- お役立ち記事
- Order timing to keep in mind when planning procurement and tips for shortening lead time
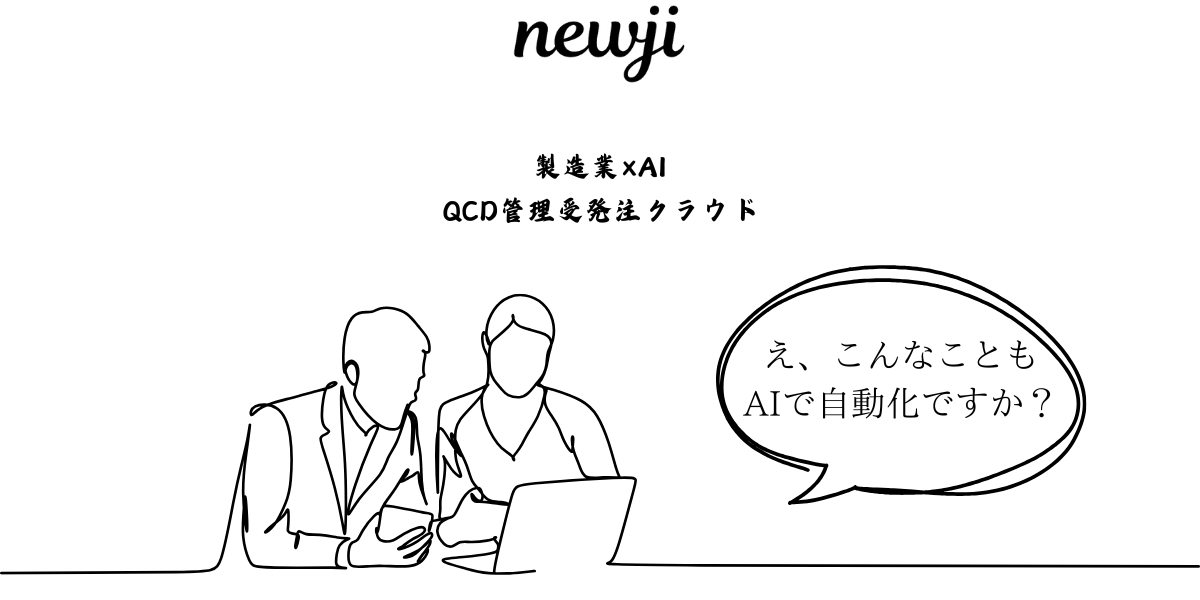
Order timing to keep in mind when planning procurement and tips for shortening lead time
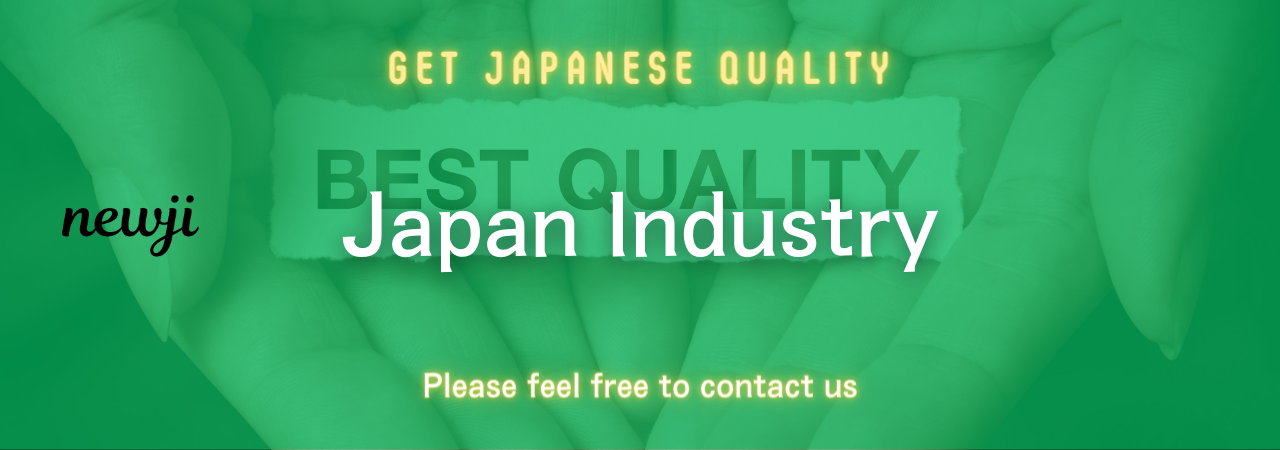
目次
Understanding Order Timing in Procurement
Effective procurement is crucial for any business to maintain smooth operations and meet customer demands.
One of the key aspects of successful procurement is mastering the timing of orders.
Understanding when to place orders can help prevent stockouts and overstock situations while also optimizing cash flow.
