- お役立ち記事
- Mechanism of metal corrosion, anti-corrosion technology, and application to prevent corrosion problems
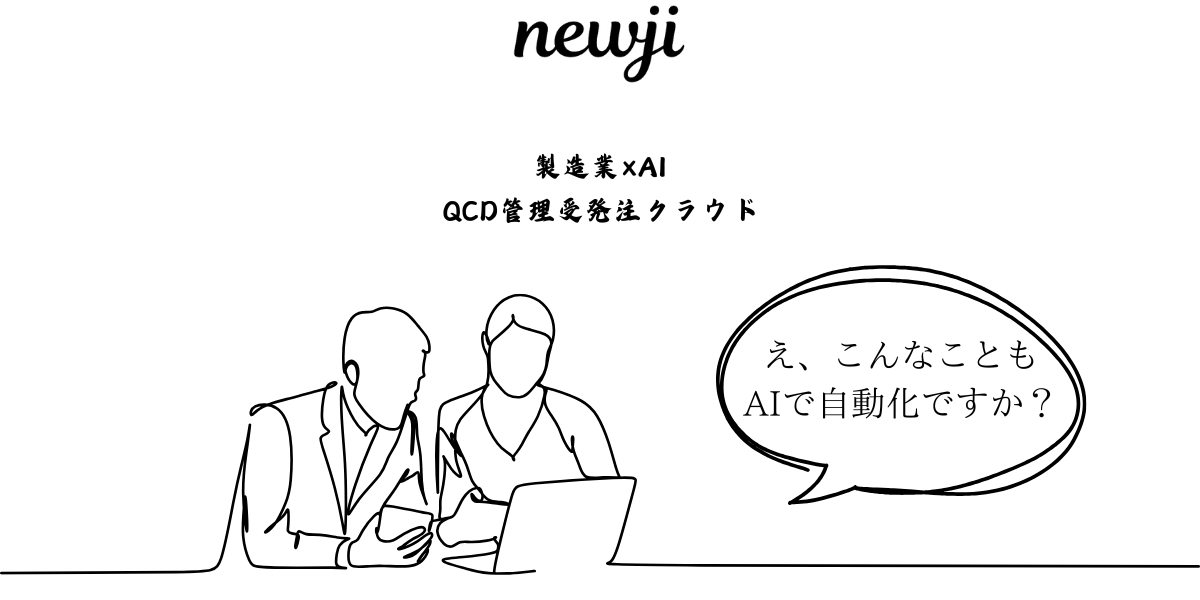
Mechanism of metal corrosion, anti-corrosion technology, and application to prevent corrosion problems
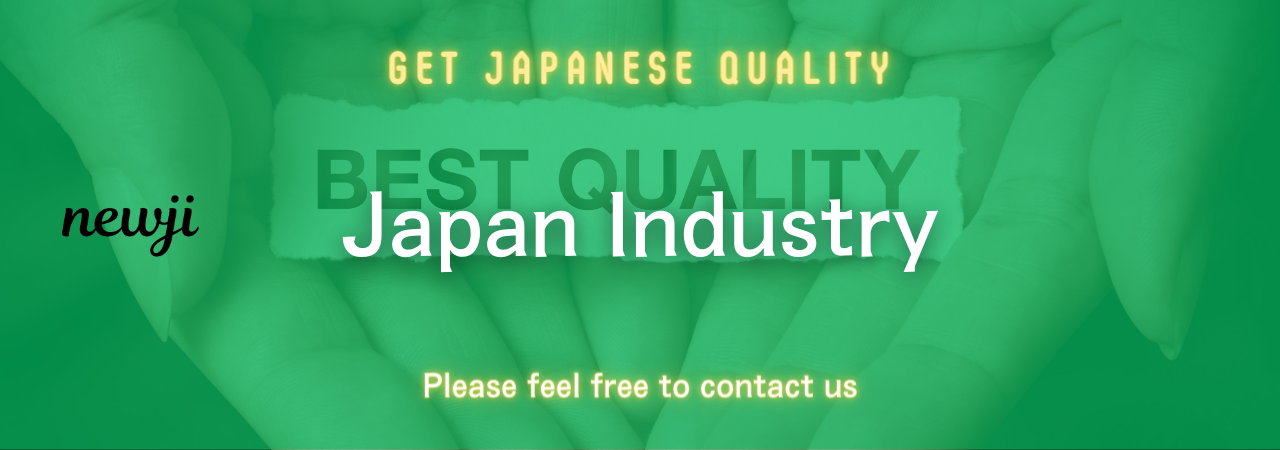
目次
Understanding Metal Corrosion
Metal corrosion is a natural process that gradually deteriorates metal objects when exposed to environmental elements like moisture, oxygen, and chemicals.
This occurs because metals tend to react with these surroundings, leading to the formation of compounds such as oxides or sulfides.
The most familiar example of corrosion is rust, which forms when iron or steel reacts with oxygen in the presence of water.
Corrosion can affect almost any material, with varying degrees of severity.
The rate at which corrosion occurs depends on several factors including the type of metal, environmental conditions, and the presence of corrosive agents.
Understanding the basics of corrosion is crucial to preventing it, especially in industries where metal integrity is vital.
The Corrosion Process
Corrosion begins at the atomic level, where metal atoms lose electrons and form positively charged ions.
This process, known as oxidation, is the first stage of corrosion.
In an aqueous environment, the electrons lost by the metal atoms are usually acquired by oxygen molecules, which further combines with hydrogen ions in the presence of water, leading to the formation of hydroxide ions.
The result is a redox reaction, which forms compounds like rust on iron.
