- お役立ち記事
- Revolutionizing Precision: Inside Japanese Manufacturing Excellence
Revolutionizing Precision: Inside Japanese Manufacturing Excellence
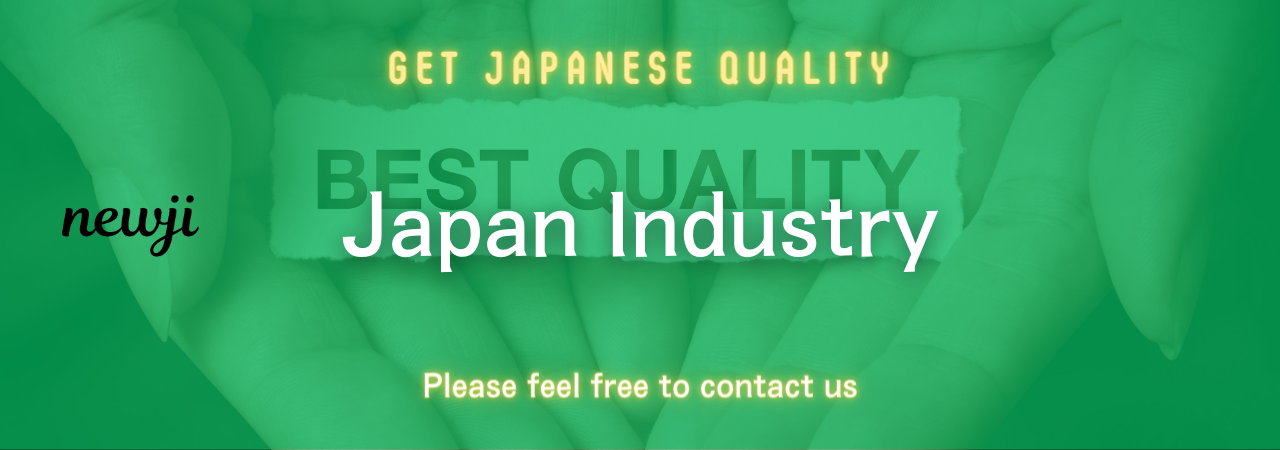
目次
Introduction to Japanese Manufacturing Excellence
Japanese manufacturing has long been synonymous with precision, quality, and innovation. From automotive giants like Toyota and Honda to electronics leaders such as Sony and Panasonic, Japanese companies have consistently set global standards. This excellence is not merely a result of advanced technology but is deeply rooted in the country’s culture, management philosophies, and operational practices. Understanding the intricacies of Japanese manufacturing can offer invaluable insights for international procurement and purchasing professionals aiming to collaborate with or emulate these industry leaders.
The Foundation of Japanese Manufacturing Excellence
Kaizen: Continuous Improvement
At the heart of Japanese manufacturing lies the principle of Kaizen, which translates to “continuous improvement.” This philosophy encourages every employee, from the assembly line worker to the executive, to seek ways to enhance processes, reduce waste, and increase efficiency. By fostering a culture where improvement is a perpetual goal, Japanese companies maintain their competitive edge and adaptability in a rapidly changing global market.
Just-In-Time (JIT) Production
Just-In-Time production is another cornerstone of Japanese manufacturing. Developed by Toyota, JIT aims to reduce inventory costs by ensuring that materials arrive precisely when needed in the production process. This approach minimizes waste, lowers storage costs, and enhances flexibility, allowing companies to respond swiftly to market demand fluctuations. For procurement and purchasing professionals, understanding JIT is crucial for coordinating timely deliveries and maintaining seamless supply chains.
Lean Manufacturing
Lean Manufacturing complements Kaizen and JIT by focusing on maximizing value while minimizing waste. This methodology involves streamlining processes, eliminating non-value-added activities, and optimizing resource utilization. The lean approach not only improves efficiency but also enhances product quality and customer satisfaction. Implementing lean principles requires a deep understanding of production workflows and a commitment to continuous optimization.
Procurement and Purchasing in Japanese Manufacturing
Strategic Supplier Partnerships
Japanese companies often view suppliers as strategic partners rather than mere vendors. This perspective fosters long-term relationships built on trust, mutual respect, and shared goals. In procurement and purchasing, this means collaborating closely with suppliers to ensure quality, timely delivery, and continuous improvement. By investing in these partnerships, Japanese manufacturers can achieve greater consistency and reliability in their supply chains.
