- お役立ち記事
- Fundamentals of PID control and applications to digital control methods and control parameter tuning technology
Fundamentals of PID control and applications to digital control methods and control parameter tuning technology
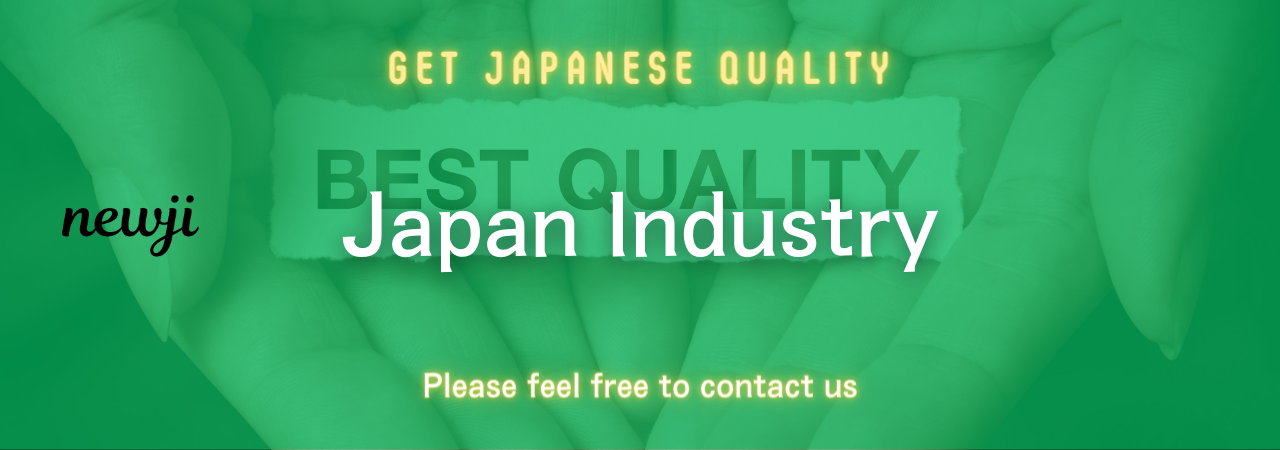
目次
Understanding PID Control
When we talk about control systems, PID control is one of the most common strategies utilized in a variety of industries.
PID stands for Proportional-Integral-Derivative, a control loop feedback mechanism widely used in industrial control, electronics, flight control, and many other fields.
The primary purpose of a PID controller is to keep a process or system at a desired setpoint by adjusting control outputs.
In simple terms, a PID controller continuously calculates an error value, which is the difference between the desired setpoint and the measured process variable.
It then applies a correction based on proportional, integral, and derivative terms.
These terms are often referred to as the controller’s “gains” and they determine the behavior of the control system.
Proportional Control (P)
The proportional term of the PID controller produces an output that is proportional to the current error value.
It’s calculated by multiplying the error signal with a proportional gain, known as Kp.
This part of the controller can make the control system respond quickly to changes in the error.
However, relying solely on proportional control can result in a steady-state error.
Even when the system gets close to the desired setpoint, a small error may persist because the proportional action is only effective when there is an error to work on.
This steady-state error necessitates the introduction of the Integral term.
Integral Control (I)
The integral term deals with the accumulation of past error over time.
It multiplies the error term by an integral gain, referred to as Ki, and sums up every moment in which there has been an error to adjust the controller’s output accordingly.
By addressing the accumulated errors, the integral action helps eliminate the steady-state error seen with proportional control alone.
While integral control is effective in eliminating steady-state errors, it can introduce overshoot and oscillation, due to its nature of accumulating past errors.
Thus, while it helps to reach the accurate setpoint, it must be carefully tuned.
Derivative Control (D)
The derivative term predicatively reduces the error by considering the rate of change of the error.
Essentially, it responds to the trend of the error, by multiplying the derivative gain, Kd, with the rate of change of the error.
This predictive element helps counteract overshoot and improve system stability.
However, derivative control is sensitive to noise, as it amplifies abrupt errors.
Thus, not all systems apply derivative control when the input signal is prone to noise.
Moreover, derivative control on its own cannot correct the error, as it depends on changes in error rather than an absolute measure of error.
Combining P, I, and D
Each of these components influences the behavior of a PID controller differently, and their proper combination is crucial for an effective control system.
