- お役立ち記事
- Basics of machining methods, design points and practical know-how for designers
Basics of machining methods, design points and practical know-how for designers
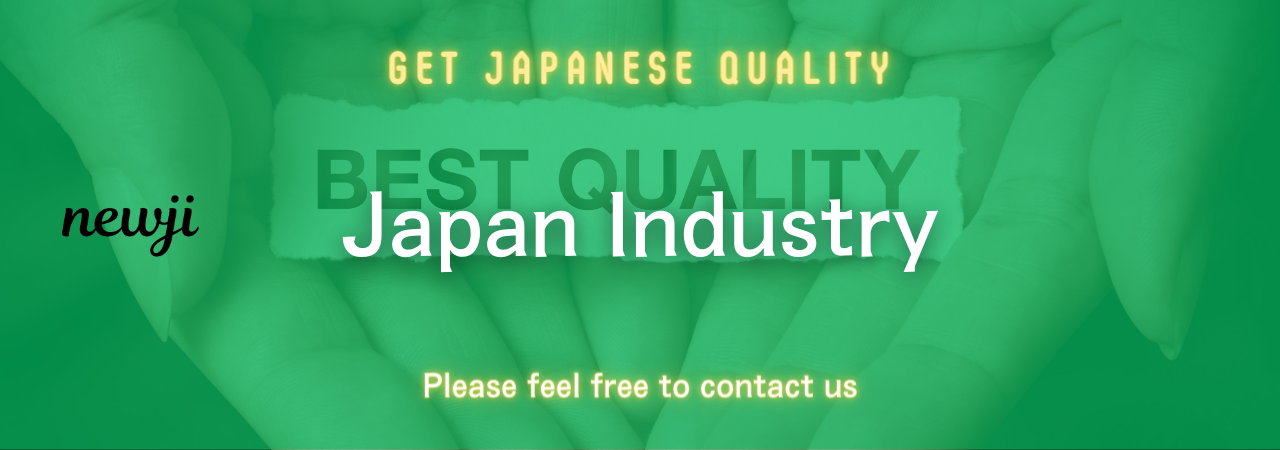
目次
Introduction to Machining Methods
Machining is a process used in manufacturing to remove material from a workpiece to shape or finish it according to precise specifications.
This process is fundamental in the manufacturing industry as it allows for the creation of complex parts used in various applications.
Understanding the basics of machining methods is essential for designers to create efficient and effective designs.
Common Machining Methods
Several machining methods are commonly used in manufacturing, each with unique characteristics and applications.
**Turning**: This method involves rotating the workpiece while a cutting tool moves across it.
Typically employed using a lathe, turning is used to create cylindrical parts, such as shafts and spindles.
**Milling**: In milling, a rotating cutting tool removes material as it advances into a workpiece.
Milling can create complex shapes and surfaces and is often used for parts that require intricate detailing.
**Drilling**: Drilling involves creating round holes in a workpiece using a rotating drill bit.
This process is essential in creating holes for bolts or other fasteners in parts.
**Grinding**: Grinding uses an abrasive wheel to finish the surface of a workpiece, providing smoothness and high precision.
It’s commonly used for finishing applications where tight tolerances are necessary.
**EDM (Electrical Discharge Machining)**: This method removes material using electrical discharges or sparks.
It’s ideal for hard materials and complex shapes where traditional machining might struggle.
Design Points for Machining
When designing parts to be produced through machining, several factors must be considered to optimize the process and cost-effectiveness.
**Material Selection**: The choice of material impacts the ease of machining and the tool wear.
Soft metals like aluminum are easier to machine, whereas harder metals may require specialized tools and techniques.
**Part Geometry**: Simplifying part geometry can reduce machining time and costs.
Designers should avoid unnecessarily complex features that might complicate the machining process.
**Tolerance Levels**: Specify realistic tolerance levels to avoid excessive machining time and costs.
While tight tolerances are necessary for some applications, loosening them where possible can be more cost-effective.
**Surface Finishing**: Specify the necessary surface finish to balance aesthetic and functional requirements.
Unnecessary finishing might inflate production costs without adding functional value.
**Tool Accessibility**: Ensure that every feature on the part is accessible by machining tools.
Considerations about tool access can significantly influence the machining setup and time.
Practical Know-How for Designers
Designers should equip themselves with practical knowledge to streamline the machining process effectively.
**Understanding Machining Capabilities**: Designers should familiarize themselves with the capabilities and limitations of different machining techniques to design manufacturable parts.
**Collaborate with Machinists**: Engaging with machinists during the design phase can provide valuable insights into practical aspects of the machining process.
This collaboration ensures that the design is feasible and efficient to produce.
**Prototyping**: Creating prototypes can provide a hands-on understanding of how design translates to real-world parts.
This practice helps in identifying potential issues early in the design phase.
**Keeping Up with Technology**: Technology in machining is continuously evolving.
Stay updated with the latest tools and techniques to incorporate new possibilities into designs and improve efficiency.
**Cost Analysis**: Understand the impact of design decisions on costs.
Opting for high-quality materials or finishes might provide significant benefits outweighing the cost, but it’s important to evaluate thoroughly.
Conclusion
Understanding machining methods and their implications in design is crucial for creating efficient and manufacturable parts.
Designers should consider material selection, part geometry, and machining capabilities to optimize their designs.
By maintaining collaborative relationships with machinists and continuously advancing their technical knowledge, designers can bridge the gap between design and manufacturing effectively.
This integrated approach ensures high-quality, cost-effective products that meet their intended specifications.
資料ダウンロード
QCD調達購買管理クラウド「newji」は、調達購買部門で必要なQCD管理全てを備えた、現場特化型兼クラウド型の今世紀最高の購買管理システムとなります。
ユーザー登録
調達購買業務の効率化だけでなく、システムを導入することで、コスト削減や製品・資材のステータス可視化のほか、属人化していた購買情報の共有化による内部不正防止や統制にも役立ちます。
NEWJI DX
製造業に特化したデジタルトランスフォーメーション(DX)の実現を目指す請負開発型のコンサルティングサービスです。AI、iPaaS、および先端の技術を駆使して、製造プロセスの効率化、業務効率化、チームワーク強化、コスト削減、品質向上を実現します。このサービスは、製造業の課題を深く理解し、それに対する最適なデジタルソリューションを提供することで、企業が持続的な成長とイノベーションを達成できるようサポートします。
オンライン講座
製造業、主に購買・調達部門にお勤めの方々に向けた情報を配信しております。
新任の方やベテランの方、管理職を対象とした幅広いコンテンツをご用意しております。
お問い合わせ
コストダウンが利益に直結する術だと理解していても、なかなか前に進めることができない状況。そんな時は、newjiのコストダウン自動化機能で大きく利益貢献しよう!
(Β版非公開)