- お役立ち記事
- Gain a Competitive Edge with Japanese Manufacturing Innovation
Gain a Competitive Edge with Japanese Manufacturing Innovation
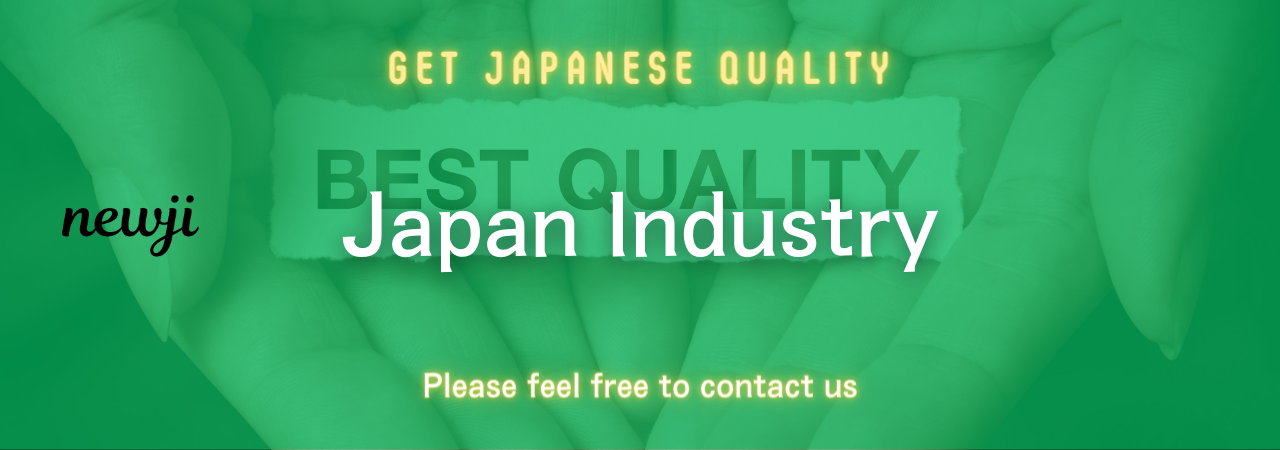
In the fast-paced world of manufacturing, gaining a competitive edge is all about innovation and efficiency. For decades, companies around the globe have looked to Japan for inspiration on how to revolutionize their manufacturing processes. From advanced technology to refined techniques, Japanese manufacturing innovation is revered for its precision, reliability, and creativity.
Understanding Japanese Manufacturing Innovation
The foundation of Japanese manufacturing excellence can be traced back to a few core principles: **Kaizen, Just-in-Time (JIT), Total Quality Management (TQM), and Lean Manufacturing**. These methodologies are intricately woven into the fabric of Japan’s industrial landscape and serve as the bedrock for its global manufacturing success.
– Kaizen: This concept focuses on continuous improvement. In Japanese, “Kaizen” translates to “change for the better.” It encourages all employees, from management to factory workers, to continually look for ways to improve their tasks. The idea is that small, incremental changes can lead to significant advancements over time.
– Just-in-Time (JIT): This inventory strategy is designed to increase efficiency and decrease waste by receiving goods only as they are needed in the production process. It allows for reduced inventory costs and minimizes the amount of capital tied up in raw materials and finished goods.
– Total Quality Management (TQM): TQM is a holistic approach to long-term success. By focusing on customer satisfaction, it integrates all quality-related functions and processes throughout the company. TQM’s primary elements include employee involvement, integrated business systems, and fact-based decision-making.
– Lean Manufacturing: Lean manufacturing aims to maximize productivity while minimizing waste within a manufacturing operation. By focusing on value creation and step-by-step elimination of processes that do not contribute to the final product, companies can streamline operations and reduce costs.
Pioneering Technologies and Techniques
Japanese manufacturers are known for adopting and pioneering advanced technologies, which provide a significant competitive advantage in the global market. Key technological innovations include the integration of Automation, Robotics, and Artificial Intelligence (AI) in production lines.
– Automation and Robotics: The utilization of automated machinery and robotics has transformed many Japanese factories into highly efficient and productive operations. Robots handle repetitive tasks with precision and speed, which reduces errors and increases output. Companies like **Fanuc and Yaskawa** lead the world in industrial automation, with robots that can work tirelessly and adapt to various manufacturing needs.
– Artificial Intelligence (AI): AI and machine learning are increasingly being used in Japanese manufacturing to predict maintenance needs, optimize supply chains, and improve quality control. AI-powered systems analyze vast amounts of data to detect patterns and anomalies, helping manufacturers make informed decisions quickly. This reduces downtime and ensures that production lines run smoothly.
