- お役立ち記事
- 製造業の現場担当者向け!QC7つ道具を活用した品質問題の原因究明方法
月間77,185名の
製造業ご担当者様が閲覧しています*
*2025年2月28日現在のGoogle Analyticsのデータより
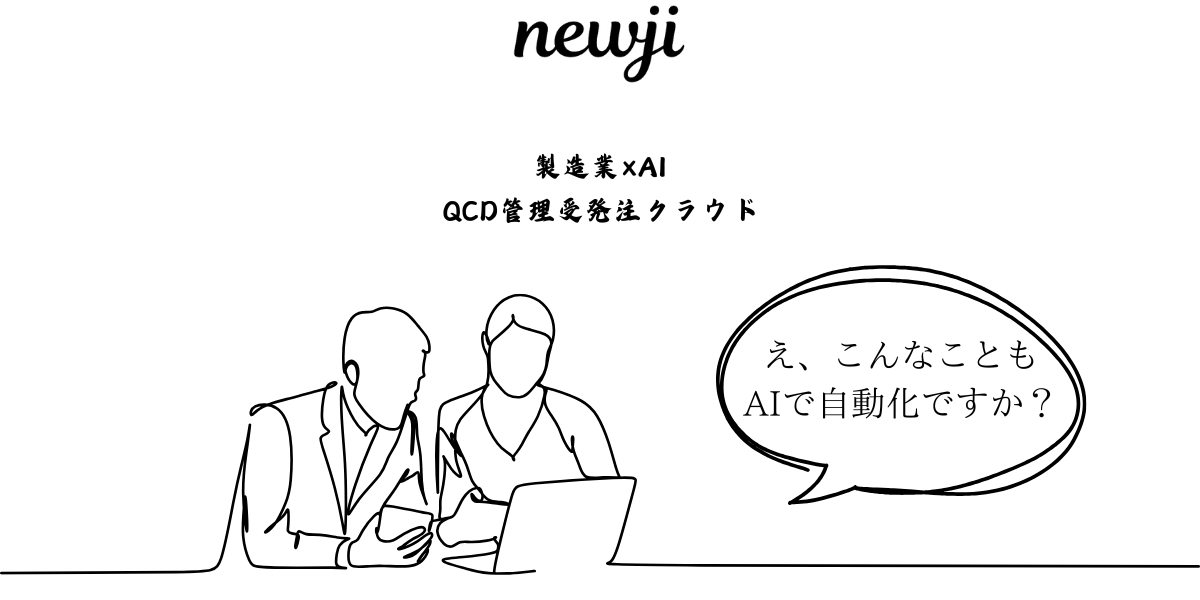
製造業の現場担当者向け!QC7つ道具を活用した品質問題の原因究明方法
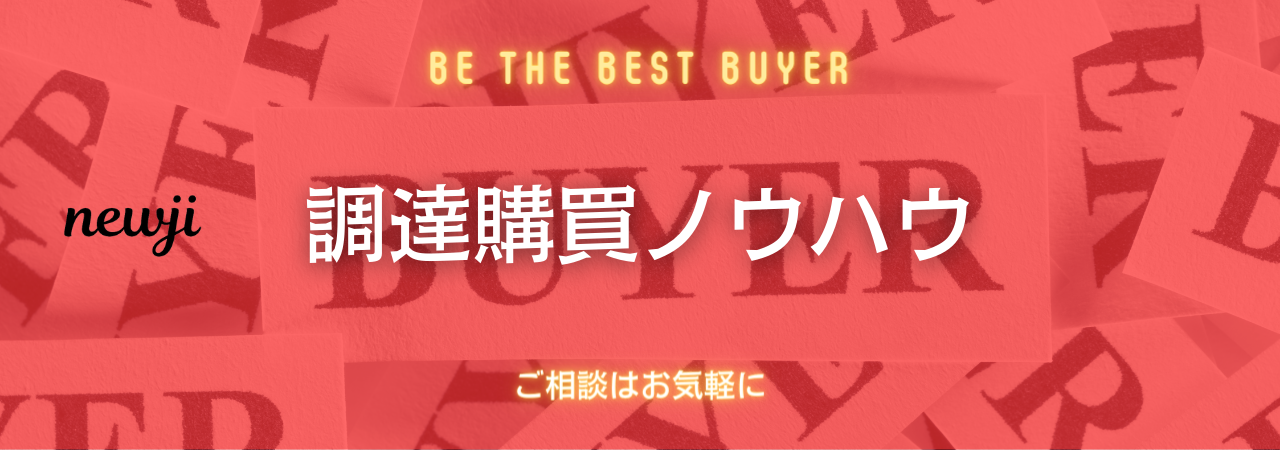
目次
QC7つ道具とは?
