- お役立ち記事
- The basics of “experimental mode analysis” and its application to vibration testing, its know-how, and how to utilize it for vibration countermeasures.
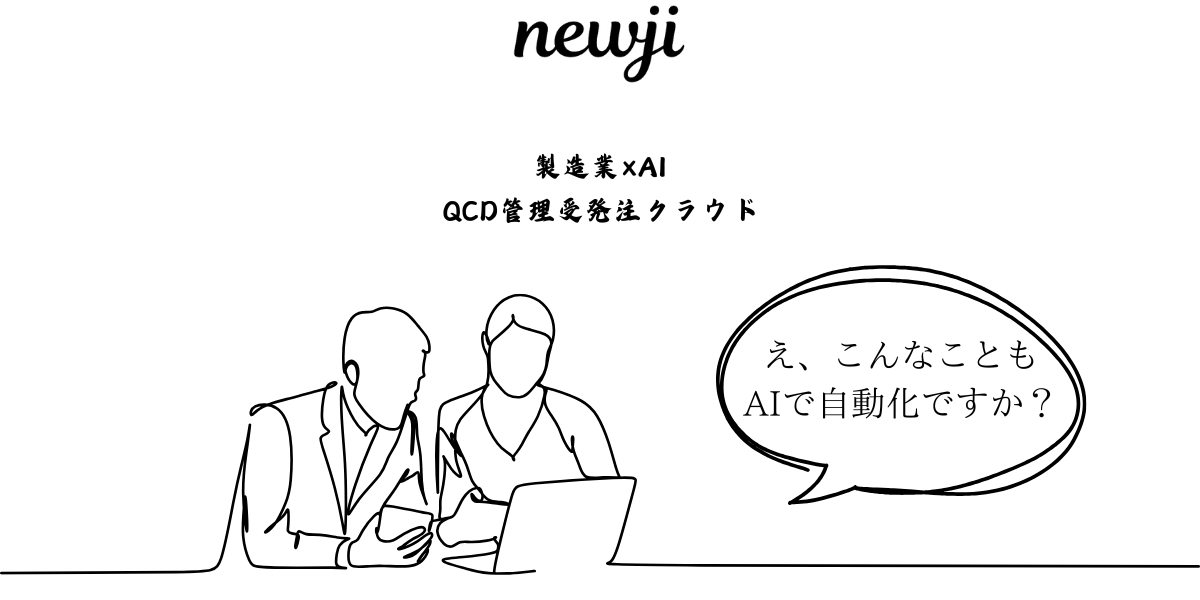
The basics of “experimental mode analysis” and its application to vibration testing, its know-how, and how to utilize it for vibration countermeasures.
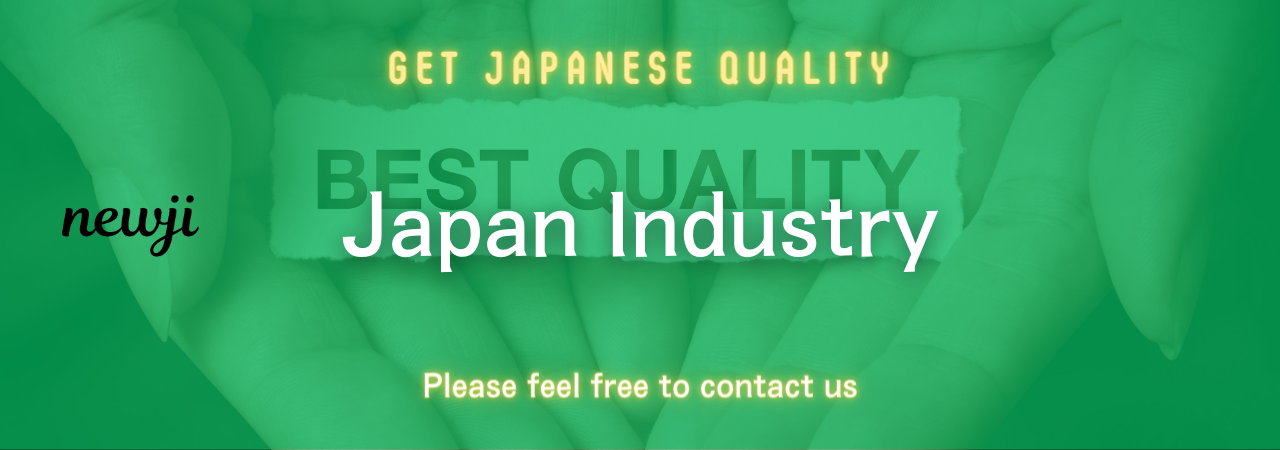
目次
Understanding Experimental Mode Analysis
Experimental mode analysis is a fundamental technique used in the study and evaluation of how mechanical structures respond to vibration and dynamic forces.
It helps identify natural frequencies, mode shapes, and damping ratios of structures, which are critical parameters for engineers and researchers.
These parameters are essential for assessing the structural integrity and dynamic performance of various objects, from small components to large bridges and buildings.
Mode analysis involves applying known forces to a structure and measuring its response using sensors.
These responses are then analyzed to extract modal parameters.
This information allows engineers to predict how a structure might behave under different conditions, facilitating improvements in design and enhancing safety.