Supplier Integration and Collaboration
Integration with suppliers goes beyond transactional relationships. Japanese manufacturers frequently involve suppliers early in the product development process, encouraging collaborative problem-solving and innovation. This integration ensures that suppliers are aligned with the company’s quality standards and can contribute to the design and improvement of components. For procurement and purchasing professionals, effective supplier integration requires robust communication channels and collaborative tools.
Emphasis on Quality Control
Quality control is paramount in Japanese manufacturing. Rigorous testing, inspection, and quality assurance processes are embedded at every stage of production. Suppliers are expected to adhere to strict quality standards, with continuous monitoring and feedback mechanisms in place. This emphasis on quality ensures that end products meet or exceed customer expectations, reinforcing the reputation of Japanese manufacturers for excellence.
Advantages of Partnering with Japanese Suppliers
High-Quality Standards
Japanese suppliers are renowned for their stringent quality control measures. Partnering with such suppliers ensures that the components or materials received meet high-quality standards, reducing the likelihood of defects and enhancing the overall product quality. This reliability is particularly crucial in industries where precision and durability are essential.
Advanced Technological Capabilities
Japanese manufacturers are at the forefront of technological innovation. Their suppliers often leverage cutting-edge technologies and advanced manufacturing techniques, providing access to the latest advancements in production. This technological prowess can lead to improved product performance, increased efficiency, and innovative features that set products apart in the marketplace.
Strong Supply Chain Management
Efficient supply chain management is a hallmark of Japanese manufacturing. Their suppliers excel in managing logistics, inventory, and delivery schedules, ensuring seamless operations and timely availability of materials. This reliability minimizes production delays and supports the smooth functioning of manufacturing processes.
Cultural Commitment to Excellence
The Japanese work ethic and cultural commitment to excellence drive suppliers to maintain high performance standards. This dedication manifests in meticulous attention to detail, proactive problem-solving, and a relentless pursuit of improvement, all of which contribute to superior product outcomes.
Challenges and Considerations
Communication Barriers
Language and cultural differences can pose significant challenges when working with Japanese suppliers. Misunderstandings may arise from nuances in communication styles, business etiquettes, and expectations. Effective communication strategies, including the use of bilingual staff or professional translators, are essential to bridge these gaps and ensure clear, efficient interactions.
Higher Costs
Japanese suppliers may command higher prices due to their emphasis on quality and advanced technologies. While the initial costs might be higher compared to suppliers from other regions, the long-term benefits of superior quality, reliability, and reduced defect rates can offset these expenses. Procurement professionals must conduct thorough cost-benefit analyses to determine the overall value.
Rigid Contract Terms
Japanese business culture often emphasizes stability and predictability, which can lead to rigid contract terms. Flexibility in negotiating terms and adapting to changing circumstances may be limited. Understanding and respecting these business practices is crucial for establishing successful and lasting partnerships.
Lead Times
The precision and thoroughness inherent in Japanese manufacturing processes can sometimes result in longer lead times. While the quality and reliability of deliveries are generally high, procurement and purchasing departments must plan for these lead times to ensure that production schedules remain on track.
Supplier Negotiation Techniques
Building Trust and Relationships
In Japanese business culture, establishing trust and strong relationships is essential before engaging in substantive negotiations. Investing time in getting to know suppliers, understanding their values, and demonstrating commitment to a long-term partnership can facilitate more effective negotiations and mutually beneficial agreements.
Understanding Cultural Norms
Being aware of and respecting Japanese cultural norms can significantly impact negotiation outcomes. Formality, humility, and consensus-building are key aspects of Japanese business interactions. Adopting a respectful demeanor, being patient, and avoiding confrontational tactics can foster a more collaborative negotiation environment.
Emphasizing Mutual Benefits
Japanese negotiations often seek win-win outcomes where both parties benefit. Highlighting how proposed terms or agreements can provide value to both the buyer and the supplier can create a more cooperative atmosphere. Focusing on shared goals and long-term benefits rather than short-term gains aligns with Japanese business practices.
