- お役立ち記事
- The secret to creating a purchasing plan to promote cost reduction activities
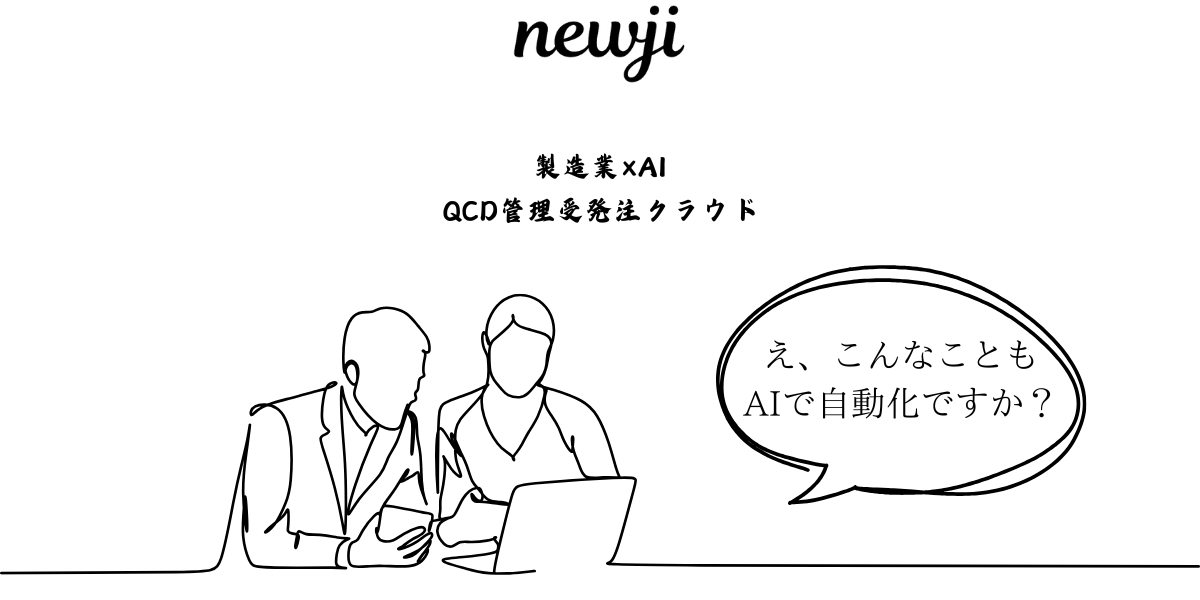
The secret to creating a purchasing plan to promote cost reduction activities
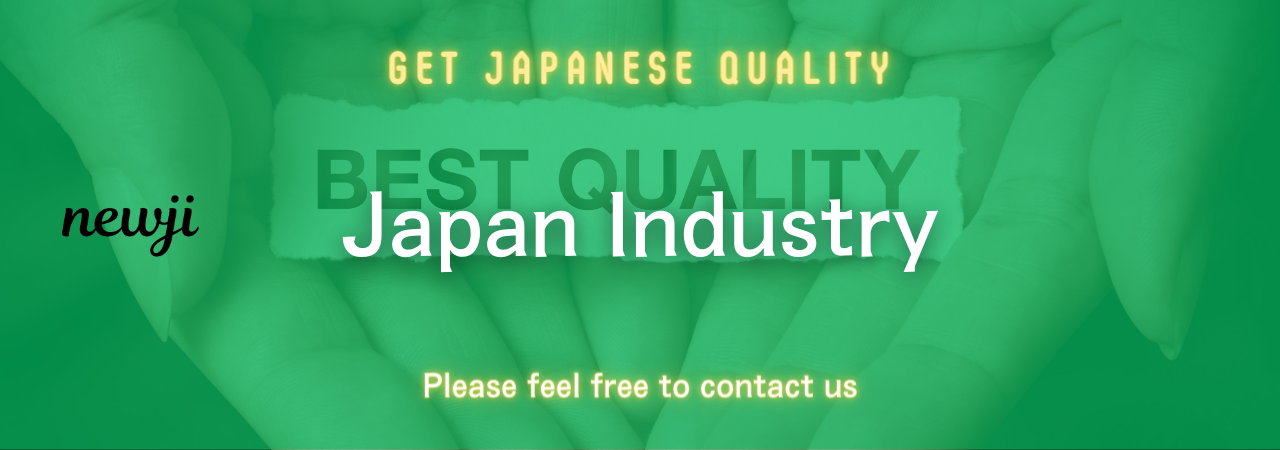
目次
Introduction to Purchasing Plans
Creating an effective purchasing plan is crucial for any business looking to optimize its operations and reduce costs.
A well-structured purchasing plan ensures that resources are allocated wisely, suppliers are managed effectively, and unnecessary expenses are minimized.
For businesses, especially those dealing with tangible products, purchasing can account for a significant portion of operational costs.
Thus, having a robust strategy in place can lead to significant savings and a more streamlined operation.
Understanding the Basics of a Purchasing Plan
A purchasing plan is essentially a strategic approach to buying goods and services necessary for running a business.
This plan outlines what needs to be procured, in what quantity, and when.
It addresses the sourcing of materials, negotiation with suppliers, and timing of purchases to ensure optimal inventory levels.