Applications in Vibration Testing
Experimental mode analysis is crucial in the field of vibration testing.
By understanding how different components or structures respond to vibrations, researchers can create models that predict their performance under real-world conditions.
This is particularly important in industries such as automotive, aerospace, and manufacturing, where vibration can cause fatigue, noise, or even failure.
In the automotive industry, for example, ensuring the comfort and safety of passengers often relies on minimizing the effects of vibration.
Experimental mode analysis allows engineers to identify which parts of a vehicle are susceptible to vibration and modify them to reduce noise levels or prevent damage.
Meanwhile, in aerospace, structures such as aircraft wings or satellite components are analyzed to ensure they can withstand the stresses encountered during flight or in space.
Steps in Experimental Mode Analysis
Conducting experimental mode analysis involves several key steps:
1. **Setting up the experiment:** The first stage involves preparing the test setup, which includes attaching sensors to the structure, ensuring that the testing environment reflects realistic conditions and selecting the appropriate excitation method. Common excitation methods in modal analysis include impact hammers and shakers.
2. **Data acquisition:** During this phase, the structure is subjected to controlled vibrations or impacts. The attached sensors, typically accelerometers or strain gauges, measure the structure’s response in terms of acceleration, velocity, or displacement.
3. **Signal processing:** The raw data collected during testing is processed to remove any noise or interference. Various techniques, such as Fourier transform and filtering, are commonly used to ensure the clarity and accuracy of the data.
4. **Modal parameter extraction:** This crucial step involves using the processed data to identify the modal parameters of the structure. Modal analysis software often assists in extracting natural frequencies, mode shapes, and damping ratios.
5. **Validation and interpretation:** The final stage is about interpreting the results to ensure they make sense in the context of the intended application. Model validation is often performed by comparing the experimental results with theoretical predictions or simulation data.
Know-How in Experimental Mode Analysis
Gaining proficiency in experimental mode analysis requires a combination of technical knowledge, practical skills, and familiarity with analytical tools.
A strong understanding of dynamics and vibration theory is foundational, as this guides the interpretation of experimental results.
Additionally, familiarity with different testing equipment and data processing software is crucial.
Practically, being able to set up experiments properly is critical.
This includes knowing how to position sensors effectively, calibrate equipment, and select suitable excitation methods.
The precision of measurements can significantly impact the accuracy of the modal parameters obtained, so attention to detail is paramount.
Moreover, interpreting the data requires not only technical skill but also creativity and experience.
Experienced engineers are adept at recognizing patterns, identifying anomalies, and considering possible explanations for unexpected results.
Continuous practice and learning are essential for refining these skills over time.
Utilizing Experimental Mode Analysis for Vibration Countermeasures
Once the modal parameters of a structure are known, this information can be leveraged to design effective vibration countermeasures.
One common approach is structural modification, which involves redesigning or altering parts of the structure to change its dynamic properties.
By doing so, engineers can shift a structure’s natural frequencies away from those that are excited by external forces, thereby reducing resonance and the potential for vibration-related issues.
Another strategy is the use of damping treatments, such as adding dampers or viscoelastic materials, which absorb and dissipate vibrational energy.
This is particularly useful for applications where redesigning the structure is impractical or where adding mass and stiffness can have adverse effects.
Experimental mode analysis also supports the development of active vibration control systems, which use sensors and actuators to counteract vibrations in real-time.
Though complex, these systems are increasingly used in high-precision industries to maintain structural stability and performance.
Conclusion
Experimental mode analysis is an indispensable tool for understanding and managing the dynamics of various structures.
Its insights are not only invaluable to researchers and engineers striving to improve safety and performance, but also to industries seeking to innovate while ensuring quality and reliability.
By mastering the techniques and applications of experimental mode analysis, professionals can contribute significantly to the advancement of technology and the optimization of mechanical systems.
As industries continue to expand, the importance of this analysis in maintaining and enhancing structural integrity is expected to grow.
資料ダウンロード
QCD調達購買管理クラウド「newji」は、調達購買部門で必要なQCD管理全てを備えた、現場特化型兼クラウド型の今世紀最高の購買管理システムとなります。
ユーザー登録
調達購買業務の効率化だけでなく、システムを導入することで、コスト削減や製品・資材のステータス可視化のほか、属人化していた購買情報の共有化による内部不正防止や統制にも役立ちます。
NEWJI DX
製造業に特化したデジタルトランスフォーメーション(DX)の実現を目指す請負開発型のコンサルティングサービスです。AI、iPaaS、および先端の技術を駆使して、製造プロセスの効率化、業務効率化、チームワーク強化、コスト削減、品質向上を実現します。このサービスは、製造業の課題を深く理解し、それに対する最適なデジタルソリューションを提供することで、企業が持続的な成長とイノベーションを達成できるようサポートします。
オンライン講座
製造業、主に購買・調達部門にお勤めの方々に向けた情報を配信しております。
新任の方やベテランの方、管理職を対象とした幅広いコンテンツをご用意しております。
お問い合わせ
コストダウンが利益に直結する術だと理解していても、なかなか前に進めることができない状況。そんな時は、newjiのコストダウン自動化機能で大きく利益貢献しよう!
(Β版非公開)