The combined effect of the proportional, integral, and derivative components allows the controller to navigate various dynamic system conditions.
The proportional component provides immediate correction, the integral component assures setpoint accuracy over time, and the derivative component gives predictive dampening to minimize oscillations.
Fine-tuning these gains ensures the system behaves optimally, responding quickly to changes without excessive overshoot or oscillation.
Applications of PID Control
PID control is intrinsic to various applications where precision is crucial.
Let’s explore some of the primary applications in which PID controllers play a vital role:
Industrial Process Control
In industry, PID controllers are used extensively for process control, managing variables like temperature, pressure, flow rate, and level.
For example, in a chemical plant, the PID controller adjusts the acid and base pumps to maintain a specific pH level.
In utilities, it can regulate boiler temperatures and pressure to optimize energy production.
Robotics
In robotics, PID controllers serve to maintain specific aspects such as arm position or speed in robotic actuators.
The controller ensures smooth and precise control over positional tasks, which is paramount for operations requiring high accuracy.
Aerospace and Automotive
In aerospace and automotive industries, PID controllers are implemented for flight control systems and automotive engine management.
Flight control systems use PID controllers to stabilize aircraft pitch, roll, and yaw, enhancing maneuverability and safety.
Meanwhile, automakers utilize PID controllers to optimize fuel injection and turbocharger control systems.
HVAC Systems
Heating, Ventilation, and Air Conditioning (HVAC) systems benefit significantly from PID control.
By maintaining setpoints for temperature and humidity, these systems maximize comfort while minimizing energy consumption.
Tuning PID Controllers
The efficiency of a PID controller depends heavily on how well it is tuned.
The tuning process involves setting the parameters Kp, Ki, and Kd to achieve optimal system performance.
Improper tuning can lead to instability, sluggish response, or excessive oscillations.
Manual Tuning
Manual tuning involves trial and error to find the right balance among the proportional, integral, and derivative terms.
This method requires expertise and is time-consuming but allows for fine adjustments to account for specific system dynamics.
Automated Tuning Methods
To expedite the tuning process, automated methods are often used.
These include techniques like the Ziegler-Nichols method, relay tuning processes, and software-based autotuners.
These methods save time and increase precision compared to manual tuning.
Digital Control and Tuning
With advancements in digital technology, digital algorithms now aid PID tuning and control more accurately.
Digital PID controllers provide advanced tuning solutions, allowing seamless integration into modern programmable logic controllers (PLCs) and control systems.
They accommodate complex computations and adapt dynamically to changing systems conditions.
The Future of PID Control
As technology evolves, PID control continues to be pivotal in diverse applications, enhanced by digital technology and sophisticated algorithms.
In the future, emerging technologies such as machine learning and artificial intelligence could provide new avenues for automated and intelligent PID tuning, further optimizing control systems.
Incorporating adaptive and self-tuning mechanisms with PID control ensures that as systems become more complex, they maintain efficiency and reliability.
資料ダウンロード
QCD調達購買管理クラウド「newji」は、調達購買部門で必要なQCD管理全てを備えた、現場特化型兼クラウド型の今世紀最高の購買管理システムとなります。
ユーザー登録
調達購買業務の効率化だけでなく、システムを導入することで、コスト削減や製品・資材のステータス可視化のほか、属人化していた購買情報の共有化による内部不正防止や統制にも役立ちます。
NEWJI DX
製造業に特化したデジタルトランスフォーメーション(DX)の実現を目指す請負開発型のコンサルティングサービスです。AI、iPaaS、および先端の技術を駆使して、製造プロセスの効率化、業務効率化、チームワーク強化、コスト削減、品質向上を実現します。このサービスは、製造業の課題を深く理解し、それに対する最適なデジタルソリューションを提供することで、企業が持続的な成長とイノベーションを達成できるようサポートします。
オンライン講座
製造業、主に購買・調達部門にお勤めの方々に向けた情報を配信しております。
新任の方やベテランの方、管理職を対象とした幅広いコンテンツをご用意しております。
お問い合わせ
コストダウンが利益に直結する術だと理解していても、なかなか前に進めることができない状況。そんな時は、newjiのコストダウン自動化機能で大きく利益貢献しよう!
(Β版非公開)