- お役立ち記事
- Fundamentals of powder, improving fluidity and filling properties, and key points for mixing powder and granular materials
Fundamentals of powder, improving fluidity and filling properties, and key points for mixing powder and granular materials
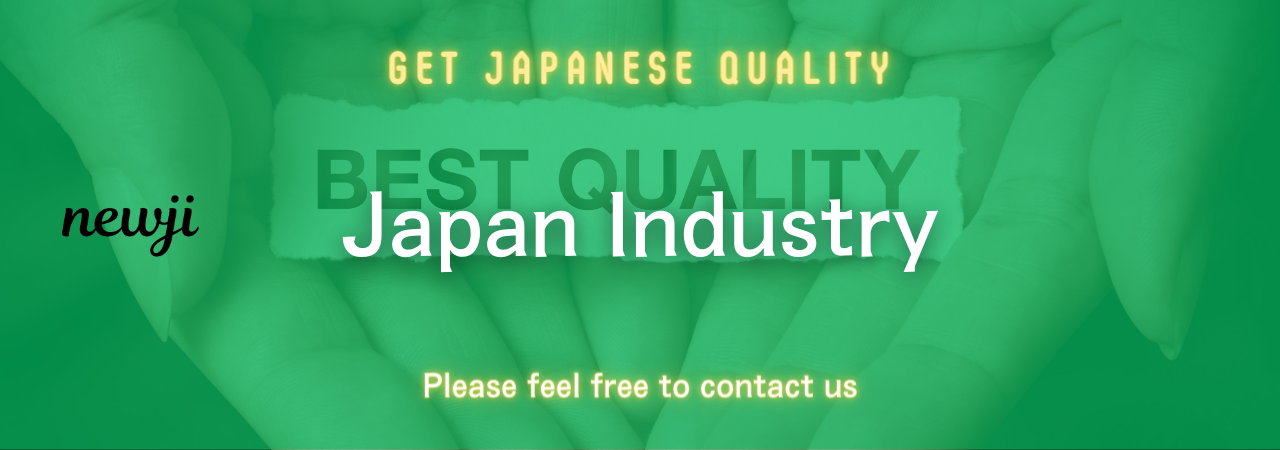
目次
Understanding the Basics of Powder
Powder is a fascinating form of matter, composed of tiny particles that, when combined, display distinct physical traits.
To fully grasp the characteristics of powders, it’s vital to understand their fundamental properties.
Powders can be found everywhere, from the food we eat to industrial applications.
Each type of powder has its own unique properties, including particle size, shape, surface area, and moisture content.
These factors influence how the powder behaves when flowing, when being packed, and in the end product’s quality.
Particle Size and Shape
The particle size and shape are crucial parameters that define the behavior of powder.
Smaller particles tend to fill voids better and often offer a smoother texture in the final product.
The shape, whether spherical, needle-like, or rough, affects how particles slide past one another, impacting the powder’s overall flowability.
Surface Area and Moisture Content
Surface area plays a pivotal role in how powders interact with fluids and other particles.
A larger surface area may enhance chemical reactions, but it can also require more energy for processing due to increased friction.
Additionally, the moisture content of a powder can deepen its complexity, as even slight changes can affect flow and packing efficiency.
Enhancing Powder Fluidity
Improving the fluidity of a powder is essential in ensuring efficient handling and processing.
Techniques to enhance fluidity are built around understanding and manipulating the powder’s intrinsic and extrinsic properties.
Intrinsically Modifying Powder Properties
One intrinsic method is adjusting the moisture content, as dry conditions promote better flow.
Controlling particle size distribution by milling or sieving can also help achieve desirable fluidity by minimizing the scatter of particle sizes.
Extrinsic Influences
Environmental factors such as humidity and temperature play significant roles in powder fluidity.
Maintaining optimal environmental conditions is critical for enhancing flow properties.
Additionally, using flow enhancers like glidants can promote particle movement and reduce inter-particle friction.
Improving Filling Properties of Powders
Ensuring uniform, consistent packing is crucial for both quality control and achieving desired end-product properties.
Several techniques can be employed to improve filling properties for powders.
Understanding Bulk Density
Bulk density is key to understanding how well a powder will fill a container or mold.
Tamping or vibrating the powder during filling can help reduce void spaces, increasing uniformity in packing.
Monitoring and adjusting bulk density is crucial for achieving desired compaction levels in a product.
Powder Conditioning Techniques
Various conditioning techniques such as granulation or drying can alter the packing properties of a powder.
Granulation, for instance, transforms fine powders into coarser granules, improving both filling properties and flowability.
Key Points in Mixing Powder and Granular Materials
Mixing powders and granular materials can be intricate, requiring attention to detail to ensure homogeneity and product stability.
Understanding the principles of mixing and employing best practices can significantly affect performance and quality.
The Role of Particle Size and Distribution
The particle size and their distribution are paramount in mixing processes.
Uniform particle size facilitates consistent mixing, whereas a mixture of particle sizes can create challenges in achieving homogenization.
Incorporating sieving can help achieve a more consistent size range, enhancing the mixing process.
Strategies for Effective Mixing
Choosing the right mixer based on the material properties is crucial.
Shear mixing is ideal for cohesive powders, while tumbling mixers suit free-flowing powders.
Batch mixing can be effective for smaller quantities, while continuous mixers handle large volumes efficiently.
Monitoring the time and speed of mixing can also prevent over-mixing or segregation, ensuring a quality blend.
Utilizing mixing aids or binders can further stabilize the mixture, promoting consistency throughout.
Conclusion
Understanding the fundamentals of powder, alongside the methods to improve fluidity and filling properties, is essential knowledge for a variety of industries reliant on powders.
Paying attention to particle characteristics and employing proper techniques in mixing powders and granular materials is crucial.
By refining these processes, manufacturers can achieve greater efficiency, product quality, and consistency.
資料ダウンロード
QCD調達購買管理クラウド「newji」は、調達購買部門で必要なQCD管理全てを備えた、現場特化型兼クラウド型の今世紀最高の購買管理システムとなります。
ユーザー登録
調達購買業務の効率化だけでなく、システムを導入することで、コスト削減や製品・資材のステータス可視化のほか、属人化していた購買情報の共有化による内部不正防止や統制にも役立ちます。
NEWJI DX
製造業に特化したデジタルトランスフォーメーション(DX)の実現を目指す請負開発型のコンサルティングサービスです。AI、iPaaS、および先端の技術を駆使して、製造プロセスの効率化、業務効率化、チームワーク強化、コスト削減、品質向上を実現します。このサービスは、製造業の課題を深く理解し、それに対する最適なデジタルソリューションを提供することで、企業が持続的な成長とイノベーションを達成できるようサポートします。
オンライン講座
製造業、主に購買・調達部門にお勤めの方々に向けた情報を配信しております。
新任の方やベテランの方、管理職を対象とした幅広いコンテンツをご用意しております。
お問い合わせ
コストダウンが利益に直結する術だと理解していても、なかなか前に進めることができない状況。そんな時は、newjiのコストダウン自動化機能で大きく利益貢献しよう!
(Β版非公開)