- お役立ち記事
- Introduction of poka-yoke techniques and error prevention measures that new leaders of equipment maintenance departments in chemical manufacturing industries should keep in mind
Introduction of poka-yoke techniques and error prevention measures that new leaders of equipment maintenance departments in chemical manufacturing industries should keep in mind
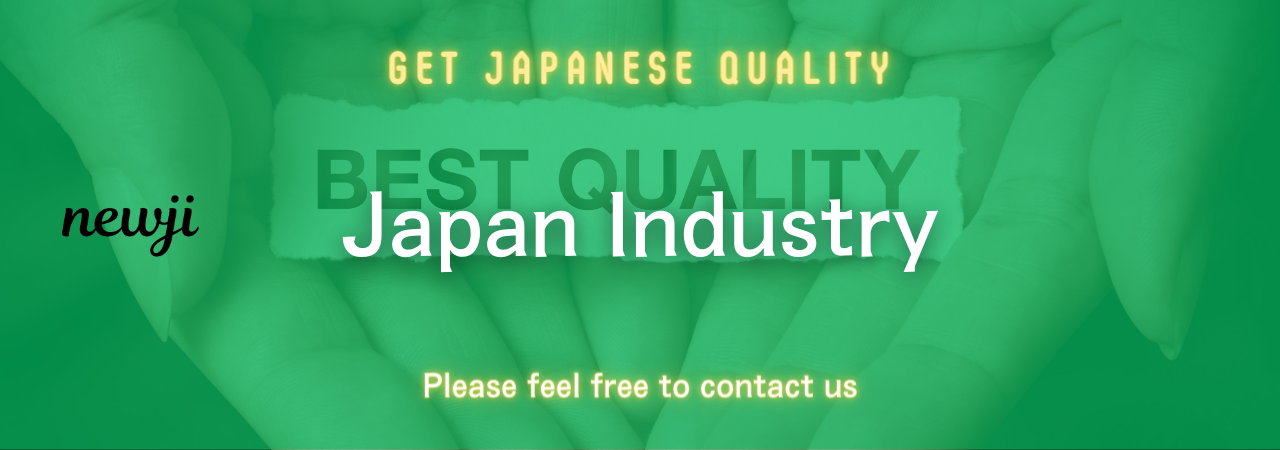
目次
Understanding Poka-Yoke
Poka-yoke is a Japanese term that stands for “mistake-proofing” or “inadvertent error prevention.”
In the world of manufacturing and maintenance, it refers to any method or device that prevents errors before they happen.
The goal is to develop processes that make it impossible for workers and machinery to make mistakes, thereby improving quality and efficiency.
Especially in chemical manufacturing, where errors can have potentially hazardous consequences, understanding and implementing poka-yoke is critical.
For new leaders in equipment maintenance departments, recognizing the importance of mistake-proofing systems can help ensure safe and reliable operations.
The Significance of Poka-Yoke in Chemical Manufacturing
In the chemical industry, precision is crucial to ensure safety and maintain product quality.
Even the smallest error can lead to serious safety hazards, financial loss, or environmental harm. This is why error prevention is so crucial.
Device malfunctions, incorrect settings, or human error can result in unintended chemical reactions or leaks, endangering both workers and the environment.
Implementing poka-yoke techniques reduces these risks by creating robust systems that reduce the likelihood of human error and equipment failure.
Poka-Yoke Techniques for Error Prevention
1. Visual Cues and Reminders
One of the most effective ways to prevent errors is by using visual cues.
These can include color-coded labels, indicators, or signs that provide clear instructions to workers.
For example, using different colors for machine controls can help operators quickly and easily identify the right button or lever.
2. Sensory Feedback Mechanisms
A sensory feedback mechanism provides immediate information to operators when something is amiss.
This can be in the form of sound or light alerts when a machine is not functioning correctly or if parameters go outside of specified limits.
Such systems can alert operators before a minor issue escalates into a larger problem.
