- お役立ち記事
- For new employees in the design department of the precision machinery industry! Fundamentals of achieving lightweight design through topology optimization
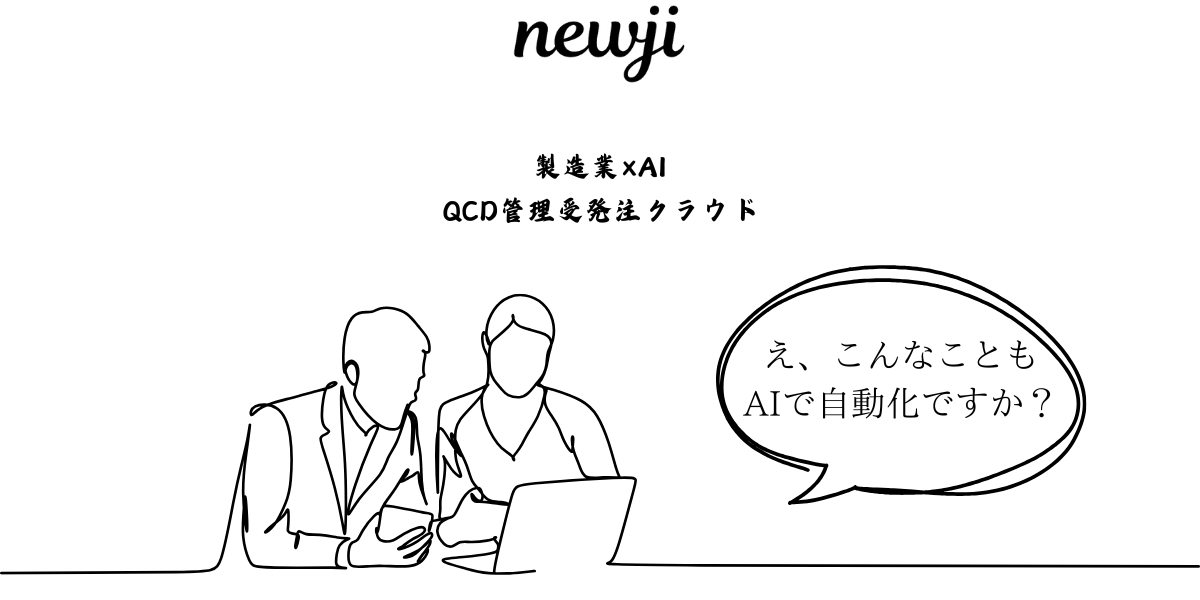
For new employees in the design department of the precision machinery industry! Fundamentals of achieving lightweight design through topology optimization
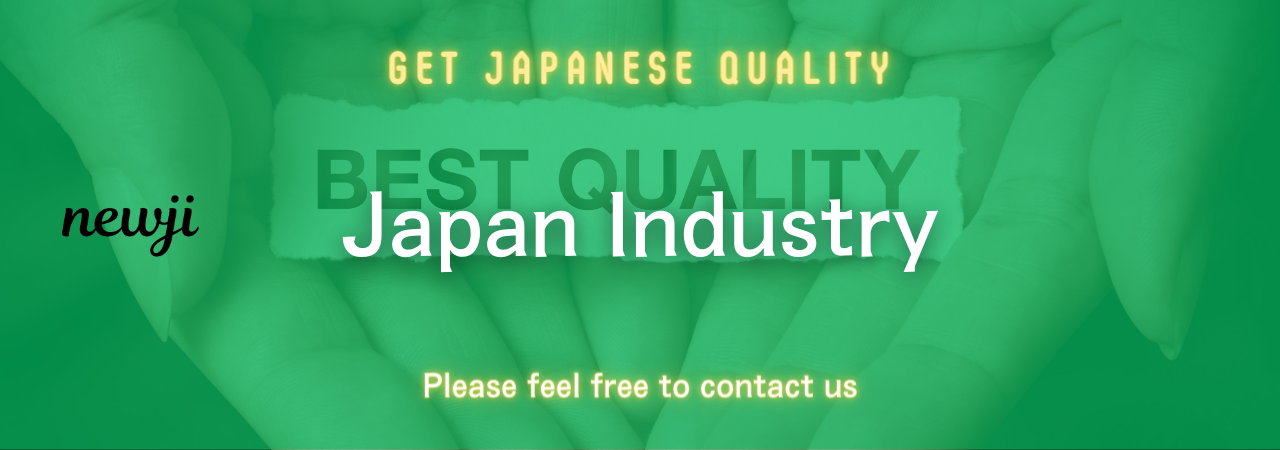
目次
Understanding Lightweight Design
In today’s precision machinery industry, achieving a lightweight design is crucial for improving performance and efficiency.
A lightweight design not only reduces material costs and increases energy efficiency but also enhances the overall functionality of machines.
For new employees in the design department, grasping the fundamentals of lightweight design is essential for contributing effectively to your team’s goals.
A key method used to achieve lightweight design is topology optimization.
By understanding and implementing topology optimization, you can significantly enhance the design process and deliver optimal solutions.
What is Topology Optimization?
Topology optimization is a mathematical approach that optimizes material layout within a given design space, subject to defined constraints and load conditions.
