- お役立ち記事
- Fundamentals of stress and strain in joining dissimilar materials and applications to strength evaluation and stress analysis
Fundamentals of stress and strain in joining dissimilar materials and applications to strength evaluation and stress analysis
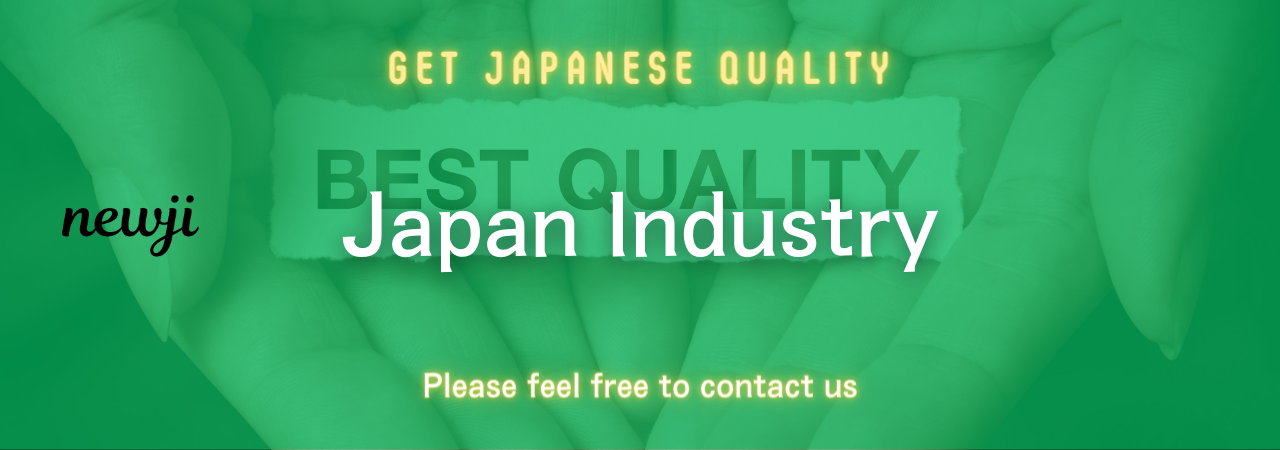
Understanding Stress and Strain in Material Joining
Joining dissimilar materials is a crucial aspect of modern engineering and manufacturing processes.
As industries strive to innovate and create products that are lighter, stronger, and more efficient, understanding the fundamentals of stress and strain in these applications becomes essential.
Stress and strain are concepts used to predict and analyze the behavior of materials under various forces and deformations.
Let’s delve into how these concepts apply to joining dissimilar materials and their importance in evaluating strength and performing stress analysis.
What is Stress?
Stress is the force applied per unit area within a material.
It is a measure of the internal resistance offered by a material when subjected to external forces.
Mathematically, stress is expressed as:
\[ \sigma = \frac{F}{A} \]
where \(\sigma\) is stress, \(F\) is the force applied, and \(A\) is the cross-sectional area the force is distributed over.
Stress can be categorized into several types depending on how the load is applied, including tensile, compressive, shear, and torsional stress.
Understanding Strain
Strain is a measure of the deformation of a material caused by applied stress.
It quantifies how much a material’s shape or dimensions alter when a force is applied.
Strain is a dimensionless quantity defined as the ratio of change in dimension to the original dimension.
The formula for strain (\(\epsilon\)) is:
\[ \epsilon = \frac{\Delta L}{L_0} \]
where \(\Delta L\) is the change in length, and \(L_0\) is the original length.
Strain types also mirror those of stress, such as tensile strain and compressive strain, each corresponding to changes in length due to the respective stresses.
Challenges in Joining Dissimilar Materials
Joining dissimilar materials is often challenging because different materials have unique thermal, mechanical, and physical properties.
Variations in expansion rates, melting points, and elastic properties can lead to unexpected stress distributions and potential failure points.
To ensure successful joints, one must consider the compatibility and behavior of each material under different stress and strain conditions.
Applications of Stress and Strain Analysis
Understanding and applying stress and strain analysis is integral to numerous applications:
1. Material Selection
Selecting materials that will be joined requires detailed knowledge of their respective properties and how these will interact under stress.
Engineers use stress and strain analysis to predict how materials will perform together, ensuring that the joint will be robust and durable under anticipated loads.
2. Design Optimization
Design optimization often involves minimizing weight while maximizing strength and functionality.
Analyzing stress and strain helps in identifying areas where materials can be replaced or modified to improve the overall performance of a component or structure.
3. Failure Analysis
In industries such as aerospace, automotive, and civil engineering, understanding the causes of failure is critical.
Stress analysis helps identify the points of failure and reasons behind them, allowing for redesign or restructuring to prevent recurrence.
Evaluating Strength in Joined Materials
Evaluating the strength of joints made from dissimilar materials involves several steps:
1. Stress Concentration Analysis
Stress concentrations around the joint are critical areas that need careful analysis.
These points are where a material’s resistance to applied forces is lower, and failure is more likely to occur.
Using both analytical methods and simulations like Finite Element Analysis (FEA) helps predict how stress is distributed across the joint.
2. Thermal and Mechanical Testing
Practical testing under controlled conditions is vital to gauge how the joint will behave under real-world scenarios.
Various tests — such as tensile tests, thermal cycling, and fatigue tests — evaluate how the joint can handle different stresses and environmental conditions.
3. Adhesion and Welding Techniques
The method of joining plays a significant role in determining the joint’s overall strength.
Welding, adhesive bonding, and mechanical fastening each have unique stress and strain distributions.
Choosing the appropriate technique requires understanding the advantages and limitations of each method.
Conclusion
Joining dissimilar materials is a complex process that requires a comprehensive understanding of stress and strain fundamentals.
By evaluating how these materials interact and behave under different forces, engineers and designers can optimize the structure’s strength, durability, and performance.
Emphasis on precise material selection, design optimization, and thorough testing ensures that joints are reliable and meet the stringent demands of modern applications.
With ongoing technological advancements, new methods and materials continually emerge, promising even more effective solutions for joining disparate materials in numerous industries.
資料ダウンロード
QCD調達購買管理クラウド「newji」は、調達購買部門で必要なQCD管理全てを備えた、現場特化型兼クラウド型の今世紀最高の購買管理システムとなります。
ユーザー登録
調達購買業務の効率化だけでなく、システムを導入することで、コスト削減や製品・資材のステータス可視化のほか、属人化していた購買情報の共有化による内部不正防止や統制にも役立ちます。
NEWJI DX
製造業に特化したデジタルトランスフォーメーション(DX)の実現を目指す請負開発型のコンサルティングサービスです。AI、iPaaS、および先端の技術を駆使して、製造プロセスの効率化、業務効率化、チームワーク強化、コスト削減、品質向上を実現します。このサービスは、製造業の課題を深く理解し、それに対する最適なデジタルソリューションを提供することで、企業が持続的な成長とイノベーションを達成できるようサポートします。
オンライン講座
製造業、主に購買・調達部門にお勤めの方々に向けた情報を配信しております。
新任の方やベテランの方、管理職を対象とした幅広いコンテンツをご用意しております。
お問い合わせ
コストダウンが利益に直結する術だと理解していても、なかなか前に進めることができない状況。そんな時は、newjiのコストダウン自動化機能で大きく利益貢献しよう!
(Β版非公開)