製造業における品質管理は、製品の信頼性と顧客満足を確保するための重要なプロセスです。
ここで紹介するQC7つ道具は、品質管理に役立つツール群であり、問題の原因を究明し、解決策を見出すための効果的な手法です。
では具体的に、QC7つ道具がどのようにして品質問題の原因究明に活かされるのかを見ていきましょう。
QC7つ道具には、以下のツールが含まれます。
1. パレート図
2. 特性要因図(魚の骨図)
3. 管理図
4. チェックシート
5. ヒストグラム
6. 散布図
7. 層別
これらのツールを理解し、適切に活用することで、品質問題を効果的に解決することが可能になります。
パレート図の活用法
パレート図は、問題の原因となる要素を視覚的に表現し、どの要因が最も大きな影響を与えているのかを特定するためのツールです。
80/20の法則として知られる、問題の80%は20%の要因によって引き起こされるという原則を基にしています。
パレート図の作成方法は以下の通りです。
– 問題に関連する要因を列挙します。
– それぞれの要因によって引き起こされる問題の影響度を定量化します。
– 影響度の高い順に要因を並べ替え、棒グラフで視覚化します。
これにより、優先的に対処すべき問題要因を明確化することができます。
例えば、製品不良の原因を分析する際、特定の部品や工程が最も多くの不良を引き起こしていることをパレート図で示すことができます。
特性要因図(魚の骨図)の活用法
特性要因図は、問題の原因を体系的に洗い出し、それらをグループ化して視覚的に表現するためのツールです。
魚の骨図とも呼ばれるこの図の特徴は、主要な要因を魚の骨のように矢状に並べ、それに付随する詳細な原因を列挙することで、全体像を理解しやすくする点です。
特性要因図を活用するステップは以下の通りです。
– 中心となる問題(特性)を図の右端に書きます。
– 問題に関連する主要な要因を骨格として矢を引きます(例:人、方法、材料、機械、環境、測定)。
– 各主要要因に付随する詳細な原因を矢に沿って書き出します。
この図を用いることで、原因とその関係性を一目で把握し、包括的な原因究明をサポートできます。
特に、根本的な原因を探る際に有効です。
管理図の導入方法
管理図は、製造プロセスの安定性を監視し、異常を早期に発見するためのツールです。
品質管理において、製品の特性が一定範囲内に維持されているかを確認することで、プロセスのばらつきを抑制し、品質を向上させる手助けをします。
管理図は以下の手順で作成します。
– 製品特性やプロセスパラメータのデータを時系列で収集します。
– データの平均値と標準偏差を計算し、正常範囲(上限管理線・下限管理線)を設定します。
– データを順番にプロットし、異常値がないか確認します。
この管理図を活用することで、異常や偏りが発生した際の即時対応が可能になり、安定した製造プロセスを保つことができます。
チェックシートの効果的な使用方法
チェックシートは、データを収集し、特定の事象の発生頻度や傾向を把握するためのシンプルで効果的なツールです。
作業員が簡単に使用できるチェックリスト形式であるため、日常的な運用に適しています。
チェックシートの作成方法は次のとおりです。
– 特定の問題やプロセスに対するチェック項目を決定します。
– データを記録するレイアウトを設定し、作業者に配布します。
– 作業者が日々の業務の中でデータを記録します。
チェックシートを継続的に使用することで、問題の発生傾向を見つけ出し、適切な改善策を講じることが可能になります。
ヒストグラムの活用と読み解き方
ヒストグラムは、収集したデータを視覚的に表現する方法で、データの分布を理解するのに役立ちます。
特定の品質特性がどのような範囲に分布しているのか、ばらつきや偏りを識別することができます。
ヒストグラムを作成するには以下の手順を踏みます。