This method helps determine the best distribution of material for a component, effectively minimizing weight while maintaining structural integrity and functionality.
Essentially, topology optimization allows engineers to pinpoint where material is needed and where it can be removed, leading to a more efficient and sustainable design.
This process leverages advanced algorithms to find the optimal structure, often resulting in organic, complex shapes that traditional design methods might not easily identify.
The Importance of Topology Optimization in Precision Machinery
In the precision machinery industry, components often have strict requirements regarding weight, size, and performance.
Lightweight components can improve machine speed, reduce energy consumption, and decrease wear and tear, ultimately extending the machine’s lifespan.
Hence, employing topology optimization becomes vital in designing components that meet these stringent criteria while ensuring reliability and cost-effectiveness.
Key Steps in the Topology Optimization Process
To effectively implement topology optimization in your design department, it is essential to understand its key steps:
1. Define Design Space and Constraints
The first step in topology optimization is defining the design space – the volume within which the component will be designed.
Within this space, engineers must also establish any constraints that the design needs to satisfy, such as load conditions, support points, and material properties.
Accurate definition of these parameters is critical, as they influence the efficiency and feasibility of the resulting design.
2. Establish Objectives
Once the design space and constraints are set, the next step is to define the objectives of the optimization.
In lightweight design, the primary goal is often to minimize the material used or the weight of the component while maintaining structural integrity and performance under given loads.
Having clear objectives ensures that the optimization process targets the right outcomes, leading to a practical and effective design.
3. Perform Simulation and Iteration
With the design space, constraints, and objectives defined, the optimization process uses advanced algorithms to simulate and generate multiple iterations of possible designs.
These simulations consider all constraints and variables to assess which materials can be removed or redistributed for the optimal arrangement.
Engineers will analyze various iterations to refine the design continuously, ensuring all design goals are met efficiently.
4. Validate the Design
After achieving an optimal topology, the design must be validated through additional simulations or physical prototyping.
Validation ensures that the final design meets all necessary performance standards and functions effectively in real-world applications.
Tools and Software for Topology Optimization
The precision machinery industry has access to various tools and software designed to facilitate topology optimization.
These platforms offer robust simulation capabilities and user-friendly interfaces to streamline the optimization process.
Popular tools like ANSYS, Altair OptiStruct, and SolidWorks Simulation are widely used in the industry, providing comprehensive solutions for engineers to implement lightweight designs efficiently.
Learning and Adapting New Technologies
One of the key aspects of being successful in the design department is staying up-to-date with the latest technologies and trends.
Participating in workshops, online courses, and seminars on topology optimization will enhance your skills and expand your understanding of lightweight design methods.
Continuously improving your knowledge of cutting-edge tools and strategies will enable you to contribute more effectively to your team and drive innovation within your organization.
Challenges in Implementing Topology Optimization
While topology optimization offers numerous benefits, it is not without its challenges.
Some common issues include computational costs, interpretation of complex organic shapes, and manufacturing limitations.
Addressing Computational Costs
The optimization process can be computationally intensive, requiring significant processing power and time to generate useful solutions.
Investing in adequate hardware and optimizing simulation settings can help mitigate these challenges.
Interpreting Complex Designs
The resulting shapes from topology optimization might be complex and difficult to interpret using traditional manufacturing methods.
However, advancements in additive manufacturing and 3D printing technology provide new opportunities for fabricating these optimized designs.
Navigating Manufacturing Limitations
Finally, it is crucial to evaluate the feasibility of manufacturing an optimized design.
Collaborating with production teams to understand manufacturing capabilities and constraints helps ensure that designs are both practical and producible.
Conclusion
For new employees in the precision machinery industry’s design department, understanding the fundamentals of lightweight design through topology optimization is essential.
This method offers a powerful approach to creating efficient, effective, and sustainable designs.
By mastering topology optimization, you will be well-equipped to contribute to your team’s success and help drive innovation in the industry.
So keep learning, stay curious, and embrace the challenges of creating cutting-edge solutions through lightweight design.
資料ダウンロード
QCD調達購買管理クラウド「newji」は、調達購買部門で必要なQCD管理全てを備えた、現場特化型兼クラウド型の今世紀最高の購買管理システムとなります。
ユーザー登録
調達購買業務の効率化だけでなく、システムを導入することで、コスト削減や製品・資材のステータス可視化のほか、属人化していた購買情報の共有化による内部不正防止や統制にも役立ちます。
NEWJI DX
製造業に特化したデジタルトランスフォーメーション(DX)の実現を目指す請負開発型のコンサルティングサービスです。AI、iPaaS、および先端の技術を駆使して、製造プロセスの効率化、業務効率化、チームワーク強化、コスト削減、品質向上を実現します。このサービスは、製造業の課題を深く理解し、それに対する最適なデジタルソリューションを提供することで、企業が持続的な成長とイノベーションを達成できるようサポートします。
オンライン講座
製造業、主に購買・調達部門にお勤めの方々に向けた情報を配信しております。
新任の方やベテランの方、管理職を対象とした幅広いコンテンツをご用意しております。
お問い合わせ
コストダウンが利益に直結する術だと理解していても、なかなか前に進めることができない状況。そんな時は、newjiのコストダウン自動化機能で大きく利益貢献しよう!
(Β版非公開)