- お役立ち記事
- For design department leaders in the auto parts industry! Successful examples of lightweight design using CAE analysis
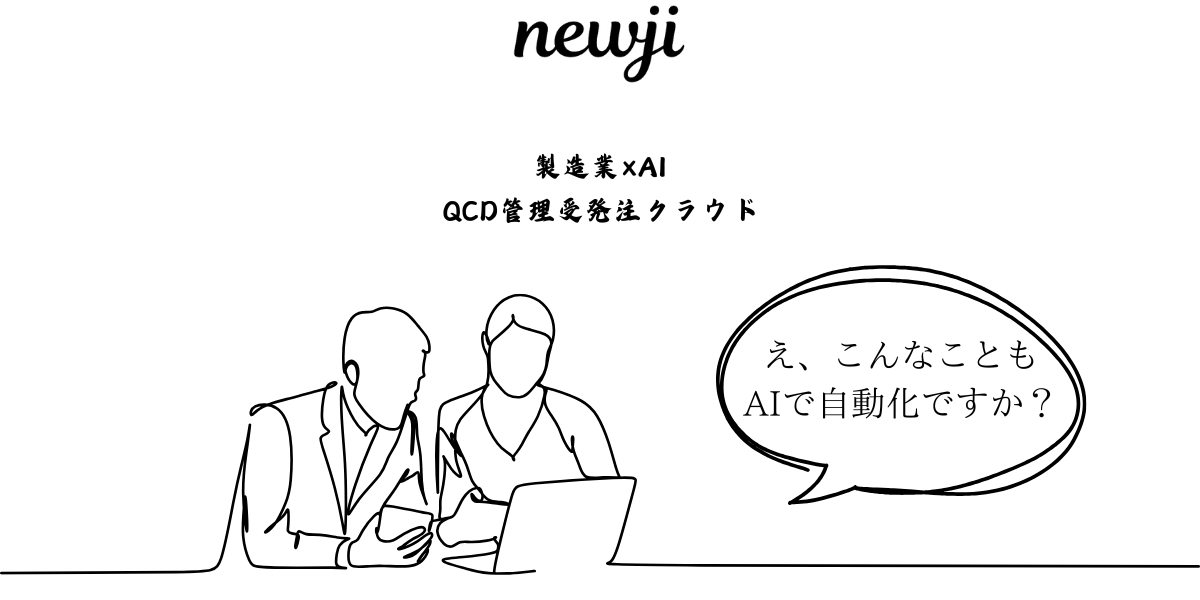
For design department leaders in the auto parts industry! Successful examples of lightweight design using CAE analysis
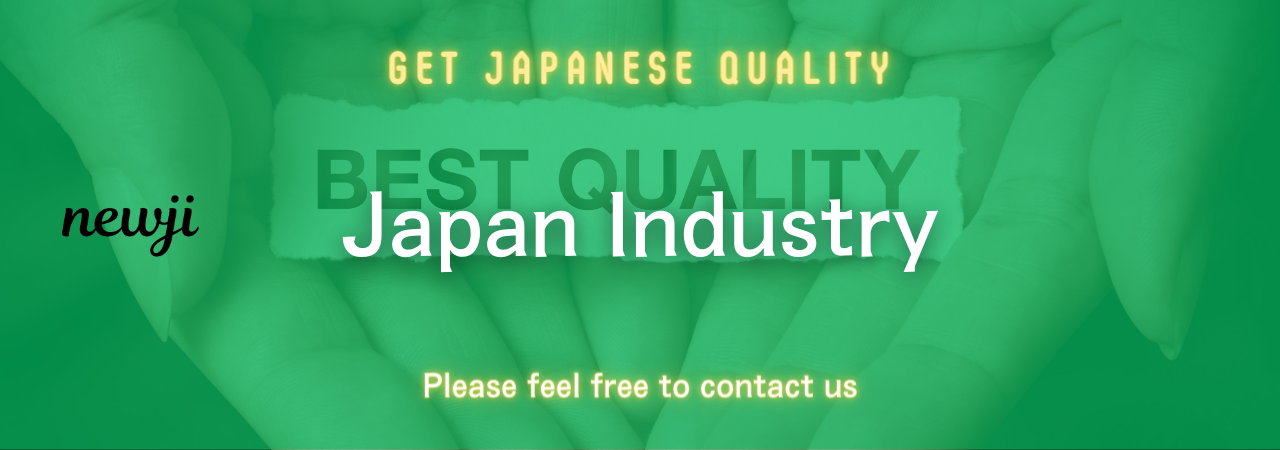
目次
Understanding Lightweight Design in the Auto Parts Industry
In the ever-evolving auto parts industry, the pursuit of efficiency is paramount.
One of the key strategies to achieve this is through lightweight design.
This approach not only reduces vehicle weight but also enhances fuel efficiency and performance.
Lightweight design involves using innovative materials and design techniques to minimize the mass of vehicle components while maintaining or improving their functionality.
CAE (Computer-Aided Engineering) analysis plays a crucial role in this process.
It allows engineers to simulate and evaluate the performance of various design alternatives in a virtual environment before physical prototypes are built.
This reduces development time and costs while ensuring optimal design solutions.
