- お役立ち記事
- Tips for Maximizing the Performance of Injection Molding Machines
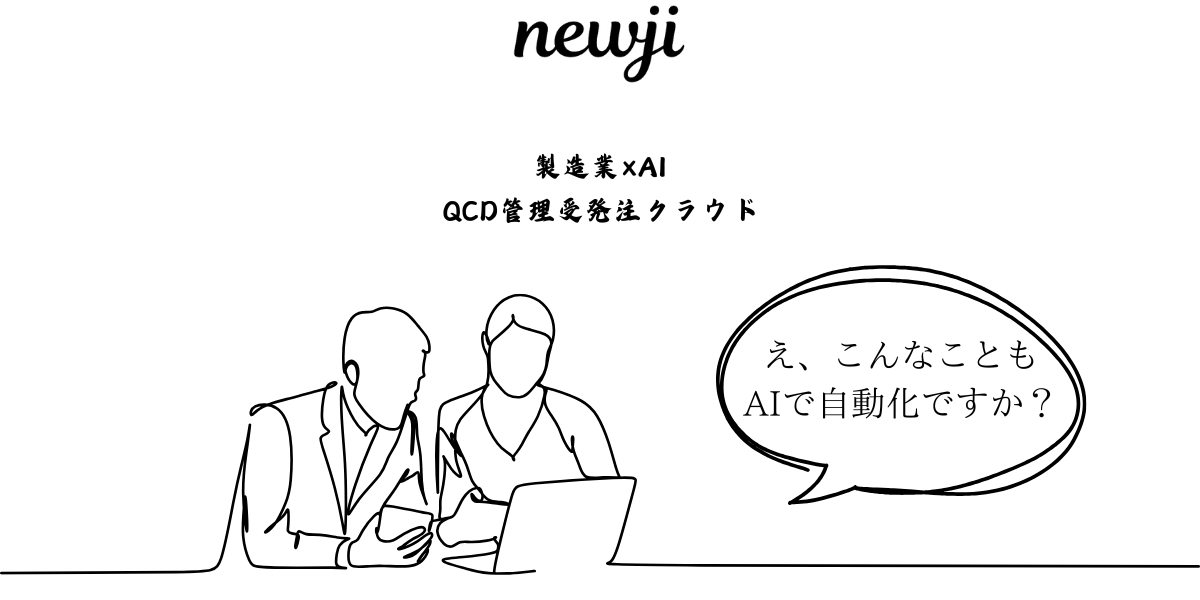
Tips for Maximizing the Performance of Injection Molding Machines
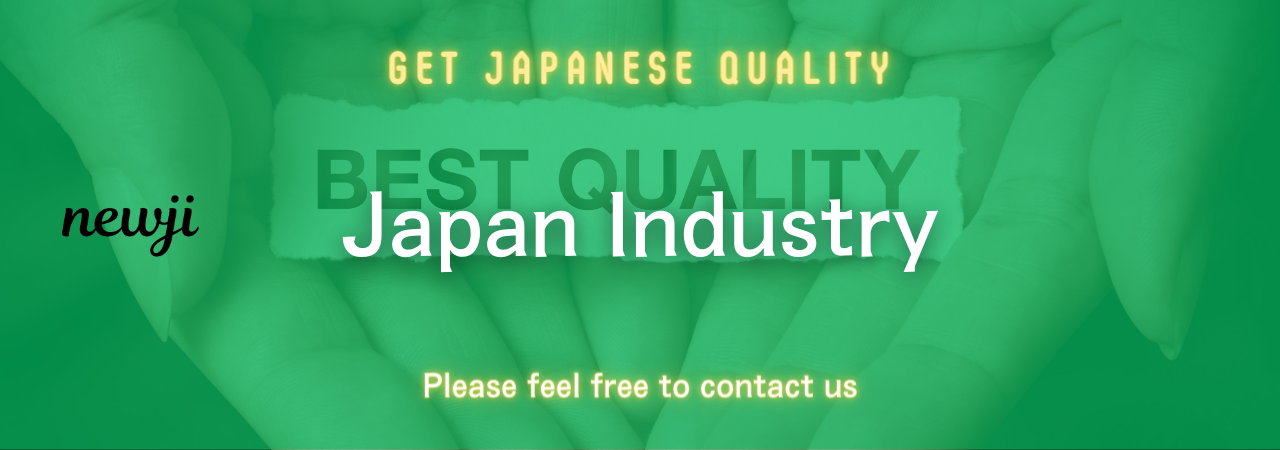
目次
Understanding Injection Molding Machines
Injection molding machines are complex pieces of equipment used to produce a wide range of plastic products.
These machines work by injecting molten plastic into a mold, where it cools and solidifies, taking the shape of the mold cavity.
Understanding how these machines function is essential for optimizing their performance.
The key components of an injection molding machine include the injection unit, the clamping unit, and the mold.
Each plays a crucial role in the molding process and contributes to the overall efficiency and quality of the finished product.
Regular Maintenance and Inspection
One of the most effective ways to maximize the performance of injection molding machines is through regular maintenance and inspection.