3. Standardization of Processes
Creating and adhering to standardized procedures ensures consistency and predictability in operations.
This includes clear documentation of maintenance tasks, operating procedures, and safety protocols that all employees can easily follow.
Consistent procedures minimize the chance of errors by making sure everyone on the team has the same understanding of what needs to be done.
4. Fool-Proofing Devices
Fool-proofing involves designing equipment so that it is not possible to assemble or operate it incorrectly.
This might include unique shapes for parts that only fit in the correct direction or using tools that only work with specific equipment parts.
By designing equipment so that errors cannot occur, you reduce the need for extensive training or retraining.
Implementing Poka-Yoke as a Maintenance Leader
Assess Current Systems
As a new leader, start by assessing the current systems in place at your facility.
Look for areas where errors are most likely to occur, whether they result from human factors, equipment design, or workflow issues.
Engage with Your Team
Engage with your maintenance team to gain insights and feedback on where they see problems occurring.
They can provide valuable input based on their hands-on experience and knowledge of the machinery.
Encourage open communication about mistakes and near-misses so you can address potential problems before they occur.
Training and Education
Ensure that all team members are properly trained on the importance of poka-yoke and understand how to implement these techniques in their daily tasks.
Training should include understanding machine operations, safety protocols, and the importance of following standardized procedures.
Regular refreshers can help maintain knowledge and awareness among employees.
Measure and Adapt
After implementing poka-yoke techniques, monitor the performance of your systems to identify any further areas for improvement.
Collect data on errors that occurred, even after interventions, and determine the root cause of any issues.
Use this information to make informed adjustments to your systems and processes.
Long-Term Benefits of Poka-Yoke
Incorporating poka-yoke methods into your maintenance protocols can deliver myriad benefits.
Your operations will be safer, more reliable, and more cost-effective.
By preventing errors, you reduce downtime due to equipment failures, increase the lifecycle of machinery, and decrease waste.
Moreover, enhancing the safety and reliability of processes makes the workplace less hazardous, improves morale and boosts confidence among team members.
An operation that employs poka-yoke effectively not only preserves the integrity of the process but also enhances reputation and compliance with safety standards.
Conclusion
For new leaders in chemical manufacturing’s maintenance departments, the adoption of poka-yoke techniques is invaluable.
Mistake-proofing through these methods not only safeguards workplace safety but also drives efficiency and reliability.
By systematically analyzing, standardizing, and continuously improving processes using poka-yoke, you lead your team towards excellence, all while mitigating risks.
Starting with small changes and cultivating an inclusive culture that embraces continuous improvement and error prevention will put your organization on the path toward a robust and secure operation.
資料ダウンロード
QCD調達購買管理クラウド「newji」は、調達購買部門で必要なQCD管理全てを備えた、現場特化型兼クラウド型の今世紀最高の購買管理システムとなります。
ユーザー登録
調達購買業務の効率化だけでなく、システムを導入することで、コスト削減や製品・資材のステータス可視化のほか、属人化していた購買情報の共有化による内部不正防止や統制にも役立ちます。
NEWJI DX
製造業に特化したデジタルトランスフォーメーション(DX)の実現を目指す請負開発型のコンサルティングサービスです。AI、iPaaS、および先端の技術を駆使して、製造プロセスの効率化、業務効率化、チームワーク強化、コスト削減、品質向上を実現します。このサービスは、製造業の課題を深く理解し、それに対する最適なデジタルソリューションを提供することで、企業が持続的な成長とイノベーションを達成できるようサポートします。
オンライン講座
製造業、主に購買・調達部門にお勤めの方々に向けた情報を配信しております。
新任の方やベテランの方、管理職を対象とした幅広いコンテンツをご用意しております。
お問い合わせ
コストダウンが利益に直結する術だと理解していても、なかなか前に進めることができない状況。そんな時は、newjiのコストダウン自動化機能で大きく利益貢献しよう!
(Β版非公開)