- お役立ち記事
- Thermal design of electronic equipment using the basics of thermofluid engineering and model-based development and its practical points
Thermal design of electronic equipment using the basics of thermofluid engineering and model-based development and its practical points
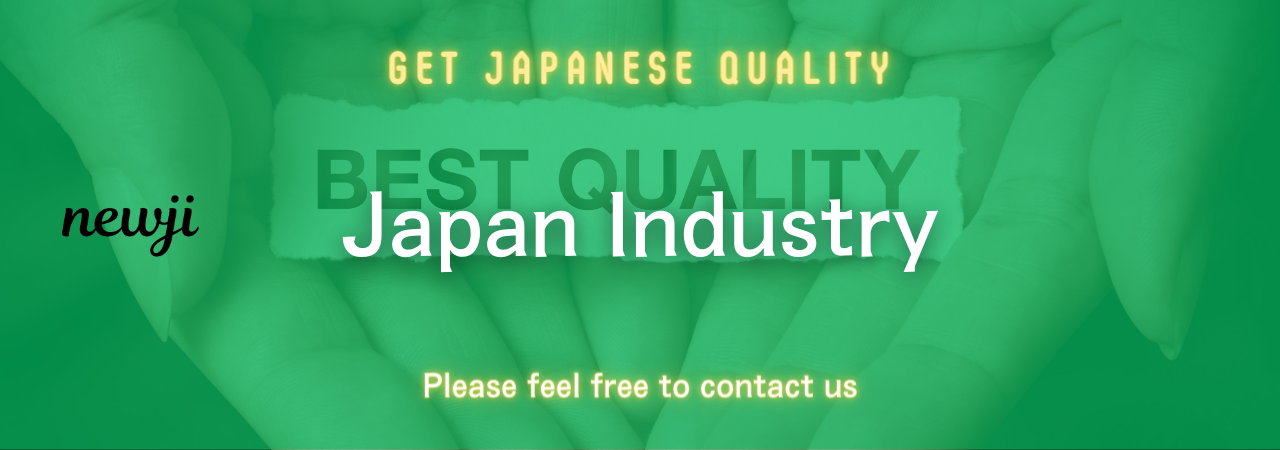
目次
Understanding Thermofluid Engineering
Thermal design is a crucial aspect of developing electronic equipment that ensures efficiency, reliability, and longevity.
At its core, thermal design involves managing the heat generated within electronic systems to prevent overheating and failure.
One fundamental approach to this is through the principles of thermofluid engineering.
Thermofluid engineering is a multidisciplinary field combining thermodynamics, fluid mechanics, and heat transfer to solve complex engineering problems.
This discipline plays a vital role in designing electronics by providing methods to analyze and control the thermal environment.
Electronic components generate heat during operation, and without effective thermal management, this can lead to performance degradation and damage.
Therefore, it’s essential to have a strong understanding of thermofluid engineering to develop efficient thermal solutions.
The Basics of Thermofluid Engineering
To effectively apply thermofluid principles in electronics thermal design, it’s important to grasp some key concepts:
1. **Thermodynamics:** This area helps in understanding how heat is generated and transferred within electronic systems.
It provides a framework for analyzing energy conversions and thermal processes.
2. **Fluid Mechanics:** It deals with the behavior of fluids, including air and liquids, which are used in cooling systems.
Engineers utilize fluid mechanics to design effective cooling paths and systems, such as fans and liquid cooling.
3. **Heat Transfer:** This is the process by which heat moves from a hotter area to a cooler one.
Understanding conduction, convection, and radiation is crucial in determining how heat spreads in electronic equipment.
By mastering these principles, engineers can design systems that efficiently manage heat, ensuring the reliability and performance of electronic devices.
The Role of Model-Based Development
Model-based development (MBD) is an approach that uses mathematical and computational models to simulate, analyze, and design systems.
In the context of thermal design for electronic equipment, MBD offers numerous benefits.
Advantages of Model-Based Development
1. **Early Problem Detection:** By using models, engineers can simulate the behavior of an electronic system in various scenarios.
This allows them to spot potential thermal issues early in the design process and make necessary adjustments.
2. **Cost-Effectiveness:** Physical prototypes can be expensive and time-consuming to produce.
With MBD, many iterations and tests can be performed in a virtual environment, reducing the need for costly prototypes.