– 収集したデータを範囲に応じてグループ化します。
– 横軸にデータの範囲、縦軸に頻度を設定し、棒グラフとしてプロットします。
このヒストグラムを使ってデータ分布を解析することで、製造工程のばらつきや異常を効果的に特定し、品質改善の方向性を見出すことが可能です。
散布図の分析による傾向把握
散布図は、二つの変数間の関係を視覚的に示すためのツールで、因果関係や相関関係の把握に効果的です。
例えば、温度と製品寸法の間に関係がある場合、散布図はその傾向を明らかにします。
散布図を作成する手順は次のとおりです。
– 二つの変数のデータをそれぞれ軸(縦軸と横軸)にプロットします。
– データ点がどのように分布するかを視覚的に解析します。
データ点の分布パターンに基づいて、例えば、片方の変数が増加するともう片方も増加(正の相関)するのか、あるいは減少(負の相関)するのかを明確にすることができます。
層別の重要性と実施法
層別は、収集したデータを特定のカテゴリーやグループに分けて分析する手法で、背後に隠れた変動要因を明らかにするために重要です。
例えば、同じ製品の異なるロット間でのバラツキを検討する場合、層別は非常に有効です。
層別を行う方法は次のようになります。
– データを特定の基準(例:時間、場所、製品の種類、担当者)に基づいてカテゴリに分けます。
– 各カテゴリ内でのデータを分析し、グループ間の違いを明らかにします。
この分析により、ばらつきの根本にある要因を特定し、適切な改善策を導入することが可能となります。
QC7つ道具の総合的な活用による品質改善
これまで紹介したQC7つ道具を組み合わせることで、より総合的な品質改善活動が可能になります。
一つのツールだけに頼るのではなく、それぞれのツールの特性を活かして連携させることが重要です。
例えば、まずはパレート図を使って最も顕著な問題を洗い出し、次に特性要因図で詳細な原因を探ります。
その後、管理図でプロセスの安定性を監視し、チェックシートで日常的にデータを集めます。
ヒストグラムや散布図でさらにデータの分布や因果関係を分析し、層別で具体的な改善策を立てる、といった流れが考えられます。
これらのツールは、現場における品質問題に対する包括的なアプローチを提供し、継続的な品質改善をサポートする重要な役割を果たします。
質の高い製品を安定して提供するためには、こうしたツールの効果的な活用と改善プロセスの継続的な見直しが不可欠です。
現場の担当者も、QC7つ道具を日常の業務に取り入れることで、より質の高い品質管理を目指すことができます。
資料ダウンロード
QCD管理受発注クラウド「newji」は、受発注部門で必要なQCD管理全てを備えた、現場特化型兼クラウド型の今世紀最高の受発注管理システムとなります。
ユーザー登録
受発注業務の効率化だけでなく、システムを導入することで、コスト削減や製品・資材のステータス可視化のほか、属人化していた受発注情報の共有化による内部不正防止や統制にも役立ちます。
NEWJI DX
製造業に特化したデジタルトランスフォーメーション(DX)の実現を目指す請負開発型のコンサルティングサービスです。AI、iPaaS、および先端の技術を駆使して、製造プロセスの効率化、業務効率化、チームワーク強化、コスト削減、品質向上を実現します。このサービスは、製造業の課題を深く理解し、それに対する最適なデジタルソリューションを提供することで、企業が持続的な成長とイノベーションを達成できるようサポートします。
製造業ニュース解説
製造業、主に購買・調達部門にお勤めの方々に向けた情報を配信しております。
新任の方やベテランの方、管理職を対象とした幅広いコンテンツをご用意しております。
お問い合わせ
コストダウンが利益に直結する術だと理解していても、なかなか前に進めることができない状況。そんな時は、newjiのコストダウン自動化機能で大きく利益貢献しよう!
(β版非公開)