Sustainable Manufacturing: A New Era of Innovation
As the world turns its focus toward sustainability, Japanese manufacturers are pioneering eco-friendly practices to reduce their environmental footprint. Sustainable manufacturing in Japan encompasses energy-efficient production processes, waste reduction, and the development of **recyclable and biodegradable materials.
– Energy Efficiency: Japanese companies invest heavily in energy-efficient equipment and technologies. For instance, Panasonic and Toyota have rolled out initiatives to lower energy consumption in their factories through the use of smart grids, renewable energy sources, and energy-efficient machinery.
– Zero Waste: The philosophy of Mottainai, which emphasizes the importance of reducing waste, is evident in Japanese manufacturing practices. Companies endeavor to find ways to repurpose or recycle everything from packaging materials to industrial by-products. This dedication to sustainability not only helps the environment but also reduces costs and improves profitability.
Collaboration and Knowledge Sharing
One of the most valuable aspects of Japanese manufacturing innovation is the spirit of collaboration and knowledge sharing. Japanese companies believe in the power of teamwork and often involve all employees in the innovation process. This inclusive approach fosters a culture where everyone feels responsible for the company’s success and encourages the free flow of ideas.
Furthermore, Japan often collaborates with international partners to drive innovation. By working with global experts, Japanese manufacturers gain access to new insights, technologies, and markets. Partnerships with companies such as Tesla and IBM enable the exchange of cutting-edge knowledge and expertise, further enhancing Japan’s competitive edge in manufacturing.
Real-World Applications and Success Stories
Many global giants have benefited from adopting Japanese manufacturing principles and technologies. Here are a few notable examples:
– Toyota: Renowned for its implementation of the Toyota Production System (TPS), which incorporates principles of JIT and Kaizen, Toyota has become a benchmark for manufacturing excellence. TPS has enabled Toyota to minimize waste, reduce costs, and improve quality, making it one of the most successful automobile manufacturers in the world.
– Sony: A leader in electronics, Sony has leveraged lean manufacturing and automation to streamline its production processes. By continually innovating and improving their manufacturing techniques, Sony has consistently delivered high-quality, cutting-edge products.
– Nissan: Another automotive giant, Nissan, has integrated advanced robotics and AI into its manufacturing plants. This has allowed the company to improve precision and efficiency while maintaining flexibility in its production lines.
Embracing Japanese Innovation: Key Takeaways
To embrace the principles of Japanese manufacturing innovation and gain a competitive edge, consider the following strategies:
1. Commit to Continuous Improvement: Encourage a culture of Kaizen in your organization. Small, incremental improvements can lead to significant gains over time.
2. Optimize Inventory Management: Implement JIT practices to reduce inventory costs and improve operational efficiency.
3. Focus on Quality: Adopt TQM practices to ensure customer satisfaction and integrate quality into every aspect of your business.
4. Eliminate Waste: Utilize lean manufacturing techniques to streamline operations and reduce waste.
5. Invest in Technology: Embrace automation, robotics, and AI to enhance productivity and precision in your manufacturing processes.
6. Prioritize Sustainability: Develop eco-friendly practices that reduce environmental impact and promote long-term sustainability.
By incorporating these principles and techniques, businesses can harness the power of Japanese manufacturing innovation to stay competitive in an ever-evolving global market.
資料ダウンロード
QCD調達購買管理クラウド「newji」は、調達購買部門で必要なQCD管理全てを備えた、現場特化型兼クラウド型の今世紀最高の購買管理システムとなります。
ユーザー登録
調達購買業務の効率化だけでなく、システムを導入することで、コスト削減や製品・資材のステータス可視化のほか、属人化していた購買情報の共有化による内部不正防止や統制にも役立ちます。
NEWJI DX
製造業に特化したデジタルトランスフォーメーション(DX)の実現を目指す請負開発型のコンサルティングサービスです。AI、iPaaS、および先端の技術を駆使して、製造プロセスの効率化、業務効率化、チームワーク強化、コスト削減、品質向上を実現します。このサービスは、製造業の課題を深く理解し、それに対する最適なデジタルソリューションを提供することで、企業が持続的な成長とイノベーションを達成できるようサポートします。
オンライン講座
製造業、主に購買・調達部門にお勤めの方々に向けた情報を配信しております。
新任の方やベテランの方、管理職を対象とした幅広いコンテンツをご用意しております。
お問い合わせ
コストダウンが利益に直結する術だと理解していても、なかなか前に進めることができない状況。そんな時は、newjiのコストダウン自動化機能で大きく利益貢献しよう!
(Β版非公開)