Preparation and Detailed Planning
Thorough preparation is crucial for successful negotiations. This includes understanding the supplier’s business, market position, and potential constraints. Presenting well-researched proposals, backed by data and clear rationale, demonstrates professionalism and increases the likelihood of favorable negotiation outcomes.
Patience and Persistence
Negotiations with Japanese suppliers may require more time compared to counterparts from other regions. Demonstrating patience and persistence, while maintaining consistent communication, can build trust and lead to more sustainable agreements. Avoiding rushed decisions and allowing negotiations to unfold organically is often more effective.
Market Conditions Impacting Japanese Manufacturing
Global Supply Chain Dynamics
Global supply chain disruptions, such as those caused by geopolitical tensions, natural disasters, or pandemics, can significantly impact Japanese manufacturing. Suppliers may face challenges in sourcing raw materials, managing logistics, or meeting production deadlines. Understanding these dynamics is essential for procurement professionals to develop contingency plans and maintain supply chain resilience.
Technological Advancements
Rapid technological advancements continue to shape Japanese manufacturing. The rise of automation, Industry 4.0, and smart manufacturing requires suppliers to continuously innovate and adapt. Staying abreast of these trends and incorporating relevant technologies can enhance procurement strategies and ensure alignment with industry standards.
Economic Factors
Economic conditions, such as exchange rates, inflation, and economic growth rates, influence Japanese manufacturing. Fluctuations in the Japanese yen can affect pricing, competitiveness, and profitability. Procurement and purchasing professionals must monitor economic indicators and consider their impact on sourcing decisions and cost structures.
Sustainability and Environmental Regulations
Increasing emphasis on sustainability and stringent environmental regulations are shaping Japanese manufacturing practices. Suppliers are expected to adopt eco-friendly processes, reduce carbon footprints, and comply with regulatory standards. Integrating sustainability criteria into procurement strategies ensures alignment with global environmental goals and enhances corporate responsibility.
Best Practices for International Procurement
Comprehensive Supplier Evaluation
Conducting thorough evaluations of potential Japanese suppliers is critical. This includes assessing their financial stability, quality management systems, production capabilities, and compliance with industry standards. Site visits, audits, and reference checks can provide valuable insights into a supplier’s reliability and performance.
Clear and Transparent Communication
Maintaining clear and transparent communication is essential for effective procurement and purchasing. This involves setting clear expectations, providing detailed specifications, and maintaining open channels for feedback and issue resolution. Utilizing collaborative tools and regular meetings can facilitate ongoing communication and prevent misunderstandings.
Integration of Technology
Leveraging technology can enhance procurement efficiency and accuracy. Implementing procurement software, supply chain management systems, and data analytics can streamline processes, improve visibility, and support informed decision-making. Embracing digital tools aligns with the technological advancements prevalent in Japanese manufacturing.
Risk Management and Contingency Planning
Developing robust risk management strategies is crucial to mitigate potential disruptions in the supply chain. This includes identifying potential risks, evaluating their impact, and establishing contingency plans. Diversifying suppliers, maintaining safety stocks, and monitoring supplier performance can enhance supply chain resilience.
Continuous Performance Monitoring
Regularly monitoring supplier performance ensures that quality standards and delivery schedules are consistently met. Key performance indicators (KPIs) such as defect rates, on-time delivery, and responsiveness should be tracked and reviewed. Providing feedback and engaging in continuous improvement initiatives can drive mutual growth and performance enhancement.
Cultural Sensitivity and Adaptation
Demonstrating cultural sensitivity and adapting to Japanese business practices can strengthen supplier relationships. Understanding and respecting cultural nuances, business etiquettes, and communication styles fosters trust and collaboration. Training procurement teams on cultural awareness can enhance interactions and negotiation outcomes.
Case Studies: Success Stories in Japanese Manufacturing
Toyota’s Supplier Integration
Toyota’s success is often attributed to its deep integration with suppliers through the Toyota Production System (TPS). By involving suppliers in the product development process and fostering a culture of continuous improvement, Toyota has achieved unparalleled efficiency and quality. This approach has enabled the company to maintain its leadership position in the automotive industry.
Panasonic’s Quality Excellence
Panasonic exemplifies quality excellence through its rigorous quality control measures and strong supplier partnerships. By implementing comprehensive testing and inspection protocols, Panasonic ensures that its products meet the highest standards. This commitment to quality has solidified Panasonic’s reputation as a trusted electronics manufacturer globally.
