- お役立ち記事
- サプライヤー品質向上のための共通基準策定と監査の手順
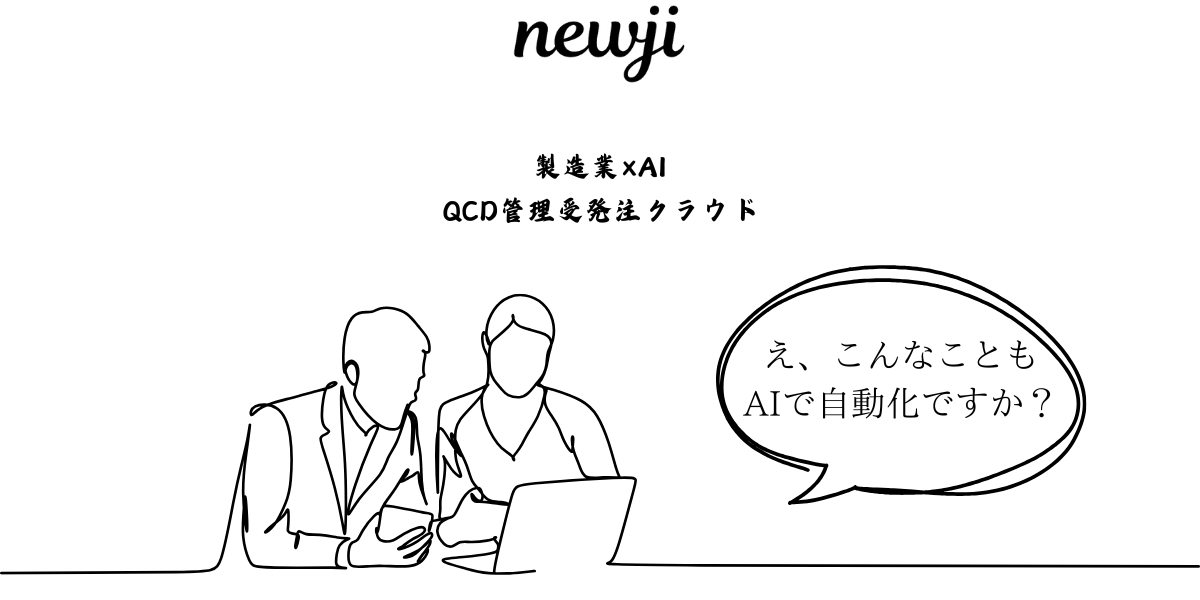
サプライヤー品質向上のための共通基準策定と監査の手順
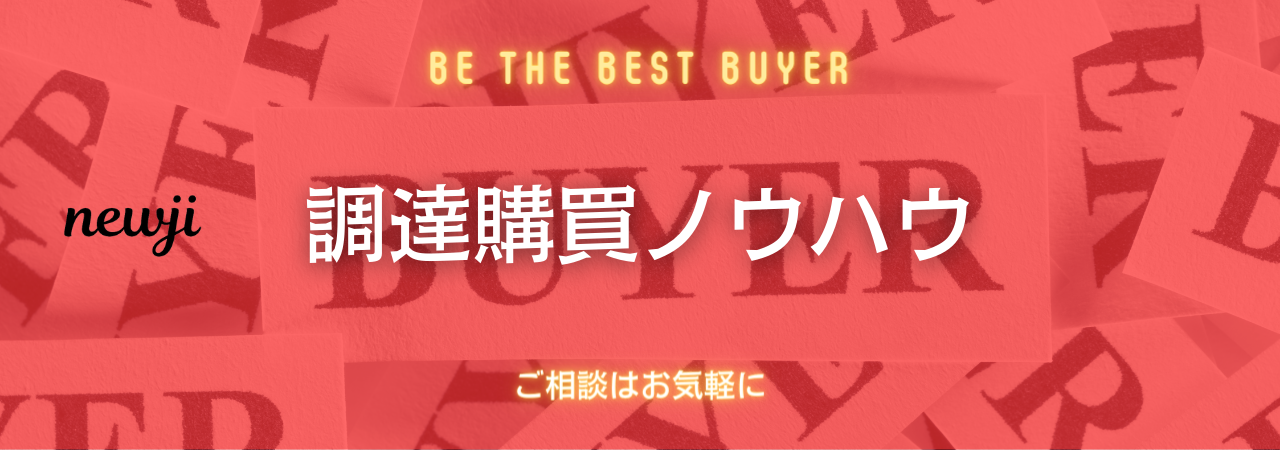
目次
サプライヤー品質向上の重要性
製造業の競争が激化する中、製品の品質は企業の競争力の根幹を成します。
高品質な製品を提供するためには、自社の製造工程だけでなく、サプライヤーが提供する部品や材料の品質も重要です。
サプライヤーの品質が低下すると、最終製品の不良やリコールのリスクが高まり、ビジネスに大きな影響を及ぼす可能性があります。
そのため、サプライヤーの品質向上を図ることは、製造業にとって不可欠な取り組みなのです。
共通基準策定の必要性
サプライヤー品質を向上させるために、まず第一に必要なのは品質基準の策定です。
多くの製造業者がサプライヤーに任せきりにするのではなく、自社の基準に基づいた品質要求を明確にすることが重要です。
共通基準を策定することで、サプライヤーとのコミュニケーションが円滑になり、期待する品質レベルを共有できます。
品質基準の要素
品質基準には以下の要素を含めることが一般的です。
– 製品仕様と性能要件
– プロセス管理と工程監視の手法
– 材料や部品のトレーサビリティ
– 検査および試験の頻度と方法
– 品質管理システム(ISO 9001など)の適用
これらの要素を具体的に定め、サプライヤーとの契約書や品質ガイドラインとして文書化することが推奨されます。
共通基準策定のステップ
ステップ1: 製品と市場の分析
まず、自社製品の特性と市場の要求を分析します。
製品の使用環境や競争製品の品質レベルを考慮し、最低限必要な品質レベルを設定します。
ステップ2: ベンチマーク調査
次に、業界のベストプラクティスを調査し、他社がどのような基準を設けているかベンチマークします。
これにより、自社の基準を相対的に評価し、必要に応じて調整します。
ステップ3: 内部および外部のステークホルダーからのフィードバック
製品開発、品質管理、購買などの関連部門やサプライヤーからのフィードバックを集め、基準に反映させます。
現場のニーズを反映することで、より実用的な基準が策定できます。
ステップ4: ドキュメント化とサプライヤーへの導入
策定した基準を文書化し、サプライヤーに導入します。
トレーニングセッションを提供し、基準の意図や詳細を理解してもらいます。
監査の手順
共通基準の策定だけでなく、その実施状況を確認するための監査も重要です。
監査は、品質基準が確実に守られているかの確認だけでなく、改善点の発見にもつながるため、定期的に実施することが望ましいです。
監査の種類
サプライヤー監査には主に以下の種類があります。
– 初回監査: 新規サプライヤーを登録する際の評価
– 定期監査: 既存のサプライヤーの維持と改善のために行う
– 特別監査: 重大な品質問題が発生した場合に行う
監査のステップ
ステップ1: 監査計画の策定
監査の目的、範囲、スケジュールを計画します。
どの製品やプロセスを対象とし、何を確認すべきかを明確にします。
ステップ2: 事前調査
過去の品質データやサプライヤーから提供された情報を調査し、リスクや焦点ポイントを特定します。
ステップ3: 現場監査の実施
監査チームがサプライヤーの現場に赴き、製造プロセス、品質管理の仕組み、従業員の訓練状況などを評価します。
