- お役立ち記事
- How to create appropriate quality
How to create appropriate quality
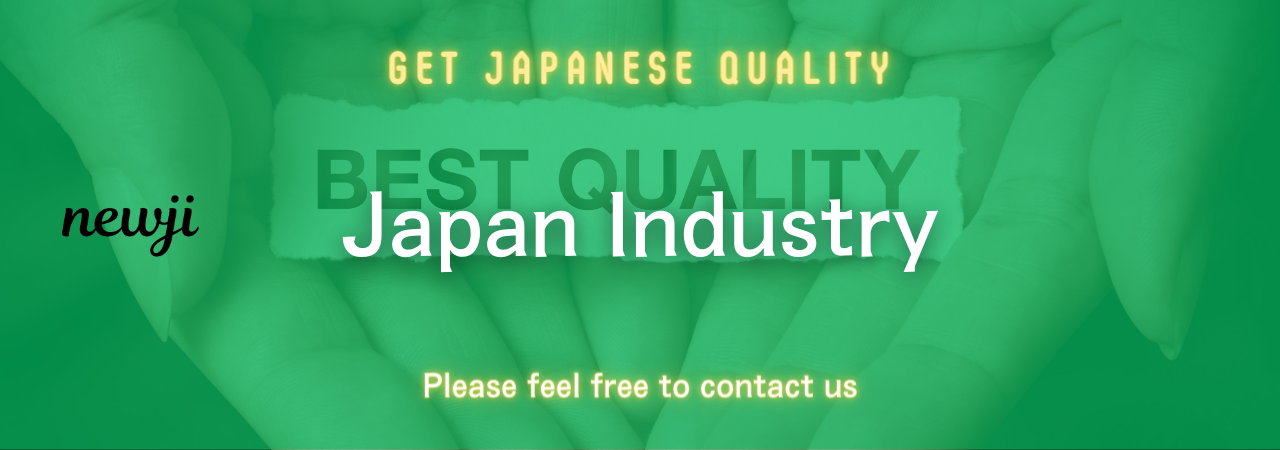
目次
Understanding Quality in a Broader Sense
Quality is a term that resonates across various fields, from manufacturing and service delivery to education and healthcare.
It is often defined as meeting or exceeding customer expectations, and ensuring that a product or service is free from defects or deficiencies.
However, creating appropriate quality involves not just meeting expectations, but also understanding what these expectations are, and balancing them with feasibility and practicality.
The Importance of Quality
Quality is crucial because it affects customer satisfaction, efficiency, and profitability.
High-quality products or services attract customers and ensure their loyalty, as they are more likely to return for repeat purchases.
On the other hand, poor quality can lead to dissatisfaction, returns, and negative reviews, which can harm a company’s reputation and bottom line.
Quality management also leads to better utilization of resources, minimizes waste, and enhances productivity.
Identifying Customer Needs
Before quality can be created, understanding the needs and expectations of customers is crucial.
This can be achieved through various methods such as surveys, interviews, focus groups, and feedback analysis.
By listening to customers and understanding their pain points, a business can tailor its offerings to better serve them.
Furthermore, it is important to keep up with industry trends and competitors to ensure that quality is not just about meeting current expectations but also anticipating future needs.
Setting Clear Quality Objectives
Once customer needs are identified, the next step is to establish clear and measurable quality objectives.
These objectives should align with the overall business goals and be specific, achievable, and time-bound.
For example, a company might aim to reduce product defects by 10% within a year or improve customer satisfaction ratings by 5% over six months.
Such objectives provide a clear focus and direction for quality improvement efforts.
Implementing Quality Standards
To create appropriate quality, businesses must adhere to established quality standards and practices.
Standards such as ISO 9001 provide a framework for setting up effective quality management systems (QMS).
A QMS helps in developing systematic processes and procedures to ensure quality at every stage, from product design to delivery.
Implementing these standards requires commitment from all levels of the organization, from top management to frontline employees.
It involves regular training, evaluations, and quality audits to ensure compliance and continuous improvement.