Sony’s Innovation through Collaboration
Sony’s innovative edge is driven by its collaborative relationships with suppliers. By encouraging joint research and development initiatives, Sony leverages supplier expertise to drive technological advancements. This collaborative approach has resulted in groundbreaking products and sustained Sony’s position as a leader in the electronics market.
Future Trends in Japanese Manufacturing
Industry 4.0 and Smart Manufacturing
The integration of Industry 4.0 technologies, such as the Internet of Things (IoT), artificial intelligence (AI), and robotics, is transforming Japanese manufacturing. Smart factories equipped with interconnected systems enable real-time monitoring, predictive maintenance, and enhanced automation. These advancements improve operational efficiency, reduce downtime, and support scalable production processes.
Sustainability and Green Manufacturing
Sustainability continues to be a major focus in Japanese manufacturing. Companies are investing in green technologies, renewable energy sources, and sustainable materials. Green manufacturing practices not only reduce environmental impact but also appeal to environmentally conscious consumers. Procurement and purchasing strategies will increasingly incorporate sustainability criteria to align with global environmental standards.
Reshoring and Localized Production
In response to global supply chain disruptions and geopolitical uncertainties, some Japanese manufacturers are reshoring production or increasing localized manufacturing efforts. This trend enhances supply chain resilience, reduces dependency on distant suppliers, and improves responsiveness to market demands. Procurement professionals may need to adjust sourcing strategies to accommodate more localized suppliers.
Emphasis on Customization and Flexibility
Japanese manufacturing is shifting towards greater customization and flexibility to meet diverse consumer demands. This trend involves adopting agile manufacturing practices, enabling rapid adjustments to production lines, and offering personalized products. Procurement strategies will need to support this flexibility by sourcing versatile materials and collaborating with adaptable suppliers.
Conclusion: Leveraging Japanese Manufacturing Excellence
Japanese manufacturing excellence offers a wealth of lessons for international procurement and purchasing professionals. By embracing principles such as continuous improvement, lean manufacturing, and strategic supplier partnerships, organizations can enhance their operational efficiency, product quality, and competitive advantage. While challenges like communication barriers and higher costs exist, the long-term benefits of collaborating with Japanese suppliers—such as reliability, technological innovation, and cultural commitment to excellence—are substantial.
To successfully leverage Japanese manufacturing excellence, procurement strategies must prioritize comprehensive supplier evaluations, clear and transparent communication, and the integration of advanced technologies. Additionally, fostering cultural sensitivity and adapting to Japanese business practices are essential for building strong, enduring partnerships.
As the global manufacturing landscape continues to evolve, Japanese companies are poised to lead with their innovative approaches and unwavering dedication to quality and precision. By understanding and applying the best practices from Japanese manufacturing, international businesses can revolutionize their own operations, achieve greater precision, and sustain success in an increasingly competitive global market.
資料ダウンロード
QCD調達購買管理クラウド「newji」は、調達購買部門で必要なQCD管理全てを備えた、現場特化型兼クラウド型の今世紀最高の購買管理システムとなります。
ユーザー登録
調達購買業務の効率化だけでなく、システムを導入することで、コスト削減や製品・資材のステータス可視化のほか、属人化していた購買情報の共有化による内部不正防止や統制にも役立ちます。
NEWJI DX
製造業に特化したデジタルトランスフォーメーション(DX)の実現を目指す請負開発型のコンサルティングサービスです。AI、iPaaS、および先端の技術を駆使して、製造プロセスの効率化、業務効率化、チームワーク強化、コスト削減、品質向上を実現します。このサービスは、製造業の課題を深く理解し、それに対する最適なデジタルソリューションを提供することで、企業が持続的な成長とイノベーションを達成できるようサポートします。
オンライン講座
製造業、主に購買・調達部門にお勤めの方々に向けた情報を配信しております。
新任の方やベテランの方、管理職を対象とした幅広いコンテンツをご用意しております。
お問い合わせ
コストダウンが利益に直結する術だと理解していても、なかなか前に進めることができない状況。そんな時は、newjiのコストダウン自動化機能で大きく利益貢献しよう!
(Β版非公開)