Routine checks help identify potential issues before they become major problems, ensuring the machine operates smoothly.
It’s essential to develop a maintenance schedule that includes cleaning, lubrication, and the examination of critical components.
Regularly inspecting parts like the screws, barrels, and molds can prevent wear and tear, reducing downtime and maintenance costs.
By keeping machines in top condition, you ensure consistent production quality and minimize the risk of unexpected breakdowns.
Proper Material Selection
Choosing the appropriate material for your injection molding process can significantly impact the performance of your machine.
Ensure you are using materials that are compatible with your machine and suitable for your specific application.
Consider factors such as the melting point, viscosity, and thermal properties of the material.
Using materials that are well-suited for your machine can prevent issues like clogging or poor part quality, thereby enhancing the machine’s performance.
Working with suppliers and experts can help you understand which materials are best for your requirements.
Optimizing Machine Parameters
To achieve the best performance, it’s crucial to optimize the machine parameters for each production run.
This involves adjusting settings such as temperature, pressure, and injection speed to suit the specific material and mold design.
Fine-tuning these parameters can lead to improved cycle times, higher product quality, and reduced waste.
Operators should be trained to understand the impact of each parameter on the overall process.
By consistently evaluating and adjusting these settings, you can ensure that the machine operates at peak performance.
Temperature Control
Proper temperature control is vital for optimal injection molding performance.
Each material has an ideal temperature range that should be maintained during the process.
Ensure that the heating and cooling systems of the machine are functioning correctly to prevent temperature fluctuations.
Consistent temperature control helps produce high-quality parts and prevents defects like warping or incomplete filling.
Injection Speed and Pressure
Injection speed and pressure settings are also critical for maximizing machine performance.
These parameters directly affect the flow of molten material into the mold and the quality of the final product.
Balancing these settings can help avoid common issues such as short shots, flash, or sink marks.
Regularly reviewing and fine-tuning these parameters based on material and product specifications can lead to more efficient production and better outcomes.
Improving Mold Design and Maintenance
The design and maintenance of the mold are equally important for the optimal performance of injection molding machines.
A well-designed mold ensures even filling and smooth ejection, reducing cycle times and improving product quality.
It’s crucial to work with experienced mold designers to create a mold that suits your production needs.
Regular mold maintenance is just as important as maintaining the machine itself.
Inspect molds for wear and damage, clean them thoroughly, and apply appropriate lubricant to moving parts.
Well-maintained molds contribute to consistent product quality and help in minimizing production hiccups.
Ensuring Skilled Personnel
Having trained and skilled personnel to operate and maintain the injection molding machines is critical for maximizing their performance.
Operators should be knowledgeable about machine parameters, process optimization, and troubleshooting techniques.
Regular training programs and workshops can keep the team updated on the latest technologies and best practices.
Skilled personnel are more likely to detect potential issues early, make informed decisions, and apply solutions efficiently.
Investing in training can improve machine efficiency and ensure high-quality production standards are met consistently.
Implementing Advanced Technologies
Embracing advanced technologies and automation can significantly enhance the performance of injection molding machines.
Consider integrating software systems for monitoring and data analysis, which can provide insights into machine performance and areas for improvement.
Automation solutions, such as robotic arms for part removal or assembly, can improve cycle times and reduce labor costs.
Technologies like IoT (Internet of Things) can offer real-time machine monitoring, predictive maintenance, and improved operational efficiency.
Staying updated with technological advancements allows for a more streamlined production process and a competitive edge in the market.
Conclusion
Maximizing the performance of injection molding machines involves a combination of proper maintenance, material selection, parameter optimization, mold care, skilled personnel, and advanced technologies.
By focusing on each of these areas, businesses can ensure that their injection molding machines operate efficiently and produce high-quality products consistently.
Continual learning and adaptation to new practices are crucial for maintaining peak performance and staying competitive in the industry.
資料ダウンロード
QCD調達購買管理クラウド「newji」は、調達購買部門で必要なQCD管理全てを備えた、現場特化型兼クラウド型の今世紀最高の購買管理システムとなります。
ユーザー登録
調達購買業務の効率化だけでなく、システムを導入することで、コスト削減や製品・資材のステータス可視化のほか、属人化していた購買情報の共有化による内部不正防止や統制にも役立ちます。
NEWJI DX
製造業に特化したデジタルトランスフォーメーション(DX)の実現を目指す請負開発型のコンサルティングサービスです。AI、iPaaS、および先端の技術を駆使して、製造プロセスの効率化、業務効率化、チームワーク強化、コスト削減、品質向上を実現します。このサービスは、製造業の課題を深く理解し、それに対する最適なデジタルソリューションを提供することで、企業が持続的な成長とイノベーションを達成できるようサポートします。
オンライン講座
製造業、主に購買・調達部門にお勤めの方々に向けた情報を配信しております。
新任の方やベテランの方、管理職を対象とした幅広いコンテンツをご用意しております。
お問い合わせ
コストダウンが利益に直結する術だと理解していても、なかなか前に進めることができない状況。そんな時は、newjiのコストダウン自動化機能で大きく利益貢献しよう!
(Β版非公開)