- お役立ち記事
- Techniques for improving wear characteristics through surface hardening that operators in the precision machinery industry should know
Techniques for improving wear characteristics through surface hardening that operators in the precision machinery industry should know
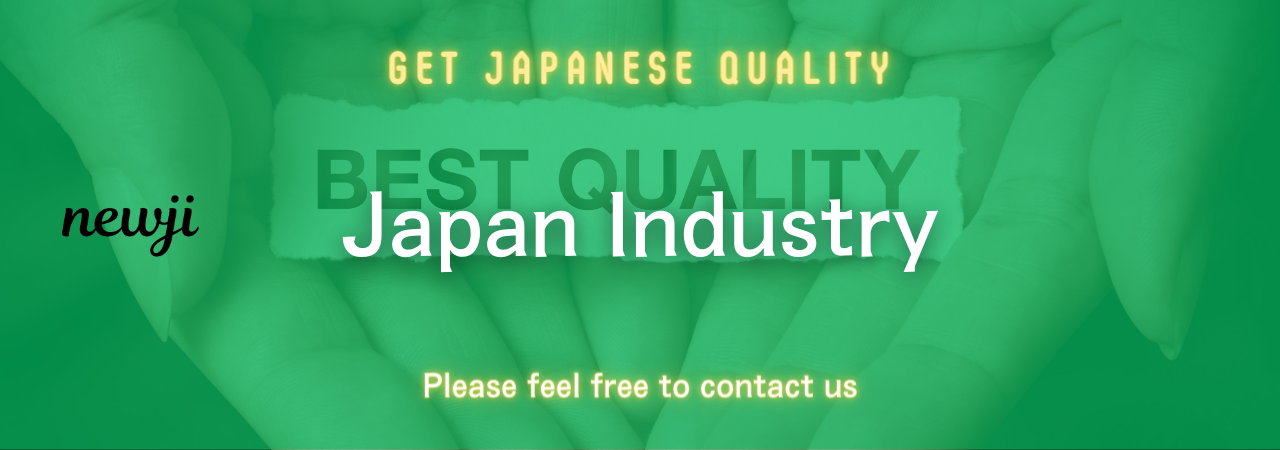
目次
Introduction to Surface Hardening
Surface hardening is a pivotal process in the precision machinery industry, tailored to enhance the durability and lifespan of components.
This technique focuses on improving the wear characteristics of machine parts, thereby bolstering their performance under strenuous conditions.
The surface of the material is hardened while the core remains soft, providing a balance between toughness and surface resilience.
Operators in the industry need to have a comprehensive understanding of these techniques to ensure optimal functionality and longevity of machinery components.
Importance of Surface Hardening
In the precision machinery industry, wear resistance is a critical factor.
Components are subjected to various stresses, such as friction, impact, and pressure, all of which can lead to wear and tear.
Surface hardening methods aim to reduce these effects, extending the service life of parts and ultimately saving time and resources.
Improved wear characteristics minimize the need for frequent replacements and repairs, enhancing operational efficiency.
This not only results in cost savings but also ensures that machines run smoothly without unexpected downtimes.
Common Surface Hardening Techniques
There are several surface hardening techniques, each with its unique benefits and applications.
Understanding these methods allows operators to select the most appropriate one for their specific needs.
Case Hardening
Case hardening, also known as carburizing, is one of the most prevalent surface hardening techniques.
It involves infusing carbon into the surface layer of low-carbon steel at a high temperature, followed by a rapid cooling process.
This method creates a hard, wear-resistant surface while maintaining a tough interior.
Case hardening is ideal for components that require a sturdy exterior to withstand wear but also need a certain level of internal toughness to handle bending or impact forces.
Nitriding
Nitriding is a heat treatment process that introduces nitrogen into the surface of steel.
This forms nitrogen-rich compounds that significantly enhance the material’s hardness.
Unlike carburizing, nitriding does not require quenching, which means it produces less distortion and is suitable for complex parts with tight tolerances.
It is often used for gears, crankshafts, and other components that require excellent wear resistance at elevated temperatures.
Induction Hardening
Induction hardening involves heating the surface of a metal component using induction coils followed by rapid cooling.
This method is highly controllable, offering precise control over the depth of hardening.
