- お役立ち記事
- A must-see for quality managers in the screw pump impeller manufacturing industry! Design technology that achieves both high efficiency and wear resistance
A must-see for quality managers in the screw pump impeller manufacturing industry! Design technology that achieves both high efficiency and wear resistance
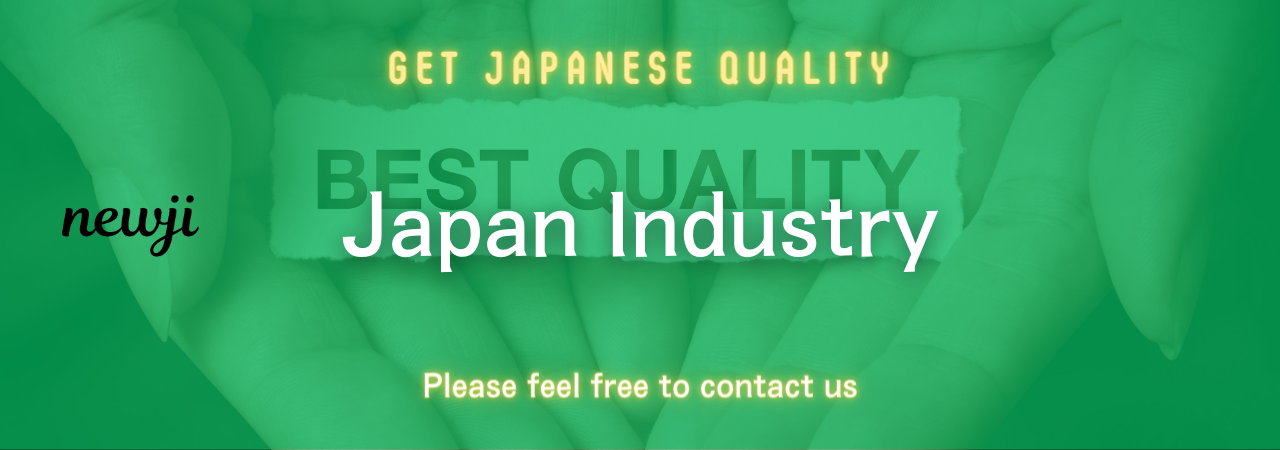
目次
Introduction to Screw Pump Impellers
Screw pump impellers play a crucial role in various industries, especially those dealing with liquids and viscous materials.
They are integral components that ensure the efficient movement of fluids.
The design and manufacturing of these impellers require precision and expertise to meet both performance and durability standards.
Screw pumps utilize a helical screw mechanism to move fluids.
The impeller within these pumps is responsible for the smooth transfer of liquid, which is essential in minimizing energy consumption and maximizing output.
Quality managers in the screw pump impeller manufacturing industry have the task of ensuring these components meet stringent efficiency and wear resistance criteria.
The Need for High Efficiency
In the competitive landscape of industrial manufacturing, efficiency is paramount.
High efficiency in screw pump impellers translates to energy savings and cost-effectiveness for end-users.
An efficient impeller reduces energy consumption while maintaining optimal performance levels over extended periods.
Efficiency can be achieved through a combination of advanced design techniques and the use of high-quality materials.
Designers must consider the fluid dynamics involved and optimize the impeller’s geometry to facilitate smooth fluid flow.
Additionally, the impeller’s surface finish should minimize friction and turbulence, further enhancing its efficiency.
Design Optimization Techniques
There are several design strategies employed to optimize the efficiency of screw pump impellers.
Computational Fluid Dynamics (CFD) simulations are extensively used to model fluid flow and identify any potential issues in the impeller design.
These simulations help in visualizing how the impeller interacts with the fluid, allowing designers to make informed adjustments to enhance performance.
Furthermore, the use of advanced manufacturing processes such as precision casting or 3D printing can result in impellers with complex geometries that traditional methods might not achieve.
These processes allow for the creation of highly efficient designs, tailored to specific industrial requirements.
Ensuring Wear Resistance
While efficiency is critical, screw pump impellers must also withstand harsh operational conditions.
