- お役立ち記事
- Factory cost reduction methods using IoT and points for improvement
Factory cost reduction methods using IoT and points for improvement
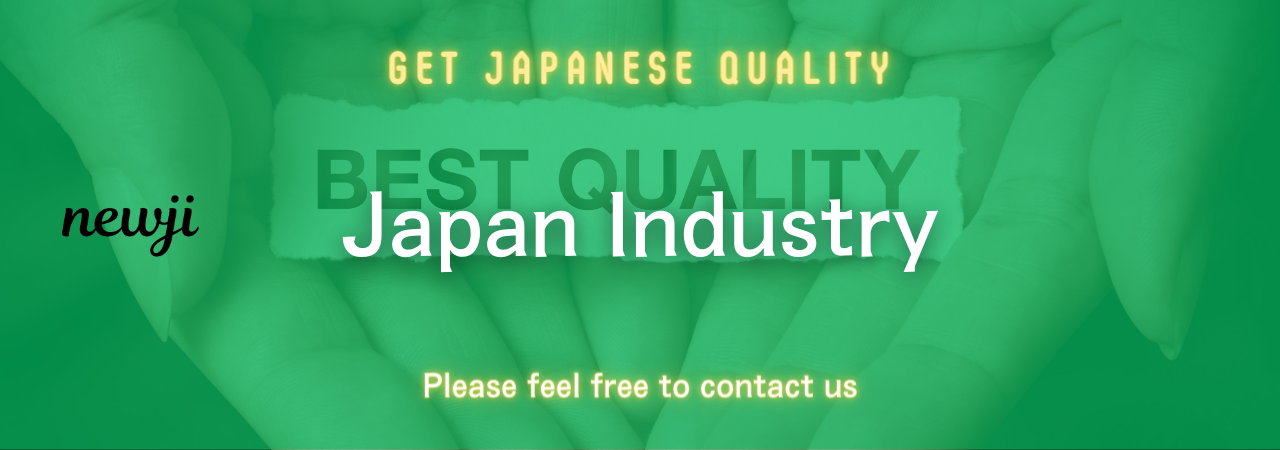
目次
Understanding IoT in Manufacturing
The Internet of Things (IoT) is transforming the manufacturing industry by integrating advanced technology into factory operations.
IoT involves connecting devices and machinery to the internet, allowing them to communicate and share data with each other.
This connectivity leads to more efficient processes, enhanced productivity, and ultimately, cost reductions.
Manufacturers implement IoT in various ways, such as installing sensors on equipment to monitor performance and detect issues in real-time.
These sensors collect data, which is then analyzed to improve decision-making, optimize workflows, and prevent costly downtimes.
Benefits of IoT in Reducing Factory Costs
Implementing IoT in manufacturing can drastically reduce costs in several ways.
First, it enhances predictive maintenance capabilities.
By predicting equipment failures before they occur, companies can avoid unexpected breakdowns, extend machinery lifespan, and reduce repair costs.
Additionally, IoT helps in optimizing energy consumption.
Smart sensors adjust power usage based on production needs, which reduces waste and cuts down on utility bills.
Efficient energy management contributes to a sustainable operation that saves money over time.
Furthermore, IoT streamlines supply chain management.
By tracking inventory levels and shipment timelines accurately, manufacturers can minimize holding costs and reduce excess inventory.
This level of oversight ensures that resources are used effectively, leading to cost savings.
Improving Operational Efficiency
IoT technology plays a crucial role in improving the overall efficiency of a manufacturing plant.
With real-time data collection, manufacturers gain insights into every aspect of their operations.
They can identify bottlenecks in the production line, evaluate worker performance, and allocate resources more effectively.
Real-time monitoring enables quicker response times to issues that arise during production.
When problems are addressed promptly, it minimizes downtime and keeps the workflow smooth.
As a result, factories operate more efficiently, produce higher-quality products, and enhance their competitiveness in the market.
Enhanced Quality Control
Quality control is vital in manufacturing to ensure consistent and defect-free products.
IoT helps improve quality control processes by providing accurate data throughout production.
Sensors can detect deviations from quality standards immediately, allowing for quick adjustments.
With this technology, manufacturers can reduce waste resulting from defective products.
Less waste means reduced material costs and fewer resources spent on rework, contributing to overall cost reduction.
Challenges in Implementing IoT
While IoT offers numerous advantages, implementing it in a manufacturing setting is not without challenges.
One primary concern is the initial investment required for IoT infrastructure.
Devices, sensors, and connectivity solutions can be expensive, and businesses may face budget constraints.
There is also a need for skilled personnel to manage and interpret IoT data.
Training staff or hiring new experts can be costly and time-consuming.
Moreover, ensuring data security is critical as IoT systems are vulnerable to cyber threats.
Manufacturers must carefully plan the integration of IoT, considering both costs and benefits, to ensure a successful and secure implementation.
Points for Improvement
To maximize the benefits of IoT, factories must focus on continuous improvement strategies.
One area to improve is data analytics.
Investing in advanced analytics tools helps convert raw data into actionable insights, enhancing decision-making processes.
Regular evaluation of IoT systems is also crucial.
By conducting periodic reviews, manufacturers can identify opportunities for upgrades and adjustments.
Staying updated with the latest technological advancements ensures that the factory remains competitive.
Lastly, addressing cybersecurity measures proactively is vital.
Implementing strict security protocols protects sensitive data and prevents unauthorized access, ensuring safe and reliable operations.
Conclusion
The integration of IoT in manufacturing processes offers substantial opportunities for cost reduction and operational efficiency.
By embracing this technology, factories can improve predictive maintenance, optimize energy use, streamline supply chain management, and enhance quality control.
Though challenges exist, focusing on continuous improvement and leveraging advanced analytics can lead to significant benefits.
IoT is revolutionizing how factories operate, and understanding how to utilize it effectively is essential.
By doing so, manufacturers can stay competitive, reduce costs, and ensure long-term success in the ever-evolving industrial landscape.
資料ダウンロード
QCD調達購買管理クラウド「newji」は、調達購買部門で必要なQCD管理全てを備えた、現場特化型兼クラウド型の今世紀最高の購買管理システムとなります。
ユーザー登録
調達購買業務の効率化だけでなく、システムを導入することで、コスト削減や製品・資材のステータス可視化のほか、属人化していた購買情報の共有化による内部不正防止や統制にも役立ちます。
NEWJI DX
製造業に特化したデジタルトランスフォーメーション(DX)の実現を目指す請負開発型のコンサルティングサービスです。AI、iPaaS、および先端の技術を駆使して、製造プロセスの効率化、業務効率化、チームワーク強化、コスト削減、品質向上を実現します。このサービスは、製造業の課題を深く理解し、それに対する最適なデジタルソリューションを提供することで、企業が持続的な成長とイノベーションを達成できるようサポートします。
オンライン講座
製造業、主に購買・調達部門にお勤めの方々に向けた情報を配信しております。
新任の方やベテランの方、管理職を対象とした幅広いコンテンツをご用意しております。
お問い合わせ
コストダウンが利益に直結する術だと理解していても、なかなか前に進めることができない状況。そんな時は、newjiのコストダウン自動化機能で大きく利益貢献しよう!
(Β版非公開)