Let’s delve into the importance of order timing and how it can impact your procurement strategy.
The Significance of Order Timing
Order timing is the strategic decision-making process regarding when to place orders for goods or services needed by your organization.
It directly affects inventory levels, production schedules, and overall business efficiency.
Placing orders either too early or too late can lead to various challenges.
Early orders can result in excessive inventory holding costs, tying up capital that could be better used elsewhere in the business.
On the other hand, late orders can lead to stockouts, production delays, or missed sales opportunities, harming customer relationships and potentially leading to revenue loss.
Factors Influencing Order Timing
Several factors can influence the optimal timing for placing procurement orders.
Understanding these factors can help businesses make informed decisions and improve their procurement efficiency.
Demand Forecasting
Accurate demand forecasting is essential in determining the right order timing.
By analyzing historical sales data, market trends, and customer preferences, businesses can predict future demand more effectively.
This enables them to place orders accordingly, ensuring that inventory levels align with expected sales.
Supplier Lead Time
Lead time, the time it takes for an order to be fulfilled by suppliers, is another critical factor.
Businesses need to consider the lead time to ensure that orders arrive just in time for use.
Longer lead times may require placing orders earlier, while shorter lead times offer more flexibility.
Economic Order Quantity (EOQ)
The Economic Order Quantity is a formula used to determine the ideal order size that minimizes total inventory costs, including ordering and holding costs.
Understanding the EOQ can help businesses decide on the optimal timing and quantity for orders, balancing costs and inventory levels efficiently.
Supplier Reliability
The reliability of suppliers in delivering orders on time and as expected is crucial for effective order timing.
Businesses should build strong relationships with reliable suppliers to ensure smooth procurement operations.
In cases where suppliers are less reliable, additional buffer time may be required to mitigate risks.
Tips for Shortening Lead Time
Reducing lead time is a vital aspect of optimizing procurement processes.
Shorter lead times can enhance agility, responsiveness, and competitiveness.
Here are some practical tips to help shorten lead time in procurement:
Streamline Processes
Reviewing and streamlining internal procurement processes can help reduce lead time.
Identify bottlenecks or redundant steps in the process and eliminate them to expedite order placement and approval.
Automation tools can also help by quickly processing purchase orders and facilitating communication between teams.
Enhance Supplier Relationships
Building strong, collaborative relationships with suppliers can result in better communication and faster response times.
Regularly engage with suppliers to understand their capabilities and limitations.
Negotiating favorable terms, such as reduced lead times, can also benefit both parties.
Invest in Inventory Management Systems
Implementing advanced inventory management systems can provide real-time visibility into inventory levels and supplier lead times.
These systems can automate reorder points and alerts, allowing businesses to stay informed and place orders promptly.
Consider Dual Sourcing
Relying on a single supplier poses risks, especially regarding lead time delays.
Exploring dual sourcing options can diversify the supply chain and ensure faster order fulfillment.
In the event of delay from one supplier, businesses can rely on an alternative source to maintain consistent supply.
Conclusion
Mastering the art of order timing in procurement is essential for maintaining an efficient and effective supply chain.
By understanding the factors influencing order timing, businesses can make informed decisions that prevent stockouts and reduce unnecessary costs.
Additionally, implementing strategies to reduce lead time can enhance agility and responsiveness, giving businesses a competitive edge in the market.
Incorporating these best practices into your procurement strategy will ultimately lead to improved operations, satisfied customers, and a stronger bottom line.
As you refine your procurement processes, remember that timing, like other aspects of business, requires continuous evaluation and adaptation to changing circumstances and needs.
資料ダウンロード
QCD調達購買管理クラウド「newji」は、調達購買部門で必要なQCD管理全てを備えた、現場特化型兼クラウド型の今世紀最高の購買管理システムとなります。
ユーザー登録
調達購買業務の効率化だけでなく、システムを導入することで、コスト削減や製品・資材のステータス可視化のほか、属人化していた購買情報の共有化による内部不正防止や統制にも役立ちます。
NEWJI DX
製造業に特化したデジタルトランスフォーメーション(DX)の実現を目指す請負開発型のコンサルティングサービスです。AI、iPaaS、および先端の技術を駆使して、製造プロセスの効率化、業務効率化、チームワーク強化、コスト削減、品質向上を実現します。このサービスは、製造業の課題を深く理解し、それに対する最適なデジタルソリューションを提供することで、企業が持続的な成長とイノベーションを達成できるようサポートします。
オンライン講座
製造業、主に購買・調達部門にお勤めの方々に向けた情報を配信しております。
新任の方やベテランの方、管理職を対象とした幅広いコンテンツをご用意しております。
お問い合わせ
コストダウンが利益に直結する術だと理解していても、なかなか前に進めることができない状況。そんな時は、newjiのコストダウン自動化機能で大きく利益貢献しよう!
(Β版非公開)