Wear resistance ensures the longevity and reliability of the impeller, reducing maintenance costs and downtime.
To enhance wear resistance, material selection plays a vital role.
The use of high-quality, wear-resistant alloys or composite materials can provide the necessary durability.
Materials like stainless steel or coated alloys are commonly used for their resistance to corrosion and abrasion.
Surface Treatment Techniques
Beyond material choice, surface treatment techniques further improve wear resistance.
Techniques such as hardening, coating, or chemical treatments can significantly extend the life of an impeller.
Hard coatings, for example, can be applied to the impeller’s surface to increase its resistance to abrasive wear.
These coatings come in various forms, including ceramic coatings or diamond-like carbon (DLC) coatings, known for their durability.
Chemical treatments like nitriding can also enhance surface hardness, making the impeller less susceptible to wear.
These treatments create a hardened outer layer while maintaining the core’s toughness, balancing both wear resistance and structural integrity.
Balancing Efficiency and Wear Resistance
Achieving a balance between high efficiency and wear resistance requires a holistic approach to design and manufacturing.
It’s not enough to focus solely on one aspect; both need to be considered to produce a quality impeller.
Quality control processes must be stringent, with regular testing and analysis to ensure that the impellers meet industry standards.
This includes conducting performance tests to validate efficiency and wear tests to assess durability.
Collaboration between design engineers and material scientists can lead to innovative solutions that fulfill these dual requirements.
By working together, they can develop new materials and technologies that push the boundaries of what’s possible in impeller design.
The Role of Quality Managers
Quality managers in the screw pump impeller manufacturing industry have a crucial role to play in ensuring these components live up to their potential.
They oversee the manufacturing processes, implement strict quality control measures, and work closely with engineers to address any design or performance issues.
They are also responsible for ensuring the impellers comply with industry regulations and standards, which often involve rigorous testing and documentation.
Constant monitoring and assessment of the production line ensure that any deviations from the desired quality are swiftly corrected.
Furthermore, quality managers must stay abreast of the latest technologies and materials that can enhance the efficiency and wear resistance of screw pump impellers.
By investing in research and development, they can introduce new innovations that offer a competitive edge in the market.
Conclusion
In conclusion, the design and manufacturing of screw pump impellers demand a delicate balance between high efficiency and wear resistance.
Quality managers play a pivotal role in ensuring that these components meet both criteria while also maintaining their reliability and performance in the field.
Through the application of advanced design techniques, material selection, and surface treatments, quality managers can guide their teams to produce impellers that serve their intended function efficiently and durably.
By embracing innovation and maintaining strict quality control, the screw pump impeller industry can continue to evolve, meeting the demands of diverse industrial applications.
資料ダウンロード
QCD調達購買管理クラウド「newji」は、調達購買部門で必要なQCD管理全てを備えた、現場特化型兼クラウド型の今世紀最高の購買管理システムとなります。
ユーザー登録
調達購買業務の効率化だけでなく、システムを導入することで、コスト削減や製品・資材のステータス可視化のほか、属人化していた購買情報の共有化による内部不正防止や統制にも役立ちます。
NEWJI DX
製造業に特化したデジタルトランスフォーメーション(DX)の実現を目指す請負開発型のコンサルティングサービスです。AI、iPaaS、および先端の技術を駆使して、製造プロセスの効率化、業務効率化、チームワーク強化、コスト削減、品質向上を実現します。このサービスは、製造業の課題を深く理解し、それに対する最適なデジタルソリューションを提供することで、企業が持続的な成長とイノベーションを達成できるようサポートします。
オンライン講座
製造業、主に購買・調達部門にお勤めの方々に向けた情報を配信しております。
新任の方やベテランの方、管理職を対象とした幅広いコンテンツをご用意しております。
お問い合わせ
コストダウンが利益に直結する術だと理解していても、なかなか前に進めることができない状況。そんな時は、newjiのコストダウン自動化機能で大きく利益貢献しよう!
(Β版非公開)