- お役立ち記事
- Basics of PID control and parameter determination method in digital control
Basics of PID control and parameter determination method in digital control
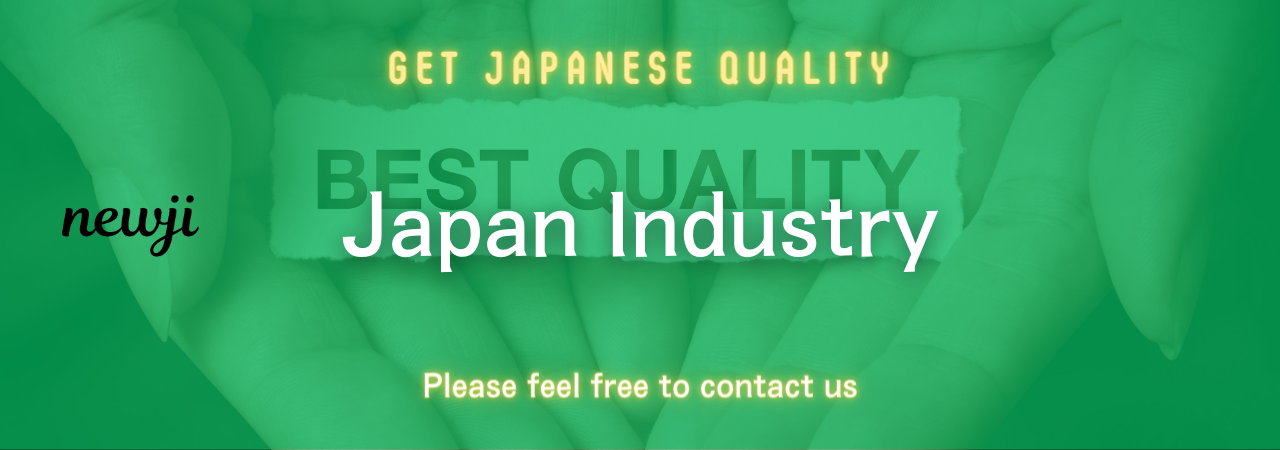
目次
Introduction to PID Control
PID control is a vital concept in the field of digital control systems, widely used across various industries for enhancing process efficiency and stability.
The term “PID” stands for Proportional, Integral, and Derivative, which are the three core mathematical functions that determine how the control system responds to errors between desired setpoint and actual process variable.
These three components work together to adjust the output of the system and maintain the desired level of control.
By understanding the principles behind PID control, engineers and technicians can effectively fine-tune their systems for optimal performance.
The Components of PID Control
Proportional Control
Proportional control is the first and most fundamental component of a PID controller.
It adjusts the control output proportionally to the current error value.
The primary goal of the proportional control is to reduce the overall error by applying a correction that is directly proportional to the magnitude of the error.
The proportional gain, often denoted as Kp, is a critical parameter in this component.
A higher proportional gain results in a larger corrective effort for a given error, while a smaller gain results in a gentler response.
However, too high of a proportional gain can lead to system instability, known as “overshooting,” where the system oscillates around the setpoint.
Integral Control
The integral component of PID control addresses the accumulation of past errors over time.
It integrates the error over time, effectively eliminating any residual steady-state error that the proportional control alone cannot handle.
This component is crucial for correcting persistent discrepancies between the desired and actual output.
The integral gain, denoted as Ki, dictates the strength of this correction.
Proper tuning of Ki ensures that errors are minimized without causing excessive overshoot or instability in the system.
Derivative Control
Derivative control predicts future behavior of the error based on its rate of change.
It acts as a dampener by providing a corrective action that is proportional to the rate at which the error is changing.
This helps in smoothing the control output and preventing excessive oscillation or overshooting.
The derivative gain, represented as Kd, needs to be carefully set, as excessive derivative action can amplify noise present in the system, leading to erratic control behavior.
Determining PID Parameters
Successful PID control implementation requires careful parameter tuning.
Finding the right balance for Kp, Ki, and Kd is essential for achieving stable and efficient control.
There are several methods for determining these parameters:
Trial and Error
One of the simplest but time-consuming methods for tuning PID parameters is trial and error.
By iteratively adjusting Kp, Ki, and Kd, engineers observe the system’s response and gradually refine the values until desired performance is achieved.
This method requires patience and a good understanding of the process to avoid prolonged trial periods.
Ziegler-Nichols Method
The Ziegler-Nichols method, named after John G. Ziegler and Nathaniel B. Nichols, is a popular heuristic tuning method.
This method involves configuring the system as a P-controller, gradually increasing Kp until the system reaches the verge of oscillation.
At this point, called the “ultimate gain” (Ku), the critical oscillation period (Tu) is recorded.
Based on these values, empirical formulas provided by Ziegler-Nichols can be used to calculate initial settings for Kp, Ki, and Kd.
Software-Based Tuning
With advancements in digital control systems, many contemporary PID controllers come equipped with software-based auto-tuning features.
These tools use algorithms to automatically determine optimal PID parameter settings by analyzing the system’s response to specific inputs.
This method significantly reduces the time required for tuning and minimizes the risk of human error.
Model-Based Design
In complex systems, model-based design provides a structured approach to PID tuning.
By developing a mathematical model of the process, simulation tools can predict how adjustments to PID parameters will affect system behavior.
This allows engineers to simulate various scenarios and select the best control strategy before applying it to the actual system.
Applications of PID Control
PID control is utilized in a wide range of applications across multiple industries, including manufacturing, robotics, aerospace, automotive, and process control.
For example, in temperature control systems, PID controllers maintain a constant temperature by adjusting heating elements based on discrepancies between the desired and current temperature.
In robotics, PID control helps achieve precise positioning by regulating motors based on feedback from sensors.
Its adaptability and versatility make PID control an invaluable asset in ensuring efficient and stable operation of complex systems.
Conclusion
Mastering PID control and its parameter determination methods is essential for engineers and technicians working with digital control systems.
Understanding the individual contributions of proportional, integral, and derivative components allows for the proper implementation of these control systems.
By employing methods such as trial and error, Ziegler-Nichols tuning, software-based tuning, or model-based design, optimal parameters can be determined to ensure system stability and efficiency.
As technology advances, the need for precise and effective control systems continues to grow, making PID control an ever-relevant and indispensable tool in the engineer’s toolkit.
資料ダウンロード
QCD調達購買管理クラウド「newji」は、調達購買部門で必要なQCD管理全てを備えた、現場特化型兼クラウド型の今世紀最高の購買管理システムとなります。
ユーザー登録
調達購買業務の効率化だけでなく、システムを導入することで、コスト削減や製品・資材のステータス可視化のほか、属人化していた購買情報の共有化による内部不正防止や統制にも役立ちます。
NEWJI DX
製造業に特化したデジタルトランスフォーメーション(DX)の実現を目指す請負開発型のコンサルティングサービスです。AI、iPaaS、および先端の技術を駆使して、製造プロセスの効率化、業務効率化、チームワーク強化、コスト削減、品質向上を実現します。このサービスは、製造業の課題を深く理解し、それに対する最適なデジタルソリューションを提供することで、企業が持続的な成長とイノベーションを達成できるようサポートします。
オンライン講座
製造業、主に購買・調達部門にお勤めの方々に向けた情報を配信しております。
新任の方やベテランの方、管理職を対象とした幅広いコンテンツをご用意しております。
お問い合わせ
コストダウンが利益に直結する術だと理解していても、なかなか前に進めることができない状況。そんな時は、newjiのコストダウン自動化機能で大きく利益貢献しよう!
(Β版非公開)