Continuous Improvement and Innovation
Quality is not a one-time achievement but a continual process.
Adopting a philosophy of continuous improvement, such as Kaizen, encourages incremental changes that lead to superior quality over time.
Regularly reviewing and updating processes, seeking feedback, and being open to change are essential steps in maintaining high-quality standards.
Additionally, innovation plays a key role in enhancing quality.
By embracing new technologies and methodologies, companies can enhance efficiency and create unique, high-quality products and services.
Balancing Quality with Cost
Creating appropriate quality often involves a delicate balance between quality and cost.
Investing in quality improvements can involve additional costs, such as better materials, more skilled labor, or expensive technology.
However, these costs need to be balanced with the expected benefits such as increased sales, reduced returns, and better customer retention.
To achieve this balance, businesses need to conduct cost-benefit analyses to determine the economic feasibility of quality initiatives.
Decision-makers should consider both short-term expenses and long-term returns to make informed choices.
Empowering Employees for Quality
Employees play a significant role in ensuring quality.
Empowering them through education, training, and resources is crucial for sustaining quality standards.
Cultivating a culture where every employee understands their role in quality improvement and feels responsible for the end results creates an engaged and proactive workforce.
Encouraging a sense of ownership and recognizing contributions can motivate staff members to be vigilant and responsive to quality issues.
Regular communication and feedback loops ensure that ideas for quality enhancement are shared and implemented effectively.
Leveraging Technology for Quality
Technology provides cutting-edge tools that can be leveraged to create and maintain quality.
Automation and advanced software solutions reduce the likelihood of human error, enhance precision, and ensure consistent results.
For instance, in manufacturing, robotics and IoT devices can monitor and optimize production processes, ensuring quality control.
In the service sector, CRM systems help track customer interactions and feedback, enabling personalized and consistent service delivery.
By staying abreast of technological advancements, companies can enhance their quality frameworks and remain competitive.
The Customer’s Role in Quality
Customers are not just the end-users but key stakeholders in quality management.
Engaging customers in the quality process through open communication, easy feedback channels, and responsive service enhances their experience and satisfaction.
By considering customer feedback in the development and improvement of products and services, companies can ensure that they are truly meeting their needs.
Moreover, engaging customers in decision-making processes, such as through customer advisory panels, can provide valuable insights and foster loyalty.
Conclusion
Creating appropriate quality is a comprehensive and ongoing endeavor.
It requires understanding customer needs, setting clear objectives, adhering to standards, and ensuring continuous improvement through the involvement of both employees and customers.
Balancing quality with cost, leveraging technology, and fostering a culture of accountability and innovation are pivotal to achieving and sustaining high-quality standards.
Ultimately, a commitment to quality not only benefits the customer but drives business success and growth.
資料ダウンロード
QCD調達購買管理クラウド「newji」は、調達購買部門で必要なQCD管理全てを備えた、現場特化型兼クラウド型の今世紀最高の購買管理システムとなります。
ユーザー登録
調達購買業務の効率化だけでなく、システムを導入することで、コスト削減や製品・資材のステータス可視化のほか、属人化していた購買情報の共有化による内部不正防止や統制にも役立ちます。
NEWJI DX
製造業に特化したデジタルトランスフォーメーション(DX)の実現を目指す請負開発型のコンサルティングサービスです。AI、iPaaS、および先端の技術を駆使して、製造プロセスの効率化、業務効率化、チームワーク強化、コスト削減、品質向上を実現します。このサービスは、製造業の課題を深く理解し、それに対する最適なデジタルソリューションを提供することで、企業が持続的な成長とイノベーションを達成できるようサポートします。
オンライン講座
製造業、主に購買・調達部門にお勤めの方々に向けた情報を配信しております。
新任の方やベテランの方、管理職を対象とした幅広いコンテンツをご用意しております。
お問い合わせ
コストダウンが利益に直結する術だと理解していても、なかなか前に進めることができない状況。そんな時は、newjiのコストダウン自動化機能で大きく利益貢献しよう!
(Β版非公開)