For metals like aluminum, the oxidation results in a thin oxide layer that adheres strongly to the surface, offering a degree of protection against further corrosion.
However, not all metals form protective oxide layers, making some more prone to severe corrosion.
Types of Corrosion
Corrosion manifests in various forms, each with distinct characteristics and implications.
1. **Uniform Corrosion**: A common type, where the metal surface corrodes at a consistent rate, leading to a uniform loss of material.
2. **Galvanic Corrosion**: Occurs when two dissimilar metals are electrically connected in a corrosive electrolyte, causing the more reactive metal to corrode faster than usual.
3. **Pitting Corrosion**: A localized form that creates small pits or holes in the metal, often associated with passive metals like stainless steel.
4. **Crevice Corrosion**: Takes place in confined spaces where stagnant water or moisture becomes trapped, leading to accelerated corrosion.
5. **Stress Corrosion Cracking (SCC)**: Happens when tensile stress and a corrosive environment combine, leading to failure in a metal component.
Recognizing these types of corrosion can aid in implementing appropriate prevention and mitigation strategies.
Anti-Corrosion Technologies
To tackle corrosion, industries employ various anti-corrosion technologies aimed at extending the lifespan of metal structures and components.
These methods range from material selection to advanced surface treatments.
Protective Coatings
Applying protective coatings is a widely used method to shield metal surfaces from corrosive elements.
Coatings serve as a barrier, preventing moisture, oxygen, and other corrosive agents from reaching the metal surface.
Types of protective coatings include:
– **Paints and Protective Films**: These are applied directly onto metal surfaces to create a barrier.
They often include chemical inhibitors that slow down the corrosion process.
– **Galvanization**: This involves coating the metal with a layer of zinc, which sacrifices itself to protect the underlying material.
Zinc has the advantage of corroding more slowly than iron, providing long-term protection.
– **Electroplating**: Applying a thin layer of another metal, like nickel or chrome, to enhance corrosion resistance and improve surface aesthetics.
Corrosion Inhibitors
These are chemicals that, when added to a corrosive environment, significantly reduce the corrosion rate.
Corrosion inhibitors work by forming a passive film on the metal’s surface or interfering with the electrochemical reactions responsible for corrosion.
Industries that benefit from inhibitors include oil and gas, where they are used in pipelines and refinery equipment, and automotive manufacturers who use them in cooling systems.
Cathodic Protection
Cathodic protection is a technique to control the corrosion of a metal surface by making it the cathode within an electrochemical cell.
This is achieved by attaching a more reactive metal that acts as the anode.
– **Sacrificial Anode Protection**: In this approach, a metal like magnesium, zinc, or aluminum is used as the sacrificial metal, which corrodes instead of the protected metal.
– **Impressed Current Cathodic Protection (ICCP)**: Involves using an external power source to supply current and shift metal ion formation processes away from the protected structure.
Applications of Anti-Corrosion Methods
Anti-corrosion technologies find significant applications across various industries to enhance metal durability and performance.
Construction Industry
In construction, corrosion-resistant materials are crucial for structural safety and longevity.
Steel structures, bridges, and pipelines often employ protective coatings and galvanization to prolong service life and prevent structural failures.
Automotive Industry
Automobiles experience constant exposure to moisture and road salts, making them prone to corrosion.
Manufacturers utilize paint coatings, sealants, and corrosion inhibitors in engine components to enhance durability.
Marine Industry
Saltwater is extremely corrosive to metals, posing serious challenges in the marine industry.
Shipbuilding employs a variety of techniques like cathodic protection and specialized marine coatings to protect vessels from external and internal corrosion damage.
Oil and Gas Industry
This industry deals with corrosive elements such as hydrogen sulfide and water, necessitating robust anti-corrosion measures to prevent pipeline leaks and enhance operational safety.
Preventing Corrosion Problems
Effective corrosion prevention is a blend of understanding the environment, choosing appropriate materials, and employing a combination of anti-corrosion techniques.
Regular inspection and maintenance are vital to detect early signs of corrosion and take corrective actions.
Educating personnel on corrosion prevention methods and investing in research for innovative solutions also contribute to minimizing corrosion-related issues.
By employing a comprehensive approach to corrosion management, industries can ensure the longevity and reliability of metal components, ultimately leading to cost savings and improved safety.
資料ダウンロード
QCD調達購買管理クラウド「newji」は、調達購買部門で必要なQCD管理全てを備えた、現場特化型兼クラウド型の今世紀最高の購買管理システムとなります。
ユーザー登録
調達購買業務の効率化だけでなく、システムを導入することで、コスト削減や製品・資材のステータス可視化のほか、属人化していた購買情報の共有化による内部不正防止や統制にも役立ちます。
NEWJI DX
製造業に特化したデジタルトランスフォーメーション(DX)の実現を目指す請負開発型のコンサルティングサービスです。AI、iPaaS、および先端の技術を駆使して、製造プロセスの効率化、業務効率化、チームワーク強化、コスト削減、品質向上を実現します。このサービスは、製造業の課題を深く理解し、それに対する最適なデジタルソリューションを提供することで、企業が持続的な成長とイノベーションを達成できるようサポートします。
オンライン講座
製造業、主に購買・調達部門にお勤めの方々に向けた情報を配信しております。
新任の方やベテランの方、管理職を対象とした幅広いコンテンツをご用意しております。
お問い合わせ
コストダウンが利益に直結する術だと理解していても、なかなか前に進めることができない状況。そんな時は、newjiのコストダウン自動化機能で大きく利益貢献しよう!
(Β版非公開)