3. **Optimized Design:** Through simulations, engineers can explore different design options to find the most effective thermal management solutions.
This optimization can result in more efficient, compact, and cost-effective electronic systems.
4. **Enhanced Collaboration:** Model-based approaches enable seamless collaboration among different teams, such as mechanical, electrical, and software engineering, ensuring a cohesive design and development process.
Implementing Model-Based Development in Thermal Design
To effectively integrate MBD into thermal design, follow these practical steps:
1. **Develop Accurate Models:** Create detailed models that reflect the real-world behavior of the electronic system.
Use appropriate software tools and ensure that all thermal and fluid dynamic aspects are included.
2. **Run Simulations:** Conduct simulations to predict the thermal performance of the system under various conditions.
Analyze the data to identify heat concentration areas or inefficiencies.
3. **Iterate Designs:** Based on simulation results, modify the design to improve thermal performance.
Consider different cooling techniques, such as heat sinks, fans, or liquid cooling systems, to achieve optimal results.
4. **Validate with Prototypes:** Once a viable design is found, produce a physical prototype to validate the simulation results.
Test the prototype under actual operating conditions to ensure it meets the design criteria.
Practical Points for Effective Thermal Design
Developing a successful thermal design for electronic equipment requires both theoretical understanding and practical insights.
Here are some essential points to consider:
Material Selection
Choosing the right materials is vital.
Materials with high thermal conductivity, like copper and aluminum, are typically used for heat sinks to facilitate efficient heat dissipation.
Consider the trade-off between thermal performance and cost when selecting materials.
Component Layout
The arrangement of components on a circuit board can impact heat distribution.
Place high-heat-generating components evenly and consider their proximity to cooling elements.
Strategically positioning heat sources and sinks can enhance airflow and cooling effectiveness.
Active vs. Passive Cooling
Decide whether the system requires active cooling (fans, pumps) or passive cooling (heat sinks, natural convection).
Active cooling is more effective but consumes more power and can introduce noise, while passive cooling is quieter and requires less maintenance.
Thermal Interface Materials
These materials enhance heat transfer between components and their cooling solutions.
Using thermal pads or pastes with high thermal conductivity can significantly improve the efficiency of heat dissipation.
Regular Monitoring
Implement sensors and monitoring systems to track the temperature of critical components in real-time.
This data can provide valuable insights for preemptive maintenance and system optimization.
Conclusion
Thermal design is a critical factor in the development of reliable and efficient electronic devices.
By leveraging the fundamentals of thermofluid engineering and the innovative approach of model-based development, engineers can create systems that manage heat effectively.
Understanding the basics of thermofluid principles, such as thermodynamics, fluid mechanics, and heat transfer, is essential.
Coupled with model-based development’s ability to simulate and optimize designs, these principles provide a robust framework for solving thermal challenges.
Finally, practical considerations like material selection, component layout, and cooling strategies play a significant role in achieving a successful thermal design.
With these tools and practices, electronic equipment can operate efficiently while maintaining longevity and performance.
資料ダウンロード
QCD調達購買管理クラウド「newji」は、調達購買部門で必要なQCD管理全てを備えた、現場特化型兼クラウド型の今世紀最高の購買管理システムとなります。
ユーザー登録
調達購買業務の効率化だけでなく、システムを導入することで、コスト削減や製品・資材のステータス可視化のほか、属人化していた購買情報の共有化による内部不正防止や統制にも役立ちます。
NEWJI DX
製造業に特化したデジタルトランスフォーメーション(DX)の実現を目指す請負開発型のコンサルティングサービスです。AI、iPaaS、および先端の技術を駆使して、製造プロセスの効率化、業務効率化、チームワーク強化、コスト削減、品質向上を実現します。このサービスは、製造業の課題を深く理解し、それに対する最適なデジタルソリューションを提供することで、企業が持続的な成長とイノベーションを達成できるようサポートします。
オンライン講座
製造業、主に購買・調達部門にお勤めの方々に向けた情報を配信しております。
新任の方やベテランの方、管理職を対象とした幅広いコンテンツをご用意しております。
お問い合わせ
コストダウンが利益に直結する術だと理解していても、なかなか前に進めることができない状況。そんな時は、newjiのコストダウン自動化機能で大きく利益貢献しよう!
(Β版非公開)