負開発型のコンサルティングサービスです。AI、iPaaS、および先端の技術を駆使して、製造プロセスの効率化、業務効率化、チームワーク強化、コスト削減、品質向上を実現します。このサービスは、製造業の課題を深く理解し、それに対する最適なデジタルソリューションを提供することで、企業が持続的な成長とイノベーションを達成できるようサポートします。
オンライン講座
製造業、主に購買・調達部門にお勤めの方々に向けた情報を配信しております。
新任の方やベテランの方、管理職を対象とした幅広いコンテンツをご用意しております。
お問い合わせ
コストダウンが利益に直結する術だと理解していても、なかなか前に進めることができない状況。そんな時は、newjiのコストダウン自動化機能で大きく利益貢献しよう!
(Β版非公開)