Induction hardening is particularly advantageous for large components or those with intricate designs, as it allows for specific areas to be hardened while leaving other sections unaffected.
This technique is widely applied in the automotive and aerospace industries.
Flame Hardening
Flame hardening utilizes an oxy-fuel flame to heat the surface of the metal, which is then quenched.
This method is used for parts where selective hardening is required and is particularly effective for large gears and heavy-duty machine components.
While not as precise as induction hardening, flame hardening is a cost-effective alternative for large-scale applications.
Factors Influencing Surface Hardening
Several factors influence the effectiveness of surface hardening, and operators must consider them to optimize the process.
Material Composition
The composition of the material significantly affects its response to surface hardening.
Low-carbon steels are often preferred for carburizing, while alloy steels with elements like chromium are better suited for nitriding due to their ability to form stable nitride compounds.
Operators need to select the material that aligns best with the desired outcome of the hardening process.
Hardening Depth
The desired depth of hardness is crucial for ensuring the part can withstand the required loads and stresses.
Too little depth might not provide sufficient wear resistance, while excessive depth could lead to brittleness.
Precise measurement and control at this stage are vital to achieving the desired balance between surface hardness and core ductility.
Cooling Rate
The rate at which the material is cooled after heating is critical in determining the final hardness and microstructure.
For instance, rapid cooling, as seen in quenching, can result in a harder surface but may introduce internal stresses or distortion.
Operators must carefully control the cooling rate to avoid these undesirable effects and ensure uniform hardness.
Benefits of Surface Hardening in the Industry
Surface hardening offers numerous benefits that make it indispensable in the precision machinery industry.
Enhanced Wear Resistance
The primary advantage of surface hardening is the substantial increase in wear resistance.
Hardened surfaces are more capable of resisting abrasion and surface fatigue, which are common in high-stress environments.
This leads to longer-lasting parts and fewer maintenance requirements.
Improved Load Capacity
By improving the surface hardness, the part’s load-carrying capacity is increased.
This is especially beneficial for components subject to high loads and stress conditions, such as shafts and bearings, ensuring they perform reliably without frequent replacements.
Cost Efficiency
While the initial investment in surface hardening processes might be significant, the long-term cost savings due to reduced downtime, maintenance, and replacement are substantial.
This efficiency translates to better resource allocation and improved productivity in manufacturing operations.
Customization and Precision
Modern surface hardening techniques allow for a high degree of customization.
Operators can precisely target specific areas for hardening, tailoring the process to meet the exact specifications required for different applications.
This precision enhances the overall quality and performance of machinery parts.
Conclusion
Understanding and implementing surface hardening techniques is essential for operators in the precision machinery industry.
By leveraging these techniques, they can significantly improve the wear characteristics of components, ensuring durability and reliability.
Whether through case hardening, nitriding, induction, or flame hardening, each method offers unique benefits that can be strategically employed for optimal results.
Careful consideration of factors like material composition and hardening depth, along with a focus on the specific demands of the application, will ensure that machinery operates at peak performance with minimal interruptions.
資料ダウンロード
QCD調達購買管理クラウド「newji」は、調達購買部門で必要なQCD管理全てを備えた、現場特化型兼クラウド型の今世紀最高の購買管理システムとなります。
ユーザー登録
調達購買業務の効率化だけでなく、システムを導入することで、コスト削減や製品・資材のステータス可視化のほか、属人化していた購買情報の共有化による内部不正防止や統制にも役立ちます。
NEWJI DX
製造業に特化したデジタルトランスフォーメーション(DX)の実現を目指す請負開発型のコンサルティングサービスです。AI、iPaaS、および先端の技術を駆使して、製造プロセスの効率化、業務効率化、チームワーク強化、コスト削減、品質向上を実現します。このサービスは、製造業の課題を深く理解し、それに対する最適なデジタルソリューションを提供することで、企業が持続的な成長とイノベーションを達成できるようサポートします。
オンライン講座
製造業、主に購買・調達部門にお勤めの方々に向けた情報を配信しております。
新任の方やベテランの方、管理職を対象とした幅広いコンテンツをご用意しております。
お問い合わせ
コストダウンが利益に直結する術だと理解していても、なかなか前に進めることができない状況。そんな時は、newjiのコストダウン自動化機能で大きく利益貢献しよう!
(Β版非公開)