- お役立ち記事
- Product development and understanding of customer needs using QFD that mid-level employees in the design department should know
Product development and understanding of customer needs using QFD that mid-level employees in the design department should know
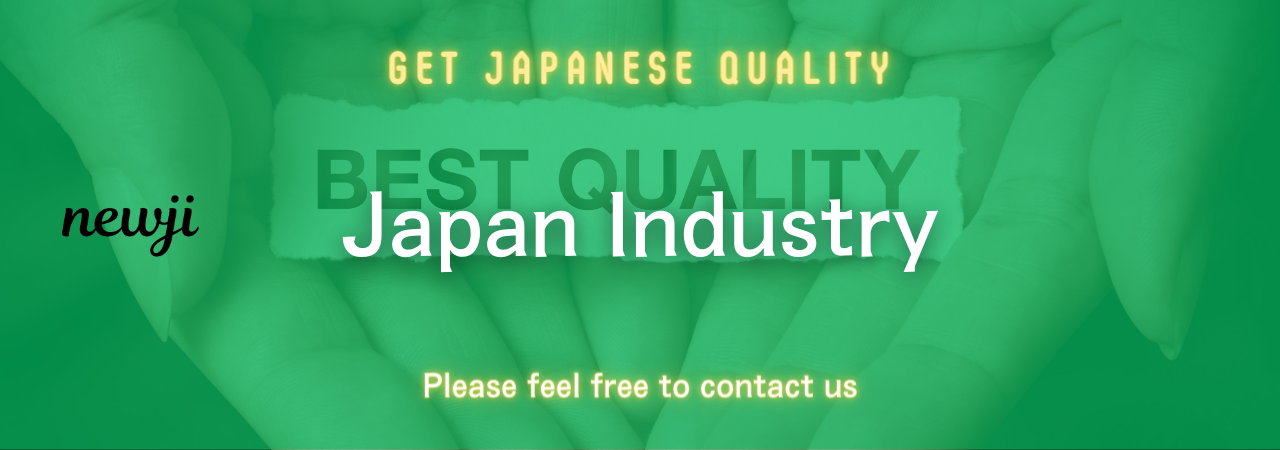
目次
Introduction to Quality Function Deployment (QFD)
Quality Function Deployment, or QFD, is a strategic method used in product development to ensure that the voice of the customer is thoroughly considered and integrated into the design and manufacturing processes.
This methodology helps bridge the gap between what customers want and what companies produce.
For mid-level employees in the design department, understanding QFD is crucial to effectively translate customer needs into specific product features.
The Importance of QFD in Product Development
QFD is not just a tool; it is a philosophy that centralizes the customer in product development.
Its primary goal is to listen, analyze, and respond to customer requirements, ensuring that the final product meets or exceeds their expectations.
By adopting QFD, mid-level design employees can prioritize features that genuinely matter to customers, leading to higher satisfaction and fewer post-launch modifications.
How QFD Enhances Customer Understanding
When it comes to understanding customer needs, QFD provides a structured approach.
It starts with gathering data directly from customers through surveys, interviews, and focus groups.
This input is then translated into a technical framework that the design team can work with.
The structured process ensures that nothing is lost in translation, which often happens when customer needs are manually deciphered.
Breaking Down the House of Quality
The cornerstone of QFD is the “House of Quality,” a matrix used to map out customer requirements against product features.
It serves as a visual representation and a communication tool for multifunctional teams to collaborate effectively.
– **Customer Requirements**: These are the “whats” – what the customer wants or expects from the product.
– **Product Specifications**: These are the “hows” – how the product will meet these customer requirements.
– **Prioritization**: Weights can be added to each requirement to signify their importance to the customer.
– **Relationship Matrix**: This part shows the correlation between customer demands and product capabilities.
Understanding how to construct and interpret the House of Quality is vital for mid-level employees, as it guides decision-making and resource allocation throughout the design phase.
Implementing QFD in Design Departments
For optimal implementation, QFD should become part of the department’s culture.
Employees at all levels, especially mid-level design employees, should be trained in QFD principles and techniques.
This involves:
Training and Development
Regular workshops and training sessions should be conducted to familiarize the team with QFD’s nuances.
This education should cover both theoretical and practical aspects, providing employees with case studies and hands-on projects to solidify their understanding.
Collaborative Cross-Functional Teams
QFD thrives on collaboration across various departments, such as marketing, engineering, and production.
Incorporating diverse perspectives ensures a comprehensive understanding of customer needs and how they can be technically achieved.
Encouraging mid-level employees to actively participate in interdisciplinary teams fosters communication and innovation.
Continuous Feedback Loop
Implementing a feedback loop is essential for refining QFD processes.
Customer feedback should be continuously sought and integrated back into the product development cycle.
Mid-level employees should be proactive in collecting and analyzing this feedback to influence ongoing and future projects.
Challenges and Solutions in Adopting QFD
While QFD provides significant advantages, it does come with challenges, especially during the initial adoption phase.
Understanding these challenges can help mid-level employees prepare and adapt.
Resistance to Change
One common challenge is resistance from team members who are accustomed to traditional methods.
To overcome this, it is crucial to communicate the benefits of QFD clearly and demonstrate its impact through pilot projects that achieve noticeable improvements.
Complexity of the QFD Process
The detailed and structured nature of QFD can be overwhelming.
Breaking the process into smaller, manageable phases can help design teams integrate QFD without feeling burdened.
Data Collection and Interpretation
Gathering accurate and useful customer data can be difficult.
Mid-level design employees should work closely with marketing and customer relations teams to ensure data is both comprehensive and relevant.
Conclusion
Quality Function Deployment is a powerful method for aligning product features with customer needs.
For mid-level employees in the design department, mastering QFD can significantly enhance their ability to contribute to successful product development.
By emphasizing customer needs, encouraging cross-functional collaboration, and addressing challenges thoughtfully, design teams can leverage QFD to deliver products that delight customers and meet business goals.
資料ダウンロード
QCD調達購買管理クラウド「newji」は、調達購買部門で必要なQCD管理全てを備えた、現場特化型兼クラウド型の今世紀最高の購買管理システムとなります。
ユーザー登録
調達購買業務の効率化だけでなく、システムを導入することで、コスト削減や製品・資材のステータス可視化のほか、属人化していた購買情報の共有化による内部不正防止や統制にも役立ちます。
NEWJI DX
製造業に特化したデジタルトランスフォーメーション(DX)の実現を目指す請負開発型のコンサルティングサービスです。AI、iPaaS、および先端の技術を駆使して、製造プロセスの効率化、業務効率化、チームワーク強化、コスト削減、品質向上を実現します。このサービスは、製造業の課題を深く理解し、それに対する最適なデジタルソリューションを提供することで、企業が持続的な成長とイノベーションを達成できるようサポートします。
オンライン講座
製造業、主に購買・調達部門にお勤めの方々に向けた情報を配信しております。
新任の方やベテランの方、管理職を対象とした幅広いコンテンツをご用意しております。
お問い合わせ
コストダウンが利益に直結する術だと理解していても、なかなか前に進めることができない状況。そんな時は、newjiのコストダウン自動化機能で大きく利益貢献しよう!
(Β版非公開)