これには、製品サンプルの検査やプロセスの観察も含まれます。
ステップ4: フィードバックと改善提案
監査結果を分析し、報告書を作成します。
サプライヤーにフィードバックを提供し、改善のための具体的な提案を行います。
サプライヤーとの効果的なコミュニケーション
共通基準の策定と監査を効果的に進めるには、サプライヤーとのコミュニケーションが鍵となります。
以下のポイントを心がけて、良好な関係を築くことが重要です。
透明性の確保
品質基準や監査結果について透明性を保ち、サプライヤーとオープンに情報を共有します。
問題が発生した場合には迅速に連絡し、一緒に解決策を考えることが重要です。
建設的なフィードバック
監査結果や日常のコミュニケーションで得られるフィードバックは、建設的かつ前向きなものであるべきです。
批判に終始せず、具体的な改善策を提示し、サプライヤーの成長を促します。
共同改善活動
サプライヤーと共同で改善プロジェクトを行います。
例えば、品質問題の根本原因分析を一緒に行い、プロセス改善やコスト削減につながる活動を推進します。
最新の業界トレンドと技術の活用
サプライヤー品質向上のためには、最新の業界動向や技術の活用も重要です。
デジタル技術の導入
IoTやクラウドベースのプラットフォームを活用して、リアルタイムでサプライチェーン情報を共有することが可能です。
これにより、品質問題を早期に検出し、迅速な対応が可能になります。
人工知能(AI)の活用
AIを用いた予測分析により、品質問題の発生を未然に防ぐことができます。
生産データを解析してトレンドやパターンを見つけ、サプライヤーのパフォーマンスを予測することが可能です。
結論
サプライヤー品質を向上させるための共通基準策定と監査は、製造業における品質管理の重要な要素です。
明確な基準の策定、効果的な監査の実施、サプライヤーとのコラボレーションを通じて、高品質な製品を提供し続けることができます。
また、最新技術を活用することで、より効率的に品質管理を行うことができ、企業全体の競争力向上につながるでしょう。
資料ダウンロード
QCD調達購買管理クラウド「newji」は、調達購買部門で必要なQCD管理全てを備えた、現場特化型兼クラウド型の今世紀最高の購買管理システムとなります。
ユーザー登録
調達購買業務の効率化だけでなく、システムを導入することで、コスト削減や製品・資材のステータス可視化のほか、属人化していた購買情報の共有化による内部不正防止や統制にも役立ちます。
NEWJI DX
製造業に特化したデジタルトランスフォーメーション(DX)の実現を目指す請負開発型のコンサルティングサービスです。AI、iPaaS、および先端の技術を駆使して、製造プロセスの効率化、業務効率化、チームワーク強化、コスト削減、品質向上を実現します。このサービスは、製造業の課題を深く理解し、それに対する最適なデジタルソリューションを提供することで、企業が持続的な成長とイノベーションを達成できるようサポートします。
オンライン講座
製造業、主に購買・調達部門にお勤めの方々に向けた情報を配信しております。
新任の方やベテランの方、管理職を対象とした幅広いコンテンツをご用意しております。
お問い合わせ
コストダウンが利益に直結する術だと理解していても、なかなか前に進めることができない状況。そんな時は、newjiのコストダウン自動化機能で大きく利益貢献しよう!
(Β版非公開)