- お役立ち記事
- Fundamentals of loop heat pipe heat transport technology, design, manufacturing and evaluation methods, and high performance and multifunctional technology
Fundamentals of loop heat pipe heat transport technology, design, manufacturing and evaluation methods, and high performance and multifunctional technology
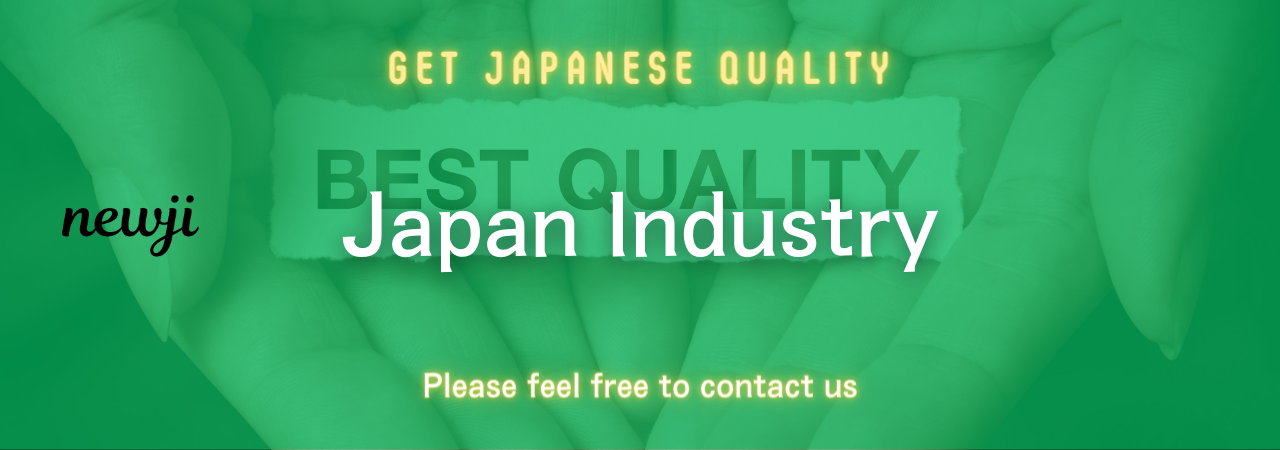
目次
Introduction to Loop Heat Pipe Technology
Loop heat pipes (LHPs) are crucial in thermal management systems, primarily because of their efficiency in transferring heat over long distances with minimal temperature drop.
Since their development, they have found applications in a range of fields, from electronics cooling to space technology.
Understanding the fundamentals of LHPs, including their design, manufacturing, and evaluation methods, is essential for developing high-performance and multifunctional thermal systems.
The Basics of Loop Heat Pipe Heat Transport
At its core, a loop heat pipe is a two-phase thermal transport device.
The basic components of an LHP include an evaporator, a condenser, a compensation chamber, and a system of transport lines.
The evaporator absorbs heat, causing the working fluid to evaporate.
This vapor moves toward the condenser through the transport lines, where it releases heat and condenses back into a liquid.
The capillary action of a wicking structure within the evaporator ensures the return of the fluid to the evaporation zone, making the system efficient and passive, without the need for mechanical pumps.
Principles of LHP Design
The design of loop heat pipes focuses on factors such as heat load, operating temperature range, and working fluid selection.
Material choice is crucial, as it must withstand the thermal and pressure cycling during operation.
Common materials include aluminum and stainless steel due to their thermal conductivity and structural integrity.
The wicking material, often sintered metal or a porous ceramic, is selected based on its ability to maintain the fluid flow despite potential blockages from vapor bubbles.
Designing the transport lines is also key, requiring careful determination of their length, diameter, and insulation to minimize heat loss.
The compressor chamber’s volume must be adequate to manage variations in working fluid volume caused by temperature changes.
Working Fluid Selection
The fluid used in LHPs directly impacts the efficiency and reliability of the system.
Commonly used fluids include ammonia, acetone, and water, chosen based on the application’s temperature range and required heat transfer capacity.
Chemical compatibility with the LHP materials and a low freezing point are also important considerations to ensure long-term operation and minimize the risk of damage from phase change stresses.
Manufacturing Practices for Loop Heat Pipes
Manufacturing loop heat pipes requires precision to ensure components fit and function correctly.
The process begins with the fabrication of the evaporator and condenser, often through precise machining and sintering processes.
Wick structures, as central elements in LHPs, are produced through powder metallurgy techniques to achieve the required porosity and structural strength.
Joinery, such as welding or brazing, is utilized to connect the various components, ensuring they withstand mechanical stresses and heat cycles.
Precision cleaning is critical; manufacturing residues can impede function by blocking the wicking structure or reacting chemically with the working fluid.
Assembly and Testing
Once assembled, initial testing for leaks and integrity is essential.
It involves pressurizing the pipe with an inert gas and checking for pressure losses.
Performance testing follows, evaluating parameters such as thermal resistance, maximum heat load, and response time to heat load changes.
Evaluation Methods for Loop Heat Pipes
Evaluating an LHP involves both experimental and computational methods.
Experimental tests might include thermal performance measurements across different orientations and heat loads.
Long-term reliability tests, exposing the LHP to cycles of operational conditions, simulate potential real-life applications over time.
Computational fluid dynamics (CFD) and finite element analysis (FEA) are utilized to model temperature distributions, identify potential design flaws, and optimize the system before physical testing.
These methods allow engineers to predict how alterations in design affect overall performance and can reduce the need for costly physical prototyping.
Enhancing Performance and Multifunctionality
Improving LHP performance involves optimizing design to increase the heat transfer rate or expanding functionality.
Recent advancements include hybrid systems combining LHPs with other cooling technologies like thermoelectric coolers, providing superior heat transfer and precise temperature control.
Material advancements in wicking structures promise increased thermal conductivity and capillary efficiency.
Multifunctional loop heat pipes integrate sensors and control systems to dynamically adjust performance based on real-time data.
Conclusion
Loop heat pipes remain at the forefront of efficient thermal management technologies.
Understanding the fundamentals of their design and manufacturing, along with advanced evaluation and performance enhancement techniques, ensures they meet the evolving demands of modern applications.
As research continues to refine materials and designs, LHPs will undoubtedly become more efficient, reliable, and versatile, solidifying their role in future thermal management solutions.
資料ダウンロード
QCD調達購買管理クラウド「newji」は、調達購買部門で必要なQCD管理全てを備えた、現場特化型兼クラウド型の今世紀最高の購買管理システムとなります。
ユーザー登録
調達購買業務の効率化だけでなく、システムを導入することで、コスト削減や製品・資材のステータス可視化のほか、属人化していた購買情報の共有化による内部不正防止や統制にも役立ちます。
NEWJI DX
製造業に特化したデジタルトランスフォーメーション(DX)の実現を目指す請負開発型のコンサルティングサービスです。AI、iPaaS、および先端の技術を駆使して、製造プロセスの効率化、業務効率化、チームワーク強化、コスト削減、品質向上を実現します。このサービスは、製造業の課題を深く理解し、それに対する最適なデジタルソリューションを提供することで、企業が持続的な成長とイノベーションを達成できるようサポートします。
オンライン講座
製造業、主に購買・調達部門にお勤めの方々に向けた情報を配信しております。
新任の方やベテランの方、管理職を対象とした幅広いコンテンツをご用意しております。
お問い合わせ
コストダウンが利益に直結する術だと理解していても、なかなか前に進めることができない状況。そんな時は、newjiのコストダウン自動化機能で大きく利益貢献しよう!
(Β版非公開)