The Role of CAE Analysis in Lightweight Design
CAE analysis is a powerful tool that aids design departments in making informed decisions about material selection and structural optimization.
Using CAE, engineers can identify stress points, predict failure modes, and assess the overall strength of components under different loads.
By simulating real-world conditions, CAE analysis enables designers to explore a wider range of lightweight materials such as aluminum, magnesium, and composites.
It helps in predicting how these materials will behave in the final product, allowing for smarter, data-driven decisions that prioritize both safety and weight reduction.
Benefits of Lightweight Design
Accomplishing a lightweight design in auto parts can lead to several benefits:
1. **Improved Fuel Efficiency**: Reduced weight directly translates to less energy required for propulsion, enhancing fuel economy.
2. **Enhanced Performance**: Lighter components contribute to better vehicle handling and acceleration, improving overall driving experience.
3. **Reduced Emissions**: With increased fuel efficiency, vehicles emit less carbon dioxide, supporting environmental goals and regulations.
4. **Cost Savings**: Though the initial cost of lightweight materials may be higher, the long-term savings on fuel and maintenance make it a cost-effective strategy.
Successful Applications of CAE in Lightweight Design
Numerous examples exist where CAE analysis has been successfully applied to achieve lightweight designs in the auto industry.
Case Study: Lightweight Suspension System
In a popular case, a leading auto manufacturer sought to reduce the weight of their suspension system without compromising its durability.
Using CAE analysis, they evaluated different material combinations and geometric configurations.
The insights gained from CAE simulations led to the selection of an innovative alloy, reducing the weight of the suspension system by 15% while enhancing its stress tolerance.
Case Study: Brake Component Optimization
Another example involved optimizing brake components for a new vehicle model.
Engineers used CAE analysis to simulate the thermal and mechanical stresses exerted on the brakes during operation.
This allowed them to redesign the components with a lightweight composite material that provided the necessary strength and heat resistance, resulting in a 10% weight reduction.
Challenges in Implementing Lightweight Design
While the benefits are clear, implementing lightweight design using CAE analysis is not without challenges.
Material Costs and Availability
Lightweight materials, especially composites and high-strength alloys, often come with higher costs.
Balancing the budget while achieving the desired weight reduction is a common challenge that design departments face.
Complexity of Simulations
Complex CAE simulations require specialized knowledge and expertise.
The intricacies involved in setting up simulation models and interpreting results can be daunting for teams not well-versed in CAE technology.
Integration with Traditional Processes
Integrating CAE-driven designs with traditional manufacturing processes requires careful planning.
There might be a need to adapt existing production lines or invest in new equipment to accommodate lightweight materials and designs.
Overcoming Challenges with Strategic Approaches
Despite challenges, several strategies can help design departments successfully implement lightweight design using CAE analysis.
Investing in Training and Tools
Providing adequate training for design teams in CAE software and analysis techniques is crucial.
Investing in the latest tools and technologies ensures that teams can conduct accurate simulations efficiently.
Collaboration with Material Experts
Collaborating with material scientists and suppliers can help in understanding the properties and potential applications of new materials.
Such partnerships can bridge the gap between theoretical designs and practical implementations.
Iterative Design Processes
Adopting an iterative approach to design and testing helps in refining lightweight solutions.
Conducting multiple simulation cycles allows for the exploration of various design alternatives, leading to the optimal balance between weight, cost, and performance.
The Future of Lightweight Design with CAE
As automotive technology advances, the role of lightweight design will become increasingly significant.
CAE analysis will continue to be an indispensable tool for the industry, empowering designers to push the boundaries of innovation.
The future promises even more sophisticated simulation capabilities, integrating artificial intelligence and machine learning to predict performance with unprecedented accuracy.
In conclusion, lightweight design using CAE analysis offers substantial advantages for the auto parts industry.
By embracing this approach, design departments can create components that meet modern standards of efficiency and environmental responsibility.
The success of such initiatives hinges on overcoming challenges through strategic investments in technology and talent, paving the way for a more sustainable automotive future.
資料ダウンロード
QCD調達購買管理クラウド「newji」は、調達購買部門で必要なQCD管理全てを備えた、現場特化型兼クラウド型の今世紀最高の購買管理システムとなります。
ユーザー登録
調達購買業務の効率化だけでなく、システムを導入することで、コスト削減や製品・資材のステータス可視化のほか、属人化していた購買情報の共有化による内部不正防止や統制にも役立ちます。
NEWJI DX
製造業に特化したデジタルトランスフォーメーション(DX)の実現を目指す請負開発型のコンサルティングサービスです。AI、iPaaS、および先端の技術を駆使して、製造プロセスの効率化、業務効率化、チームワーク強化、コスト削減、品質向上を実現します。このサービスは、製造業の課題を深く理解し、それに対する最適なデジタルソリューションを提供することで、企業が持続的な成長とイノベーションを達成できるようサポートします。
オンライン講座
製造業、主に購買・調達部門にお勤めの方々に向けた情報を配信しております。
新任の方やベテランの方、管理職を対象とした幅広いコンテンツをご用意しております。
お問い合わせ
コストダウンが利益に直結する術だと理解していても、なかなか前に進めることができない状況。そんな時は、newjiのコストダウン自動化機能で大きく利益貢献しよう!
(Β版非公開)