By planning purchases effectively, businesses can avoid overstocking or stockouts and strike beneficial deals with suppliers.
Identifying Business Needs
The first step in creating a purchasing plan is to clearly identify the needs of your business.
This involves understanding what products or services are essential for the operation and how they contribute to the overall business strategy.
Consider factors such as production schedules, market demand, and product lifespan when determining these needs.
Assessing Current Spending
Analyze current spending patterns to understand where your resources are being used and identify any areas of inefficiency.
Review past purchasing data, invoices, and expense reports to spot trends and variances.
It’s essential to determine if the current purchasing strategy aligns with the overall business objectives or if adjustments are necessary.
Supplier Relationships and Selection
Building strong relationships with suppliers is a cornerstone of a successful purchasing plan.
Evaluate potential suppliers based on their reliability, quality of goods, pricing terms, and service levels.
Establish criteria for selecting suppliers and maintain an updated list of preferred vendors.
Negotiating favorable terms with suppliers can lead to significant cost reductions.
Implementing Cost Reduction Strategies
Integrating cost reduction strategies into your purchasing plan is vital for maximizing savings.
These strategies are designed to trim expenses and enhance profit margins without compromising on quality or service.
Volume Buying
Purchasing in bulk can lead to attractive discounts and price concessions.
Negotiate bulk buying agreements with suppliers to take advantage of these cost savings opportunities.
However, ensure that your inventory management system is robust enough to handle increased stock levels without incurring additional holding costs.
Just-In-Time Purchasing
Adopting a Just-In-Time (JIT) purchasing approach is another effective way to reduce costs.
This strategy involves aligning purchase orders closely with production schedules to minimize inventory holding costs.
By receiving goods only when they are needed for production, businesses can reduce storage expenses and decrease the risk of obsolescence.
Leverage Technology
Utilize technology and software solutions to streamline the purchasing process.
Adopting automated procurement systems helps to track spending, manage supplier relationships, and ensure compliance with purchasing policies.
Technology can provide insights into purchasing trends and help identify areas for cost savings.
The Role of Data Analysis
Data analysis is crucial in formulating and refining purchasing plans.
By analyzing purchasing data, businesses can gain insights into spending patterns, identify inefficiencies, and make informed decisions.
Tracking Performance Metrics
Establish key performance indicators (KPIs) to evaluate the effectiveness of your purchasing plan.
Metrics such as cost savings, supplier reliability, order fulfillment rates, and inventory turnover can provide benchmarks for success.
Regularly review these KPIs to ensure your purchasing strategy continues to align with business goals.
Predictive Analysis
Utilize predictive analysis to forecast demand levels based on historical data.
Understanding future demand helps in making informed purchasing decisions, securing the best deals, and maintaining optimal inventory levels.
Effective demand forecasting helps prevent both excess stock and shortages, contributing to cost reduction.
Continuous Improvement
A purchasing plan should not be static but rather a dynamic document that evolves with the business.
Periodic review and adjustment are necessary to adapt to changing market conditions, new supplier options, and shifts in business strategy.
Regular Review and Feedback
Conduct regular reviews of the purchasing plan to ensure its continued relevance and effectiveness.
Gather feedback from stakeholders across different departments to understand how the purchasing strategy impacts overall operations.
Adapt the plan as needed to better meet business objectives and respond to market changes.
Embrace Innovation
Stay informed about new trends and innovations in the field of procurement.
Adopting new technologies, methodologies, and best practices can give your purchasing plan a competitive edge, making it more efficient and cost-effective.
Experiment with innovative tools and processes to evaluate their potential benefits to your purchasing strategy.
Conclusion
A well-crafted purchasing plan is essential for businesses looking to reduce costs and enhance operational efficiency.
By carefully planning purchases, nurturing supplier relationships, and embracing technology, businesses can achieve significant savings.
Continual improvement and data-driven decision-making are key to maintaining a successful purchasing strategy that supports business growth and sustainability.
Embrace these strategies and watch as your business thrives in a competitive market environment.
資料ダウンロード
QCD調達購買管理クラウド「newji」は、調達購買部門で必要なQCD管理全てを備えた、現場特化型兼クラウド型の今世紀最高の購買管理システムとなります。
ユーザー登録
調達購買業務の効率化だけでなく、システムを導入することで、コスト削減や製品・資材のステータス可視化のほか、属人化していた購買情報の共有化による内部不正防止や統制にも役立ちます。
NEWJI DX
製造業に特化したデジタルトランスフォーメーション(DX)の実現を目指す請負開発型のコンサルティングサービスです。AI、iPaaS、および先端の技術を駆使して、製造プロセスの効率化、業務効率化、チームワーク強化、コスト削減、品質向上を実現します。このサービスは、製造業の課題を深く理解し、それに対する最適なデジタルソリューションを提供することで、企業が持続的な成長とイノベーションを達成できるようサポートします。
オンライン講座
製造業、主に購買・調達部門にお勤めの方々に向けた情報を配信しております。
新任の方やベテランの方、管理職を対象とした幅広いコンテンツをご用意しております。
お問い合わせ
コストダウンが利益に直結する術だと理解していても、なかなか前に進めることができない状況。そんな時は、newjiのコストダウン自動化機能で大きく利益貢献しよう!
(Β版非公開)